引言
轮毂轴承、齿轮箱齿轮、机床床身导轨、弓网接触副和内燃机等重要的摩擦副经常处于动载状态。
在汽车尾气排放和轻量化需求不断提升的背景下,其转速和爆发压力持续升高,使得不断增强的动负载对其摩擦磨损行为的作用更为显著,呈现出一种不规则、反常的特征。
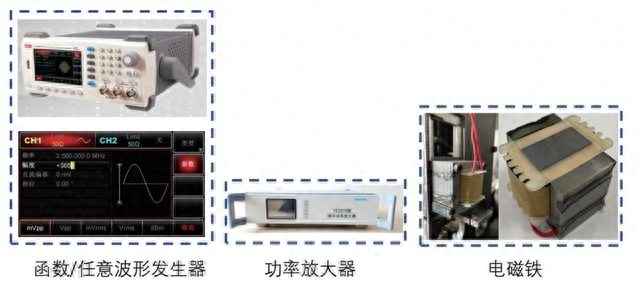
通过对同一材质的摩擦副的摩擦学特性进行了分析,得出了在相同材质下,由于负载特性的不同,所得到的摩擦学特性也有很大的差别。
比如,一些在常载条件下磨损较好,但在动载条件下磨损会显著降低。因此,探索高强度钢在动载下的摩擦磨损机制是目前迫切需要解决的科学问题。
另外,现有的滑动式实验装置通常都是采用固定负载,而不考虑动负载对实验结果的影响,这给实验带来了很大的困难。
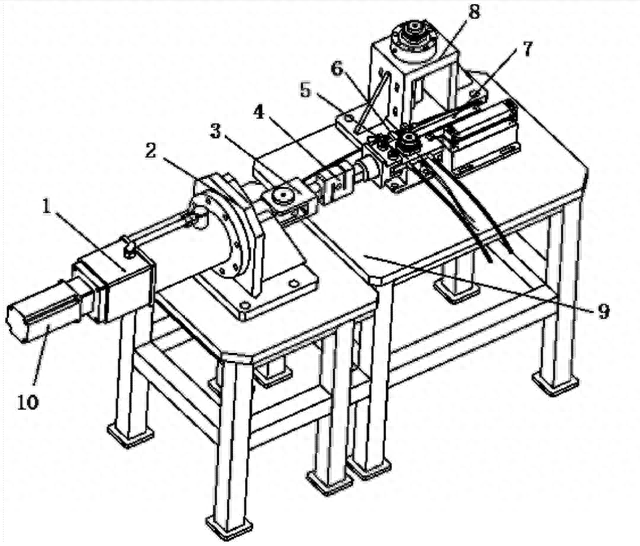
因此,建立动载下的滑移-摩擦学实验装置,对其进行实验和分析,并对其进行实验验证,是一项非常有意义的工作。
摩擦学的发展有赖于实验的开展,而实验的开展则依赖于实验设备,实验设备是实验设备,它为实验设备的研制和应用奠定了基础。样品级别的测试一般是按照一定的测试参数,在试验台上进行的。

它具有测试周期短、灵活性高、成本低等优点,可以按照测试需求进行系统性测试,从而获得比较完整的测试结果,但是测试结果只有样品级,并且与实际工作环境相分离,使得测试结果在设备上的可用性不高。
虽然存在着以上缺陷,但因其费用低、使用简便,在进行摩擦学理论和摩擦学理论的研究中仍然被广泛应用。

在实验室样件级测试中,经常使用的是模拟台架试验,因为使用的是更接近实机工况的测试设备。从而可以有效地解决样品级别的测试中存在的测试资料可用性低的问题。
另外,仿真台架实验无需在真实设备上进行,可以快速获取大量的实验数据,提高实验结果的可靠性和可用性。但此法费用高昂,与实用测试并不能相提并论。
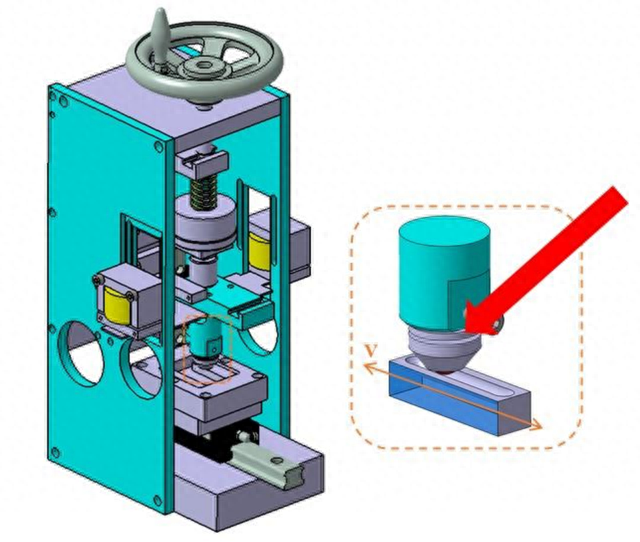
在将以上两种测试或者是其中一种测试全部完成之后,还需要在实际应用中对所知道的结果进行进一步的检验,一般情况下,都是采用与实际应用条件非常接近的实际应用测试,得到的测试结果的可靠性是最好的。
但是,由于受实验环境的制约,实验时间很长,并且反复进行实验,这一问题就更加严重了。
总之,在对某些典型的材料进行选材和对其进行摩擦学特性的测试时,一般都会使用室内样品级别的测试手段,从而形成了类型最多、覆盖面最广的一种类型。
摩擦磨损试验机的发展始终是被科学研究的方向所制约的,在其发展的初期,主要是对摩擦副的接触试样在整机中的接触形式、温度、气氛、载荷等因素进行了研究,而所作用的载荷大多是恒定载荷,因此,所开发的试验机大多是在恒定载荷下的摩擦试验机。
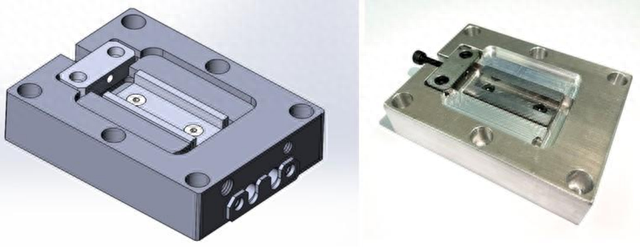
在研制等负荷试验机过程中,贵昌霖主编的《摩擦磨损试验机设计基础》按摩擦副的移动方式将试验机划分为:滑动摩擦试验机,滑动摩擦试验机,微动摩擦试验机。
滚珠接触摩擦磨损试验机:滚珠摩擦指的是两个或两个以上的物体在没有滑动的情况下进行滚动时,所发生的一种摩擦。
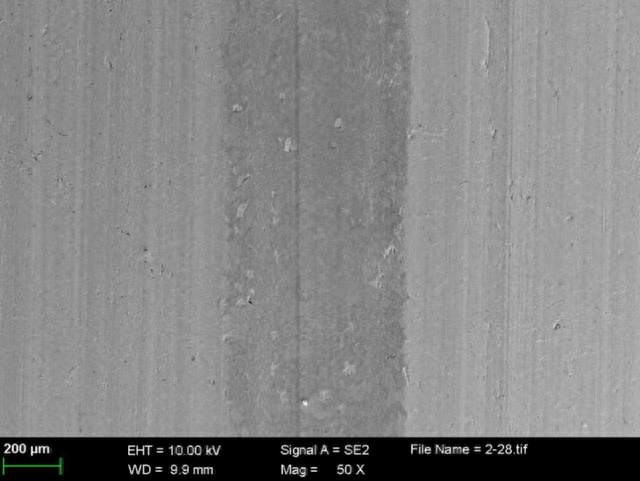
它的研究范围包括了滚珠的滚珠滚道,铁路机车的轮轨接触,汽车的车轮转动,各种机械铰链的运动,正是因为它的存在范围很广,所以对它进行摩擦学的研究是非常重要的。
杨建春发明的一种基于伺服马达驱动螺杆转动,使得螺杆上的重量沿着螺杆轴线方向运动,以达到对负载的可控调节,适合用于测量转动构件内部的滚动体的摩擦和磨损特性。
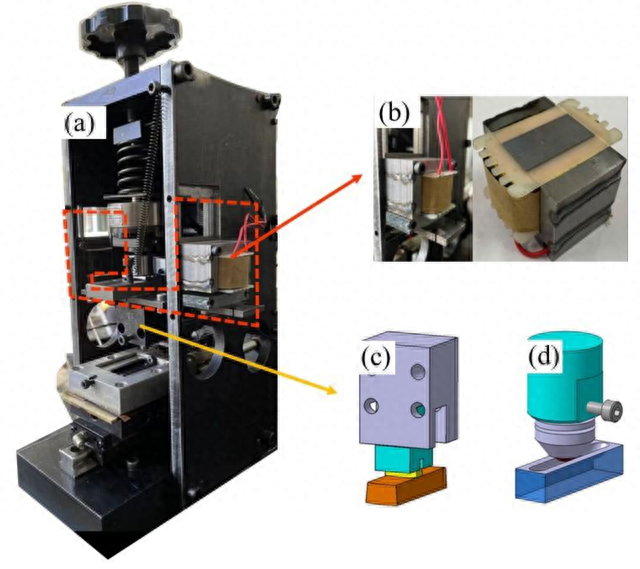
在实验装置的研制过程中,利用 ANSYS软件对实验装置及载荷体系进行了静态分析,并对实验装置的稳定性进行了检验。
实验结果表明,本实验装置的实际工作特性达到了设计要求,能够实现较好的工作状态,但仅限于常载条件下的实验。
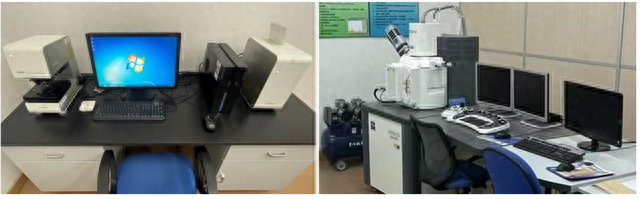
Kalin和 Viintin等人已经开发出了一台可以在很大的范围里调整运转速度,改变载荷,并且可以在很多接触表面情况下进行滚动摩擦磨损测试。
Faccoli M公司研发的一种新型的可测试轮轨钢轧制工艺,通过高速摄像技术实现了对轮轨钢轧制工艺参数的实时监测。
经过测试,该机器能正常运转,接着又进行了干、湿、干、湿三种状态的测试。本文对轮轨两种钢种的摩擦磨损特性和破坏机制进行了分析。

Manoj等人研制可变载荷、可调速、可改变润滑状态的摩擦实验机,对冷处理后的齿轮-轴承钢的滚动接触伴随的摩擦磨损状态进行了研究。
采用 LabView及 Matlab编程实现了测量控制,实现了测量过程中各种参量的实时测量,并进行了数据的保存与记录。根据所收集到的振动和噪声信号,对其进行了分析,以确定其是否出现了疲劳磨损。
Lee, Dongju等人研制出了一款高速滚动接触摩擦试验机,他们相信,这款滚动摩擦磨损试验机的使用将会改变过去只进行中低速滚动摩擦试验的现状,而进行高速滚动接触摩擦的研究将会使橡胶摩擦领域的研究水平得到更大的提升。
三、动载荷下的摩擦学性能测试装置的发展许多设备都会受到动载的影响,动载工况下的摩擦力不可忽略。以往,许多学者对各摩擦副在常数载荷下的摩擦磨损规律进行了深入的研究。
但是,对于动态载荷下的滑动摩擦实验机的研发和对其的影响规律的探讨还有待于进一步的完善,因此,动载荷下的磨损机制依然是一个迫切需要解决的问题。
杨红娟以高铁弓网面接触副的非正常磨耗为出发点,利用自主研发的动载滑动式摩擦磨损试验台,分别以纯碳片和金属片作为实验对象,进行了动载下的摩擦与磨损实验。
实验结果显示,在列车行驶过程中,由于车轮、轨道、风等因素的共同作用,导致了弓网面接触副发生了明显的振动现象,且其对摩擦学性能有显著的影响。

曹东海等利用自主研发的垂直动态载荷摩擦磨损试验台,对垂直振动条件下,不同材料、不同表面处理方式,以及表面粗糙度、动态振动幅值、振动波形等条件下,进行垂直振动下的静态摩擦因数的测试,并对其进行实验验证。
在静态摩擦力方面,以45钢、锰钢和铜为例,考察了其在超声波作用下的摩擦力。静态摩擦因数与动力幅,载荷大小,接触方式等相关。
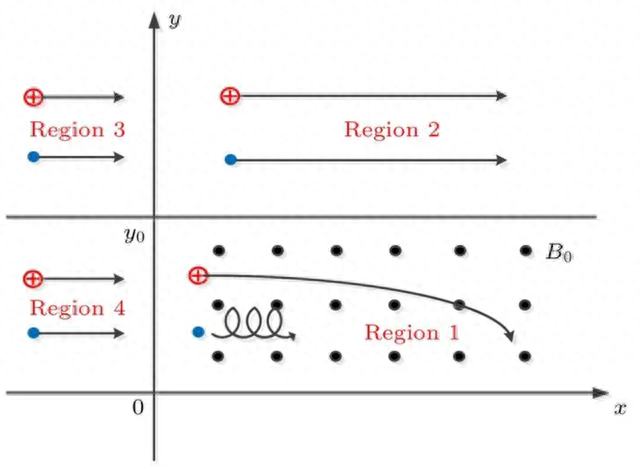
Y. Sasatani等在一台动载摩擦试验台上,从研究超声波振动对摩擦的作用机理出发,通过实验研究,得出了在某一特定区域,超声波振动的动力幅值,摩擦副相对移动速率,以及超声波振动的三个参数与摩擦副的相对移动速率,以及超声波振动的动荷载之间的关系。
超声波对摩擦阻力的影响随着动力载荷的增加而增加,摩擦阻力的大小与实验工况下的摩擦阻力呈线性关系。

另外,在超声波作用下,摩擦系数的下降还与外部负载有关,负载较大时摩擦系数的下降更为显著。结果表明:随着相对转速的增加,超声波的减摩作用逐渐降低,达到一个临界值后就不会随着转速的增加而改变了。
泰德尔特等研究了超声波在摩擦过程中,滑动速度,动态力和材质对摩擦的影响。研究发现,只要动载荷振幅大于0.1微米,就会引起摩擦因数的下降,并且在某一特定的区间内,动载荷振幅与减摩效应之间存在着显著的正向关系。
而随着摩擦速率的增大,超声波对摩擦磨损的影响也会随之减小。程光明等学者在前期工作和自己的工作的基础上,对振荡产生的摩擦进行了理论分析,认为振荡产生的摩擦本质上是一种微小的“腾空”现象。
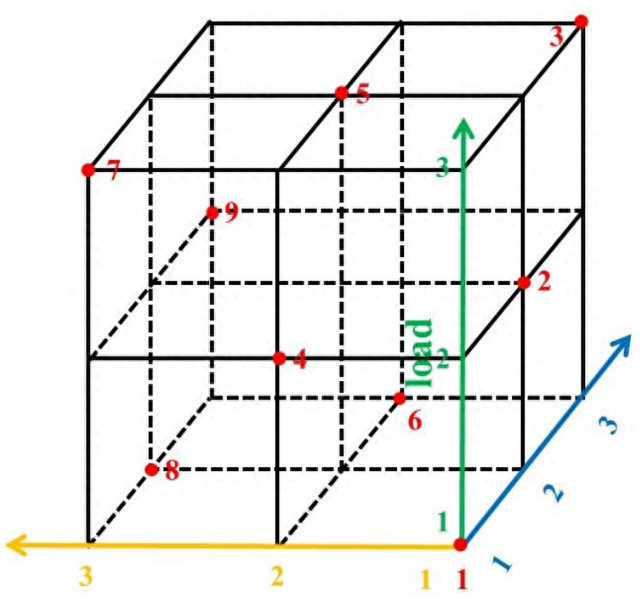
由于“腾空”现象的出现,使得与物体的接触面的实际接触面的时间变短,因此,在宏观上达到了减小的摩擦力。
随后,程光明在原有工作的基础上,在2000多年进行了进一步的研究,并在此基础上,进一步提出了由振动引起的接触面积减少引起的摩擦因子下降的观点。
并据此得出结论:一是由于声波在超声波声场中的辐射效应,使接触面相对升高。而振荡则能使润滑剂在接触面上的分散更为均衡和加深,从而改善了润滑效果。
结语目前已上市的动态负载磨耗试验台,基本上可以满足动态负载的要求,但是在动态负载调整精度、动态频率和动态力幅值等方面还需要进一步的改进,而且大多数都是动态负载的滚动接触或撞击型的摩擦磨损试验台。目前能用于滑动式摩擦磨损研究的实验装置还很少见。
参考资料
《Adachi K , Kato K. The micro-mechanism of friction drive with ultrasonic wave[J]. Wear, 1996, 194(1- 2):137-142.》《杨红娟. 振动对弓网电滑动摩擦磨损性能影响的试验研究[D]. 成都: 西南交通大学, 2014.》《Chowdhury M A, Helali M M. The effect of frequency of vibration and humidity on the wear rate[J]. Wear, 2007, 262(1):198-203.》