摘要:
随着封装工艺的不断发展,芯片 I/O 数越来越多,高密度芯片封装必须采用倒装焊的形式。底部填充作为芯片倒装焊封装后的加固工艺,填充胶与倒装焊使用的助焊剂的兼容性对于研究倒装焊电路的长期可靠性至关重要。分析了底部填充胶与助焊剂的兼容性,以及助焊剂的残留对底部填充胶加固效果的影响。若助焊剂清洗不干净,会导致底部填充胶的粘接力下降,影响器件的质量。
关键词: 底部填充胶;助焊剂;陶瓷封装;芯片倒装
1
引言
随着封装工艺的不断发展,倒装焊封装技术已经逐渐成为封装行业的主流技术之一。倒装焊封装是先在芯片上制备凸点,再将芯片凸点面朝下贴装到基板上,通过焊接的方式实现稳定可靠的电气互连。作为加固材料的底部填充胶主要沿芯片边缘注入,借助于液体的毛细作用,底部填充胶会被吸入并向芯片基板的中心流动,填满后加热固化,如图1所示。倒装焊技术中芯片是由凸点作为媒介,实现芯片与陶瓷外壳产生的互连。凸点需要通过焊接或者电镀的方式与芯片产生连接,一般通过焊接与陶瓷基板产生连接。在传统的倒装焊技术中助焊剂的使用不可避免。一般倒装焊后会对残留助焊剂进行清洗,以此来除去助焊剂。清洗干净的芯片如图2(a)所示。若助焊剂清洗不干净,会导致芯片表面出现助焊剂的痕迹,如图2(b)所示。倒装焊后工序为底部填充工序,助焊剂的残留可能会对底部填充产生影响。助焊剂一般由松香、有机酸、有机溶剂等构成;底部填充胶由环氧树脂、固化剂、填料等构成,其中环氧树脂与固化剂的反应是底部填充胶固化的关键反应。若助焊剂残留,可能导致底部填充胶的成分与助焊剂的成分发生复杂的物理或化学变化,导致底部填充胶无法正常进行固化。
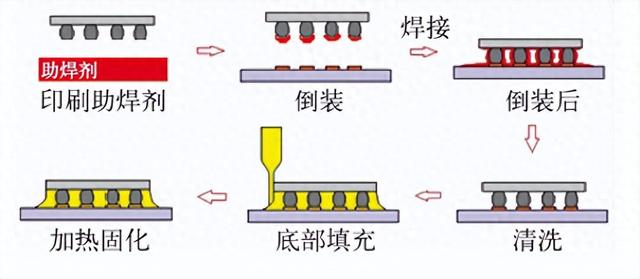
图1 底部填充工艺流程示意图
本文研究助焊剂残留对底部填充胶的影响,探究助焊剂是否对底部填充胶的固化以及其粘结强度产生影响,这对于集成电路倒装焊封装的研究十分重要。
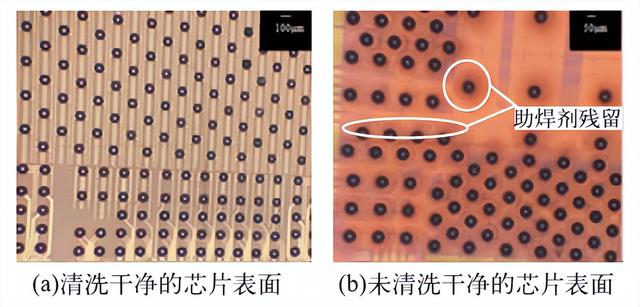
图2 芯片(带凸点)表面清洗后的状态
2
试验材料与方法
本文主要探讨助焊剂和底部填充胶之间的兼容问题,主要从凝胶时间、粘结强度等方面进行研究,对混入不同比例助焊剂的填充胶的凝胶能力和粘结强度等进行测试,以此研究助焊剂残留对底部填充胶的影响。
2.1实验材料
实验的陶瓷外壳均由京瓷公司生产,陶瓷种类为A440;实验选用的芯片为硅基芯片;实验选用的助焊剂为A公司的水溶性助焊剂;实验选用C品牌环氧树脂底部填充胶,其黏度为40~50Pa·s(25℃),填料为硅化合物,含量40wt%~70wt%。
2.2实验内容
本文主要研究助焊剂残留对底部填充粘接强度的影响,主要对二者的兼容性进行研究,采用试验组和对照组进行对比的方法,分别对凝胶时间、粘结性能等进行研究。
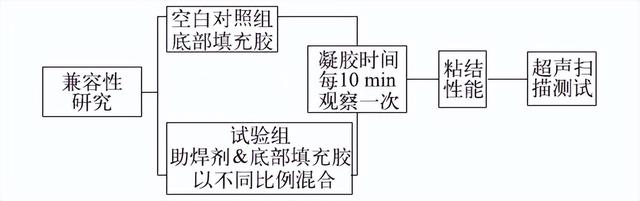
图3 助焊剂与底部填充胶兼容性试验流程图
针对底部填充胶与助焊剂的兼容性,我们分别将底部填充胶和助焊剂按照质量比1:1、2:1、3:1、5:1以及10:1的比例进行均匀混合,各取0.1g样品在150℃下进行固化监测,每隔10min进行一次检测,最长检测至120min(120min为胶本身固化时间),估计出凝胶时间。
随后用混合后的胶将芯片(5mm×5mm)粘接在陶瓷外壳上,并进行芯片剪切测试,测试其粘结强度。同时,模拟倒装器件状态,在陶瓷外壳上均匀涂抹一层助焊剂(约3×10-4g/mm2),使用纯胶将芯片(5mm×5mm)粘接在陶瓷外壳上表面,其结构如图4所示,并进行芯片剪切测试,测试其粘结强度。具体参数为剪切速度254mm/s,距陶瓷面的剪切高度15μm,剪切力极限值为70kg。
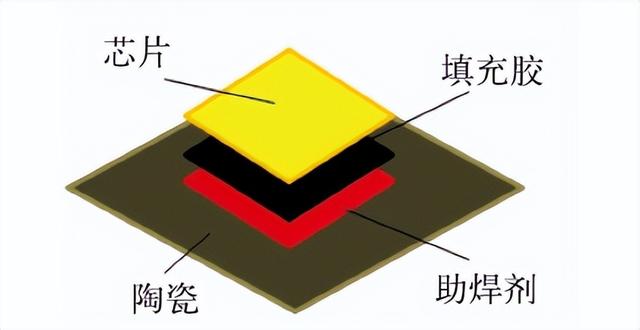
图 4胶接结构
分别对助焊剂清洗干净和未清洗的两个倒装焊器件进行填充,固化后进行超声扫描。
3
实验结果与分析
3.1不同质量比的凝胶时间
凝胶时间是指环氧树脂变稠到拉丝中断的时间,可以在一定程度上代表环氧树脂的固化时间。为了确认助焊剂的残留是否会导致底部填充胶延迟固化或者影响其固化,本文每隔10min监控样品的状态,结果如表1所示。
纯胶在10~20min时开始凝胶;比例为10∶1时,20~30min时开始凝胶;比例为5∶1和3∶1时,均在30~40min时开始凝胶;比例为2∶1时,在40~50min时开始凝胶;比例为1∶1时,无法在固化时间内凝胶以及固化;由此可以推断,助焊剂混入底部填充胶,会延迟固化甚至阻止固化。助焊剂比例越高,阻碍效果越明显。
3.2粘结性能结果分析
粘结性能主要表征底部填充胶粘结芯片和陶瓷基板的能力,分别将底部填充胶和助焊剂按照质量比1∶1、2∶1、3∶1、5∶1以及10∶1的比例进行均匀混合,与纯胶的粘结性能进行对比。

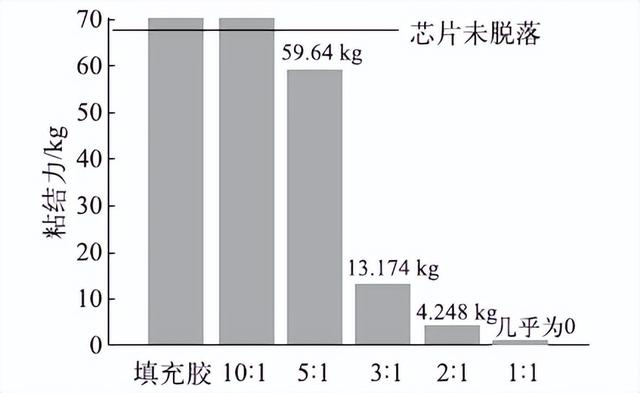
图5 不同比例混合的样品的粘结性能结果
如图5所示,纯胶在70kg的剪切力下,并不会发生失效;比例为10∶1时,未发生失效;比例为5∶1时,粘接力为59.640kg;比例为3∶1时,粘接力为13.174kg;比例为2∶1时,粘接力为4.248kg;比例为1∶1时,粘接力几乎为0。由此可知,助焊剂残留量越大,粘接力越低。这说明,助焊剂残留对底部填充的力学性能具有一定的影响,且残留量越大,降低粘接性能越明显。
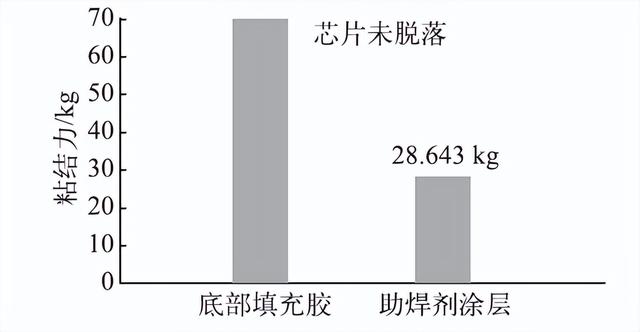
图6 底部填充胶粘接在助焊剂涂层上的粘结性能结果
如图6所示,纯胶在70kg的剪切力下,并不会发生失效;但在陶瓷表面增加一层助焊剂后,粘结性能明显下降,仅为28.643kg。由此可知,助焊剂残留量较小,由于位置集中,集中位置的助焊剂浓度增加,仍会导致粘接力下降。这说明,局部助焊剂残留可以导致粘接性能降低。
3.3超声扫描结果分析
本文分别对助焊剂清洗干净和未清洗的两个倒装焊器件进行填充,固化后进行超声扫描。采用反射扫描模式,对器件的底部填充层进行扫描,扫描结果见图7。
如图7所示,图7(a)为清洗干净的器件进行底部填充后的超声扫描图,图7(b)为未清洗的器件进行底部填充后的超声扫描图,由图中可见均没有发生空洞和分层。这说明助焊剂未清洗干净进行底部填充,无损超声扫描检测无法有效检测出底部填充胶与芯片或者陶瓷表面发生分层的问题。
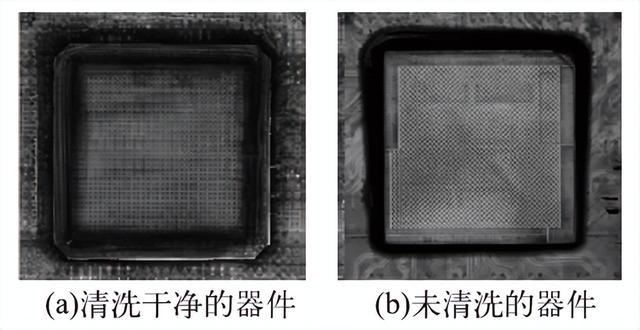
图7底部填充位置的超声扫描结果图
4
结论
底部填充在芯片倒装之后,若助焊剂清洗不干净,会导致底部填充延迟固化甚至不固化,同时会导致底部填充胶的粘接力下降,影响器件的质量。助焊剂残留量少但比较集中,仍会导致底部填充胶的粘接力下降。倒装焊后的助焊剂需清洗干净,才能有效保障倒装焊器件的长期可靠性。