金锡合金密封空洞控制技术研究
田爱民 赵鹤然
(中国电子科技集团公司第四十七研究所)
摘要:
金锡合金密封工艺广泛应用于高可靠军用电子元器件产品上,对密封空洞的控制有很高的要求,基于此,以某型号控制电路需求为依托,针对陶瓷气密封装的密封空洞控制技术,研究了影响密封空洞的基本前提和关键因素。提出了焊料环设计、焊接气氛、原材料表面状态是决定密封空洞能否被有效控制的基本前提。在焊接峰值温度和焊接压力两个关键因素上进行优化方法对比实验,得出了最佳的提高密封空洞控制水平的有效方法。成果推广到多种封装形式上,有助于提高军用元器件密封质量,可广泛应用于航空航天和空间设备仪器的核心电路封装中,在行业内具有一定的指导意义。
1 引 言
金锡合金密封是高可靠性集成电路封装行业内的主流密封技术,具有焊接强度高、耐腐蚀性强、气密性良好的特点,广泛使用在航空、航天、导弹、船舶等高可靠元器件上。对于航天和军用产品气密封装,主要关注气密性、内部气氛、焊接强度、密封空洞等方面,随着密封技术的不断提升和设备能力进步,大多数问题都已解决,成品率得到很大提升,但是在密封空洞控制技术上还没有形成统一明确有效的控制方法和技术标准。
密封空洞是一种较为常见的封装质量隐患,它的存在会使产品的密封强度和气密性降低,随着服役时间的延长,极易诱发多种致命的失效模式。引起密封空洞的因素有多种,包括温度曲线、焊接压力、原材料表面状态、焊料环设计、焊接气氛等。近年来随着 X 射线设备的普及和宇航级半导体集成电路通用规范的推广,行业内大多数用户都对密封空洞控制提出了明确的要求。
以某型号控制电路的需求为依托,主要研究陶瓷气密封装的密封空洞控制技术,分别阐述密封空洞控制的基本前提和主要因素,总结各种常见失效现象的原因和机理,提出一种有效规范的密封空洞控制方法。
2 密封空洞的影响因素
2.1 焊料环设计
与管壳密封区相匹配的焊料环设计是控制焊接空洞的基本前提之一。
在低温烧结密封过程中,焊料环的宽度决定了焊料融化后可以有效铺展的范围。
如果焊料环的宽度相对于密封区域过窄,在密封过程中,熔融焊料由于总量不足,无法填满整个密封区域,必然会在边缘或者内部形成密封空洞,一些部位的焊料层厚度也会明显比周围的区域要薄,这就对密封可靠性造成非常大的隐患;如果焊料环的宽度相对于密封区域过宽,焊料总量过于充分,受热熔化后势能增大,极具铺展性,固化后,往往会溢出密封区域,甚至爬到盖板表面。
2.2 焊接气氛
良好的焊接气氛也是控制焊接空洞率的基本前提之一。
根据金锡合金的氧化机理,氧易与金锡合金中的锡反应生成金属氧化物,在表面形成氧化膜,反应过程如下式所示。

氧化膜在密封过程中阻碍熔融焊料与金属镀层之间的浸润,导致焊料熔融状态铺展不良,形成焊接空洞。
控制焊接气氛的核心要素有两个,一是保护气体的纯度,二是焊接炉腔体内抽真空的真空度。这两个因素共同作用,可以有效避免焊接过程中焊料的氧化。
2.3 原材料表面状态
表面状态不良对焊接空洞有较大影响,包括表面沾污、划伤、氧化、镀层缺陷、平整度等因素,都会阻碍焊料的流淌和浸润。良好的表面状态也是控制焊接空洞的基本前提之一。
可采用外部目检将镀层缺陷、表面沾污、划伤等不合格品剔除。进一步,采用等离子清洗对管壳表面和盖板焊料环表面进行清洗,以去除原材料表面的氧化物和有机物 。
2.4 温度曲线
焊接温度曲线是控制焊接空洞的核心要素之一。
温度曲线的精确设计,相当于是对焊料融化和流淌过程的精确控制。在焊接温度设计中,温度过高或者加热时间过长,焊料熔融剧烈,流淌性很强 ,部分焊料会溢出封焊区域,造成密封区内焊料不足,进而形成空洞;反之,焊料熔化不充分,熔融后的焊料较脆,铺展效果不好,边缘区域的焊接效果无法保证,多发空洞现象。
2.5 焊接压力
焊接压力也是控制焊接空洞的核心要素之一。焊接压力,与焊接温度、焊料状态之间存在微妙的平衡。一方面,焊接压力的施加,可以弥补焊接温度、焊料状态等因素的设计缺陷,对焊料提供铺展的驱动力,加强焊料的铺展作用。另一方面,焊接压力与空洞的控制关系非常密切,适当的加压一方面可以使母材和焊料形成紧密的接触,有利于金镀层与金锡焊料之间扩散反应的进行;除此之外,由于焊料受到挤压沿着焊接面间隙外溢运动,可以排除焊料中吸附的气体成分,从而降低密封的空洞。
3 密封工艺优化方法及实验结果
3.1 密封空洞控制的前提
在 2.1-2.3 中已经提到,焊料环的设计、焊接气氛的控制、原材料表面状态是控制密封空洞的前提。上述三个因素如果出现异常,密封效果会出现较大的偏差,在比较严重的情况下,不但密封空洞难以控制,还会衍生出新的失效模式。
(1)焊料环优化设计
要想确保密封完成后焊料在合理范围内流淌,焊料环宽度 ε1,焊料环距密封区内侧距离 ε2,盖板外侧密封区宽度 ε3,三个宽度必须符合一定的比例,且倒角设计要求密封区内侧倒角与焊料环内侧倒角半径一致,密封区外侧倒角与焊料环外侧倒角半径一致,如图 1 所示。经过大量实验总结出,ε2 在0.005-0.010 英寸,ε3 在 0.010-0.015 英寸。ε1、ε2、ε3 的比例关系是焊料环设计的关键,不同生产线应有不同的控制规范。
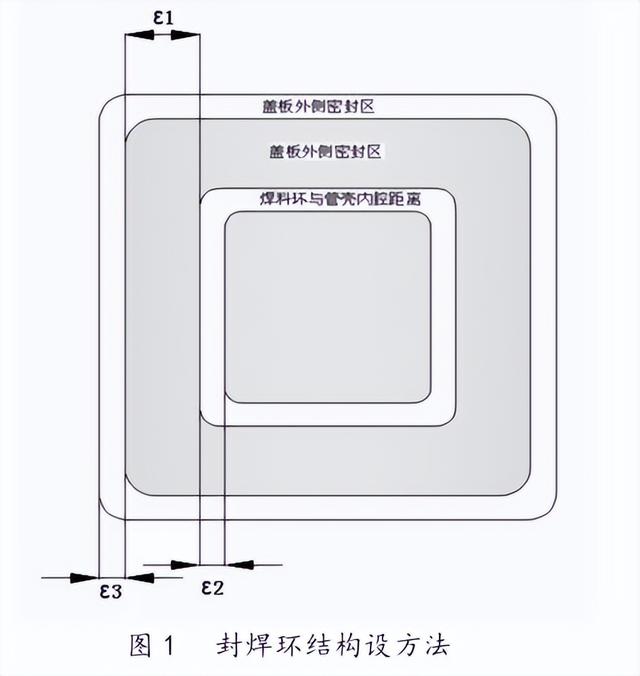
图 2 为焊料环优化前后的密封效果对比图,从图中可以看出,焊料环设计过窄,密封后封焊区域靠近管腔一侧边缘空洞明显;焊料环设计过宽,密封过程中焊料极易溢出封焊区,形成爬盖或者内溢形成泪滴状焊球。焊料优化设计后,焊接效果良好,基本无空洞。
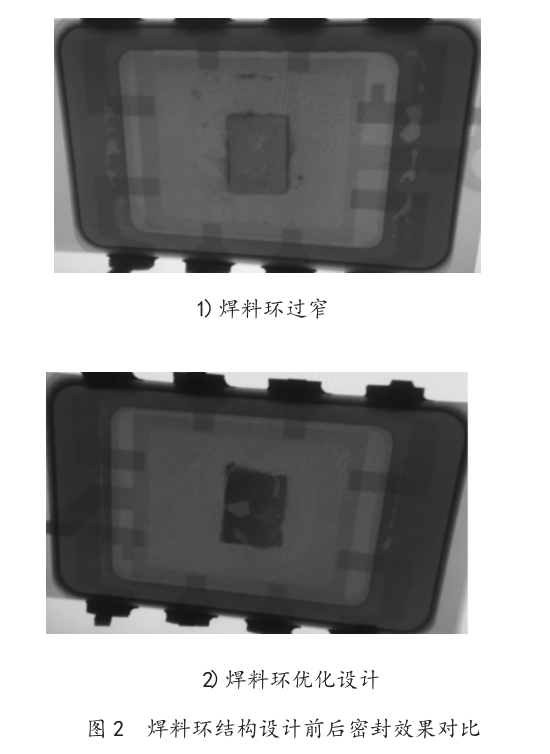
(2)焊接气氛控制
在密封过程中,一般要求真空炉内真空度小于1.0Pa,氮气纯度在 99.999% 以上,以避免在焊接过程中,氧化反应参与到共晶反应当中,在焊料表面形成氧化膜,阻碍金锡焊料与母材的浸润。图 3 为焊接气氛控制前后密封效果对比。
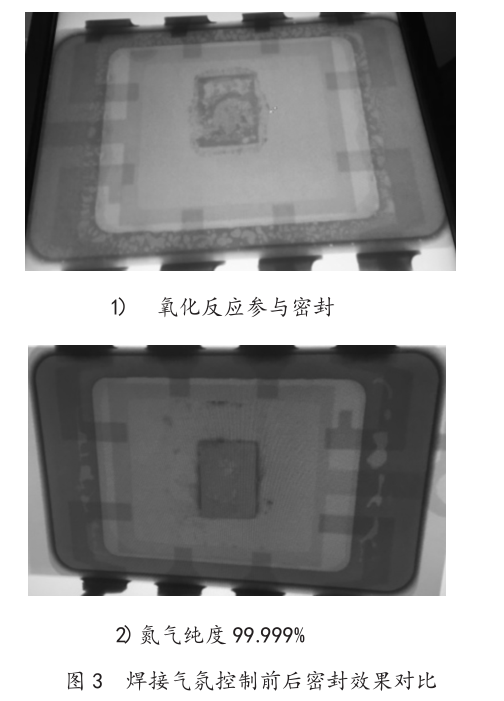
3.2 密封空洞控制的核心要素
在 2.4-2.5 中已经提到,焊接温度曲线和焊接压力是控制密封空洞的核心要素,对空洞的大小和数量有直接的影响。
(1)焊接温度曲线优化设计
图 4 是某型号 DIP8 电路优化前金锡合金密封的工艺曲线,通过现有工艺曲线在进行电路密封时,最大空洞的宽度占设计宽度的 20% 左右。通过大量工艺曲线优化实验发现,在温度曲线中,峰值温度对密封空洞的尺寸大小有非常大的影响,其余条件对空洞影响则较小。
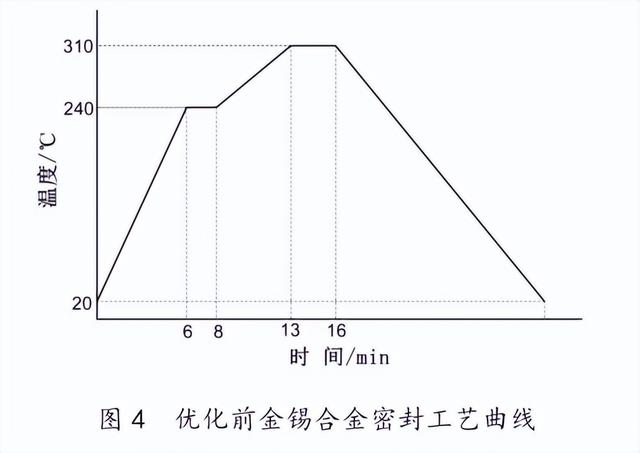
研究在原有工艺曲线基础上,针对焊接峰值温度设计了专项的优化方案,从 310℃至 340℃之间按每 10℃一个温度梯度设置优化试验方案,观察空洞率的变化。图 5 给出了不同峰值温度时的密封效果对比。表 1 是不同峰值温度时,最大空洞宽度占设计密封宽度的比值。
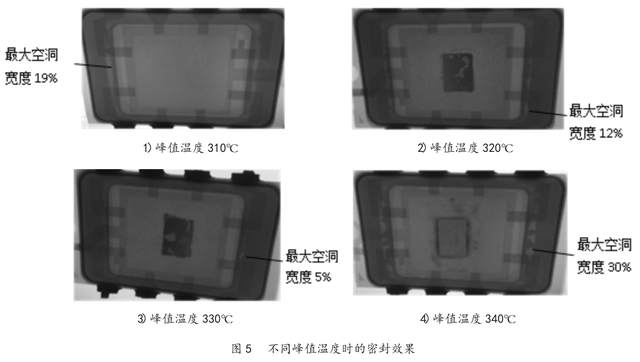
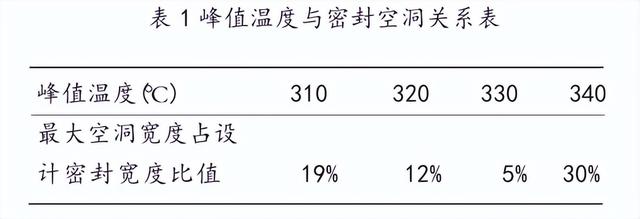
从结果可以看出,峰值温度在 330℃时,密封后电路空洞的大小和数量要优于其他峰值温度密封后电路。
(2)焊接压力优化设计
焊接压力也是控制密封空洞尺寸的核心要素,通过不锈钢弹簧夹施加压力到管壳和盖板上,在4N~10N 焊接压力之间,以 2N 为步进单位进行优化试验。
图 6 给出了不同焊接压力时的密封效果对比。
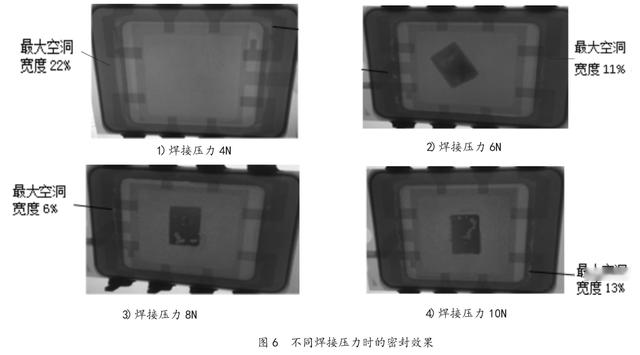
表 2 是不同焊接压力时,最大空洞宽度占设计密封宽度的比值。
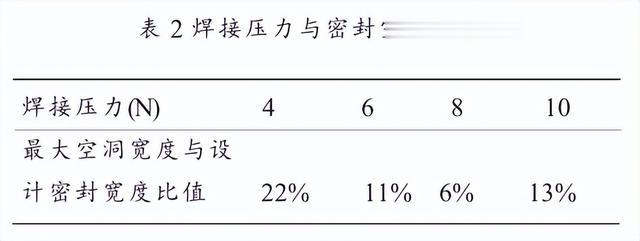
根据表 2 中的结果可以看出,当焊接压力小于2N 时,密封空洞尺寸很大。 焊接压力在 8N 时,密封效果后处于最优状态,电路空洞的大小和数量要优于其他焊接压力密封后的电路。
4 方法的推广及验证
根据优化后的密封控制方法, 以 PGA84 和PGA132 封装形式的外壳为例, 对密封效果进行了X 射线照相验证, 图 7 是 X 射线照相检验结果图。从图中可以看出, 两种封装形式密封的效果良好,最大空洞宽度占设计宽度的 5% 以下,可见,研究结果可以推广到同类产品之上。
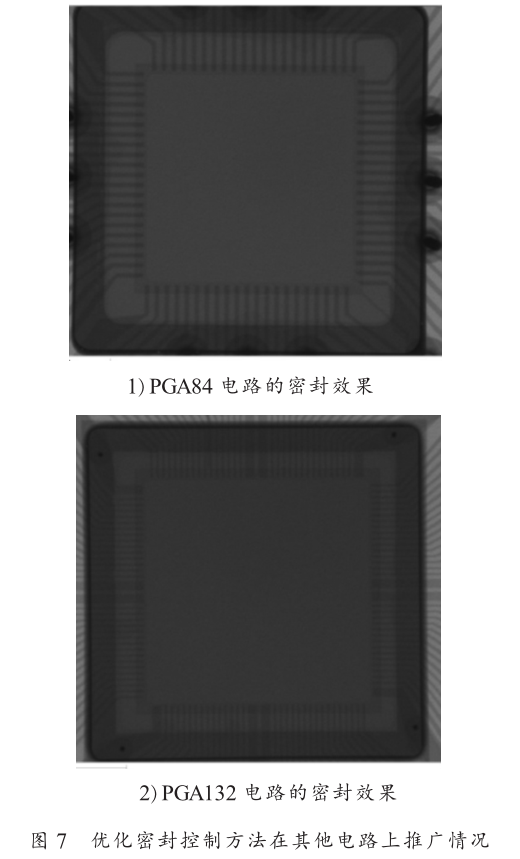
5 结束语
通过对陶瓷管壳集成电路密封空洞的实验研究,得到了金锡合金密封空洞控制的基本前提和关键因素。 从试验结论可以看出,焊料环尺寸设计、焊接气氛控制、原材料表面状态是金锡合金密封空洞控制的基本前提, 在控制好以上因素的基础之上,密封空洞的控制能够达到一个很高的水平;如果基本前提控制得不好,焊料的流淌很怪异,从而引发各种焊接问题,在此情况下空洞很难达到要求的控制标准。
另一方面,对控制密封空洞的关键因素进行了总结, 主要包括峰值温度和焊接压力两个关键项,并以 DIP8 封装形式为例, 通过峰值温度和焊接压力的优化设计,大幅提高了金锡合金密封的质量控制水平,将空洞率降低到 5% 以下。 研究成果还以推广到 PGA84 和 PGA132 等多种封装形式上,效果良好。
控制金锡合金密封空洞的优化方法有助于提高军用元器件的封质量,可广泛应用于导弹、飞船、雷达、舰艇、航天器等航空航天和空间设备仪器的核心电路封装中,在行业内具有一定的指导意义。