如果把双螺杆挤出机分成“挤出”和“传动”两大关键部分, 那么“挤出部件”是“保证品质”的关键部件,“传动部件”就是“提高效率”和“保证品质”的关键部件。
与此相对应的,扭矩是传动技术的关键参数,制约着加料量,也是双螺杆性能提升的最关键的技术指标;而螺杆间隙则是挤出部件的关键参数,控制着加工物料的停留时间分布,物料在机筒内的停留时间分布区间越小,说明原料在机筒内混炼时间一致,产品的品质越稳定,所以螺杆间隙是挤出产品品质稳定的最关键的技术指标。
螺杆间隙
螺杆间隙小,可以增加螺杆的推进效率,减少回流,提高产量;均匀的螺杆间隙,保证了物料在机筒内均匀的停留时间分布,从而保证了产品品质的稳定性和一致性,使精密挤出、稳定挤出成为可能;物料的停留时间稳定均匀同时使温度控制的稳定性能提升,加工温度的稳定保证了工艺稳定性,从另一方面也保证了挤出产品的品质稳定。
众所周知,德国挤出机的螺杆间隙往往非常优秀,者也是基于他们传动系统稳定输出技术的突破,只有在输出轴跳动稳定、不发生变化的基础上,才能使用小的螺杆间隙。
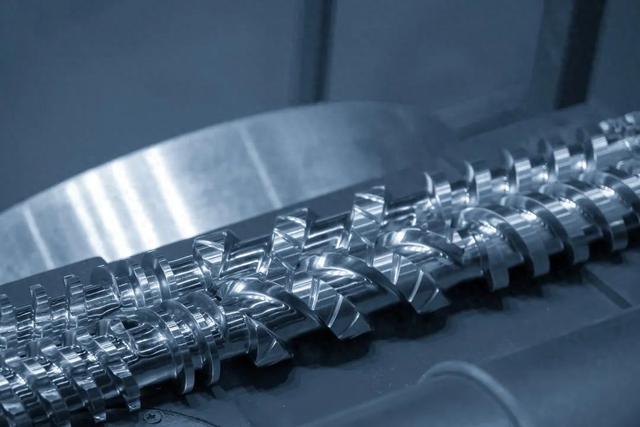
挤出元件的材料
表1列举了代表双螺杆技术进步的几个基本指标,1、2、3分别代表产品的等级,第1级为最高级,即现在世界上挤出技术的顶级水平,第2级为标准高端配置,第3级为目前国内通用配置。由表1可以看出:在齿轮箱承载能力保证前提下,提高螺杆转速对提高生产效率和降低运行成本有很大贡献。随着螺杆转速的提高,材料和元件之间的磨损加速,降低了元件的使用寿命,向我们提出了材料耐磨性能的要求。
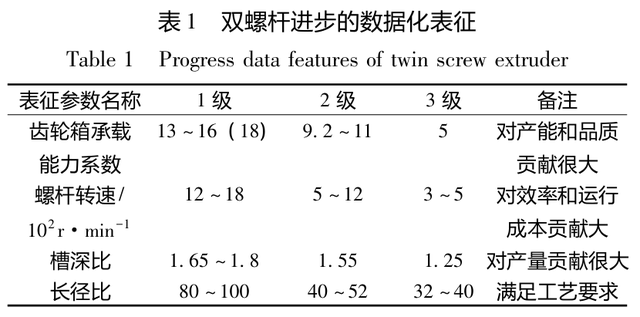
表1同时显示:螺槽深度的增加,对产量有很大贡献,但是螺槽深度的增加必然减小芯轴的直径尺寸,对芯轴的强度也提出了更高的要求。
实际上扭力分配技术突破以后,制约双螺杆发展的因素发生了根本性变化,之前是齿轮箱的输出扭矩和使用寿命,即芯轴的强度系数高于传动箱,而现在强的是传动箱,芯轴的强度成了制约因素,所以现在双螺杆的制造者把研发的重心放在了芯轴、筒体内套和螺杆元件上,开发更高强度的芯轴、更耐磨的筒体内套和螺杆元件。
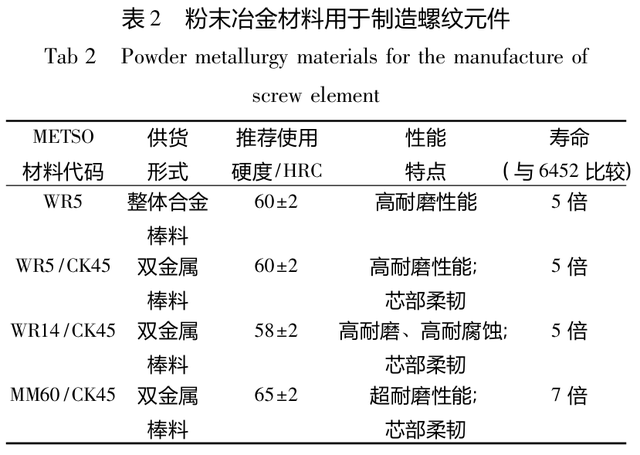
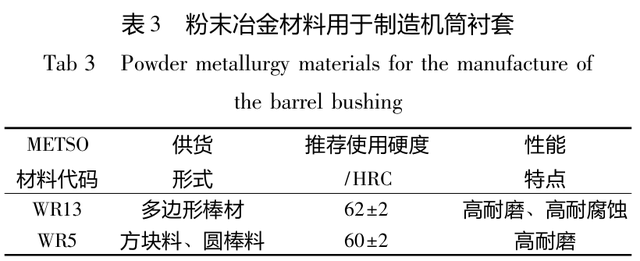
其主要方案是:采用热等静压粉末冶金成型工艺(PM-HIP)制造高抗磨蚀材料,经过该冶炼工艺生产的钢材WR15E和WR30兼具高耐磨性和高韧性,其中WR30还具有高耐腐蚀性,是加工高强度高韧性长芯轴的最佳材料;WR5、WR14、MM60具有高耐磨性和优良的加工性,是加工螺杆元件的最佳材料,其中WR14具有高耐腐蚀性能,MM60具有超高耐磨性,可用于加工含金属粉末的加工工艺;WR13和WR5可以铸造成整体钢套,作为机筒内衬,其中WR13不仅具有高耐磨性,还具有高耐腐蚀性能。
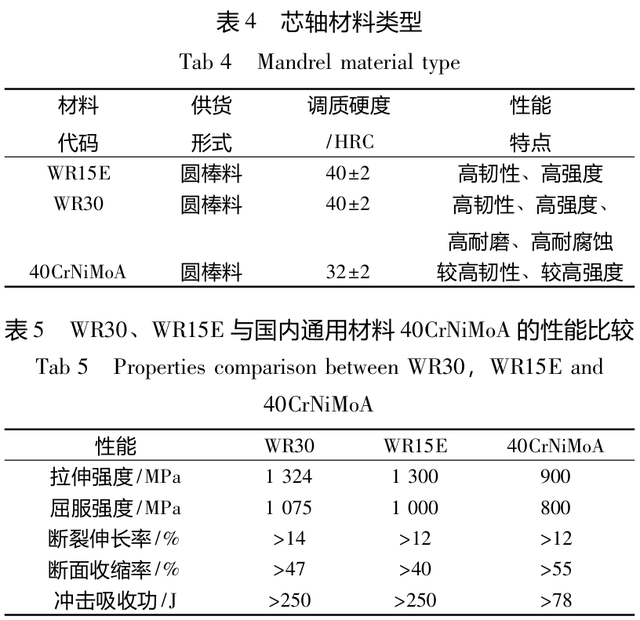
由表4、表5可见,由粉末冶金材料WR30和WR15E加工的芯轴的冲击吸收功远远大于国内通用的芯轴材料40CrNiMoA的相应值,约为国内材料的3倍,证明该材料冲击性能高、韧性好。能够配套高扭矩齿轮箱,可大幅度提高设备输出扭矩和生产能力。
应用以上材料,可以有效提高设备挤出部件的整体耐磨性,使挤出机在高转速下提高使用寿命成为可能,这也是前文提到的挤出设备的几个考核指标之一。当然随着国内钢铁冶铸工业的发展,这类材料的选择会越来越多。