键合参数对电镀金键合性能的影响
王世春 沈若尧 任长友 张欣桐 武帅 邓川 王彤 郭可升 刘宏 郝志峰
(季华实验室 深圳市联合蓝海应用材料科技股份有限公司 广东工业大学轻工化工学院)
摘要:
采用超声波键合对由无氰电镀金和含氰电镀金制备的封装材料进行金丝键合测试,研究了键合工艺参数(超声功率、超声时间、键合压力) 对键合性能的影响。结果表明,采用无氰电镀金液的底材材料硬度高,金丝焊球处发生失效的现象较多,而采用含氰电镀金液的底材材料硬度低,金丝焊球处发生失效的现象较少。对于低硬度的电镀金层,其焊球直径和键合高度都较低,有助于键合金丝和电镀金界面实现更好的融合。超声时间是影响键合性能的主要因素,当超声时间增加至300 ms,金丝焊球不再出现失效,有效解决了键合性能不良的问题。
0 引言
金镀层表面具有抗氧化性好、接触电阻低、导电性能好、可焊性好及耐腐蚀性强等优点,被广泛用于集成电路封装领域。
金丝具备良好的延展性和导电性,且键合后有足够的键合强度,易形成良好的回线形状,因此金丝键合被广泛应用于半导体封装工艺。金丝键合技术采用热压超声键合方式,通过结合热压与超声能量,降低了加工温度,提升了键合质量,同时对提升器件可靠性具有积极影响,是目前主流的键合方法之一[1]。
在封装过程中,金丝键合主要分为球焊键合与楔焊键合,球焊键合具有方向灵活、可靠性高等特点,通过球焊键合首先在芯片表面形成第一焊点,继续在基板上键合第二焊点,可以实现最小化的弧形结构,且每个焊点所占面积都相对较小。影响金丝球焊键合质量的因素众多,从设备角度看,其与超声功率、键合时间和压力等相关;从键合表面角度看,其与表面清洁程度、材料特性及加工过程等紧密相关。影响金丝球焊键合质量的核心因素可归纳为超声功率、超声作用时间以及键合压力[2]。
金丝键合通过超声波能量激发劈刀振动,诱发金丝与芯片表面的金属元素结合,实现金属间的稳固连接。若键合时超声功率过强,金属原子会向外膨胀,在材料内部形成较大的空隙,导致键合区域面积减少以及焊缝强度下降,引起导线塑性变形。若超声能量不足,则无法有效去除键合区域的杂质与氧化物,导致键合强度下降,甚至引发键合作业失败[3]。
在超声功率和键合压力保持恒定的情况下,若超声作用时间不足则无法彻底消除金丝及被焊芯片表面的附着层与氧化膜,原子间未形成冶金结合,导致键合不牢固,容易引发脱黏问题。然而,如果超声作用时间过长,轻微情况下会降低焊点的机械强度,严重时则可能导致焊点损坏。
键合压力是指在焊缝处垂直施加的力,若压力不足,金丝无法实现牢固键合,同时可能引发金丝与劈刀尖端之间的黏附现象。若压力过大,可能会导致金丝的变形程度加剧,甚至引发导线断裂,从而破坏芯片表面的金属层。
本文分别使用无氰电镀金液和含氰电镀金液制备2种金镀层,在此基础上进一步研究金丝超声波键合工艺的影响因素,揭示超声波键合参数(超声功率、超声时间和键合压力)对2种金镀层键合性能的影响。
1 实验方法及设备
1.1 实验基材及设备
本实验使用无氰电镀金液(AURIFAB SC-2000)和含氰电镀金液(AURIFAB SC-3000)制备键合所用的基材。使用无氰电镀金液制备的镀金层基材为无氰样品,使用含氰电镀金液制备的镀金层基材为含氰样品。采用显微维氏硬度测试机(HM-200)测试镀金层硬度。
1.2 实验方案设计
使用直径为34 μm 的金丝进行金丝键合,使用推拉力测试仪(Dage 4000)进行拉线测试。
采用正交实验方法研究键合工艺参数对键合质量的影响,将热台温度设置为200 ℃,选取超声功率、超声时间和键合压力3 个工艺参数作为实验对象,每个参数选取2个因素为变量,表1为键合因素水平表,选用L8(23)表形式,正交实验方案如表2所示,对每组样品进行20次金丝键合。

1.3 键合质量评价
在大规模生产中,对每根键合引线进行拉力破坏实验会造成太大的损耗,因此可通过显微镜观测焊点外形,初步判断键合样品的优劣。在键合实验完成后,记录下每个第一焊点界面的焊球直径D 和键合高度h,图1为焊球参数测量示意图。
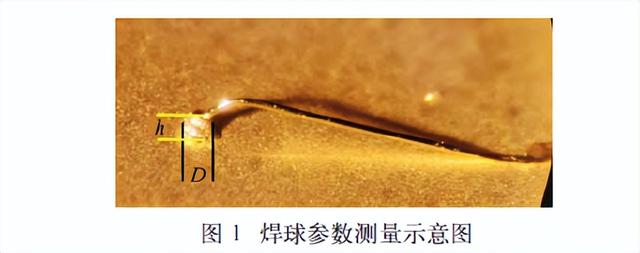
键合质量的好坏最终要通过破坏性实验中的拉力测试来判断。键合拉力测试是常用的检测方法,影响测试结果的因素除工艺参数外,还有键合基材质量、焊盘材质、拉力位点、弧线拉伸高度等。常见的键合引线断裂位置如图2所示,其中要求拉伸引线断点不能在A点(球形键合处)和E点(楔形键合处)2个位置[4]。在抗拉强度测试中,记录下拉力值和断裂模式,出现在A点或者E点的断裂会被判定为键合性能不良。
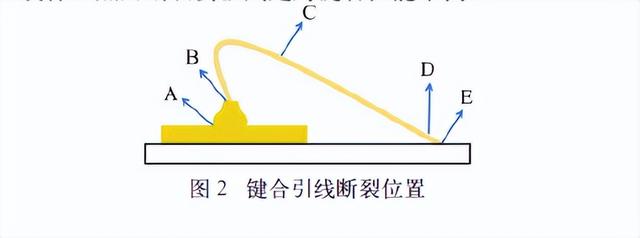
2 结果与讨论
2.1 镀金层硬度测试结果
镀金层的硬度影响封装件的耐久性和稳定性,硬度测试结果如表3所示,无氰样品电镀后的镀金层硬度为130~160 HV,含氰样品电镀后的镀金层硬度为90~120 HV,无氰样品的平均硬度相较于含氰样品高出约40 HV。

2.2 拉力测试下样品失效模式统计
拉力测试失效位置统计结果如图3所示。实验结果表明,所有发生断裂样品的断裂点均位于第一焊点处,表明第一焊点处是最容易发生拉断、键合强度最弱的部位。无氰样品在A点发生失效的比例较含氰样品高出15%,表明无氰样品在键合性能上总体表现较差,这可能与无氰样品的金镀层硬度较高有关,较高的硬度导致金丝不容易被键合。2种样品在E 点都不存在失效现象,这是因为E 点的键合面积比A点大,其结构更为稳定,不容易发生失效。
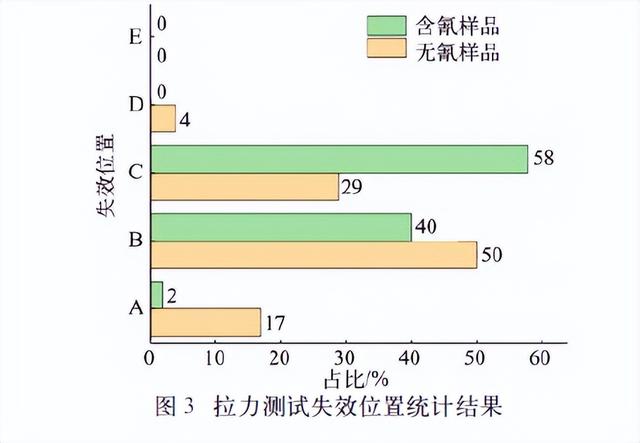
2.3 键合参数对焊点形状的影响
由于拉力测试主要适用于小规模样品的取样,并不适用于工程领域或大规模生产的产品检验,因此通过观察、测量等非破坏性方法进行键合质量评估尤为重要。利用光学显微镜和其他观察方法来记录键合点的形态并测量键合点的尺寸,是评估键合质量的简单、有效的方法。可以通过测量键合点焊球的直径和高度来判断键合质量的优劣[5]。
2.3.1 镀层焊球直径
无氰样品和含氰样品的焊球直径测量结果如表4所示。对比无氰样品焊球直径D1与含氰样品焊球直径D2,结果表明,在参数一致的条件下,大部分情况下D1大于D2。这可能是由于无氰样品的硬度较高,导致在键合过程中金丝很难与底材的电镀金实现共熔。由于未能形成共熔相,金球不得不向外铺展。
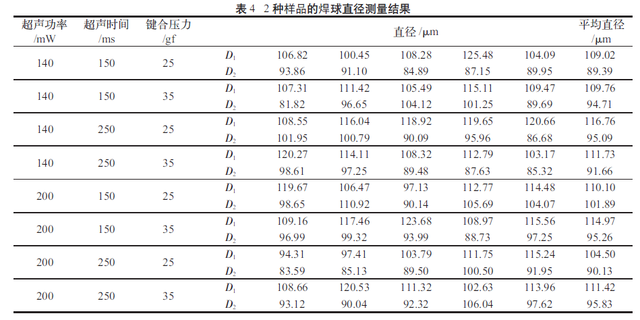
2.3.2 镀层键合高度
2 种样品的键合高度测量结果如表5 所示,对比无氰样品的键合高度h1 与含氰样品的键合高度h2,结果表明,在参数一致的条件下,大部分情况下h1 大于h2。这同样是由于无氰样品的硬度较高,未能形成共熔相。大多数超声能量可能都被用于金丝焊球的形变上,这导致金丝焊球的直径和高度都相对较大。因此,较小的焊球直径和键合高度会提升键合性能。
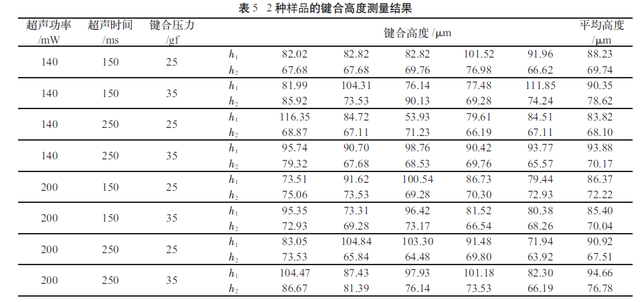
2.4 键合参数对键合拉力的影响
依据正交实验方案,对每组无氰样品分别进行20次金丝键合,拉力测试结果如表6所示。
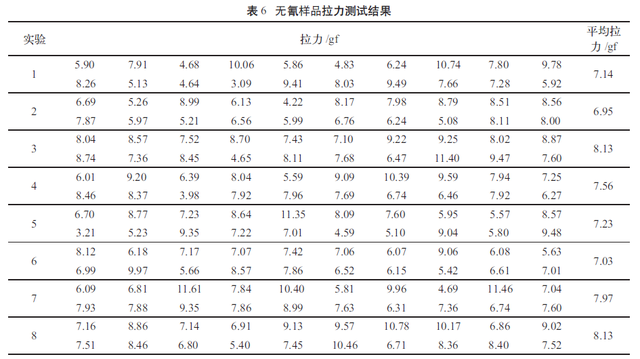
对拉力测试结果进行方差分析,以探究不同因素及其交互作用对拉力值的影响。表7为测试结果方差分析表。
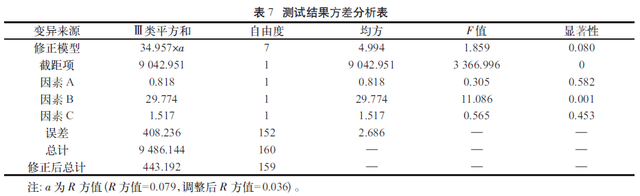
方差分析的结果表明,因素B 对键合拉力的影响较大,因素A 和C 的影响不显著,各因素对金丝键合影响的主次顺序为因素B>因素C>因素A。
表8 为测试结果极差分析表。根据极差R 的数值,可以确定因素对实验指标的影响顺序[8]。进一步的验证结果表明,对无氰样品拉力值影响最大的是因素B,各因素影响的主次顺序为因素B> 因素C> 因素A,该顺序与方差分析的结果一致。实验最佳因素水平如下:超声功率为140 mW,超声时间为250 ms,键合压力为25 gf。

2.5 延长超声时间对无氰样品键合性能的影响
由于超声时间是影响键合性能的主要因素之一,为进一步减少无氰样品的失效,在最佳因素水平下,增设超声时间为300 ms和350 ms 2 个变量,新增40个样品进行实验,拉力值测试结果如表9所示,补充该实验以进一步优化工艺。
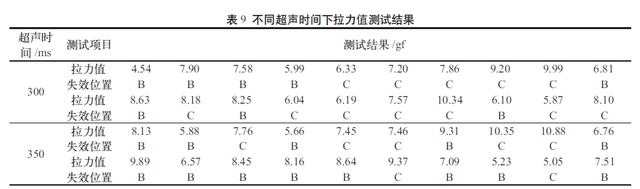
由表9可知,延长超声时间后在A点和E 点并未出现失效现象,因此延长超声时间可以有效降低具有较高硬度的镀金层在A点发生失效的概率。
不同超声时间下焊球直径与键合高度如表10 所示,由表10 可知,相较于250 ms,当超声时间延长至300 ms 和350 ms 时,无氰样品的焊球直径和键合高度总体上会减小,且无氰样品在A点均未出现失效现象,进一步验证了较小的焊球直径和键合高度可以有效地提升键合性能。
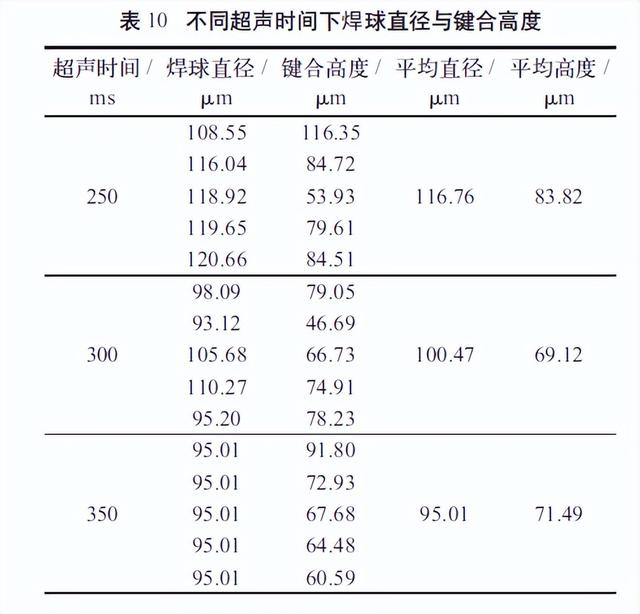
延长超声时间可提升无氰样品的键合性能,这可能是因为在保持超声功率和键合压力恒定的情况下,增加超声时间有利于清除被焊芯片表面的吸附层和氧化膜,原子间的冶金结合更加彻底,从而促使金球与基板之间形成更好的金属间化合物连接。
3 结论
本文对比了无氰样品和含氰样品2种电镀金镀层的硬度,探究了电镀金镀层硬度对键合性能的影响以及工艺参数对金丝键合失效的影响。结果表明,相较于低硬度镀金层,高硬度镀金层出现脱键现象的比例更高,因此高硬度镀金层的键合性能相对较差。对于高硬度镀金层而言,较小的焊球直径和键合高度能提升键合性能。各因素对拉力影响的主次顺序为超声时间>键合压力>超声功率。延长超声时间可以有效减少高硬度镀金层发生脱键的现象。为了进一步深入探究,后续计划采用扫描电子显微镜表征焊球的失效形貌并研究其失效机理。