光刻工艺中增粘剂的失效分析
孙洪君 吕强 韩洋 王浩然
(沈阳芯源微电子设备股份有限公司)
摘要
六甲基二硅氮烷(hexamethyldisilazane,HMDS)是常用于集成电路光刻工艺中硅衬底晶圆增粘处理的化学试剂。在高温下,HMDS与衬底表面氧化层键合,将硅衬底表面从亲水变为疏水,使衬底表面可以很好地与光刻胶结合。本文对涂覆HMDS的晶圆进行失效分析,并探究HMDS的持久性对涂胶工艺的影响,结果表明,对于不同性质的光刻胶,有无HMDS对涂胶工艺的影响不同。硅衬底表面的HMDS需要经过化学清洗等方法才能去除,简单的空气中静置或光刻胶溶剂清洗不能够将其完全去除,研究结果可为光刻工艺缺陷问题提供数据支撑。
0引言
集成电路(integratedcircuit,IC)芯片作为信息技术的基础之一,已经广泛地融入人们生活的各个方面。大量资金和人力物力的投入,导致半导体生产高昂的分摊成本,加之竞争激烈,产品价格持续下滑,这驱使大部分芯片生产厂持续运行在大规模量产、高产品良率的水平上。维持并提高产品良率对半导体工艺生产至关重要[1]。随着器件的掩模版图形越来越复杂(图1),图形面积也越做越大,然而线条要求却越来越细,器件性能和精度要求也越来越高。
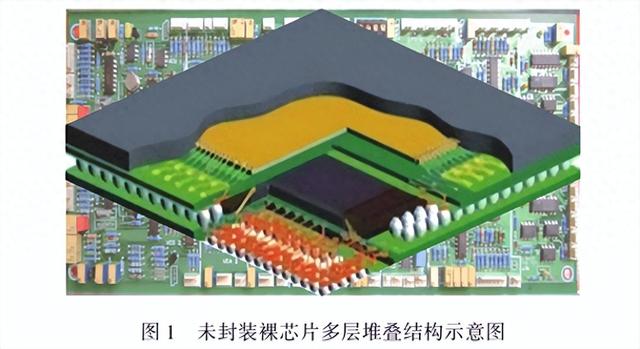
在整个IC芯片制造过程中,光刻工艺是关键工序,其中涂胶工艺是光刻工艺中最为基础的工序之一。产品晶圆上光刻胶涂覆的好坏,决定了产品良率的高低。因此,为了减少光刻胶涂覆工艺过程中的缺陷,产品晶圆在涂覆工艺之前会经过一系列表面预处理,包含化学湿法清洗、干法刻蚀、脱水烘焙等。经过预处理的晶圆表面并不完全适用于光刻胶的涂覆,有些经过预处理后的晶圆表面是亲水的,即水溶液或水基溶液在其表面的流动性相对较大,有些晶圆表面是疏水的[2]。而大多数光刻胶都是不亲水的,所以需要额外对晶圆表面进行增粘处理,用来增加衬底表面疏水性,增加表面光刻胶吸附能力,使晶圆与光刻胶更容易结合,减少光刻胶涂覆工艺过程中缺陷的产生,图2展示了增粘处理对产品表面图形的影响[3]。
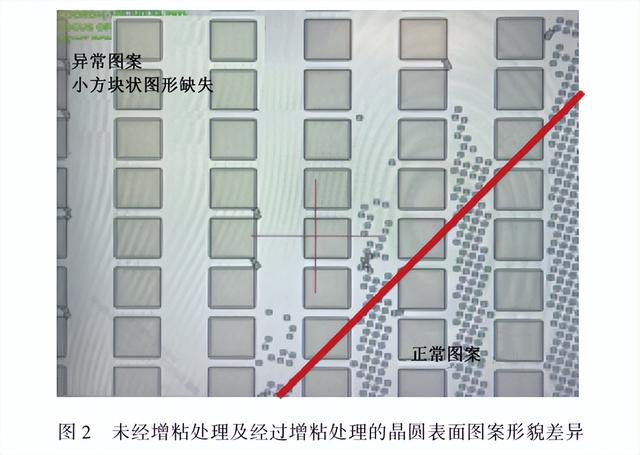
1实验方法
1.1理论背景
硅衬底晶圆在空气中极易氧化,表面形成一层SiO2薄膜,SiO2层具有亲水性,空气中的水分子易于吸附在其表面。然而,大多数光刻胶是疏水性的,这就造成了光刻胶和衬底的粘合性较差。因此,硅衬底晶圆表面经清洗预处理后,需要通过增粘处理才能执行光刻胶涂覆工艺步骤。六甲基二硅氮烷(hexamethyldisilazane,HMDS)是集成电路光刻工艺中硅衬底晶圆常用的表面增粘试剂[4],常温下,HMDS为无色澄清液体,易燃,必须密封使用,半导体工业中所用的HMDS纯度应大于99.70%[5]。但HMDS毒性较大,使用过程中需要做好安全防护,穿戴好化学品防护用具,按照标准操作说明书进行操作。在高温下(约120℃),HMDS与衬底表面氧化层键合,将H2O置换出来,使硅衬底表面由亲水性变为疏水性(图3),进而使衬底表面可以很好地与光刻胶结合。
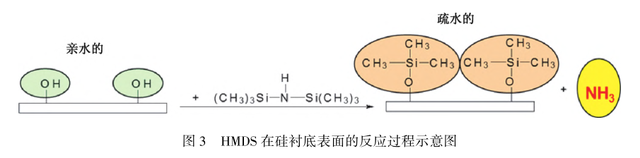
增粘效果的好坏可由晶圆表面的水接触角表征。常规涂胶工艺下,经增粘处理后的晶圆表面,水接触角大小一般为大于65°~70°(图4),而且基于均匀性要求,不同测量点的水接触角数值变化范围不能超过5°,而未经增粘处理的晶圆表面,水接触角大小为0°~20°。

光刻胶涂覆工艺过程中,通常将HMDS以气相引入,在相对较高的环境温度下,直接喷淋在晶圆表面。增粘处理后的晶圆需要立即被传送到涂胶单元进行光刻胶涂覆,否则,长时间暴露在空气中,HMDS易发生水解,使晶圆衬底表面的疏水性失效。HMDS的增粘处理工艺几乎贯穿整个芯片生产流程,尤其是在光刻工艺过程中扮演着重要角色。因此,HMDS增粘效果的持久性一直是光刻工艺研究的重点内容。根据HMDS的相关特性,本文主要对涂覆HMDS的晶圆进行失效分析,同时探究HMDS的持久性对涂胶工艺的影响,记录并统计水接触角测量数据,按照式(1)对晶圆表面接触角均匀性进行计算。

式中,MAX表示测量出的接触角的最大值;MIN表示测量出的接触角的最小值。
1.2测量方法
本研究采用KSM-FT涂胶显影设备,使用增粘单元(图5)进行HMDS涂覆,使用涂胶单元进行光刻胶涂覆工艺。使用OCA25L或OCA20XL接触角测量仪进行晶圆水接触角测量。使用KLA光学膜厚仪KTCD100设备进行光刻胶薄膜厚度测量。
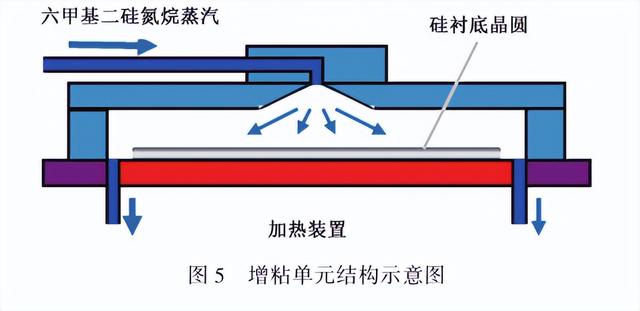
硅衬底晶圆表面水接触角测量步骤如下:①将完成增粘工艺的晶圆水平放置在接触角测量仪的样品台上,打开测量软件并进行设备初始化;②开始水接触角测量,设定滴液2~3μL,移动样品台,通过实时监测窗口观察wafer与液滴的镜面成像,使待测晶圆接触液滴,液滴在表面张力的作用下脱离针头,滴落在待测晶圆测量点上;③进行晶圆表面液滴的左右接触角测量,测量结束保存结果。通常情况下,水接触角测量设备可以设定自动固定点位测量配方,也可以手动对非固定点位进行测量。
本研究使用硫酸和过氧化氢去除晶圆表面的有机或无机污染物,将晶圆进行等离子体灰化,使得晶圆表面不会发生多余的氧化反应。本研究共计设置3组实验,实验所用晶圆都经过同样的前期处理,避免由于晶圆表面状态差异造成的实验结果偏差。实验设置如下:①N片晶圆在同条件下进行HMDS增粘处理,分别在FOUP盒子和空气中静置1h、2h、3h、6h、12h,以此类推至7×24h,测量其水接触角变化,观察静置过程中,晶圆表面HMDS的持久性。②N片晶圆在同条件下进行HMDS增粘处理,测量不同清洗次数(1、2、3、5、8、10、15、20、30、50次)条件下,晶圆表面的水接触角变化,观察溶剂清洗是否能清除晶圆表面的HMDS,并记录数据,对比不同区域的接触角变化情况。③N片晶圆在同条件下进行HMDS增粘处理,同等条件下进行光刻胶涂覆工艺,并测量晶圆表面光刻胶厚度。将涂覆后的晶圆使用对应溶剂进行不同次数(1、2、3、5、8、10、15、20、30、50次)清洗后,再次进行光刻胶涂覆,并测量晶圆表面光刻胶厚度,观察多次清洗对晶圆表面粘附性及光刻胶薄膜膜厚的影响。
2结果与讨论
2.1晶圆表面HMDS的持久性
结果显示,HMDS在短时间内(2~6h)并未完全消散失效,6h后接触角数值大小及均匀性变化不大。3个月内每周进行一次测试,结果发现晶圆表面接触角数值减小,波动范围在10°~30°,均匀性下降40%~50%,而且空气中静置的晶圆接触角变化比在FOUP盒中静置的晶圆变化大。因此,虽然理论上HMDS暴露在空气中2h左右失效,但实验数据得到,硅晶圆衬底表面HMDS增粘处理后,在不进行其他外部处理的情况下,需要很久才能完全消散失效。
2.2清洗溶剂对晶圆表面HMDS的影响
本研究采用的清洗溶剂是30%丙二醇甲醚醋酸酯与70%丙二醇甲醚配制的混合溶液(3∶7,V/V)的稀释液,清洗一次消耗80mL,清洗时长为86s。测量水接触角结果发现,清洗次数较少时,晶圆水接触角变化并不明显,变化数值在1°~3°,而且中心接触角大小低于边缘区域,这可能是中心定点冲洗方式导致。清洗次数增多后,晶圆水接触角数值明显降低,降低幅度在5°~20°,但并未达到未涂覆HMDS时水接触角数值。
此外,本研究还对比了加大溶剂清洗液的冲洗流量至300mL/min时,测试水接触角变化,结果发现,同等时间内,大流量冲洗比常规流量(80mL/min)冲洗,晶圆表面水接触角随冲洗次数增加的变化更大,在5°~15°。经过长时间大流量冲洗,HMDS增粘处理后的晶圆水接触角明显降低,降低幅度在10°~30°。
2.3多次清洗对晶圆表面粘附性及光刻胶薄膜膜厚的影响
将未经过增粘处理的晶圆在同等条件下进行相同的光刻胶涂覆工艺,并测量晶圆表面光刻胶厚度,作为实验中膜厚对比基准。结果发现,对于涂覆某底部抗反射涂层(bottom anti-reflection coating,BARC)光刻胶,薄膜厚度标准为1000Å,而晶圆衬底经HMDS处理后,光刻胶薄膜厚度变化波动不大,为0~10Å,其原因可能是未烘烤的BARC类光刻胶的分子结构具有亲水性,烘烤具有疏水性,可以很好地涂覆于感光性光刻胶(photo resist,PR)或聚酰亚胺类(poly imide,PI)光刻胶与晶圆衬底之间。经过多次清洗后,再次涂覆光刻胶发现,薄膜厚度有所降低,这是由于溶剂的多次清洗,使得溶剂分子在晶圆表面残留,造成了光刻胶的稀释。
对于涂覆某AZ系列PR光刻胶,薄膜厚度标准为8500Å,涂覆HMDS晶圆后,光刻胶薄膜的厚度比未涂覆的晶圆厚50~200Å。根据2.2节可知,随着清洗次数增多,HMDS的增粘效果逐渐减弱,那么薄膜厚度也逐渐与未经过增粘处理的晶圆表面薄膜厚度接近。相比于涂覆某I-line系列PR光刻胶,经HMDS处理的晶圆表面光刻胶的均匀性比未涂覆的晶圆均匀性更好,但薄膜的整体厚度变化不明显。经过多次清洗后的晶圆表面薄膜厚度与未经过增粘处理的晶圆薄膜厚度和初始薄膜厚度基本相差不多。可见,对于不同性质的光刻胶,HMDS的影响不同。
3结语
本文对涂覆HMDS的晶圆进行了失效分析,同时探究了HMDS的持久性对涂胶工艺的影响。结果表明,对于不同性质的光刻胶,有无HMDS对涂胶工艺的影响不同。硅衬底表面的HMDS需要经过化学清洗等方法才能去除,简单的空气中静置或光刻胶溶剂清洗不能够将其完全去除,这有可能对后续工艺结果造成影响。