在电子产品服役过程中,由于温度和振动等外部环境的影响,焊点的焊料与封装结构的树脂等材质热膨胀系数(CTE:Coefficient of Thermal Expansion)的不匹配会使得焊点发生蠕变而造成疲劳开裂[1]。倒装类的BGA封装具有较高的集成度且已广泛地被应用于通信端的信号处理和存储领域。为了提高这类焊点的热疲劳寿命,业内采用较多的是在芯片底部填充树脂(底部填充工艺)使其与基板胶黏固定[2],从而降低温循过程中的热失配应力、起到提升焊点机械强度与热疲劳可靠性的作用。

目前较多的研究均集中在底部填充工艺后的有限元仿真分析上。通过建模仿真得到底部填充前后焊点内的应力应变分布,模拟计算底部填充后对焊点寿命的改善效果[3-5]。在随机振动应力仿真方向发现,采用底部填充胶对焊点进行填充可以有效地降低随机振动载荷作用下焊点内的应力应变,底充胶弹性模量越大,密度越小,越有利于减小焊点内的随机振动应力应变[3]。热循环仿真方向的结论显示,选取一种CTE较小的环氧类底部填充胶对封装焊点进行填充能有效地减小组件内部热应力和焊点蠕变[4]。这类仿真在进行建模时考虑的都是胶水是否完全填充,从而忽略了具体的工艺生产中的胶水填充比例的实际影响。此外,在施加环境应力的过程中认为底部填充胶水的性能不发生老化或者改性。
关键词:焊料 电阻值 焊点
本文基于IPC 7091A《表面贴装锡焊件性能测试方法与鉴定要求》设计了菊花链结构的电路板及阻值实时监测系统。实验参考仿真结果,选取了不同的玻璃化转变温度(Tg)和CTE的胶水在TC4(-55~125℃)温循条件下测试焊点的热疲劳寿命。实验中还考虑实际的免洗工艺中助焊剂残留等问题导致胶水无法100%填充的情况,建立了内部底部填充工艺的评估方法,对于胶水的选型及工艺质量评估具有一定的参考意义。本文最后还对温循后失效焊点焊料的金相结构和undefill胶水的形貌进行了分析。
1 底部填充工艺及焊点热循环可靠性试验1.1 BGA焊点菊花链电路设计本文选取了Amkor公司15 mm×15 mm×1.2 mm菊花链结构的BGA芯片。焊球为17×17的四周阵列排布,共208个,间距(pitch)为0.8 mm。将PCB侧的焊盘同样设置为菊花链结构,使得焊接后所有的焊点通过芯片侧和PCB侧的链状结构全部串联在一起。PCB选择FR4(Tg:130℃,Td:310℃)的6层叠板结构。其中,两层芯板均为S1141,3层玻纤布为S2116,板厚为1.6 mm,铜厚为0.035 mm。焊料采用无铅SAC305体系的ALPHA OM-340。焊点菊花链结构设计如图1所示。
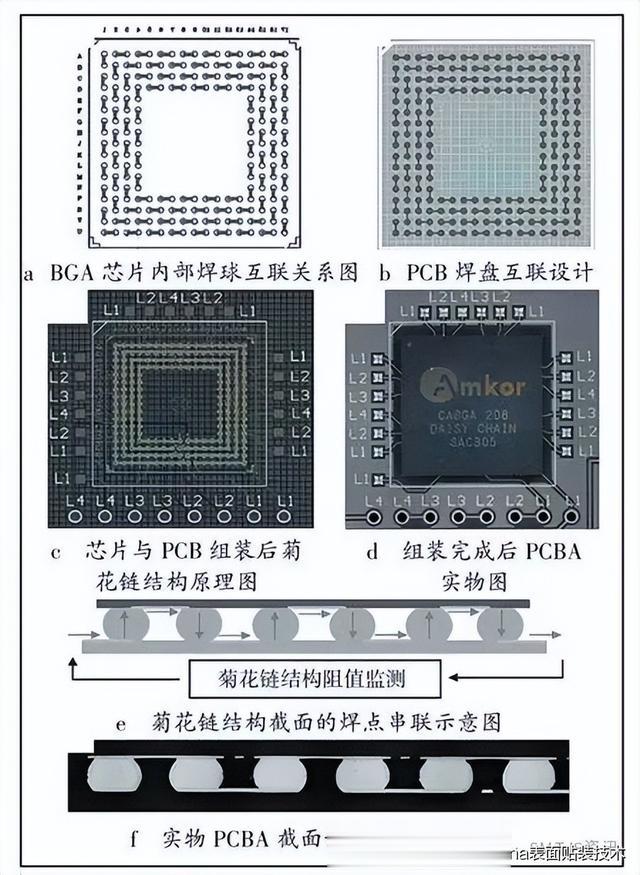
图1 焊点菊花链结构设计
1.2 底部填充工艺及胶水填充质量底部填充胶是利用毛细作用使得胶水渗透进入BGA芯片底部,经加热固化后在芯片封装和PCB之间形成牢固的填充层,起到包裹保护焊点的作用。当填充工艺不良时,容易出现芯片底部胶水渗透不良而产生气泡或者芯片封装侧面充填高度不足;而过量涂覆,则会导致胶水溢出流到器件表面或其他位置,影响外观及后续的组装测试。此外,目前的电子产品一般均采用无铅免洗工艺,助焊剂的残留也容易导致胶水无法完全包裹焊点。底部填充工艺质量如图2所示。
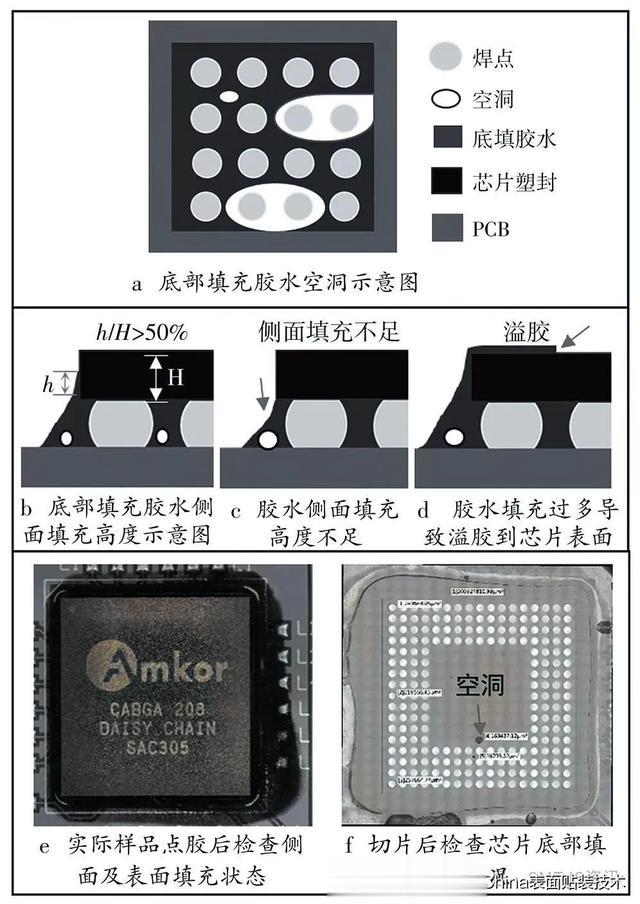
图2 底部填充工艺质量
综合衡量各类产品的底部填充需求,本项目考虑从底部填充比例和侧面的填充高度来对底部填充胶水的工艺质量进行管控。
为了保证底部填充胶水能有效地包裹所有的焊点,本文中底部填充质量的评估标准是侧面填充高度超过芯片塑封体厚度的1/2(如图2所示,h/H>50%)且底部的胶水填充率>95%。允许焊点PCB侧存在少量的气泡,但所有的焊点周围均要有填充,不允许胶水外溢到芯片封装的表面。
部分研究结果显示,底填胶水对焊点的热疲劳寿命改善效果与胶水的CTE相关[4]。因此本实验选取了3款典型的CTE胶水,同时兼顾了胶水是否可返修性能(A的Tg值最小,最容易返修;C的Tg值居中,可以返修;B类Tg值较高不可返修),如表1所示。
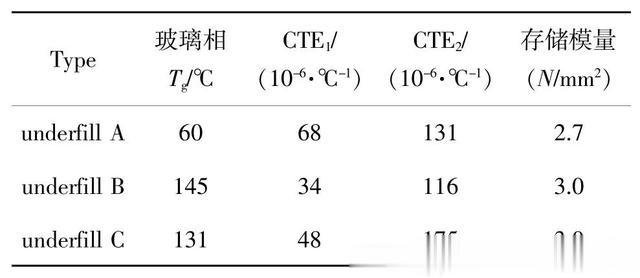
表1 3款待评估底部填充胶水的材料性能参数
2 热循环可靠性试验2.1 温度循环条件本实验参考了IPC 7091A中的TC4等级加速条件(-55~125℃)。最高温和最低温驻留时间都为10 min,温变时间为15 min(温变速率为12~20℃/min)。
温度参数设置完成后,实际监测箱内温度与焊点处的温度发现,箱子内部温度变化情况与设置温度基本一致,但焊点处的实际温度与设置温度存在较大的差异,实际的焊点温度范围为:-42.3~101.6℃,如图3a所示。经排查发现,温差是由于实验测试板的热传导系数决定的,PCB的铜箔和树脂等材料的散热性能和温变速率使得焊点处的温度无法与设置参数保持一致。焊点经历的实际温度循环条件仍呈现周期性且与设置参数的周期一致,但是最高温与最低温以及温变速率存在差异。后续的仿真分析需考虑这一实际情况。
测试开始后同步监测某条菊花链结构的电阻值变化,结果如图3b所示。初始状态下(常温且焊点结构正常)电阻约为6.4Ω,此时电阻值来源于焊点、导线等处的互联电阻。当温循开始时,电阻值随温箱内温度同步呈现小范围内的周期性波动,这是由温箱内的焊点及导线内阻随温度变化而导致的。

图3 温度循环测试结果
2.2 焊点阻值监测结果某菊花链焊点结构1 000个循环过程中的阻值变化如图4所示。参考IPC 7091A,本文将菊花链的电阻值变为100Ω的时刻作为焊点完全失效的判断点。
图4显示,实验开始后电阻值维持在很小的值不变,从某一时刻开始出现波动,此后一直呈现更大范围的变化。聚焦到电阻值开始波动的那一个时刻发现,在此时刻之前,焊点菊花链的电阻值基本与初始时刻一致且仍是保持随温度呈现周期性变化的规律。从该时刻起,阻值开始变大,且此后迅速地变为几千欧姆甚至无穷大,呈现为无规律的电阻值波动。当电阻值超过100Ω后,后面的温度循环周期内,焊点阻值也不会恢复正常状态,可以排除此时刻电阻变化是环境变化等导致的异常点,该点时刻可以用来表征焊点阻值随时间的变化情况。
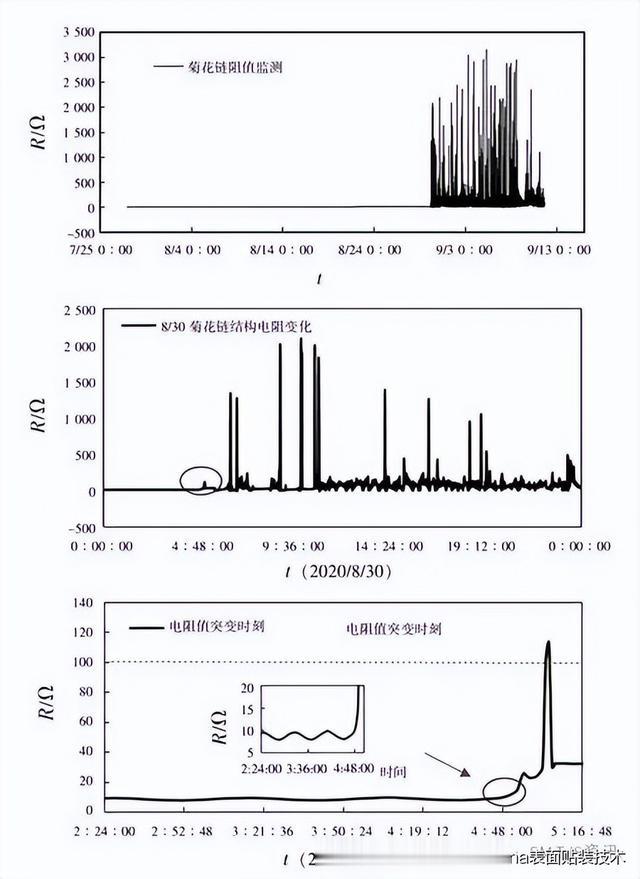
图4 焊点菊花链结构电阻值监测结果
监测每一个菊花链结构的电阻值变化并统计焊点失效点时刻,以此作为该结构的焊点热疲劳循环寿命。
2.3 焊点温度循环热疲劳寿命统计1 000个温度循环测试后菊花链焊点失效循环数。经检验,该数据符合两参数的威布尔分布,焊点寿命分布如图5所示。
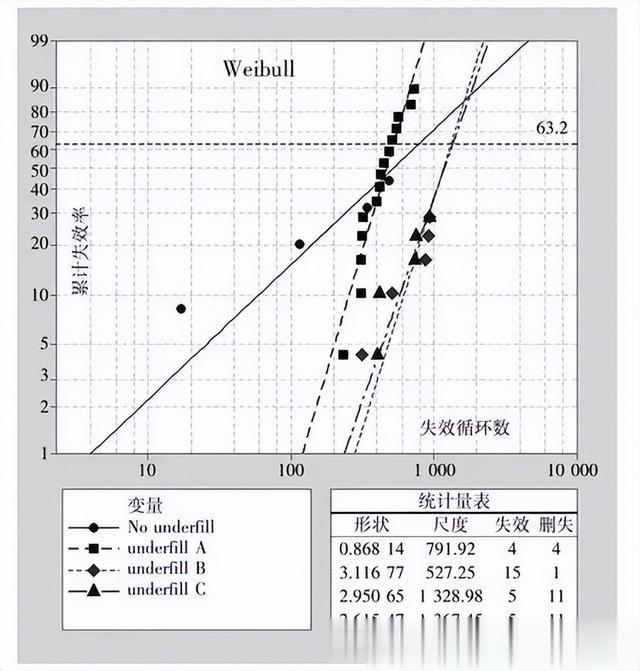
图5 温度循环测试后焊点热疲劳寿命的威布尔分布
统计分布数据表明,B和C两种底填胶水的寿命Nf(63.2%)约为1 350个循环,相比于无底部填充胶时焊点寿命约提升了2倍。然而,A类底部填充胶后的焊点寿命约为527个循环,比无底部填充胶可靠性差。
3 实验结果分析3.1 焊点热疲劳失效分析分别选择这几类温循后失效的菊花链焊点进行切片分析发现,焊点内部确实出现了热疲劳性开裂,并且芯片的最外圈焊点开裂得最多,这与仿真结果(边缘焊点最容易开裂)一致。
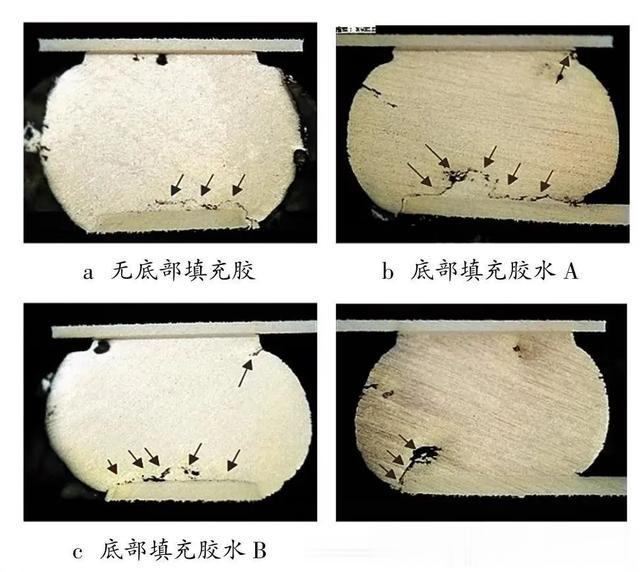
图6 菊花链结构失效焊点切片分析
进一步对失效焊点裂纹进行金相结构分析发现(如图7所示),裂纹是从焊点边缘处的金属间化合物(IMC)开始产生的,然后逐渐地向焊点内部扩展。SEM结果显示,焊料裂纹基本是沿着大的颗粒Ag3Sn的晶界处生长,这些大的晶粒来源于温度循环过程中焊料的重结晶。随着结晶过程的产生,晶粒开始生长粗化从而产生更大的晶界,并逐渐地扩展为微裂纹。
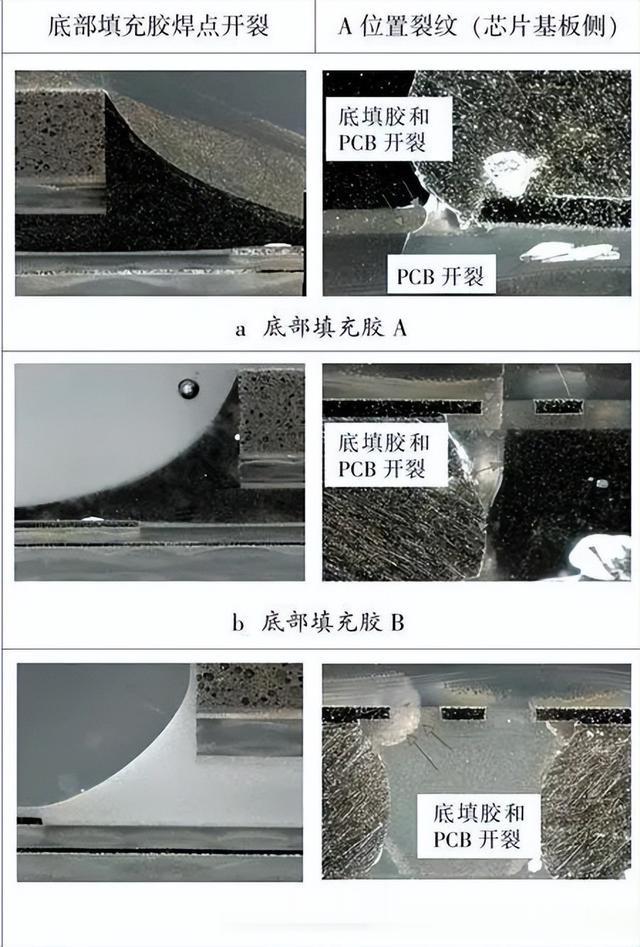
图7 失效焊点裂纹金相及SEM分析
一般认为,焊点的IMC处最脆最容易出现机械应力开裂[5-6]。当焊点边缘IMC处出现起裂点后,裂纹沿着焊料内部晶粒粗化形成的晶界微裂纹生长,并最终形成贯穿整个焊点的大裂纹。
3.2 温度循环实验后底部填充胶水分析如图8所示,对有底部填充工艺的样品进行切片检查发现,本实验中样品的底填工艺侧面填充质量均良好,并且实验后未发现侧面胶水有分层开裂异常。进一步地检查焊点周围的胶水发现,A、B和C 3类胶水均存在不同程度的开裂,部分位置的胶水裂纹有向PCB或者芯片基板中扩展,甚至PCB焊盘和内部玻纤有被拉扯变形和开裂。
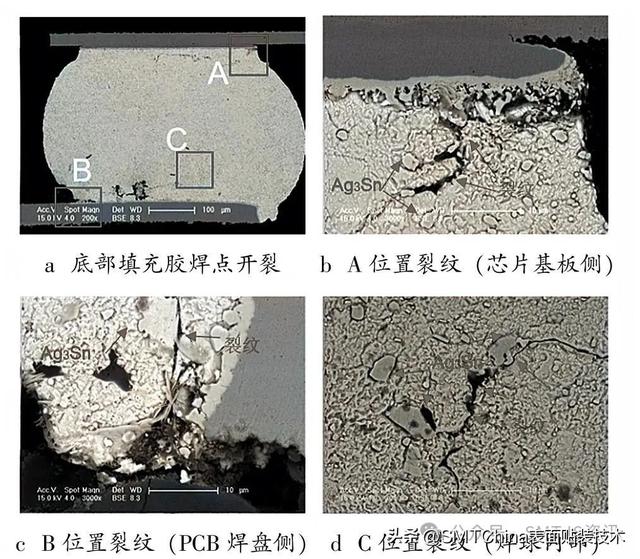
图8 温度循环测试后底部填充胶水的形貌分析
底部填充胶水裂纹主要是从胶水与焊球的接触位置开始出现的。这是由于SMT使用的免洗工艺导致焊球边缘有助焊剂残留包裹,使得底填胶水与焊料或者PCB的粘合强度导致的。胶水的吸湿性能以及在热循环条件下的性能退化(老化),也会加速胶水的老化开裂[7]。
4 结束语本文基于IPC 7091A焊点可靠性实验参考标准,设计并讨论了在热循环交变条件下的无底部填充工艺和有底部填充工艺下的BGA焊点可靠性寿命,得出了以下几点结论。
a)底部填充胶水对焊点热疲劳寿命的改善效果与胶水的性能密切相关。选择高Tg值与低CTE的底部填充胶水,可以增强焊点的热疲劳寿命;而低Tg和高CTE的胶水则会带来相反的效果,导致焊点更容易热疲劳开裂。
b)采用无铅免洗工艺会使得焊点周围有较多的助焊剂残留并影响底部填充效果。进行底填工艺时,应通过工艺改善优化,减小底填胶水内的空洞。建议底部填充率>95%,且芯片表面无溢胶。
c)进行可靠性温循实验,焊点处的实际温度与温箱设置温度存在差异,下一步进行焊点有限元仿真分析时需关注实际的温循条件。
d)焊点热疲劳裂纹是从IMC处开始产生的,然后向焊料内部扩展。焊料内的微裂纹沿晶格重结晶晶粒的晶界处生长。底填胶水的老化开裂,也是加速焊点热疲劳失效的原因。
