前言:钣金广泛应用于各个行业,如汽车、航空航天、建筑、家电等。钣金工艺的主要步骤包括剪、冲/切、折。其中,剪切是将材料按照所需尺寸进行切割;冲压则是利用模具对材料进行塑性变形,以达到所需的形状和尺寸;折弯则是将材料按照所需角度进行弯曲。此外,钣金工艺还需要使用到各种辅助设备,如开卷机、校平机、去毛刺机、点焊机等。
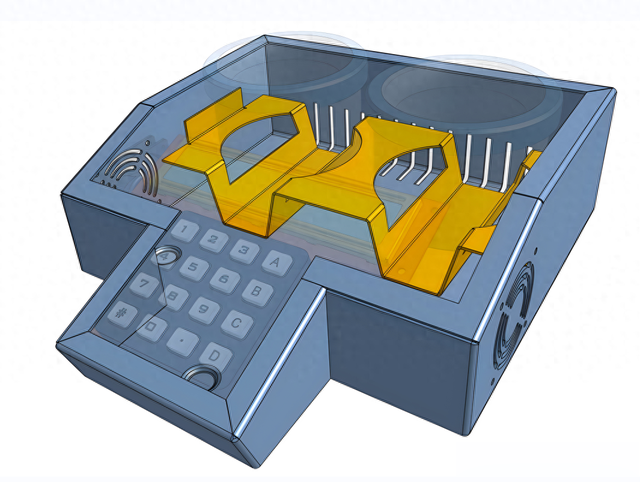
一、剪板机下料工艺
1. 剪板机下料工艺应用范围
1.1 该规程适用于各类黑色金属立体边缘毛坯材料的剪切以及类似性质的下料工作。
1.2 待剪钢板厚度宜控制在 0.5~6 毫米区间,最大宽度可达到 2500 毫米。
2. 原材料要求
2.1 原材料必须遵循严格的技术标准进行验收。
2.2 原材料选用冷轧钢板,其外观不得出现严重的擦伤、滑痕、杂质、锈斑等现象。
3. 设备及工艺装备工具
3.1 配备板子、钳子、油壶、螺丝刀、手锤等工具。
3.2 游标卡尺、外径千分尺、钢板尺、钢卷尺、直角尺、划针等计量器具。
4. 工艺准备阶段
4.1 熟谙图纸及相关工艺要求,精确掌握工件结构及尺寸。
4.2 依图取材,仔细核对所选原材料是否满足工艺规格。
4.3 考虑降低成本及提升利用率,配套裁剪法的运用应合理测算。
4.4 将合规原材料有序码放在机床周围。
4.5 为保证机器运转顺畅,应对各润滑点实施加油作业。
4.6 检查剪床刀片之锐度及稳固性,依板厚恰当调节刀隙(详见附表 2)。
5. 工艺流程
5.1 初步测量刀口与挡板两侧间的距离(依据工艺卡片而定),重复多次后实际剪切小样进行精度核实。如公差符规要求,即可继续正式剪切;反之则需调整定位距离直至达标。随后调试纵板,以保持与横板或刀口呈 90°角且稳定可靠。
5.2 开机前需确认板材各边线相互垂直,首件检验符合工艺卡片要求后方能正式投入生产,否则需重新调整纵横板。
5.3 辅助人员需协同作业,全程监控加工过程中的尺寸、毛刺、角度变化,并与操作员保持良好的交流互动。
5.4 完成剪切的半成品或成品须按不同规格分类摆放,防止混乱。
5.5 为减缓刀片磨损,必须保持钢板板面及机床台面清洁,禁止工具及其他材料在剪板机床床上摆放。
5.6 剪切板料宽度不宜小于 20 毫米。
6. 工艺规范
6.1 根据生产批量采取合理的套裁方法,先下大料,后下小料,尽量提高材料的利用率。
6.2 零件为弯曲件或有料纹要求的,应按其料纹、轧展的方向进行裁剪。
6.3 钢板剪切截断的毛刺应符合表 1 的规定
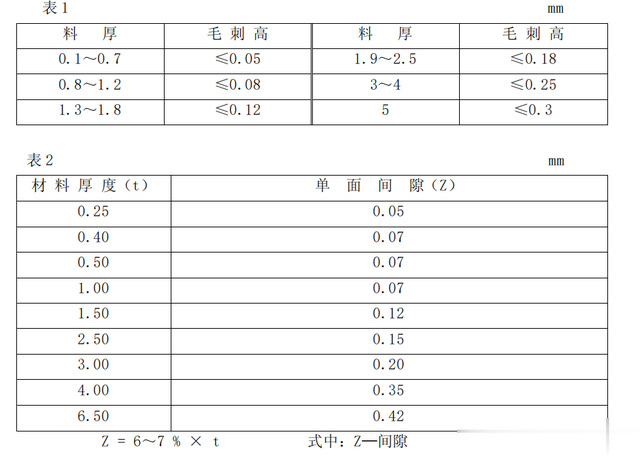
二、冷冲压工艺
1. 适用范围
本守则适用于压力机加工各种黑金属板料制件(包括落料、裁料、冲孔、弯曲、压平、翻边、拉伸、挤压等)。
2. 材料
2.1 材料应符合图纸要求。
2.2 应具有良好的表面质量,表面应光洁平整、无锈蚀等缺陷,厚度应符合公差规定。
2.3 冷轧钢板板面,不允许翘曲、表面有擦伤、滑痕。
3. 设备及工艺装备
a.压力机
b.模具
c.扳手、镊子、手钳、毛刷、油壶、螺刀、手锤;
d.游标卡尺、钢板尺、卷尺及其它测量工具。
4. 工艺准备
a)检查材料的宽、长、厚及料纹方向是否符合工艺卡片的要求。
b)检查模具是否符合图纸、工艺的要求。
c)按工艺选用压力机。
d)检查压力机有无异常状况,各种旋钮(按钮)位置是否正确,打料装置的位置是否正确,电机开动前离合器一定要处于非工作状态。
e)给压力机各加油孔加油。
f)在安装调整冲模时,一定要使压力机的闭合高度大于冲模的闭合高度。
g)在安装冲模时,找好压力中心,调好间隙,紧固在机床上,在紧固螺栓时,要注意均衡紧固。模座下的垫板要适当、平整、不得堵塞漏件孔。为了防止在生产过程中下模座和垫板移动,应垫上纸或砂纸(一般裁料后在 3 毫米以上,模具比较大时用砂纸)。
h)在进行冲压作业前要先开几个行程的空车,检查有无异常音响,当判定正常后在开始生产。
i)按工艺要求的顺序和要求调好定位装置(可用试冲零件,专用工具或常用量具调整)。
5. 工艺过程
5.1 生产过程中模具刃口应经常涂油。
5.2 操作者必须进行首件检查,中间抽查,合格才能继续加工。
5.3 在加工过程中必须经常检查紧固件是否松动,观察模具是否正常。
5.4 落料、冲孔、剪切、裁断毛刺应符合表 1 的规定
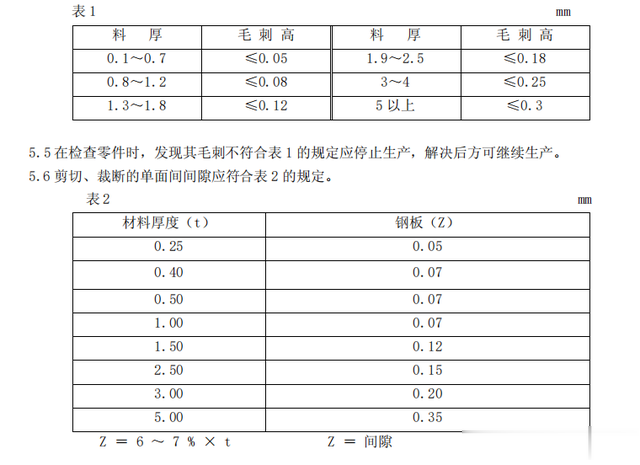
三、钢板折弯工艺
1. 适用范围
本守则适用于折弯机床加工的各种黑色金属的各种角度的折弯加工。
2. 材料
2.1 材料应符合图纸要求。
2.2 应具有良好的表面质量,表面应光洁平整、无锈蚀等缺陷,厚度应符合公差规定。
3. 设备及工艺装备
a. 折弯机;模具;
b. 扳手、毛刷、手锤、油壶;游标卡尺、钢板尺、卷尺、角度尺等。
4. 工艺装备
4.1 检查材料的长、宽、厚,料纹方向应符合图纸要求,板材应清洁卫生。
4.2 根据图纸选用合适模具。
4.3 检查折弯机状况并进行卫生清理及保养。
4.4 工件加工完后应对折弯机及模具进行卫生清理。
5. 工艺守则
5.1 折弯守则的几点说明:
5.1.1 本折弯守则根据现有折弯机凸凹模的几何形状而定。
5.1.2 不同弯边圆角采用不同 R 的凸模弯制,不同的材料厚度则需调换不同深度(即不同宽度)的凹模弯制。
5.1.3 本守则列有弯角尺边、弯外翘边、弯内翘边的有关极限尺寸表(表四、五、六、七、八)及材料厚度,弯边圆角与凹模深度关系 表,弯边圆角展开尺寸表和各种材料最小弯曲半径表(表一、二、三)
5.1.4 复式弯边是角尺边、外翘边、内翘边的数种情况的相互结合,其弯制方法可参照表九。
5.1.5 本守则所列的各项参数可作为产品图纸弯边设计的依据。
5.2 材料厚度、弯边圆角与凹模深度关系表(表一)
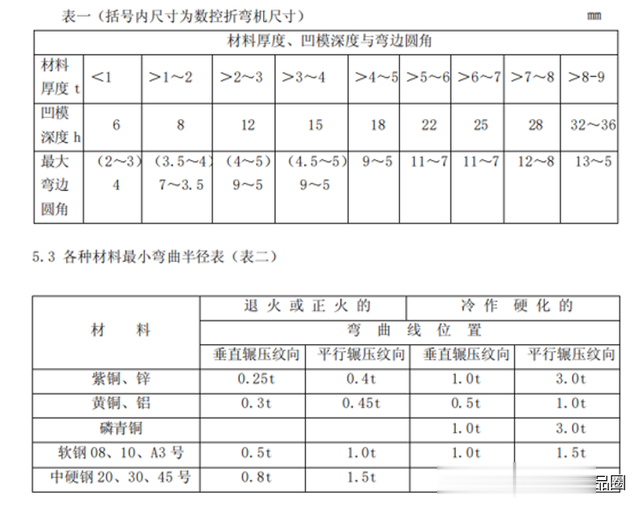
5.4 弯边圆角展开尺寸
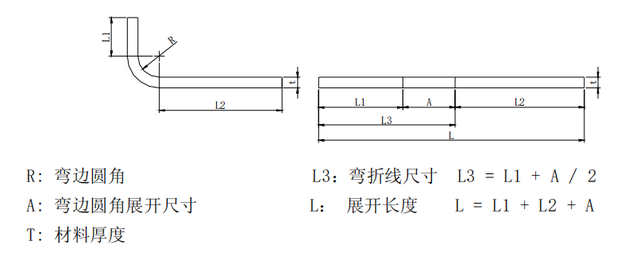
四、角钢下料工艺
1. 适用范围
本工艺守则适用于角钢的下料。
2. 设备及工具
a)根据角钢规格使用的冲床及工装;
b)角钢校直机;
c)V 型切断模具;
d)活动搬手、钢板尺、划针、宽座角尺、钢卷尺、手锤。
3. 准备工作
3.1 按分配的任务熟悉图纸和有关工艺文件,弄懂图纸和工艺文件规定另件几何形状,各部分尺寸。
3.2 不同规格的角钢应分别放置,整齐堆放、防止堆放变形。
3.3 根据施工批量进行套裁,先下长料,后下短料,充分提高材料利用率。
3.4 所用角钢材料 1 米内直线度超过 5 毫米时,均需经过校直,方可下料。
4.工艺过程
4.1 根据零件图纸尺寸或下料明细的展开尺寸调下模具定位装置,角钢端头紧靠定位板,先冲试样,进行首件检查尺寸偏差是否在规定范围,如符合图纸或本守则公差,才能正式加工,若不符合图纸尺寸,应调正定位板,必要时可调正模具。
4.2 角钢下料加工时应将原料角钢首端和末端变形部份切除。
4.3 需要进行冲孔、切角等延序的在制品件应分别堆放,便于搬运,防止混料。
4.4 加工完的角钢在制品或半成品件,应分清规格、型号经检查合格后转下道工序或半成品库。
5.工艺要求
6. 1 下料长度允许偏差见下表
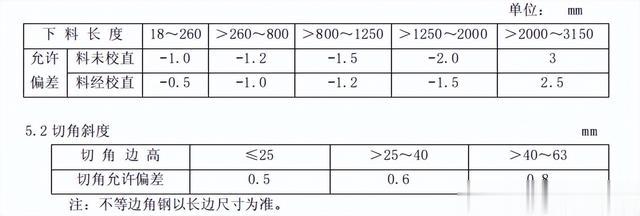
五、箱体结构焊接工艺
1. 适用范围
本守则适用于箱体结构焊接。
2. 材料
电焊条、图纸和有关技术资料规定的半成品零部件和辅料。
3. 设备及工具:
a. 交(直)流弧焊机,CO2保护焊。
b. 电焊钳、面罩。
c. 平台、柜体胎具(根据柜体结构大小配备)。
d. 钢卷尺、角尺。
e. 各种焊接夹具、手锤、清砂用尖锤扁铲等。
4. 准备工作
4.1 接受生产任务单后应熟悉所分配的任务,充分了解图纸中的技术要求和各部件焊接尺寸。
4.2 领取所有焊接部件,按图号分类堆放,便于操作时对号取件准确无误。
4.3 所有半成品件在运输过程中应轻拿轻放,防止因受外力碰磕、挤压,造成工件变形。
5. 工艺过程
5.1 操作者应熟悉自己经常使用的设备、胎具、工夹具、量具的性能及操作保养方法。
5.2 接受任务后应熟悉图纸和工艺文件,在图纸和有关技术文件没有弄懂以前切勿盲目施工。
5.3 工序转来的半成品零件和部件是否符合图纸和其他技术文件要求,如不符合技术要求,应找出原因及时解决,切不可将不合格的零部件组装到骨架结构上。
5.4 检查所有的使用的焊接工胎夹具应是合格的。
5.5 首件焊接的左右侧壁要按图纸严格检查,各部位尺寸,角度正确与否,如发现错焊或严重扭曲变形,应及时改正和整形。
5.6 基本骨架完成后,按图纸要求焊接电器元件的安装梁、板、支承件、门板、铰链及其他零部件,其焊接顺序应是自上而下,由前到后,先关键件后一般件。
六、电焊工工艺
1. 适用范围
本守则适用于箱(柜)体焊接。
2. 材料
电焊条,电焊丝
3.设备及工具
a)交(直)流电焊机,CO2 保护焊;
b)电焊钳;
c)电焊帽;
d)清砂用手锤、尖锤;
e)扁铲等;
4.工艺过程
4.1 熟悉 GB324《焊缝符合表示法》。
4.2 熟悉电焊工常用设备及工具的性能及保养方法。
4.3 接受工作任务后要认真消化图纸和有关工艺文件,备齐所需的各种工艺装备,并检验工艺装备的完好性,正确无误。
4.4 根据工件材料和焊缝要求,选择焊条型号规格和施焊电流,如下的选择电流方法可供参考。
4.4.1 焊条选择应从以下两方面考虑。
a)焊条的种类应依焊接材料及焊缝要求选择。
b)焊条的直径的选择应按工作厚度焊缝的几何形状,及焊接规范等因素进行考虑,在不影响焊接质量的前提下为了提高劳动效率,提倡选用较大直径的焊条,下表所列 数据可供参考。 交(直)流电焊机。

CO2保护焊
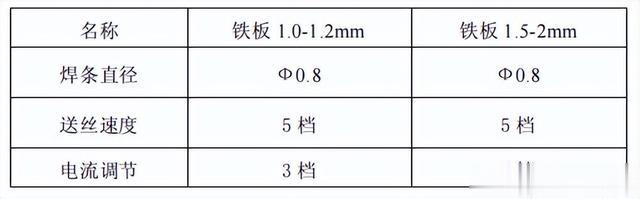