与全球所有领先的汽车制造商一样,位于德国巴伐利亚州兰茨胡特的汽车制造商宝马公司(BMW)很早就开始研究所谓的 “一体化压铸 “或”巨型压铸”的优缺点。特斯拉在其汽车结构中采用大型压铸件(例如 Model Y 的后车身底部结构)引起了广泛关注。
用大型铸件替代尽可能多的单个零件和工序,从而在简化生产流程的同时降低成本、重量和二氧化碳排放量,这种方法听起来很诱人。但另一方面,对新系统和基础设施的前期投资、产品线的重新配置以及与大型部件的生产和进一步使用相关的技术挑战都很高。 在兰茨胡特宝马轻金属铸造厂与克劳斯-萨默尔(Klaus Sammer)和托马斯-科普(Thomas Kopp)博士进行的背景讨论中,双方得以讨论支持和反对的主要论点,并了解宝马公司的具体观点。
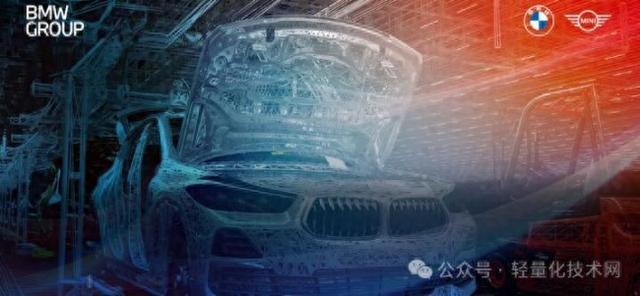
说到一体化压铸或者巨型压铸,没有“对”与“错”之分
Kopp 和 Sammer 深入研究了与大型铸件生产相关的问题,并深知其中的利弊。
2024年宝马位于兰茨胡特的轻金属铸造厂的情况如何?
位于兰茨胡特的宝马集团轻金属铸造厂是一个极具创新性的厂址,拥有广泛而独特的铸造技术。其中包括传统的重力铸造和低压铸造。一种特殊的重力铸造工艺是喷射铸造工艺,该工艺由兰茨胡特的铸造专家于2007年开发并获得专利。它结合了重力铸造和低压铸造的优点。在浇注开始时,使用喷射器对型腔进行填充,出口位于模具底部。在浇注过程中,注射器缓慢向上移动。在填充过程中,出料口始终低于熔池表面。这导致了分层模具填充,对凝固过程产生了积极影响。这种工艺可用于生产高度复杂的功能部件,如电机的中央外壳。生产底模所需的砂芯完全采用无机粘结剂系统。正如 Kopp 和 Sammer 所强调的那样,这使得铸造过程几乎不排放废气,而且这种情况已经持续了 15 年以上。除了传统的射芯工艺,兰茨胡特生产基地还可以使用无机粘结剂喷射系统进行增材制造的方法生产砂芯。这确保了该基地未来的可行性。
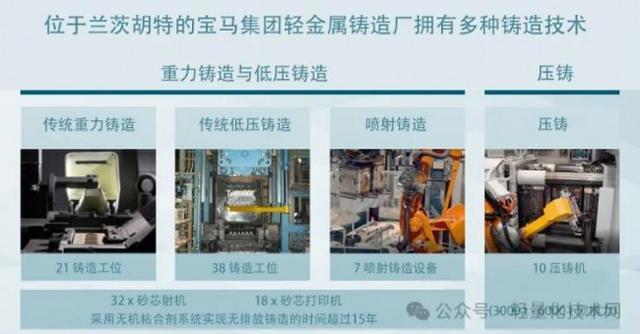
在压铸领域,该生产基地拥有十套设备,锁模力从 3,000 吨到 6,000 吨不等。当然,有充分的理由支持使用锁模力超过6000吨甚至高达16000吨的压铸单元。”对”或 “错”的问题并不能一概而论,因为它总是与整体环境有关。 决定是否使用巨型铸造在很大程度上取决于生产工艺的具体要求、现场条件(如物料流/物流)以及公司的标准和目标。
众所周知,铸造件的一个优点是可以替代钣金部件,从而省去制造和装配步骤。一个简单的例子是减震塔,这意味着可以替代大约15个部件。在这种情况下,由于可替代部件的数量较少,轻量化的潜力相当低。减震塔是在压铸机上制造的,锁模力在2000吨至3000吨之间。
后纵向构件的替代程度较高,轻量化潜力较大。然而,由于喷砂面积较大,还需要4000吨的大型机器。
如果目的是尽可能多地替代部件,那么一体化后底板是正确的选择。在这种情况下,可以替换80到100个部件。这些所谓的一体化压铸件是在锁模力超过8000吨的系统上生产的。然而,这并不一定是轻量化潜力最大的解决方案。为了能够通过压铸生产部件,下图中红色的金属板表面(如行李箱底板或车轮拱罩)必须具有一定的最小壁厚。这通常大于负载所要求的壁厚,因此会增加部件的总重量。增加重量的同时也增加了材料成本,因为昂贵的轻量化材料铝被用在了一些本可以用更薄的板材(如成型金属板)的位置。
在正确的位置使用正确的材料和正确的制造工艺(拓扑优化)至关重要。在重量和替代程度方面,4000吨到6000吨之间的压铸机生产的部件是最佳选择。
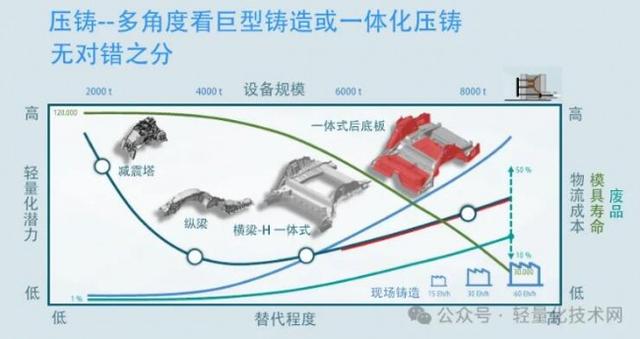
然而,除了轻量化潜力之外,在做出决定时还需要考虑许多其他因素。在这一点上,应该提到与热处理同时进行的功能要求。维修方案的重要性也不容忽视。对于大型铸件来说,修复方案的适用范围有限,而且通常需要支付额外费用。
另一个关键是物流成本,随着部件尺寸的增大,物流成本也会显著增加。为了解决这个问题,铸造厂必须与整车厂相连,从而投资新的压铸系统。所需的系统数量在很大程度上取决于整车厂的产量和每条生产线的变型产品数量。通常需要多台压铸机才能可靠地向汽车生产线供货。
对于压铸模具也提出了类似的挑战。由于部件尺寸大,预计模具磨损会增加,从而导致维护间隔缩短,因此需要的模具数量也会增加。
原则上,应该指出的是,目前在宝马公司使用锁模力大于 6000 吨的铸造单元并不具备有效的优势。位于兰茨胡特的宝马零部件工厂拥有强大的供应商网络,从而确保了整车厂的供应。
在宝马公司,重点不在于可行性,而在于通过创新和大量的专业知识实现最佳效果,同时在正确的位置使用正确的工艺铸造正确的材料。
关于宝马兰茨胡特工厂
在宝马集团兰茨胡特工厂,约有 3,700 名员工生产由铸造轻合金制成的发动机、底盘和车身结构部件、用于汽车外饰的塑料部件、碳纤维车身部件、驾驶舱和设备范围、发动机和传动轴。兰茨胡特工厂是宝马集团全球最大的零部件工厂,为宝马集团在全球的所有汽车和发动机工厂提供零部件,因此几乎为每一辆宝马、MINI、劳斯莱斯和宝马摩托车提供零部件。兰茨胡特宝马集团工厂代表着以数字化和可持续发展为特征的零部件生产,以及对资源的负责任利用。
凭借面向未来的技术,兰茨胡特宝马集团工厂在汽车行业及其供应商行业的技术转型中扮演着创新驱动者的角色。在与工厂直接相连的轻量化和技术中心(LuTZ),来自各个领域的专家积极推动未来车型的可持续发展。他们在早期阶段就参与到新车型的开发过程中。在兰茨胡特和下巴伐利亚地区,宝马集团兰茨胡特工厂是一个具有社会责任感、创新性和吸引力的雇主。
关于托马斯-科普博士和克劳斯-萨默尔
克劳斯-萨默尔自1985年以来一直是宝马集团的一员,最近曾担任丁格芬工厂的车身涂装规划主管,2018年至2021年担任匈牙利德布勒森在建工厂的车身涂装主管。之后,他接管了宝马集团兰茨胡特工厂轻金属铸造厂的产品和工艺规划管理工作。除了在宝马集团任职外,萨默尔还是多个协会的顾问委员会成员。
2001年至2005年 慕尼黑宝马工厂项目经理2005年至2011年 慕尼黑宝马工厂研发团队主管2011年至2015年 慕尼黑宝马工厂装配和整车验证部门主管2015年至2018年 规划车身车间主管 – 丁格芬宝马工厂2018年至2021年 德布勒森宝马工厂冲压车间和车身车间总经理2021年至2023年 技术中心铸造、工厂列车制造、维护和原型制造以及产品和工艺规划负责人 – 兰茨胡特工厂 托马斯-科普(Thomas Kopp)博士自2016年完成博士学位后一直在宝马集团工作。他目前在轻金属铸造技术中心担任高级开发团队协调员,负责进一步开发用于未来汽车的创新铸造部件。曾任职务包括生产子项目经理以及重力铸造和低压铸造质量团队负责人。除了在宝马集团工作外,托马斯-科普博士还是多个协会的顾问委员会成员。
l 来源:轻量化技术网
知之既深,行之则远。基于全球范围内精湛的制造业专家智囊网络,3D科学谷为业界提供全球视角的增材与智能制造深度观察。有关增材制造领域的更多分析,请关注3D科学谷发布的白皮书系列。
网站投稿 l 发送至2509957133@qq.com