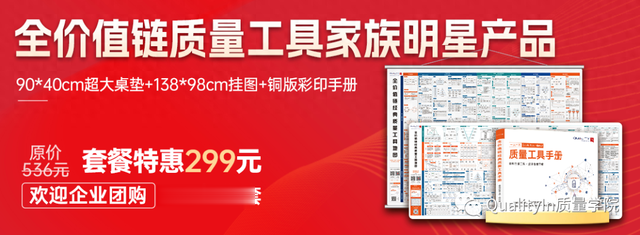
质量零缺陷,是所有企业都在努力追寻的终极目标。以日本丰田为代表,在2,000多人参与组装3万个零部件的汽车制造过程中,居然在线检验员人数为0个,最后却实现了零缺陷。丰田公司能达到如此效果,防呆防错Poka Yoke起到了举足轻重的作用。
所谓防错就是为防止不合格品的发生,在产品的设计和制造过程的设计开发中采用的技巧和方法。
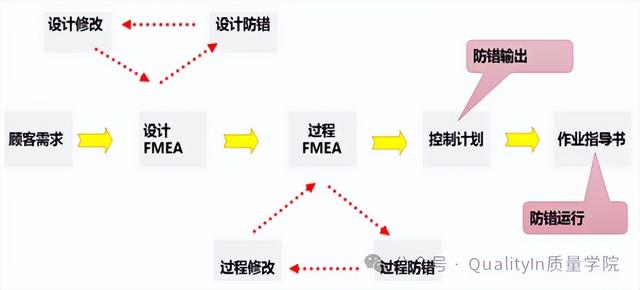
防错管理,是由防错设计、防错的实施、防错验证和防错经验教训的沉淀四个环节,共同组成的“P-D-C-A”闭环过程。
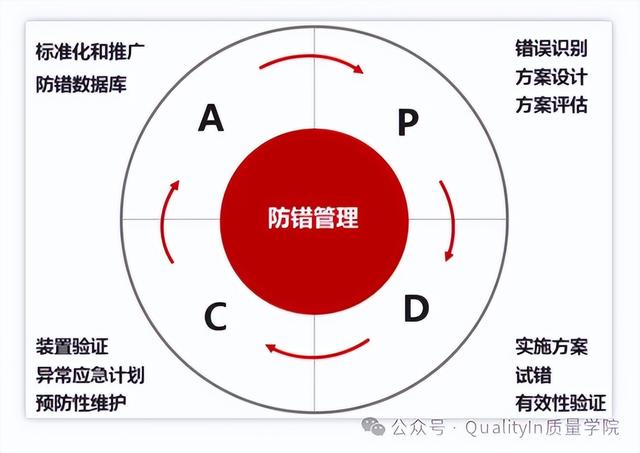
其中,防错设计又包括:错误识别、方案设计、方案评估,防错流程的执行过程中需要一系列的工具进行支撑。在防错设计阶段,会使用到DFMEA和PFMEA分析,可利用以往成功的防错经验、可使用头脑风暴的灵感,还可以使用5Why、鱼骨图等质量分析工具。在防错实施阶段,会利用控制计划、标准化作业等将防错的要求纳入标准化作业和跟踪监控范围;在防错验证阶段,需要利用产品试错、产线试错、OK/NG样件等方式对防错装置的有效性进行验证,对于防错装置可能出现的防错装置失效,应建立应急计划,并根据防错验证的结果,作为制定对防错装置实施的预防性维护计划。
一、防呆法的作用
各种失误在生产制造过程中随时随地都可能发生,其结果是造成产品缺陷和质量损失。防错技术的应用,可以有效避免或减少失误的发生,从而降低质量损失。
① 防呆法意味着“第一次把事情做好”。
② 防呆法意味着“有人为疏忽或者外行人来做也不会出错即不需要专门的经验或特别注意”的制程“傻瓜化”。
③ 提升产品质量,减少由于检查而导致的浪费、消除返工及其引起的浪费。
④ 实现自动化,提高效率。
⑤ 保证安全。
二、四种防呆模式
防呆针对不同的过程和失误类别,分别采用不同的防呆模式,分别是:
① 有形防呆
有形防呆模式是针对产品、设备、工具和作业者的物质属性,采用的一种硬件防错模式。如电饭煲中的感应开关即为一种有形POKA-YOKE防错模式。如果电饭煲中未加入水,加热开关就无法设定至加热位置,只有加水,加热开关方可打至加热位置。
② 有序防呆
有序防呆模式是针对过程操作步骤,对其顺序进行监控或优先对易出错、易忘记的步骤进行作业,再对其他步骤进行作业的防错模式。
③ 编组和计数式防呆
编组和计数式防呆模式是通过分组或编码方式防止作业失误的防错模式。
④ 信息加强防呆
信息加强防呆模式是通过在不同的地点、不同的作业者之间传递特定产品信息以达到追溯的目的。
三、防呆的等级
根据防呆装置的防呆效果,可将其分为3个水平:
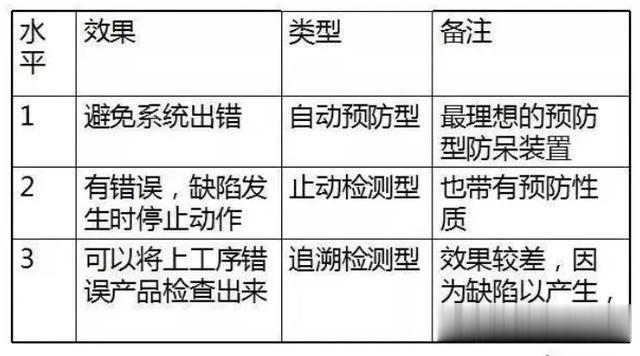
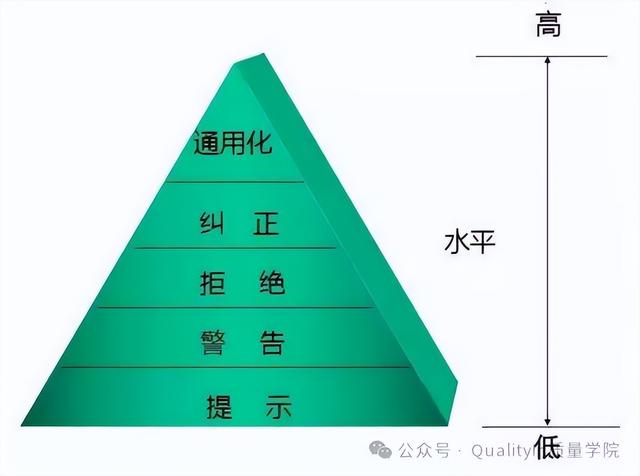
四、防呆法实施的原则
以下是几个基本的防呆法则,遵循这些法则,可有效防止作业失误。
① 轻松原则
难以辨认:难拿,难动的作业,易产生失误的作业。
改善:
用颜色区分- - - -容易辨认。
加上把手- - - -容易拿。
使用搬运器具- - - -动作轻松。
② 简单原则
需要高度技能与直觉的作业,容易让人产生失误。
考虑用夹具,工具使新人或辅助人员也不容易出错。
③ 安全原则
使操作人员在无意识作业或不太注意力时候也可以保证安全。
④ 自动化原则
依赖人的感观进行作业容易产生失误,治具或夹具的运用减少了人对本身感观的依赖。
例:
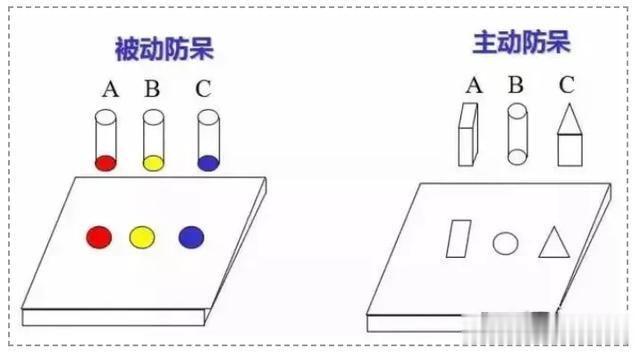
五、如何推行防错?
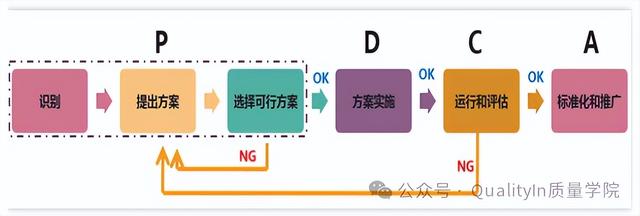
▲防错推行流程图
第一步,成立防错小组,俗话说“闻道有先后,术业有专攻”,专业的事要交给专业的人做,用擅长于防错的人做,小组成员应包含设计、工艺、生产、品质等相关人员。
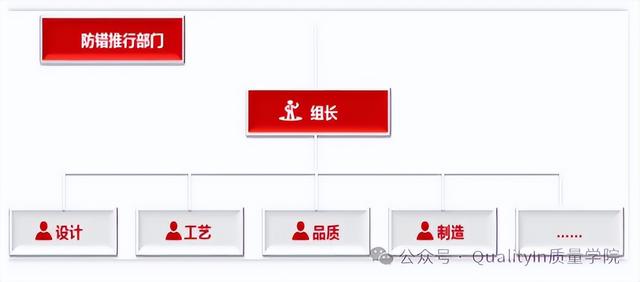
第二步,发现问题,来源于:
a . 以往产品或类似设计缺陷导致防错失效;
b . 零部件供应商、总装生产、服务店、用户反馈等反馈的问题;
c . 产品设计标准;
d . 产品/设计FMEA;
e . 分析SPC数据;
……
第三步,分析错误原因。对已经存在的人为错误进行分析,找出错误原因所在,以及这些错误可能造成的后果进行预测分析。确定根本原因是对应用防错技术以消除缺陷至关重要的。找出缺陷发生的源头,用质量管理七工具和5Why方法找出根本原因。
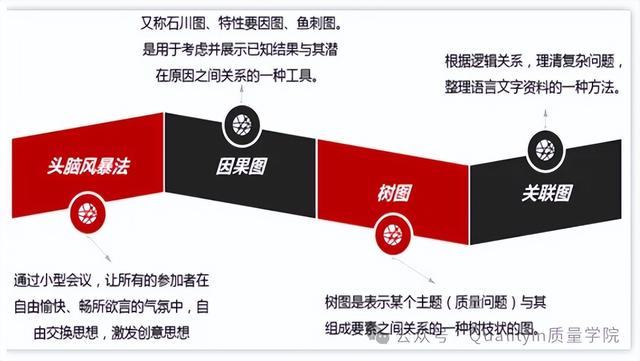
▲原因分析常用方法
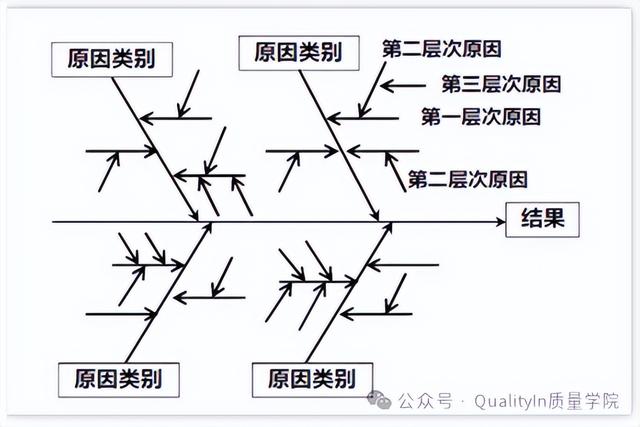
▲因果图
第四步,制定解决问题的基本方案。头脑风暴是一种可以激发产生大量的有创意的点子方法。也可利用工厂相似的防错装置。错误预防是通过产品设计、装配辅助措施等只允许以正确的方式进行生产活动的方法,实际生产要确保在产生错误的环节(缺陷来源)就直接将错误探测出来。
第五步,评估选择正确的解决方案。防错方案的评估和选择,应当遵循“简单、高效、低成本”的原则,对于防错的投入产出分析,对方案进行成本/效益分析,评审行动方案,选择最优方案,在此基础上提出实施计划。然后确定工序上的更改,选择合适的防错装置,制定责任及时间表,分配所需的资源。要站在产品的生产周期的角度来评判,局部和静态的思维会阻碍正确决策的形成。对于设计无法满足防错(成本、产品平台化、复杂生产工艺)进行工艺控制防错。
方案评估时应考虑:
a . 产品功能、结构设计增加防错;
b . 制造过程中工艺防错。
第六步,实施方案。在实施方案过程中,要不断根据实际的情况进行调整,并不断地进行改进还完善,实现方案的利益最大化。
第七步,运行和评估。收集数据与实施前相比较。
第八步,标准化和推广。对防错过程进行评审,前面的过程和结果进行总结,建立防错案例数据库,探讨方案能否复制、推广其他类似产品,特别要注意标准化,它包括:(更多资讯,请关注公众号:百家管理)
a . 为新的系统/装置建立文档、图纸;
b . 更新现有文档,清理无用的文档;
c . 重新评估现有的工作程序(包括操作、维护、检查等)并进行必要的修定对相关人员进行培训。
建立防错数据库,为以后新项目/产品进行防错。数据库来源于:
a . 以往产品或类似设计缺陷导致防错失效;
b . 以往生产经验,总结出常见的人为错误;
c . 零部件供应商、总装生产、服务店、用户反馈等反馈的问题;
d . 产品设计标准;
e . 产品/设计FMEA;
……
接下来,分享一份完整版日本企业的《POKA YOKE培训教材》,欢迎收藏学习!
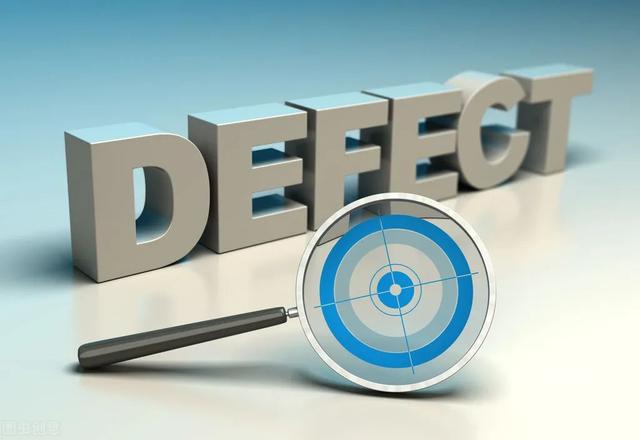
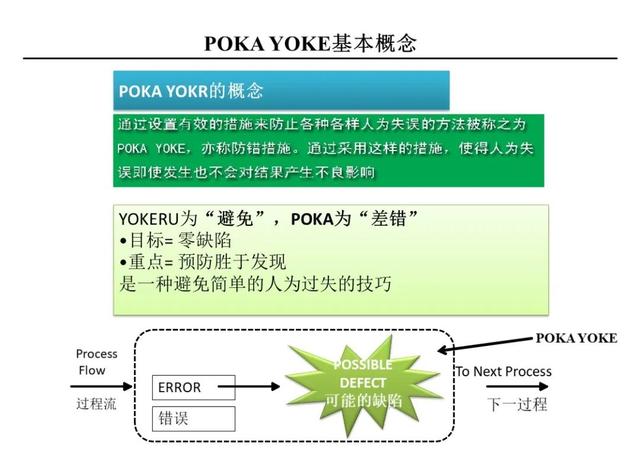
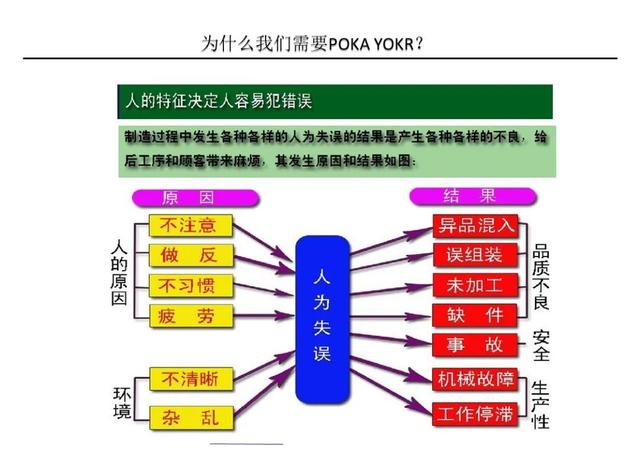
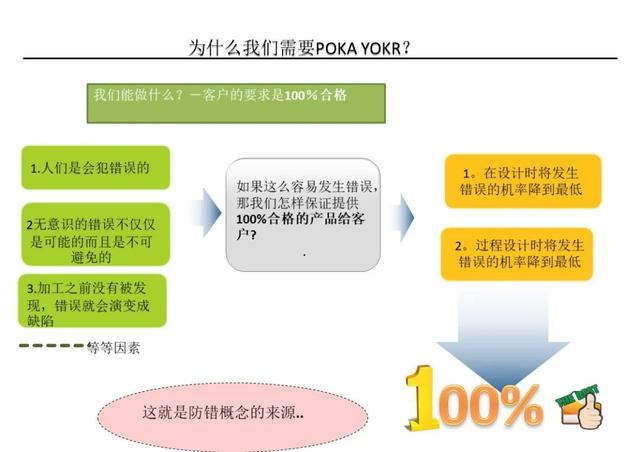
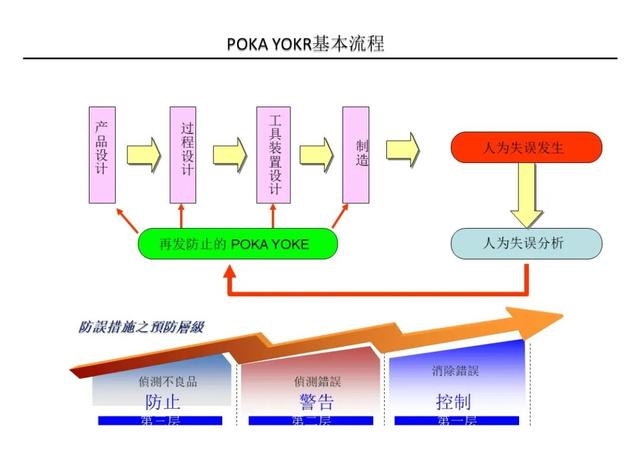

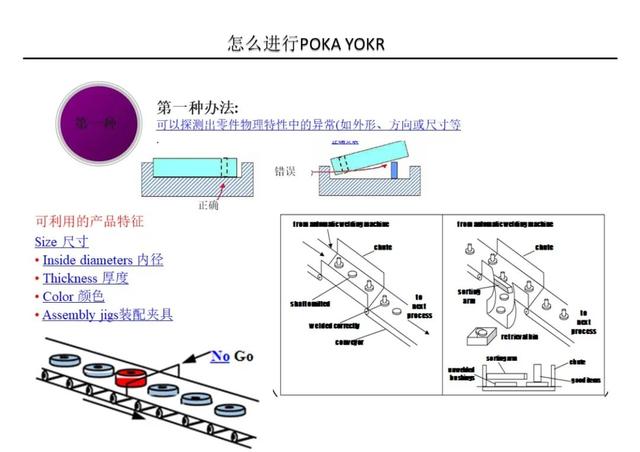
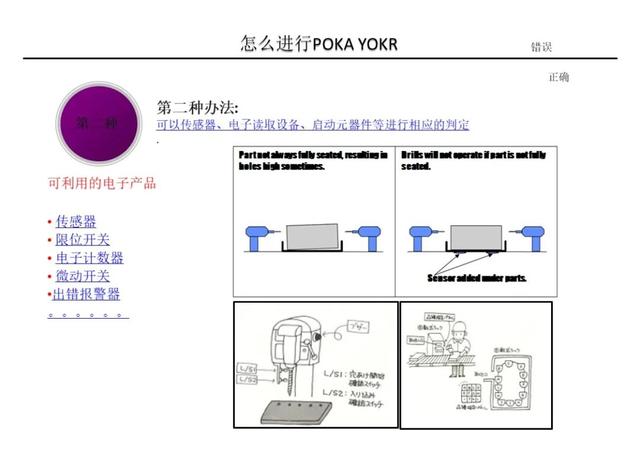
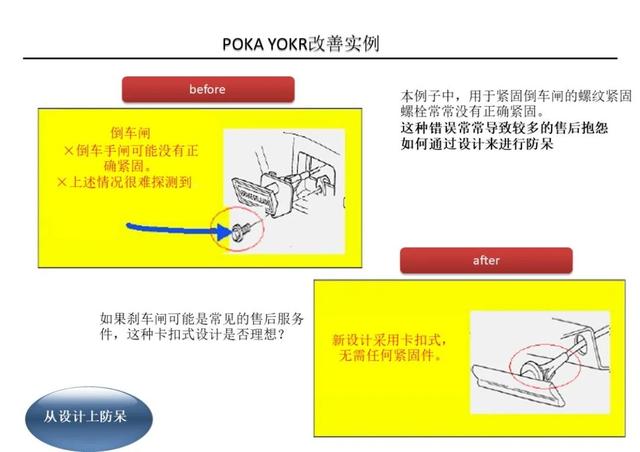
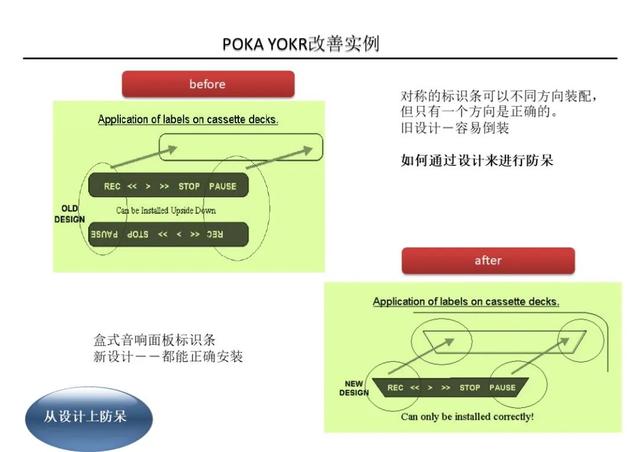
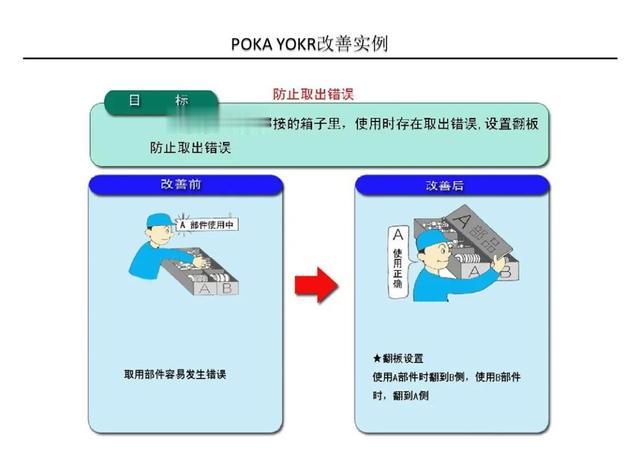
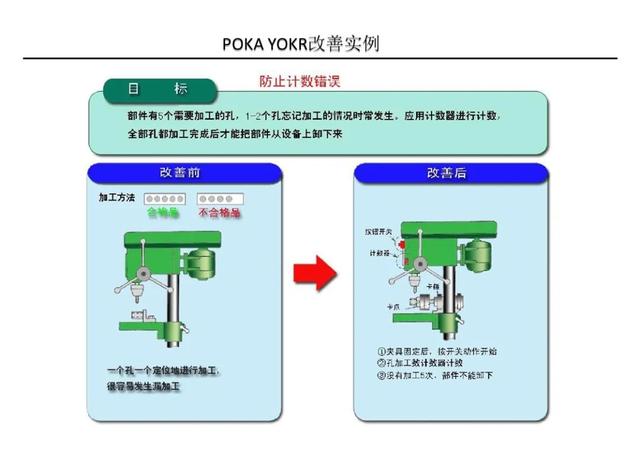
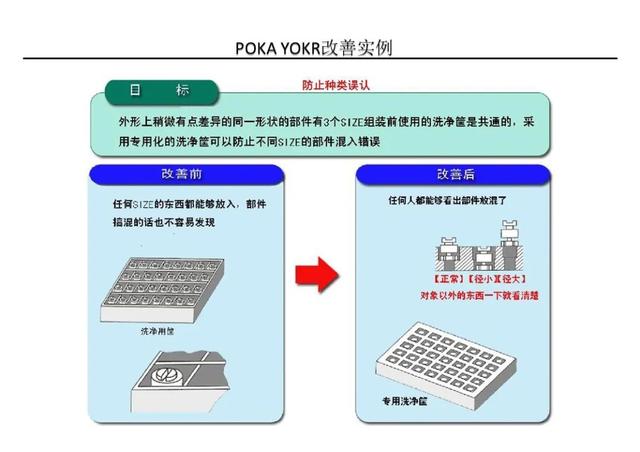
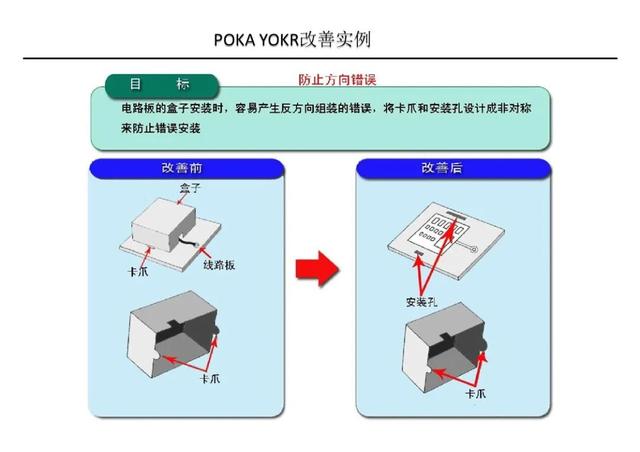
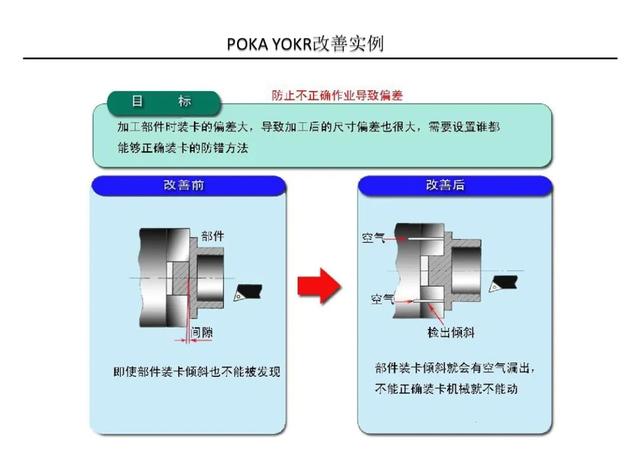
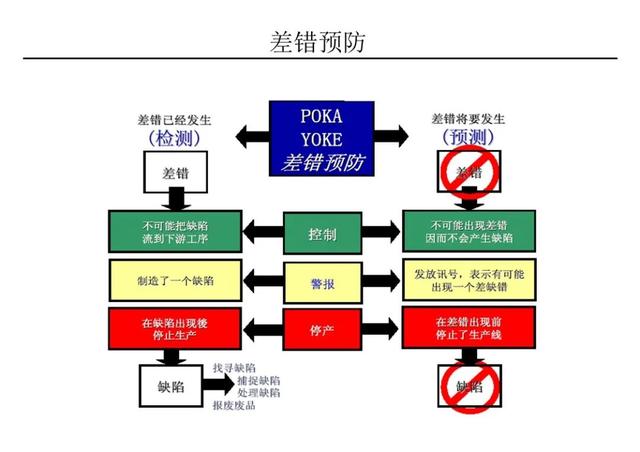
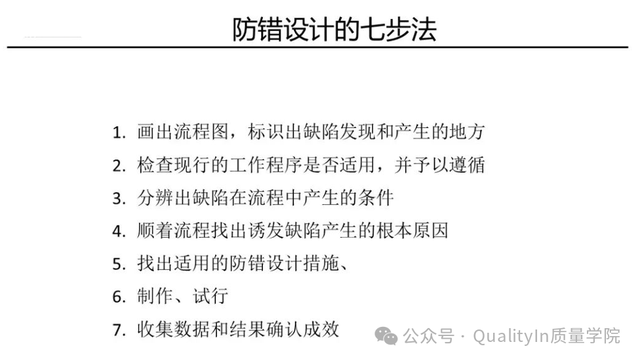
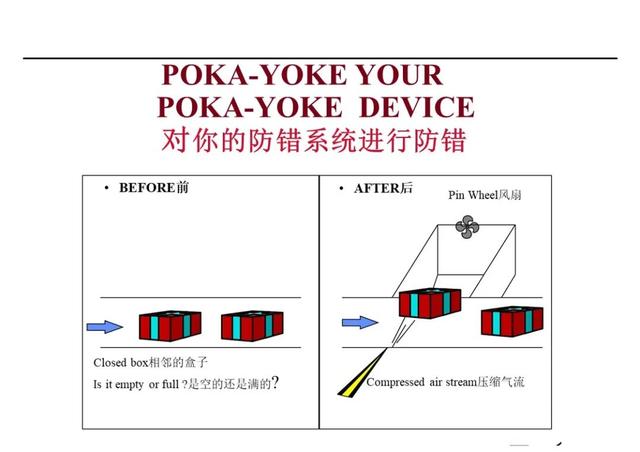
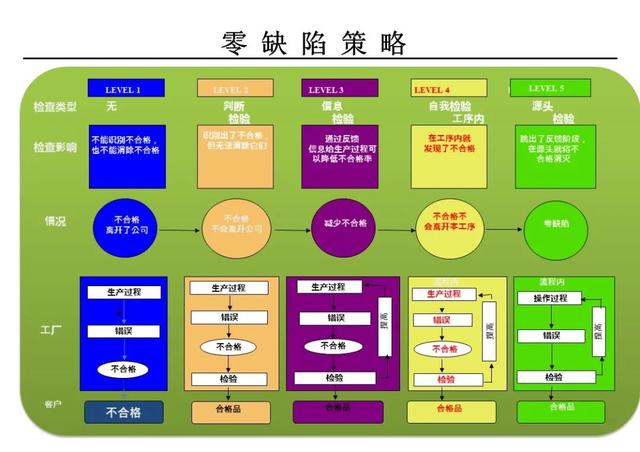
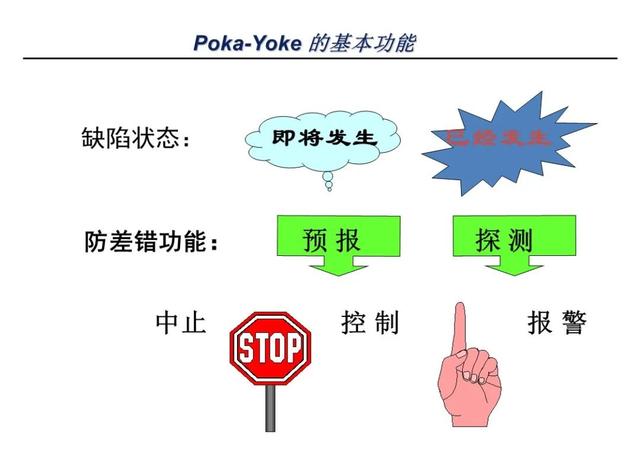

跟多专业质量文章,请访问QualityIn质量学院官网www.quality-in.com
One More Thing
「全价值链质量工具实操知识」明星家族产品
每个人都值得拥有的质量知识宝典
随时学习,指导工作!
▼▼▼
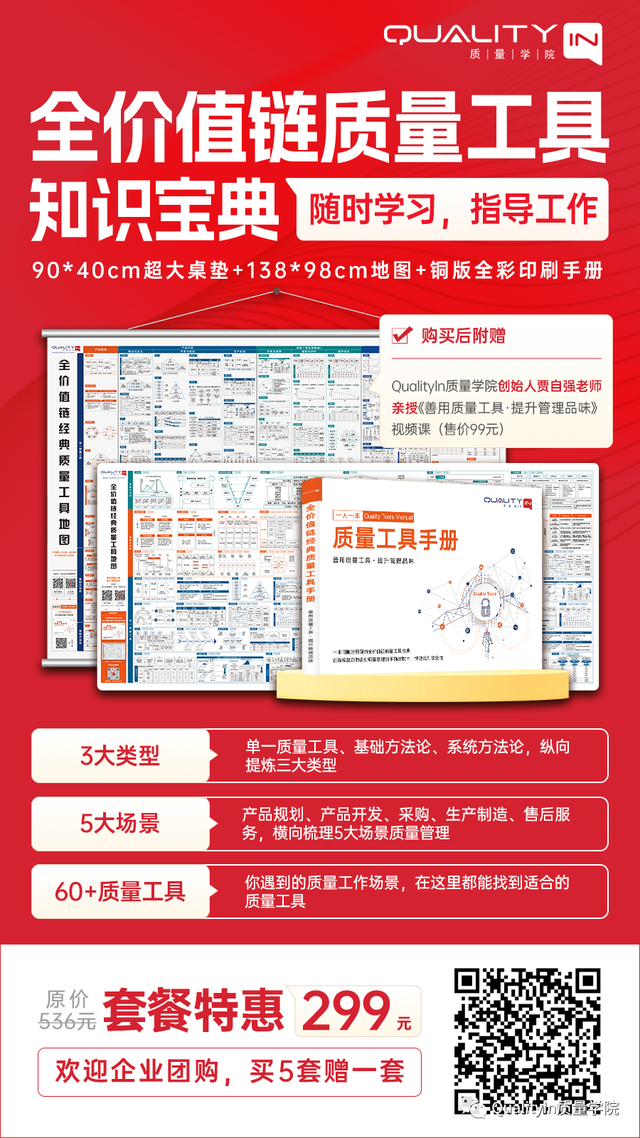