作者:陈 利 刘金峰 袁锡志 周尚松。
期刊《2021秋季国际PCB技术/信息论坛》
摘要
金线引线键合工艺基于其良好的导电性、稳定性而广泛应用于半导体封装领域。对于半导体封装载体印制线路板而言,优良的表面涂覆方式以及良好的工艺控制能力是引线键合封装良率的重要保障。文章基于行业内化学镍钯金产品在引线键合过程中的常见失效问题,通过系统的机理分析以及试验验证,探究影响化学镍钯金产品引线键合可靠性的关键因子并输出管控方案。
引言
IC封装是芯片由制造转向应用的重要流程,其主要作用在于四个方面:保护、支撑、连接以及可靠性;保护与支撑是对载体印制线路板的基本要求,而连接及可靠性则对工艺方法以及工艺能力提出了较高要求,这方面的失效对于终端设备是致命的,因而对于制程可靠性的分析把控具有重要意义。
连接是芯片与载体印制线路板进行电性导通的过程,主要通过引线键合技术实现,即通过金属线连接导通。金线由于其良好的导电、导热、耐腐蚀等性能,逐渐成为封装领域主流材料;对于载体印制线路板而言,目前有电镀软金以及化学镍钯金两种表面涂覆适用于金线绑定;为满足绑定需求,电镀软金表涂需要提供较高的金层厚度,如此高的金厚不但成本高而且不利于非绑定区域的焊接;而化学镍钯金工艺能够在低金厚条件下,同时具备良好的绑定及焊接性能,因此在封装领域的应用愈发广泛。

封装可靠性直接影响终端产品可靠性,而如何保证可靠的性能则需要对金线引线键合过程以及结构进行深入的分析,金线引线键合的微观结构如图2所示,键合焊点由金线与化学镍钯金焊盘两部分组成,而连接的方式就是通过引线键合。
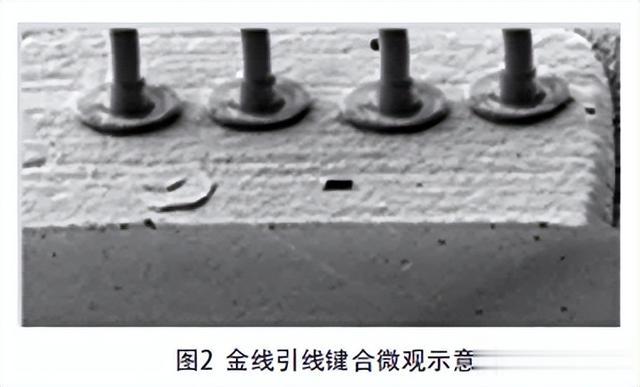
为更清晰系统的了解影响金线引线键合可靠性的影响因素,将化学镍钯金金线引线键合影响因素做树状图分析,如下图3所示,分析各因子的作用以及关键控制点,对于制程整体的认识更为深刻。本文基于目前常见的失效模式分析结果,进行实验验证找出关键控制点,输出提升引线键合可靠性的管控方。
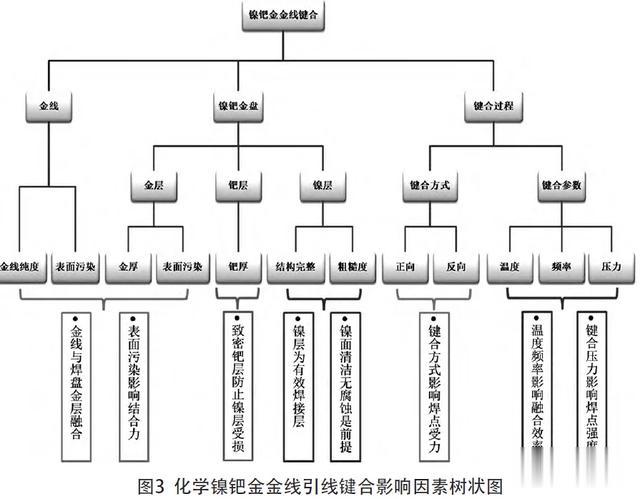
1 化学镍钯金及金线引线键合工艺
1.1 化学镍钯金工艺制程
印制线路板中用于焊接的盘为铜,但是铜在空气中易缓慢氧化为不导电、无焊接能力的氧化铜,因而要对盘面进行表面涂覆处理,以保证连接盘的焊接性能稳定。化学镍金工艺由于金、镍层易迁移扩散导致黑盘,严重影响金线键合可靠性,为解决此类问题而引入了化学镍钯金工艺,其工艺流程如下。

化学镍钯金工艺流程相对于传统的化学镍金工艺,在于镍金层中间多了一层致密的化学钯层,能够有效的阻止金层与镍层的相互扩散,化学镍、钯层均为还原沉积法,不会破坏基底金属层晶格,且相对于化学镍金工艺的置换法沉积金层,化学镍钯金工艺采取半置换半还原的沉积金工艺,减少对镍层的侵蚀,有效保证了镍层可靠性。
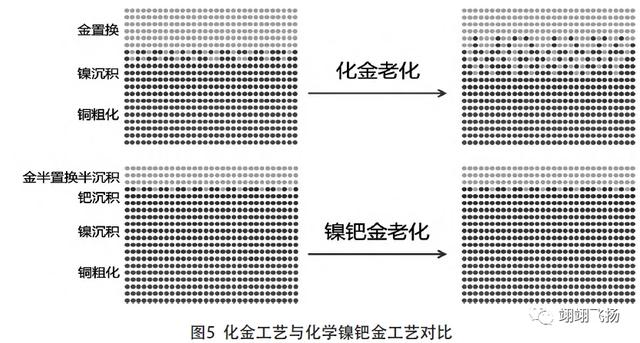
分解化学镍钯金工艺关键流程步,能够更为清晰的了解化学镍钯金品质控制关键要点:
(1)除油:铜面清洁,除去铜面脏污、氧化的同时一定程度上活化铜面;
(2)微蚀:铜面粗化,铜面的微观形貌直接影响化学镍钯金成品表面形貌,粗糙的铜面能够吸附沉积镍所需的钯离子,并提升铜镍金属间结合力;
(3)化学镍:采用次磷酸钠还原镍离子沉积在铜面,同时焊接、打线过程直接受力点在镍层,为保证焊点可靠性,需要保持镍层良好的晶型结构;
(4)化学钯:钯离子还原沉积在镍层表面形成致密的钯层,性质稳定,作为中间层分隔镍层与金层,防止黑盘现象的发生;
(5)化学金:采用半置换半沉积药水体系,轻微置换填充缝隙后自沉积金层,相较于化金工艺需要的金层较薄,同时不会破坏镍层结构。
通过上述流程分析,化学镍钯金工艺镀层结构较为复杂,层间的结合力也是影响化学镍钯金品质的关键因素。
1.2 金线引线键合过程分析
化学镍钯金金线引线键合过程[4]可以简化如图6所示:
(1)磁头加热熔出金球;
(2)金球下降至焊盘形成第一焊点;
(3)磁头按轨迹牵引金线至另一焊盘,下压并通过振动、温度形成焊接作用,形成第二焊点。

上述图示为引线键合宏观过程,但要分析键合可靠性,需要立足于微观结构分析焊点的形成过程,目前金线引线键合工艺一般采用热超声法,其焊点形成过程如图7所示:
(1)金线与焊盘接触,形成局部连接;
(2)在持续压力与超声震动下,扩大接触面,金填充焊盘表面较大缝隙;
(3)高温作用下降低金球表面张力,填充细微缝隙的同时焊盘表面金、钯层溶解;
(4)金属原子层间发生相互扩散,金属间隙消失形成焊点。
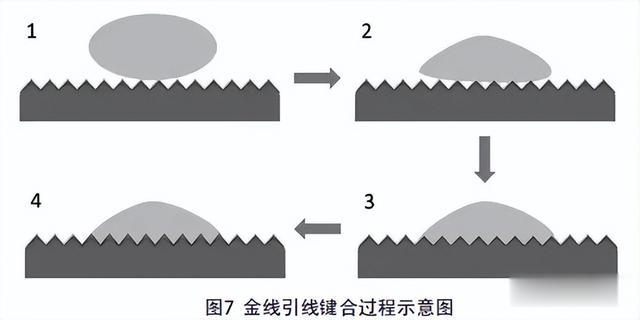
2 化学镍钯金金线引线键合可靠性控制点
在了解化学镍钯金以及金线引线键合工艺过程以及原理的基础上,通过分析目前化学镍钯金金线引线键合遇到的失效问题,梳理异常产生的可能原因并验证。
2.1 化学镍钯金金线引线键合失效模式
金线引线键合的品质确认一般采用键合后拉力测试的方式进行,金线拉力测试方案如图8所示,通过拉力确认键合质量,对于印制线路板而言,测试拉力>3 g且失效模式正常则认为键合效果合格,拉力越大表明键合效果即可靠性越好。

在上述测试标准下,目前主要的失效模式有以下三种:
(1)金线拉脱,而化学镍钯金焊盘表面金层无或少量打线痕迹;
(2)金线拉脱,顺带拉脱焊点部分金层,焊点部分露镍;
(3)金线未拉脱,而在拉力作用下铜镍层间发生分离而失效。
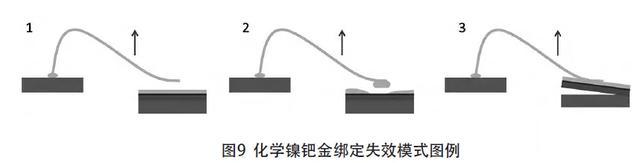
2.2 引线键合拉力失效关键因子梳理
2.2.1 失效模式1分析及控制
失效模式1主要表现为金线拉脱焊盘,分析打线过程可知金线与化学镍钯金金层未能融合或少量融合,导致焊点未完全形成,焊接不良。而金线与化学镍钯金金层的融合过程为金属原子相互扩散的过程,可以将问题视为扩散过程受到阻碍。而影响金镀层性能的原因包括金镀层遭受破坏(划伤、氧化、变形、镀层污染等)以及镀层性能发挥遭到阻碍(镀层结合力不良、粗糙度不合理等)两个方面。
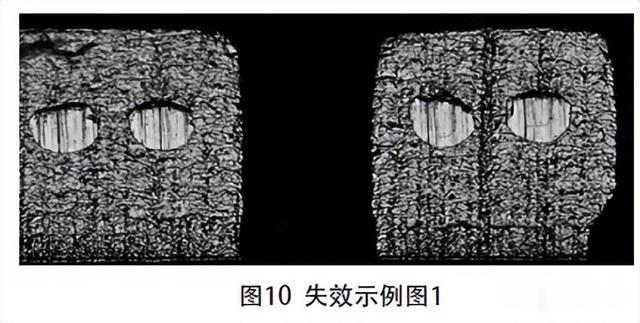
表面脏污、划伤、氧化一般来自于化学镍钯金后制程不规范导致,规范清洁流程以及外观检验即可。印制线路板的焊接工艺一般是先进行器件回流焊接,再进行金线引线键合,因而镀层污染分为两种
1、金层沉积厚度不合理或化学金药水槽受到污染,沉积金层参杂其他元素(金槽为高价值槽体,日常监控频繁,此类异常较少发生);
2、化学镍钯金产品钯层厚度不足起不到良好的隔离作用,导致热回流过程中金镍原子迁移,破坏镀层;
另外金线焊接过程的第一步是需要填充表面缝隙,当焊盘表面粗糙度超出合理范围亦可能导致焊接性能降低。
相对于化金工艺,化学镍钯金的主要优势在于增加了钯层以隔离金镍层的原子交换,而合适的钯层厚度是此类隔离性能的保障,如下图11所示。

钯层厚度与打线拉力强相关,在钯厚不足的情况下甚至会出现单点NG的现象,对比0.03 mm与0.3 mm钯厚化学镍钯金焊盘经回流、剥金后SEM图片,如图12所示,薄钯板镍层相对于厚钯板呈现更加明显的晶格间隙,与上述理论相符。
因此在性能与成本的综合考量下,建议钯厚控制在0.1~0.3 mm区间范围。

金层作为保护层,不论是对于化学镍钯金焊盘结构完整性的防护还是对于打线过程焊点的形成都具有重要作用,因此合适的金层厚度是焊接性能的良好保证。因此测试对比不同金厚的引线键合拉力结果(固定钯厚为0.2 mm),结果如下图13所示,金厚在一定范围内引线键合拉力较为接近,表明化学镍钯金键合性能不是与金涂覆层厚度强相关。
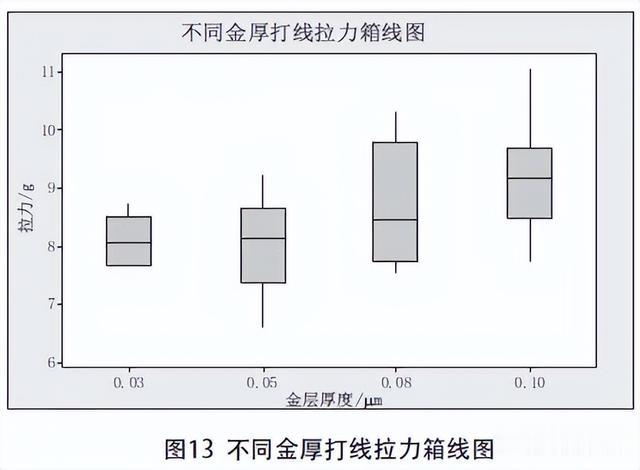
化学镍钯金焊盘表面粗糙度会影响沉镍催化剂钯离子的吸附以及铜镍接触面的鳌合程度,而粗糙表面同时意味着引线键合过程金线浸润时间要增长,影响金线引线键合效果,因此粗糙度对于化学镍钯金镀层沉积以及键合可靠性的影响尤为关键,以下为不同的表面粗糙度下金线引线键合拉力表现情况如下:
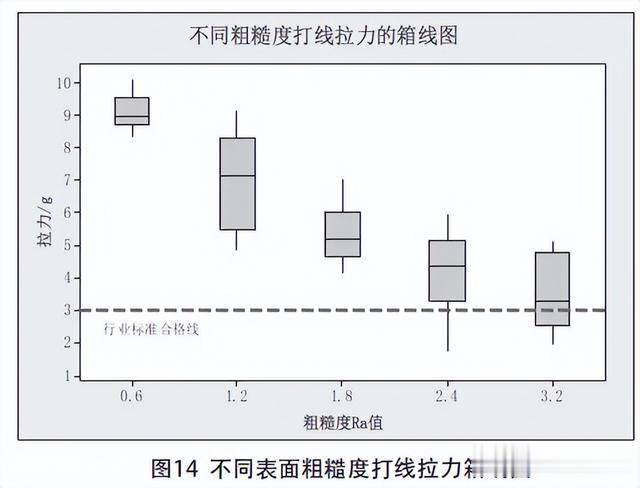
通过图14可知,表面粗糙度与引线键合拉力在一定区间内反向强相关,主要原因在于粗糙度大金线绑定初期接触面积小,键合需要填充的空间更大,影响键合效果。由上述分析可知,在保证镀层结合力的前提下,为确保良好的金线引线键合性能,建议表面粗糙度控制越小越好。
2.2.2 失效模式2分析及控制
失效模式2主要表现为引线键合过程中PCB焊盘金层拉脱,通过引线键合过程可知,该失效情况属于金线与焊盘表面金层融合后,再与钯镀层融合或与镍镀层消除缝隙过程中受阻,导致金线从焊盘表面抽离过程中拉脱焊盘镀层;焊盘镀层拉脱缺陷状态如下图15所示,通过对镀层拉脱后裸露部分及拉脱卷起部分进行元素分析,镀层拉脱后底层部分无钯金元素,说明钯层与金层同步拉脱,而卷起部分则含有较高的钯金元素,由此可知主要问题发生于金线与镍层形成焊点的过程中。通过FIB观察失效位置与正常位置对比发现,失效位置有严重镍腐蚀,如下图16所示。
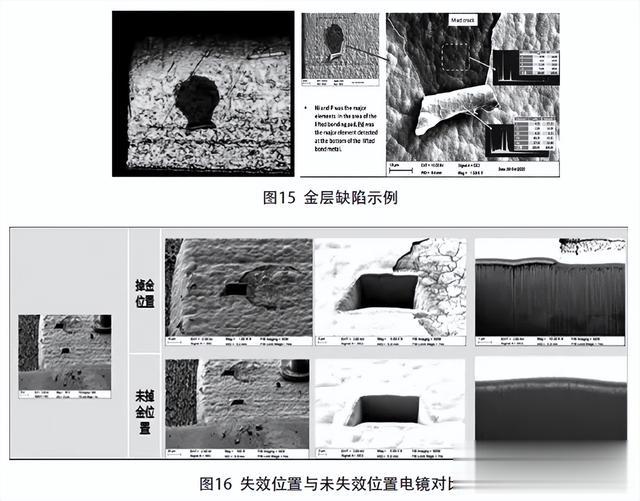
通过上述分析可知此类引线键合过程中金钯层剥落的缺陷是由于镍层可靠性不良导致,而影响镍镀层可靠性的因素主要包括两个方面,镍层晶格完整性以及表面污染。化学镍到化学钯的具体流程如下图17所示,化学镍沉积镍层,水洗清洁镍面,化学钯沉积形成致密金属层防止镍层受侵蚀。

镍层的完整、清洁需要上述三个流程的稳定控制,但是镍面受损、污染最直接也最容易忽视的原因在于水洗流程。化学沉积镍层表面活性较高,水洗过程中产生的细微波动都会对镍面性能产生致命影响。水洗流程的作用是清洁镍面,防止槽体交叉污染,清洁效果与对镍面的冲击需要形成良好的平衡,最为直接的水洗参数包括水洗时间以及清洁度。水洗时间的长短意味着高活性的镍层暴露在外时间的长短,长时间的暴露无疑会增加镍层氧化腐蚀的风险,通过对比分析镍后水洗时长与引线键合良率之间的关系,如下表1所示。
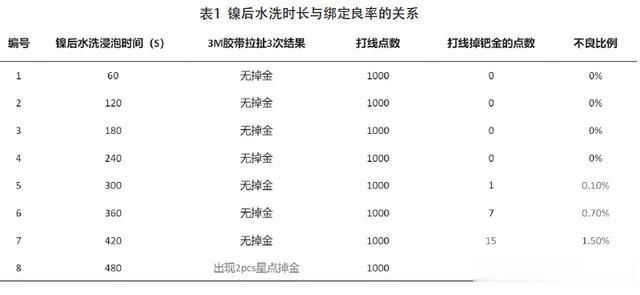
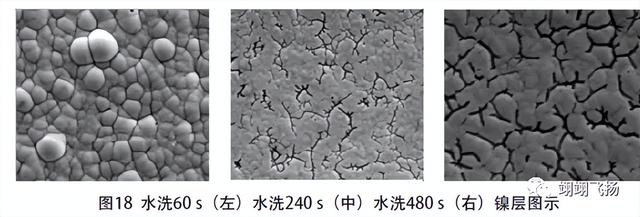
水质良好的情况下水洗时间到达300 s时金线绑定呈现一定的失效概率,通过上述电镜图18可知长时间的水洗浸泡对镍面晶格造成了严重的破坏。同时水洗的作用在于清洁板面残余的镍缸药水,从而水洗槽极易受到污染,分析污染与镍层破坏的关系,可以进行不同电导率条件下的水洗验证,设定水洗时间为120 s,通过分析镍后水洗水质对于引线键合良率的影响,如下表2所示。
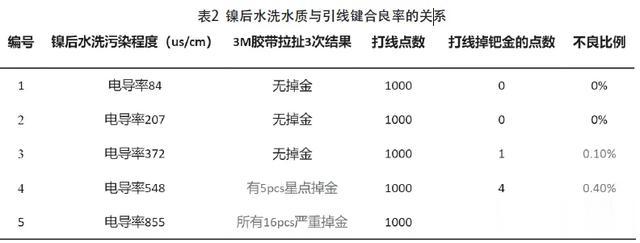
相同水洗时间下,水质对于镍层可靠性具有直接影响,水质越差,镍层可靠性遭到破坏的比例越高。在现有水洗时间、水质要求的规范下,是能够保证镍层的完好性能。但是由于水洗水质监控周期不足,或者水洗流程步妥协于其他关键流程步,导致水质失控或者水洗时间超标,影响镍层可靠性,因而输出控制方向如下:(1)针对镍厚水洗槽设置在线水质监控以及定时自动换水;(2)天车程序优化,设置固定的水洗浸泡时间以及空气中停留时间;
2.2.3 失效模式3分析及控制
失效模式3主要表现为焊点完好,而在拉力测试过程中拉脱部分镍层,说明镍层与铜层间的结合力不足,分析化学镍前流程,主要作用为清洁、粗化铜面,清洁、粗化效果都直接影响到铜镍结合效果。在现有的流程体系中,轻微的铜层氧化、油污都能够有效的去除,而有些不易观察到的缺陷才是影响金线引线键合可靠性的关键因素。梳理现有的键合异常,主要原因为前流程脏污残留。这里的前流程脏污残留具有不易发现、不易去除的特性,其缺陷产生现象如下图19所示,不仅打线位置出现异常,未打线位置也出现掉金现象。
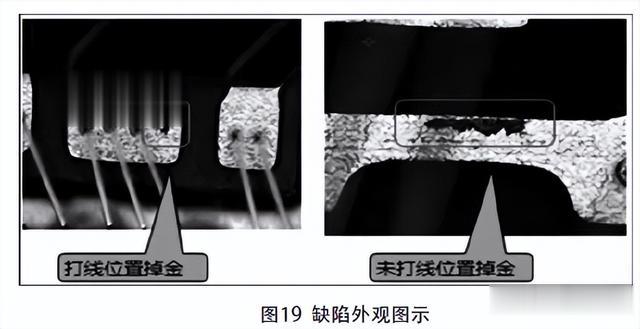
这类缺陷位置进行EDS分析,结果如下图20所示,缺陷位置未见其他杂元素,仅发现C、O元素含量偏高,梳理印制线路板流程,造成此类异常的原因为板件残胶,影响铜镍结合力。
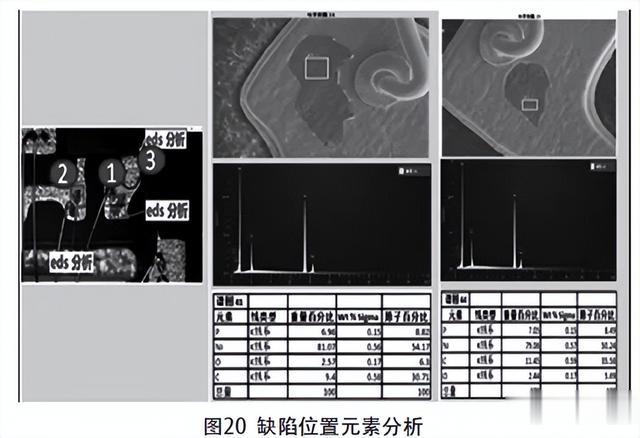
这一类异常的现象分析有时会受到其他元素的干扰,如下图21所示,缺陷位置EDS分析发现较大比例的Al元素,而Al元素来源于化学镍钯金前处理的金刚砂(Al2O3),而金刚砂本身对于铜面无吸附能力,在经过多次清洗粗化处理后,出现在金属层间,表明此类金刚砂残留异常是残胶粘附导致的。

残胶的来源有两个方面,1、前流程板件贴胶带而后续未能进行有效清洁,导致残胶;2、线体带胶带过板,残胶吸附在滚轮上污染后续板件。这类残胶难以察觉,在异常发生前板件外观几乎无异常,对板件性能的影响却非常致命。因此输出以下管控方向减少残胶:
(1)减少前制程胶带的使用,对于必要使用的板件注意清洁板面;
(2)严格限制板件在贴胶带状态下过水平线,注意清洁周期。
2.3 小结
本章系统梳理了化学镍钯金金线引线键合可能产生的缺陷,通过流程及机理分析确定关键控制点,并给出了相应的管控措施建议。
3 金线引线键合过程控制点
3.1 金线引线键合关键因子梳理
金线引线键合工艺的目标在于形成稳定可靠的焊点,基于上述焊点的形成过程,可以发现焊点的可靠性来源于各金属层间的熔融扩散效果,其直接影响因素为温度、超声频率,目前行业内研究较为广泛,但是打线过程整体的键合压力与过程拉力的交叉影响易受忽略。
金线引线键合的压力对于焊点的面积具有直接影响,从而影响到焊点的结合力;而金线引线键合的目的在于导通印制线路板绑定盘与芯片,因而焊接方式基于其顺序分为以下两种,1、第一焊点为芯片上焊盘,第二焊点为印制线路板上绑定盘,按此顺序键合称为正打方式;2、第一焊点为印制线路板上绑定盘,第二焊点为芯片上焊盘称为反打方式。
两种方式对于印制线路板绑定盘的受力具有微小差异,但是此受力过程在上一个焊点的形成初期,因此对于焊点的结合效果的影响需要慎重评估。
3.2 金线引线键合压力与打线方式交叉验证
通过上述影响键合可靠性因素梳理,选择金线引线键合压力与打线方式进行DOE交叉验证,验证方案与不良率表现结果如下表所示:

对上述DOE结果进行分析,R-Sq值为92.18%,结果可靠,通过主效应图可知,打线方式以及键合压力均与金线引线键合不良率呈现明显的相关性,且交互作用图显示两者呈现一定的交互影响。
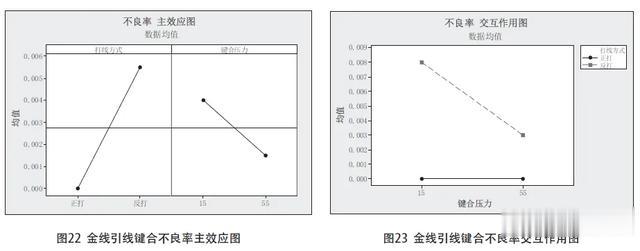
通过上述交叉验证分析,键合压力与打线方式均为关键影响因素,打线方式的影响斜率大于键合压力斜率,基于上述分析,为保证化学镍钯金金线引线键合焊点可靠性,优选正打方式键合,在工艺限制需要反打时,建议提升键合压力以保证键合良率。
3.3 小结
本章通过DOE分析了金线引线键合中键合压力、打线方式与键合掉金的关系,通过主效应以及交互作用的分析,输出提升引线键合良率的方向是采用正向打线方式以及适当提升打线压力。
4 结论与展望
化学镍钯金工艺应用于金线引线键合领域具有其独特的性能及成本优势,但是其性能优势的发挥需要对于化学镍钯金制程机理、金线引线键合过程的细致拆解、分析,分析化学镍钯金金线引线键合过程中可能发生的异常,基于化学镍钯金制程及金线引线键合机理,梳理异常现象的根因,从而快捷有效的输出对应的关键控制要素以及控制措施,快速解决过程异常。在过程中提升控制能力,以提升化学镍钯金金线引线键合可靠性。