半 导 体 塑 封 模 具 模 架 设 计
丁 宁,曹玉堂,汪宗华,周小飞,赵 松,周逢海
铜陵文一三佳科技股份有限公司技术部
摘要
介绍了半导体封装专用模具模架基本结构、工作过程,指出半导体塑封模具设计时注意事项,核心零部件设计要点、计算公式;同时系统地介绍了半导体塑封模具各部件功能、作用、设计原则,为行业内人士了解半导体塑封模具技术要素提供了依据、有益参考,对半导体塑封模具设计人员具有一定的指导意义。
1 引言
随着科技进步日新月异,半导体塑封模具发展呈多元化发展,塑封工艺是半导体生产中极其重要的工艺手段之一,它具有质量稳定、生产批量大、成本低、效益高等优点,广泛应用于集成电路、半导体分立器件、电阻、电容、线圈等元件的封装。随着我国科技的发展,塑封工艺在不断更新,塑封模具的结构也在相应创新中。无论是采用先进的自动封装系统封装还是传统的单注射头、多注射头塑封模封装,其核心部件设计万变不离其宗。本文根据作者过去多年工作中所得的一些心得体会拟稿成文,愿与行业内人士共勉,望对大家了解半导体塑封模具的技术要点、使用与维护有所帮助。
2 塑封压机资料
按照所搜集的塑封压机资料,对确定好的模具总高进行校核。设计模具总高须注意以下几点:
(1)模具总高在油压机行程范围之内。
(2)开模距离满足上料、取料、清模的开模空间需要。
(3)上注射模注射头行程在注射油缸行程范围之内。
(4)注射头起始位满足塑封料投料空间的需要。
油压机上、下台板开模距离一般为750mm,上台面固定,下台板为动板,动板行程一般为300mm,安装模具后,开模空间一般在220mm以上,开模空间过小,会带来上料、取料、清模等操作上不便。模具总高一般设计在530mm左右,单料筒模确定总高时,一般上面高过下模,因为上面需考虑从料槽放置塑封料饼的空间,一般上模总高在310mm左右,下模总高设计在220mm左右。注射头及其连接杆安装在油压机注射油缸柱塞头端部,伸出上台面,注射头离料筒之间的距离,就是塑封料的加料空间,这个空间一般要求90mm以上,注射注射行程一般有295mm、300mm两种,注射头空走到行程尽头时,要求注射头从上模面能够可伸出5mm以上。如可伸出长度不够,注射塑封料时可能引起压力不足而导致型腔注塑不满。图1所示为一台单料筒模具的前侧视图,标注的几个尺寸表示了单料筒模具高度校核计算是用到的几个关键指标。
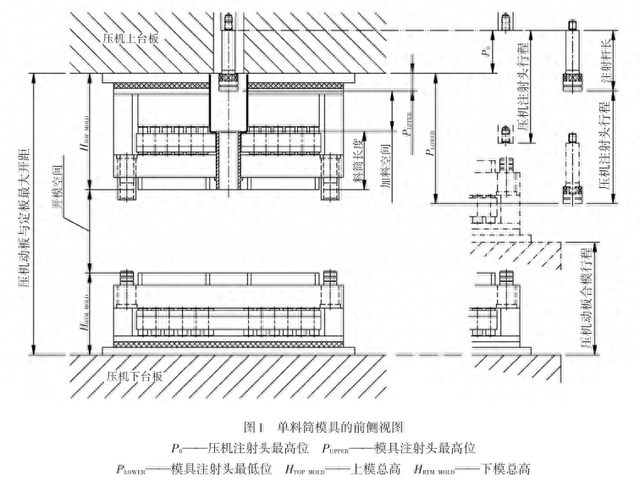
模架各板件、支撑件、承载隔热板都要求有较高的平面度及其平行度,组装后才可以保证整个分型面上各点合模压力相同,在对模架进行设计时,先设计好模架的平面排布图与闭合尺寸侧视图。
3 上、下模板的设计
模板的厚度一般选60mm左右,模板的正面安装有模盒及中心流道板,中心流道板一般为一个,模盒则有多个数模盒安装的个数一般为偶数,6模盒、8模盒数量最为常见。每个模盒安装孔有模盒定位销钉孔、连接螺纹孔、顶料杆过孔,在平面排布图上定出各个模盒的中心位置,一般各个模盒相关的连接孔与顶杆过孔为一组,它们相对于模板中心呈180°旋转对称。左边的各组模盒之间相对于模板Y向,也就是面对操作者的前后方向等步距排列,右边的各组模盒之间也按同样的规律排列,对固定安装的模盒或者中心流道板,在它们的取模孔相对的位置,可在模板上开设直径大于取模孔直径的低位,目的是防止取模操作时将模板表面划花或产生毛刺,从而影响模面平整度。
发热管孔一般沿模板左右方向插装。模架发热管为圆形直筒式,常用的规格有直径为 ϕ 12.5mm、ϕ 12.7mm两种,孔的直径按加大0.2~0.3mm设计,间隙过小,发热管加热后会涨紧难以拔出;间隙过大,会影响到热传导,甚至导致烧管。管孔内壁要求有较好的光洁度和圆度,发热管要求均匀排布,并刻印可插装发热管的功率瓦数,排布的规律是一般从中间到两边瓦数逐渐加大,目的是在发热管加热达到模温后模面各点温度基本均衡,一般控制在±5℃以内。按照模板左右一半模盒的数量,发热管的数量为半模盒数加一,当模面实际温度总是左右低于中间模面时,可在模具左右合适位置加装前后方向插装孔。发热管孔周围配有发热管的安装固定孔,安装固定孔的位置应注意适合发热管尾线的方便固定,对多点测温的油压机温控系统,要求上下模板每支发热管附近,可插装热电偶。无多点测温要求时,一般分别在上下模板的后侧左右对称位置各安装一支测温热电偶,油压机温控系统还要求上下模板各插装一支超温切断保护传感器。
4 支撑柱与支架的排布
在模架排布图设计时,涉及到支撑柱的排列,60mm厚的模板有很好的强度与刚性,但在较大的注射压力的作用下,注射料可能将模板挤弯变形,引起引线脚正面溢料。支撑柱排布时要求每个模盒下面排布均匀,排列间距上维持一定的密度,不能过于稀松,支撑件的位置不能与顶杆位置发生干涉,通常在顶杆间缝中对支撑柱进行有规律的等步距排列。
在数十上百吨合模压力的作用下,每个支撑柱起到支撑作用是强度与刚性要求保持一致,同一个支撑面上的截面面积相当的支撑件要求等高,高度精度控制在0.005mm以内,直径相对其它支撑柱小得多的支撑件,可适当加高0.01~0.02mm,目的是让它们在受压弹性变形后维持相当的支撑能力。支撑件的淬火硬度一般在35HRC以上,但同模支撑件须保持硬度的一致性。
为了管理方便,通常将上下模支撑柱作成高度一致,单料筒模上面推板空间不足的高度用形状较为厚实的支撑块来撑垫。
5 顶料机构的设计
推板与复位板紧贴固定在一块,动作是将安装其上的所有顶杆同时推出,或回位。塑封模上下模具开模时顶杆推出的合理行程为1.5~2mm,不同作用的顶杆,根据顶出腔深度的不同,顶杆有不同的高度。为避免出错,在封闭尺寸侧视图上确定分型面与推板推料面的高度,从而可以算出各类顶杆与复位杆的高度,型腔顶杆在塑封体上产生的印记不允许突出塑封体表面,塑封工序图上规定塑封体顶针印的深度,一般为0.05~0.15mm。流道顶杆设计时顶杆端面一般与流道底面平齐,引线框架顶杆设计上要求顶杆端面低于引线框架,如顶杆端面突出模面,合模时会压伤引线框架。
6 弹簧力的计算
出模顶料需要的力根据顶杆的多少进行估算。
直径为 ϕ 3mm以内的力的计算:F 1 =N×3kgf/根
直径为 ϕ 3mm以上的力的计算:F 2 =N×3kgf/根
弹簧预压力的计算:F 3 =L 1 (预压量,单位mm)×f n(弹性系数)×N(弹簧个数)
弹簧终压力的计算:F 4 =L 2 (总压缩量,单位mm)×f n (弹性系数)×N(弹簧个数)
设计上要求弹簧终压力大于顶杆顶出时所需要的力,一般单料筒模大于顶杆所需力约在 400~800kg,MGP模每个模盒设计弹簧总出力大于顶杆所需力约在40~80kg。
7 下模的气浮板设计
气浮板与油压机连接,气浮板需开设压机顶出杆过孔,尺寸根据压机资料来确定。上下安装板需开设与螺钉锁紧位置,对中间夹有隔热板的三文治形式的安装夹板,金属板之间有密集的互连螺钉,将隔热板夹紧。螺钉间距推荐距离为90~120mm,气浮板必须开设气浮孔与气浮槽,一般模具重约1t左右,模具安装调试时,需要有气浮功能辅助完成。当压缩空气(5~7bar)导热下安装板与压机台板之间,形成一根气膜层,这时候移动模具,产生震动,并显得异常轻松,常见顶棍孔位置与气浮孔设计示意图如图2所示。
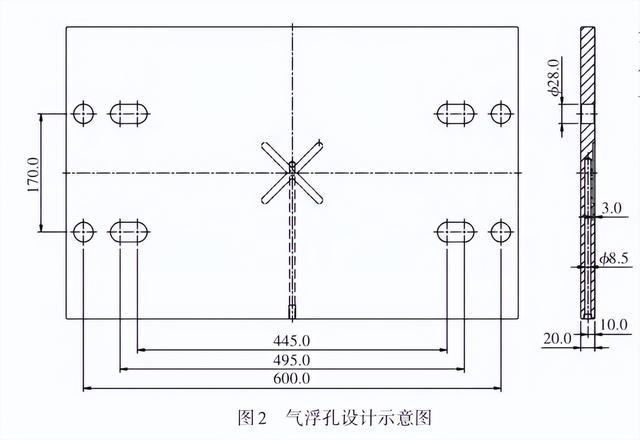
8 模具保温被的设计
模具正常工作时,模板内发热管在油压机温控系统的控制之下,断续的给各个模盒组加热,以维持塑封料的正常模温需求。为防止热量过度辐射散失,设计一套模具的保温被,可以减缓温度散失,降低模具能耗。
上下模具保温被分开制造,一般在模具的前后左右四侧面贴张保温材料,设计时在模套上开孔让出模具侧面各种功能性结构,如发热管孔、手柄孔等。
9 引线框架上料架的设计
定位针与托板中心位置需考虑热膨胀影响因素,通常考虑在预热温度(140℃),正常模温(175℃)下引线框架不与定位针发生干涉。计算方法是:
P 1 =P 2 ×0.9985
式中 P 1 — —引线框架托板定位针距离,mm
P 2 — —对应的引线框架定位孔按模盒设计步距计算的定位孔之间的距离,mm
0.9985 — —材料为AL6061的引线框架上料架相对模面步距的热膨胀差引起的折
算系数,AL6061 的热膨胀系数为23.4×10 -6 mm/℃,模具的热膨胀系数取 11.0×10 -6 mm/℃,温差为预热台工作时上料架温度与室温差
上料架定位(见图3):上料架无论在模面,还是在预热台上放置时需要考虑料架自身的定位,正常封装生产过程中,需配备至少两副料架轮流替换,塑封料固化过程中,其中一副料架放置于模具上,开模取料时才可以取出。在固化等待的过程中,另外一幅备用的上料架可以同步进行排料片的工作。
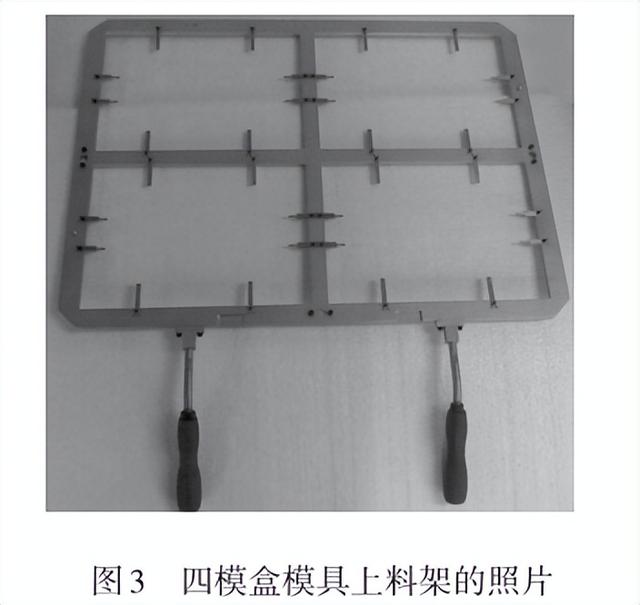
10 预热台的设计
预热台结构上包括加热板、发热管、温控箱3部分,加热板的大小根据引线框架上料架的大小来设计,加热板上按照模盒位的对应位置设计模盒数量的几组引线框架承接块。
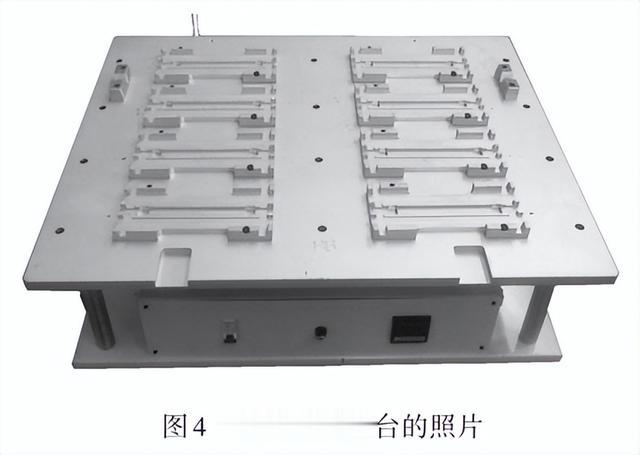
11 结论
半导体塑封模具技术是一项细致复杂的工作,思路要清晰、结构要合理;在整个设计过程中,设计、审核要协调好思路和意见,在设计开始前,要把半导体塑封模具整体结构的评审工作做好,避免设计人员的重复劳动和不必要的损失。经过多年的设计研发和使用实践,对半导体塑封模具技术有了一个深刻的认识和研究,并形成了一套较为系统的半导体塑封模具设计标准,为促进中国半导体封装产业持续、快速发展做出自己应有的贡献。