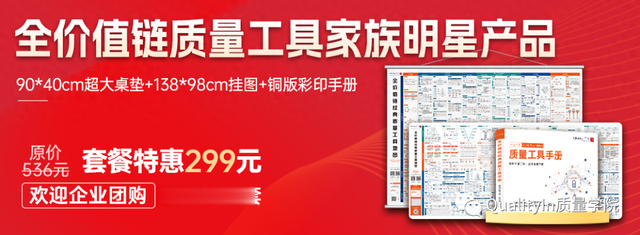
职场中,我们内心本愿都是想做正能量满满的好员工,无奈,职场这个江湖,看不见的刀光剑影。掌握几招必杀技防身,保护好自己才能考虑后续的发展。职场防背锅术,SQE必须学会!
真实案例:
小李是一个刚入职不久的SQE,目前在一家公司上班有半年了,之前的项目虽然算不上一帆风顺,但是总算还能顺利开展了。
但就在新项目量产了,据说很多项目阶段未暴露或者未解决的问题,在量产可能会出现。
到时候一切责任都是SQE的,出现让SQE背黑锅的情况,那么怎么避免呢?
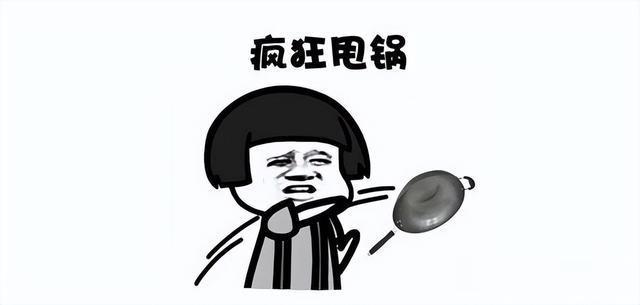
下面的一位从业多年的资深SQE给出了很好的建议,一起来学习!
SQE前期必须充分介入!!!
不介入的危害:
一、研发设计的装配公差不合理。
供应商进入量产后有些零件弄到下限,然后生产线不能装配停线,但是工人往往都不知道怎么回事,有很多公司没有技术,工程上线分析原因;
工人或生产经理就直接把火撒在SQE头上,说你们怎么管的供应商,东西都装配不上,SQE找IQC分析了半天,尺寸全都合格。。。
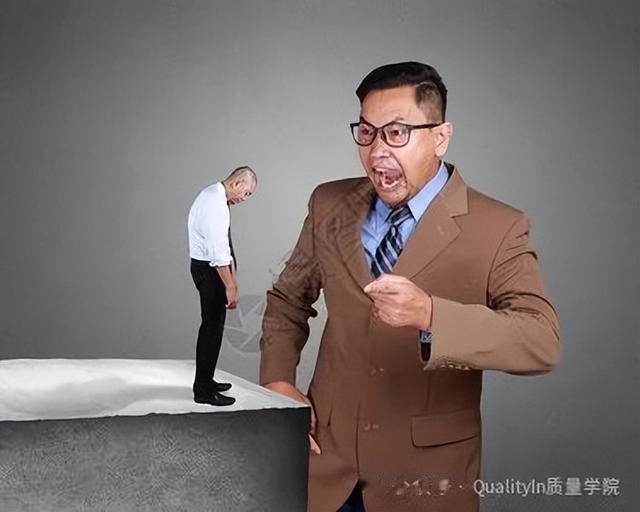
二、前期没人和供应商约定好包装方式,也没对包装方式做足够的验证。
实际这应该是SQE做PPAP的一部分,但有很多公司SQE只管后期,前期给供应商的样品承认是项目或工程做的。
最后供应商的产品送过来,包装已经稀巴烂,内部零件全都破损,最后演变成SQE要处理的质量问题。
但是供应商拒绝换更好的包装,除非给他加价。SQE夹在中间勉为其难。
三、供应商内部良率很差,样品都是精挑细选出来的,量产后成天叫不出货。
最后采购一问说是供应商内部品质问题导致,然后顺利成章把活推给SQE,让SQE驻厂辅导。
SQE驻厂后才发现供应商的制程能力严重不足,用的设备精度根本无法保证产品公差,供应商也不愿意投资更好的设备,也不愿意花人力全检。
四、公司内部是对产品外观有要求的,但是没有明确的检验标准。
即便是同一批零件,今天这个检验员看了有灰,明天那个检验员看了有划痕,后天再一个检验员看了有色差。
然而图纸没有提到有任何外观要求,研发说外观要求不应该写入图纸,这是品管的事。SQE最后沦为一个做外观检验标准的人。
最后定严了供应商做不到,定松了,内部QE和生产不干,有些供应商和你们采购或老总有关系的还会反咬一口,说你们SQE连标准都定不清楚,要求都不明确,而且这些要求都是量产后提出的,能力太差。
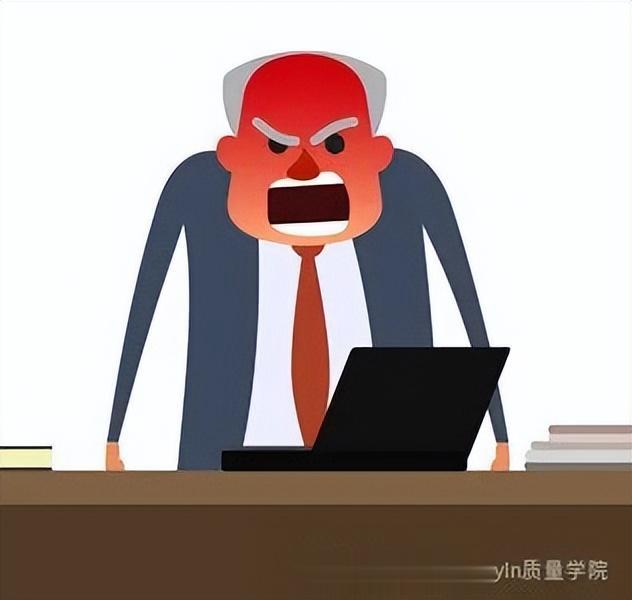
五、供应商的产品为镀锡产品,结果在仓库放了三个月变黄了。
供应商说不接受退货,因为电镀产品只能保证3个月保质期,是你们自己仓库环境不好和超期不使用导致。
因为前期没约定保质期,SQE最后还要四处协调,看看内部能否可控制库存周转时间和改善内部仓库温湿度管控。(例如蓄电池,在库房久置未装车,亏电导致装车后无法启动)
六、图纸没有规定粗糙度,但是你们最后产品因为粗糙度产生了严重的客户投诉,最后SQE才发现供应商和你们IQC没有人去检测粗糙度。
因为一直没有标准,最后内部就说反正供应商制程不稳定,小批量试产时粗糙度怎么是好的?
你们SQE赶紧去把客户投诉损失的50万RMB去找供应商谈判,让他们赶紧接受。
你谈不定,最后总经理说就是你SQE能力太差,标准也弄不清楚,供应商也搞不定。
采购在一边隔岸观火,说这个是质量问题而非商务问题,SQE去谈判。
七、供应商因为人手紧缺。
PPAP样品时,他们觉得不重要的尺寸,虽然他们内部不合格,但是还是故意变成合格,省去和你们沟通浪费的时间。
但是你们内部资源也紧缺,IQC对供应商的PPAP样件全尺寸不进行任何的检验和复核,偶尔复核几个重点尺寸,然而你们研发有些装配尺寸是没划入重点。
直接上线生产,试生产的人有很多问题没有观察仔细,实际生产线装配是有点困难的。
最后量产了,生产线发现装配一直都比较费工时(需要用力才能插进去,自己有时候还要找锤子敲)。
最后不干了,说零件有问题,SQE经过确认后发现尺寸竟然是超差的,质问供应商为何PPAP都合格,供应商狡辩说双方测量系统有差异,最后折腾了半天,内部对SQE还是愤愤有加,抱怨连连。

八、前期没有人和供应商约定。
最小包装量和纸箱和托盘尺寸大小,量产后供应商托盘太大,仓库说放不进货架,生产说纸箱子太大生产线放不下,最后所有人推给SQE让其去解决
九、电镀品图纸没有要求盐雾试验。
量产后客户投诉盐雾试验24小时有红锈,最后发现客户没和研发说清楚要求;
或是和Sales说了,Sales没告诉研发,或是客户没有图纸给你们,让你们自己弄图纸和标准,最后总之就是遗漏了。SQE你去搞吧。
作为质量管理岗位,SQE应该是综合管理能力要求非常高的岗位,可以说要具备“既能上天,又能入地”的能力。
SQE的使命就在于通过对供应商的品质进行管理来保证进料品质。其核心目的在于保证进料的品质而不是去帮供应商做QE。
一方面,SQE论专业是比不过供应商的。但SQE遇到技术问题就不管了吗?当然不是。更何况在SQE的日常工作里,只有很少的问题是需要很强的专业技术知识去解决的。SQE应该更多的时间去推动供应商改善,人都是逼出来的,供应商当然也不例外。关于供应商品质提升这一块,审核还是很有必要的,但审核需要有手段,需要审核到实处,而且审核后的管理更是重要。因为很多问题供应商自己看到或没看到,都懒得去做(人的本性),这个时候SQE就起到一定的作用。
另一方面,对于8D/5C等改善报告,SQE一定要将其落实到实处(至现场稽核就是非常好的手段),保证供应商改善了,而且是永久性的改善。最后,最重要的也是最根本的,SQE一定要有power,要有绩效考核以及对供应商经济处罚的权利。不然,供应商有时也会不理你。
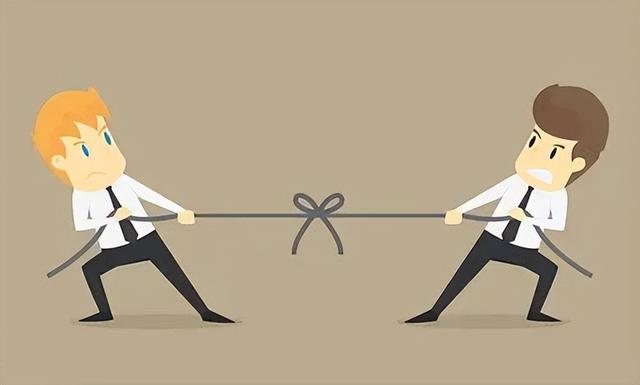
解决材料问题是SQE的事情,提升供应商能力也是SQE的工作,孰重孰轻,应根据你所服务的公司的性质来定义。
话要说回来,轻易不要谈到什么供应商能力的“提升”,一般的SQE都没有这个资格,也没有这个能力。
首先,你所负责的供应商都是专业的生产厂家,都不是在市场上打拼了一天两天的,论管理/论专业你都不可能比专业的人士高到哪里去,除非你更专业,若是你更专业我想你也不会只是一个SQE,你至少已经成为了一个Manager。
当然SQE本来就以客户身份自居,完全有一些理由去挑战供应商,但若是每次都讲得道理不够充足,你的威信会丧尽,你的人格魅力也将荡然无存,到那时,除了个客户的身份,你什么都不是!
品质工作大部分情况是对比标准或差异找出问题,你的依据都是别人制定的标准,也就证明你的工作是建立在别人基础之上的,所以你不可能有所谓去提升专业人士的能力。那该如何去讲呢,可以使用控制这个词,SQE的工作其实就是供应商品质控制,你的管理其实就是控制,不要拓展的太广。至于如何控制,凡是做过质量的都可以讲出一堆指标/一对措施。
很多事情,只有自己经历了,才会有感觉。书本上得来的,最终要靠实践来检验,在实践中体会,在实践中总结,最终才会变成自己的。
其实,供应商质量工程师这个岗位是非常有挑战性的。供应商质量工程师所接触的范围广,打交道的人也多,对自己的提升有很大的帮助。
在更多的时候,供应商质量工程师更象一个管理者,对各个方面的知识都需要了解,如果得到很好的锻炼,职业前景应该是很不错的。不论是自己创业,还是作为职业经理人,都有着很好的基础。因此,供应商质量工程师要对自己,对工作有信心。
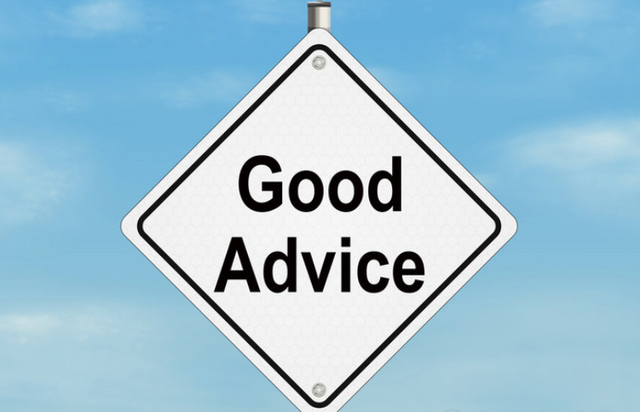
其实作为供应商质量工程师,在给供应商培训或者在公司内部进行培训的时候,常常会讲起以下几条比较有用的原则,在这里也一并记录,希望能对各位有所启发:
目标驱动一切:对供应商质量工程师来说,不论是供应商整体提升,还是新项目开发,抑或是质量整改,都是我们工作的目标,那么我们所有的工作与努力,都是围绕这些目标展开的。目标是方向,也会点燃激情。
同时,这一原则不仅仅适用于工作,也适用于生活,可以思考一下我们生活的目的,是否明确,我们是否在向目标走去。
第一次把事情做对:有了目标,就需要努力去达成,而第一次把事情做对就是为了能够最快最有效地达成目标。第一次把事情做对,会省去后续更多地麻烦。当然,要做到第一次把事情做对,就需要很好的策划了。
所谓磨刀不误砍柴工,先磨好刀,会使砍柴更顺利,而没有磨好刀,没砍几下就钝了,重新磨过,就造成太大的浪费了。
PDCA循环:对于质量人员而言,PDCA循环的重要性及实用性应该是不言而喻了。不仅在新项目管理中要用到,在质量整改中要用到,而且在前面提到的目标的达成过程中也要用到。
团队工作是必需的:众所周知,单打独斗的日子早就过去了,对质量人员来说,想必体会会更深,团队,小组在工作中随处可见,但是要学会真正成为一个团队,让团队充分发挥作用。在生活当中,同样也可以,并且也必须借助团队的力量获得成功。
接下来,分享一份完整版《供应商质量管理》培训教材,从8个部分阐述了SQE的工作职责和供应商质量管理的基本知识,非常有参考价值。
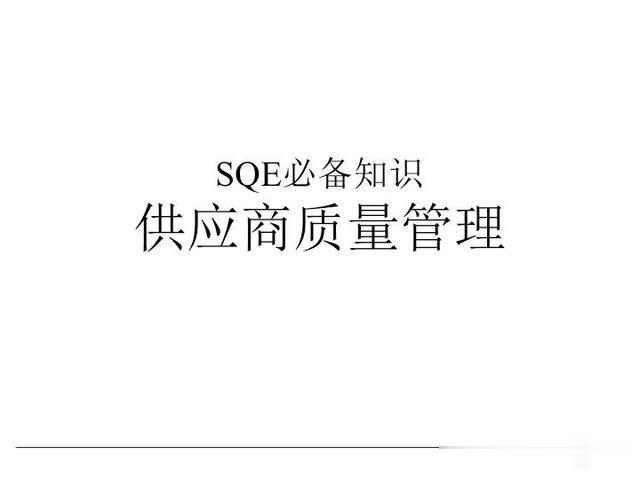
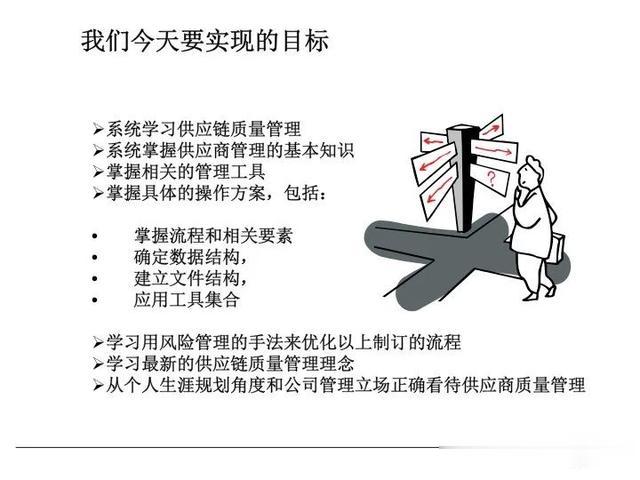
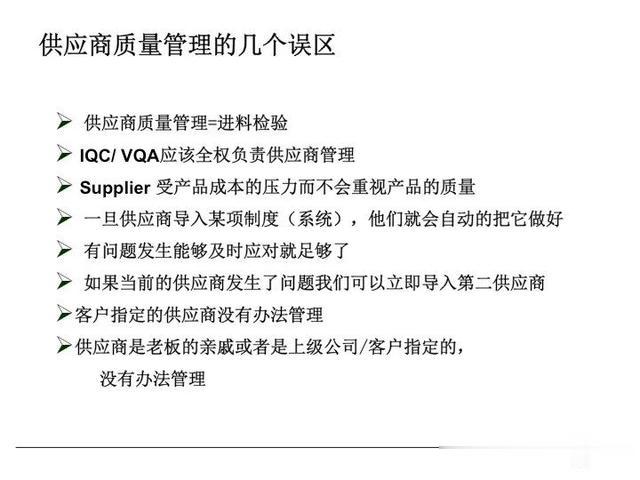

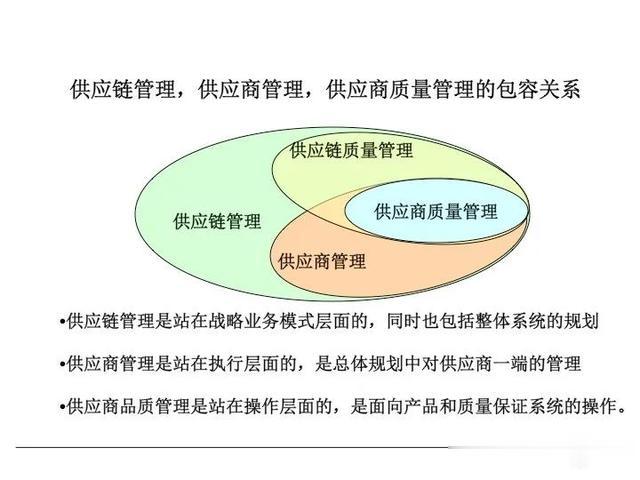
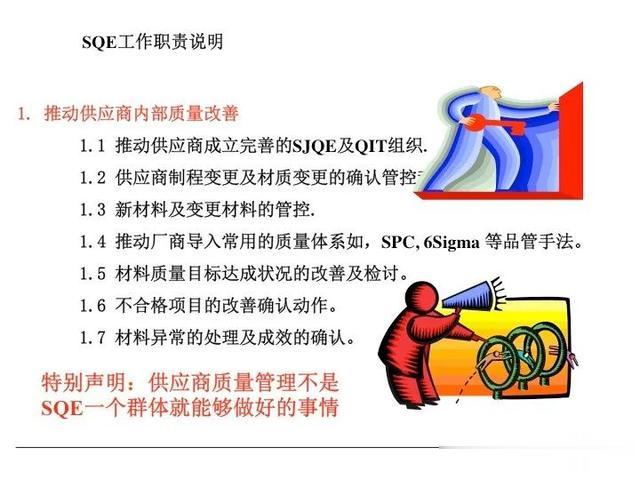
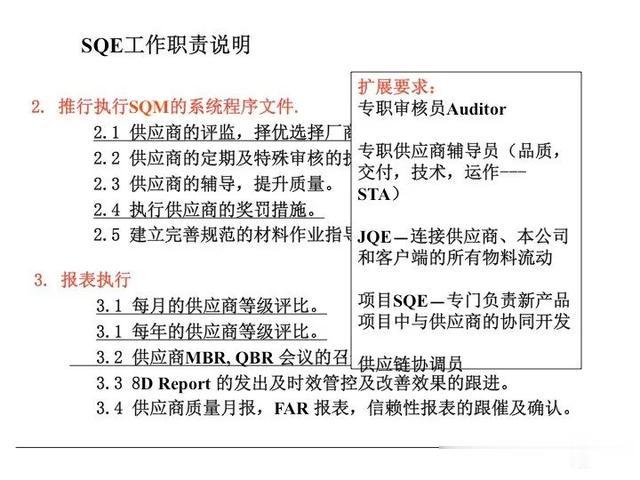
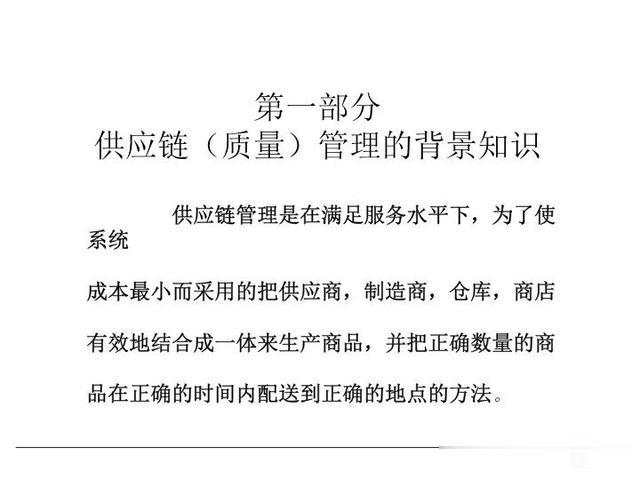
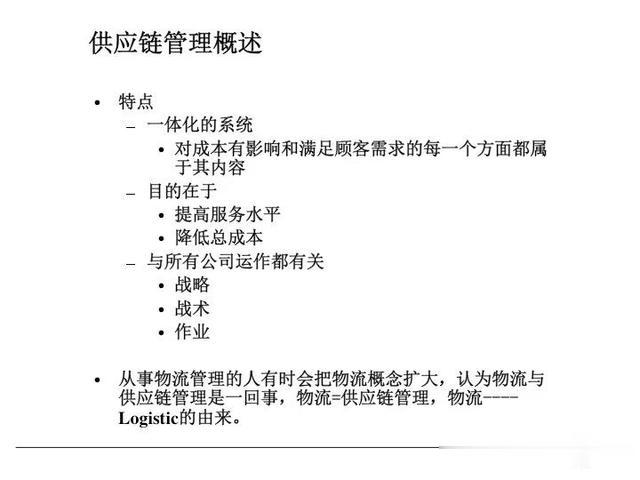
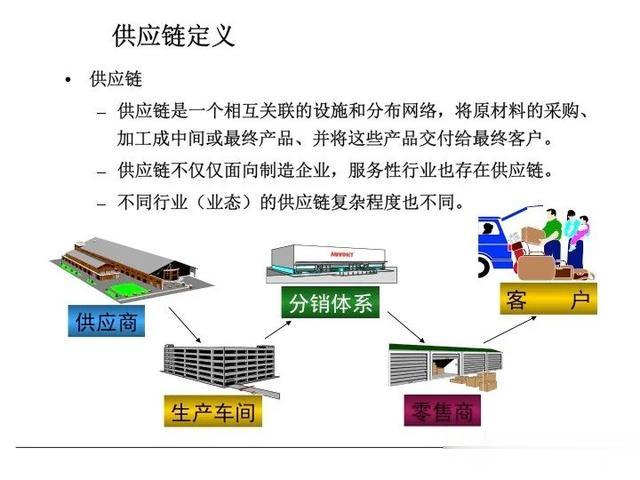
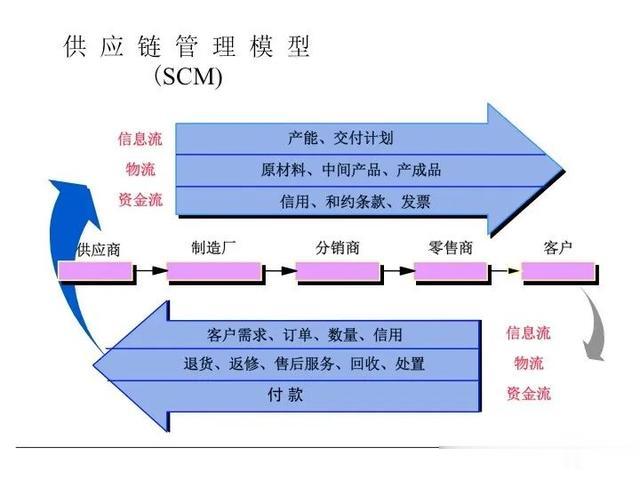
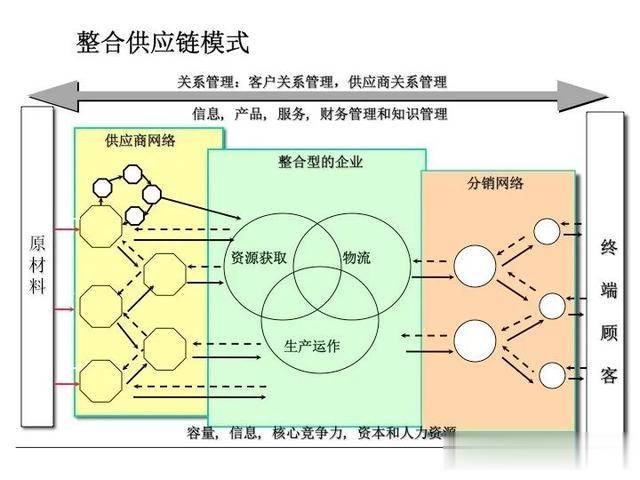
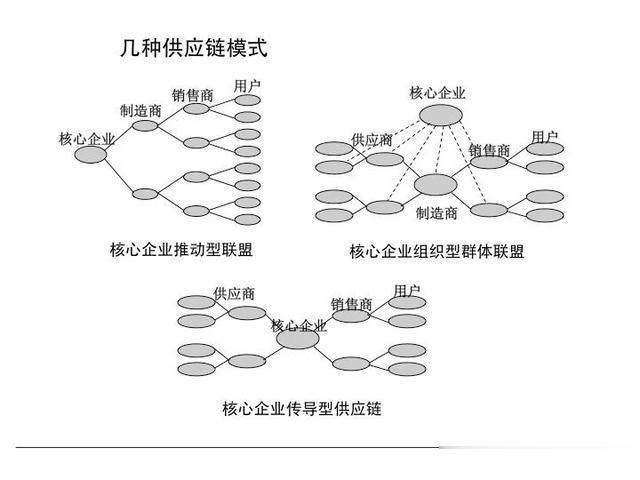
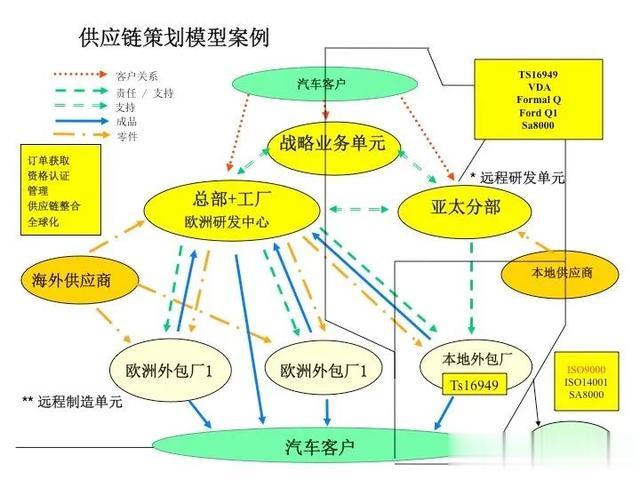
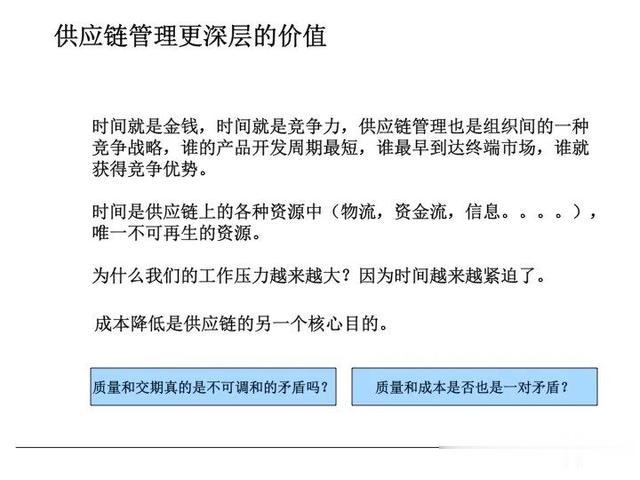
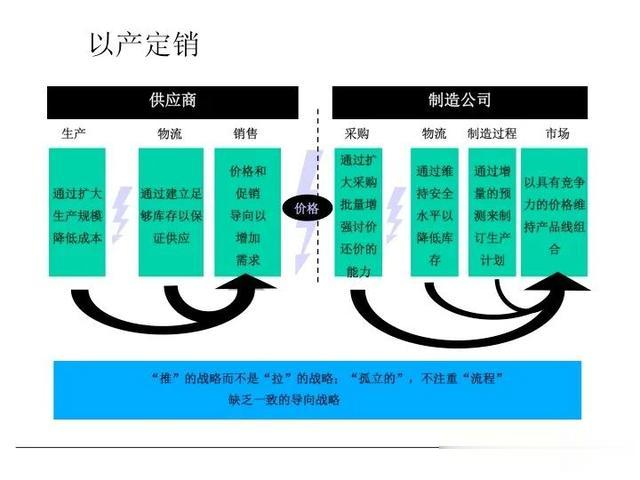
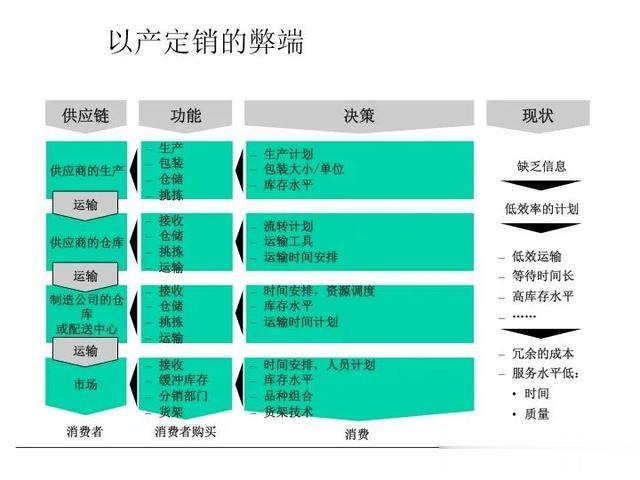
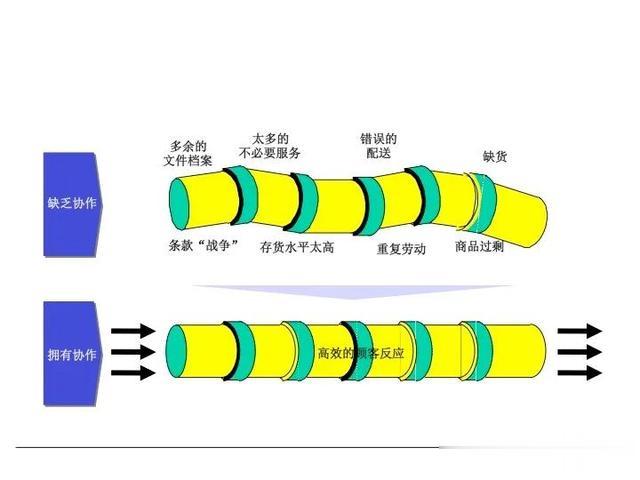
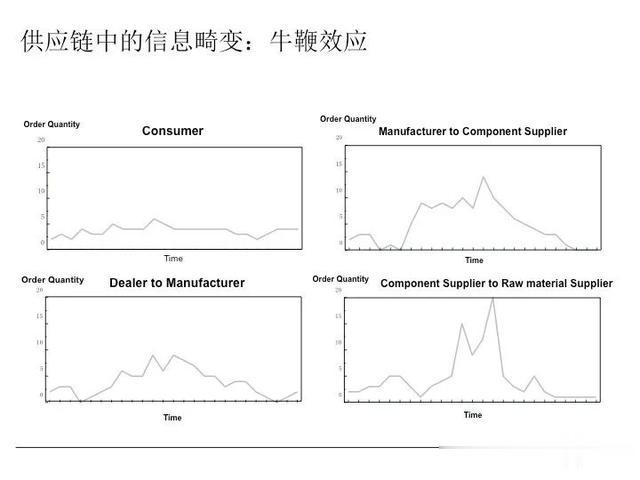
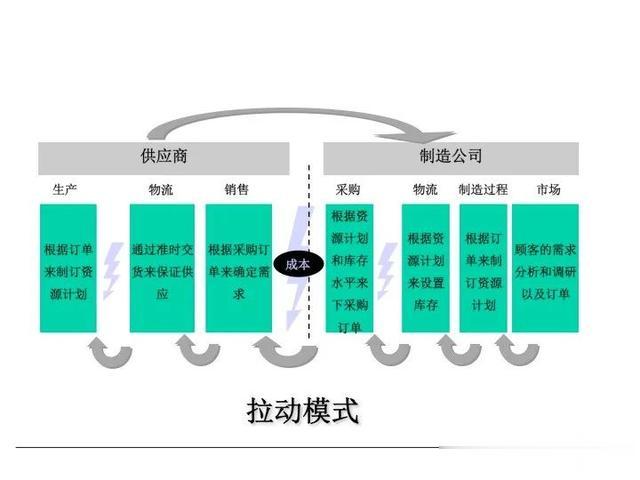
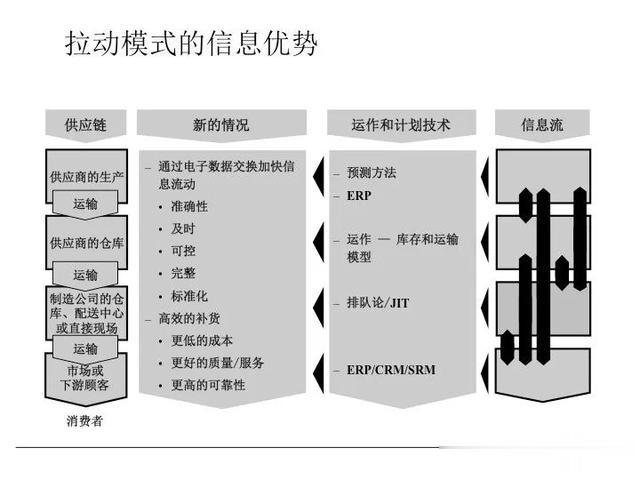
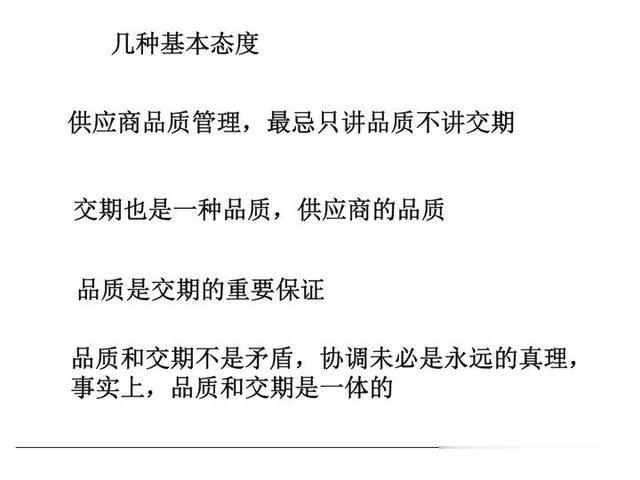
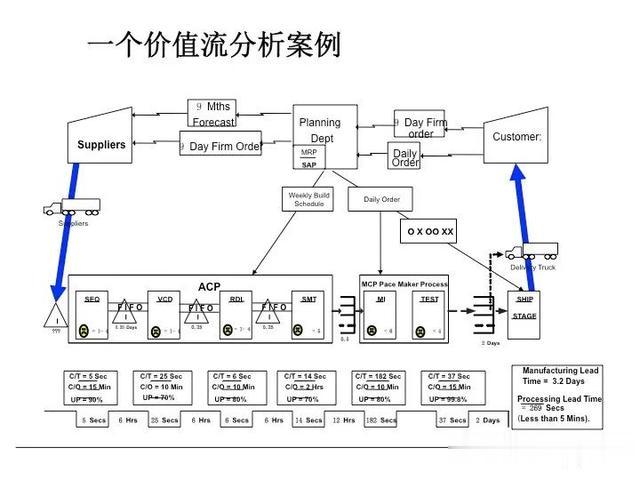
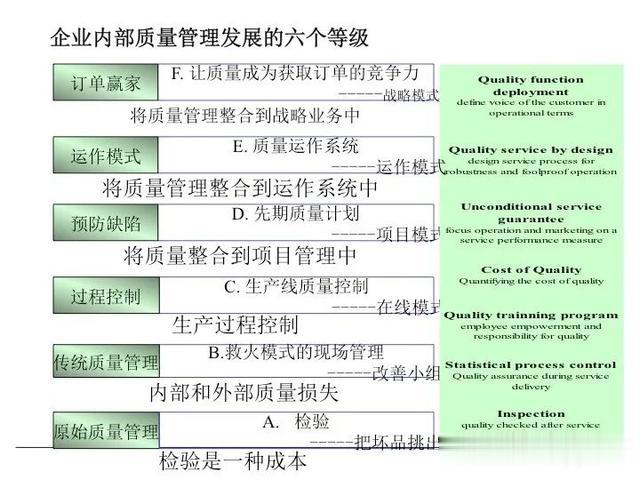
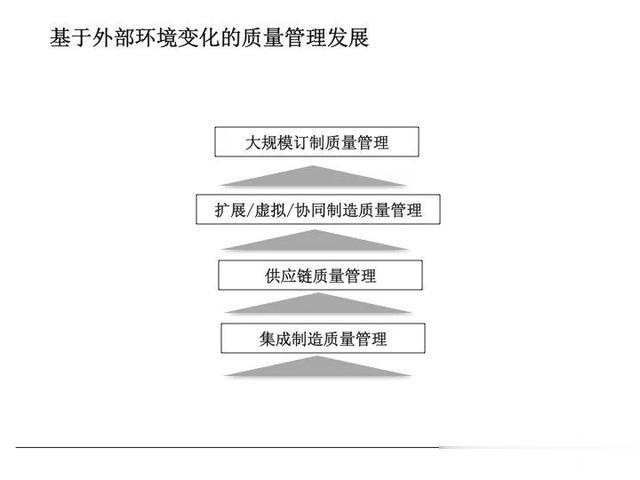
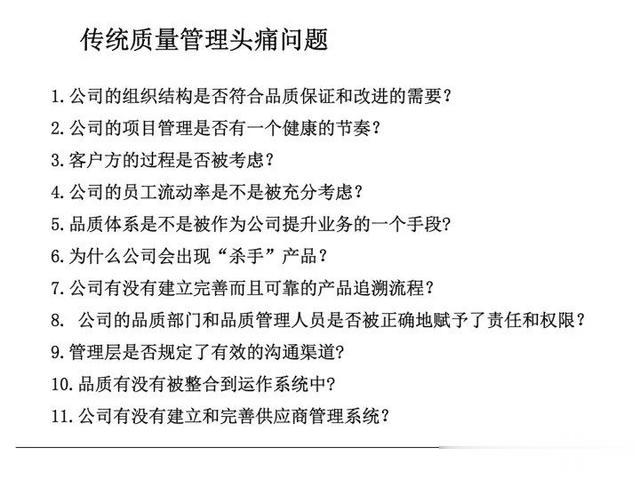

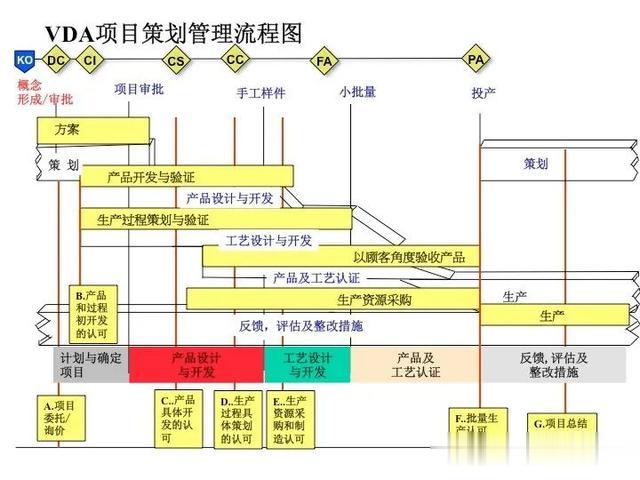
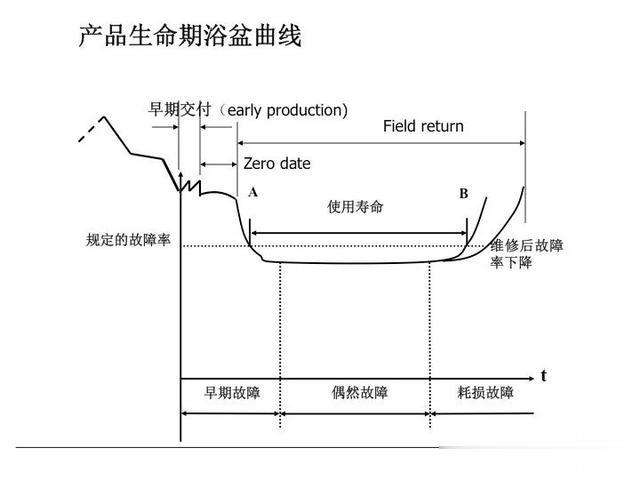
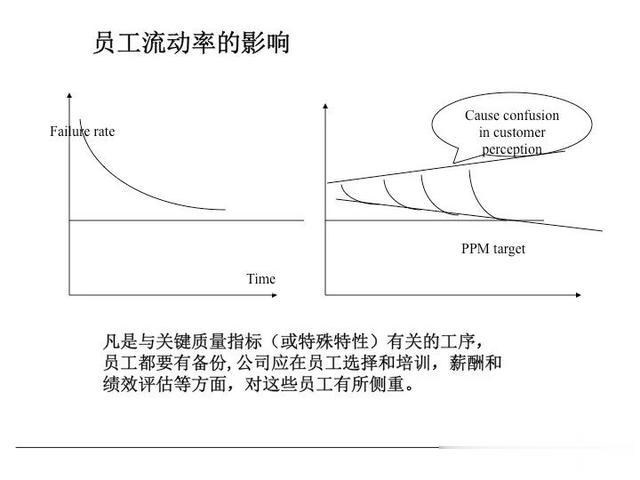
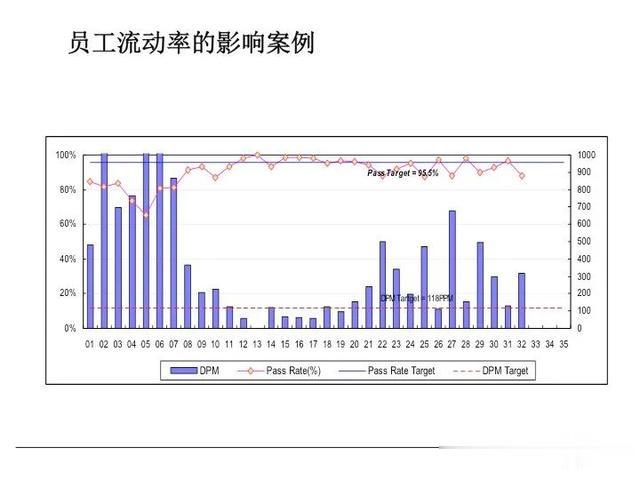
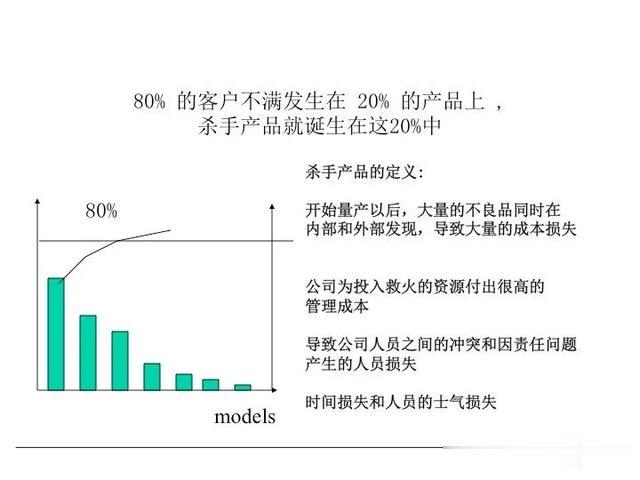
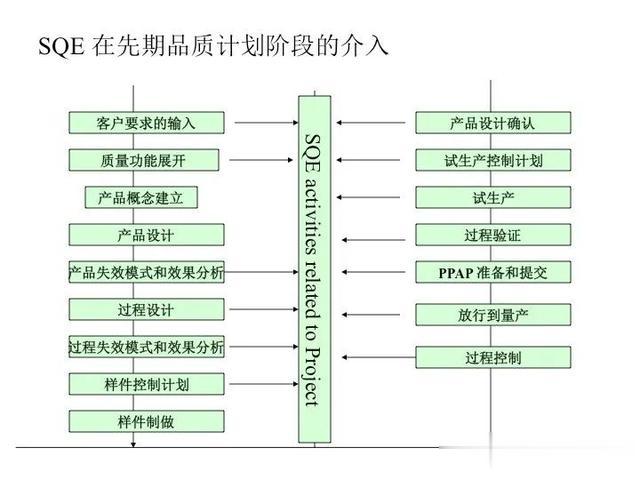
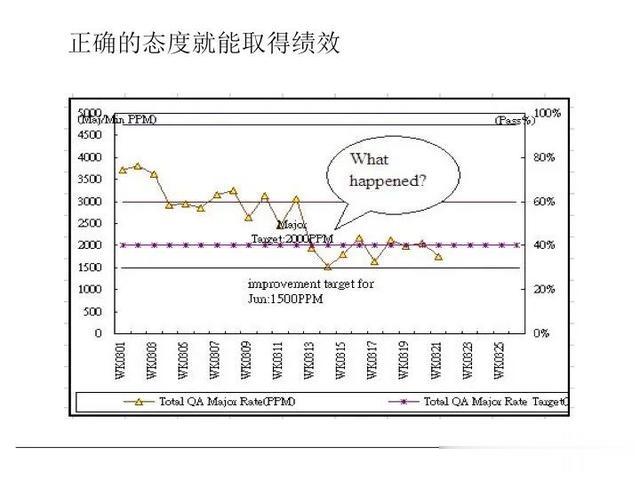
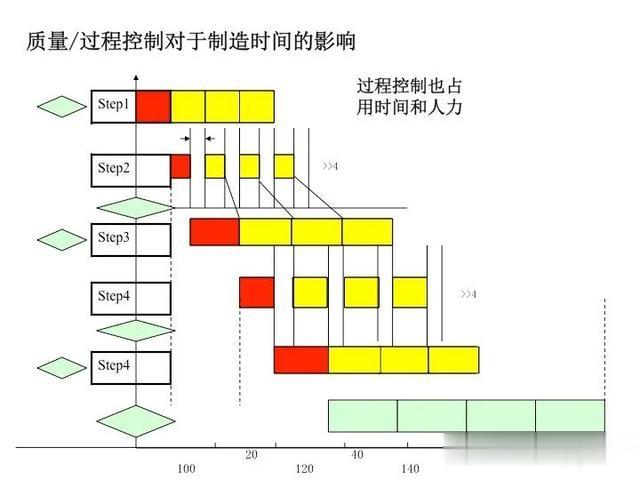
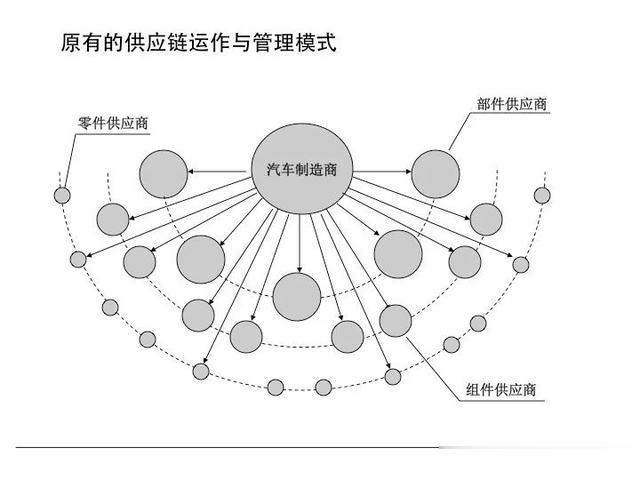
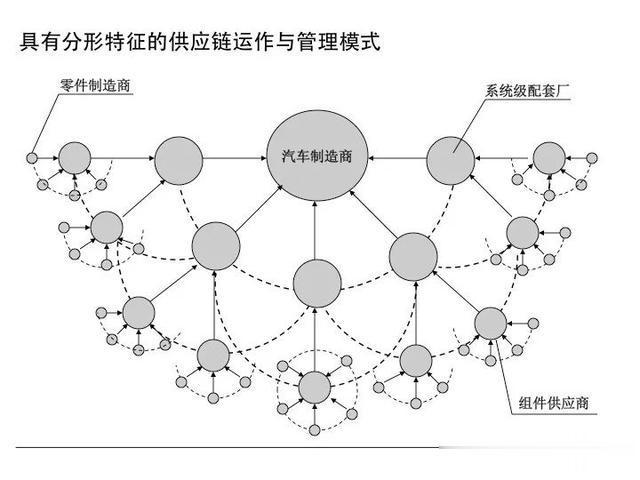
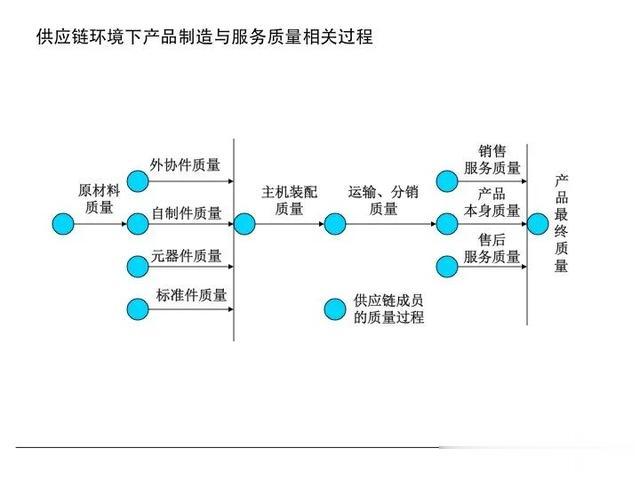
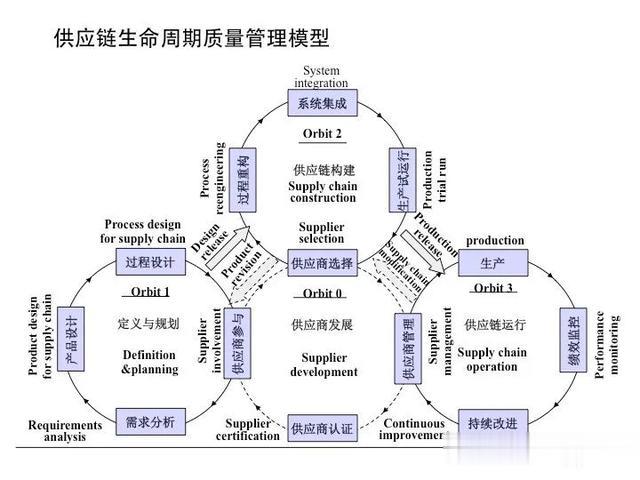
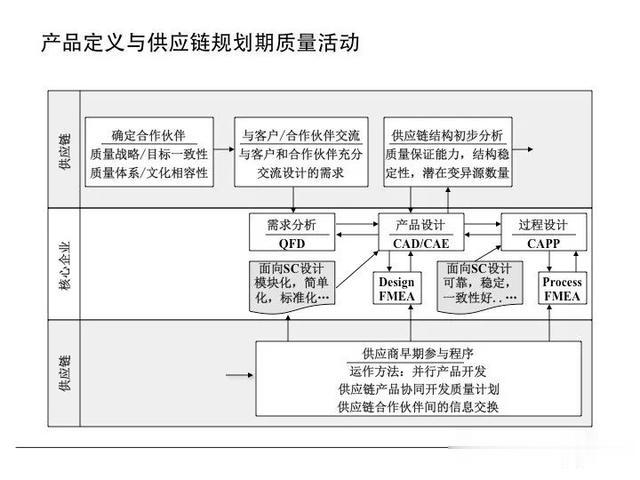
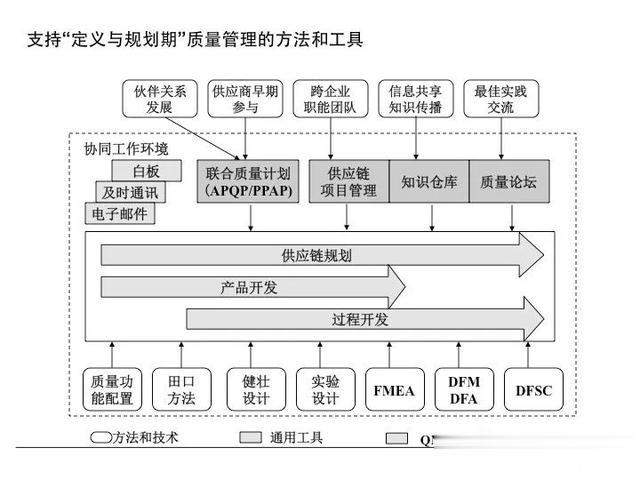
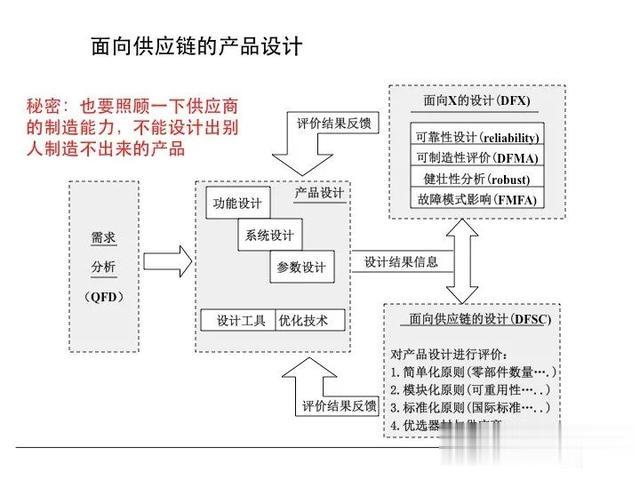
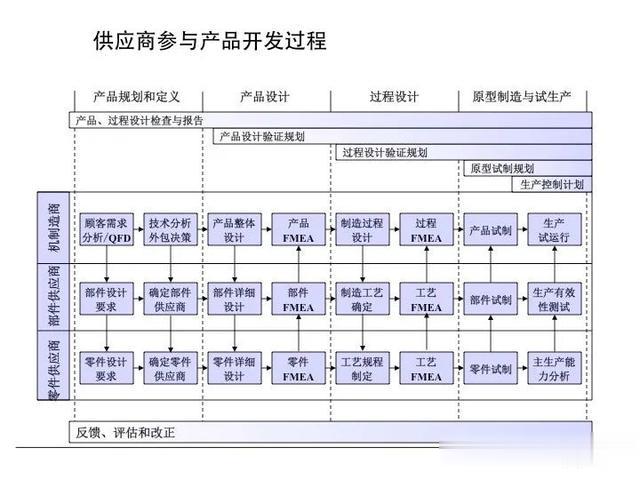

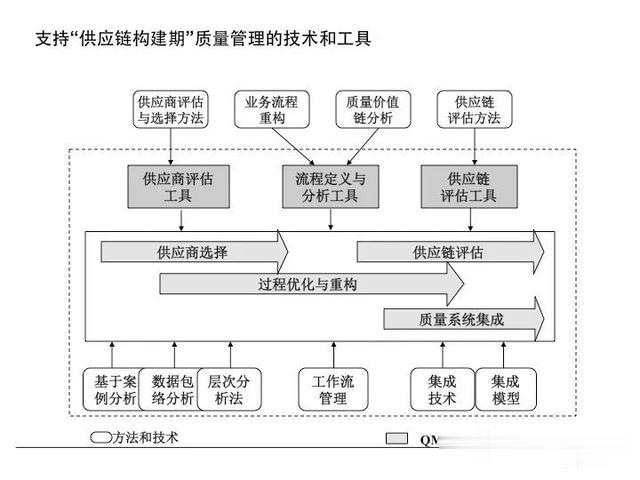
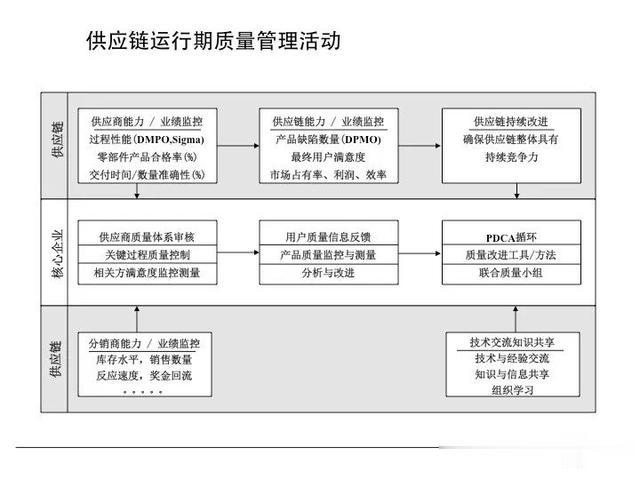
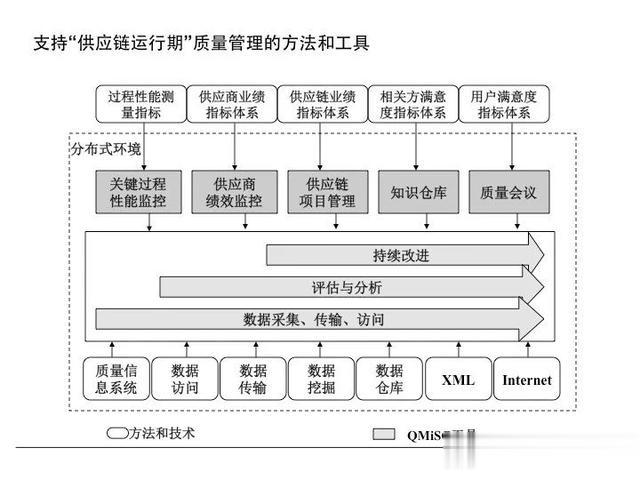
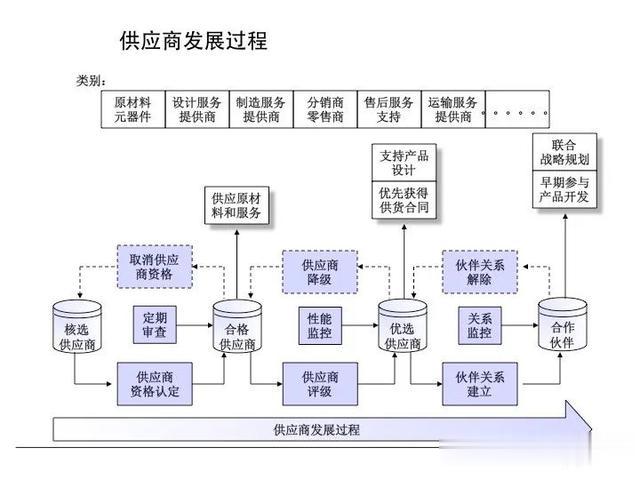
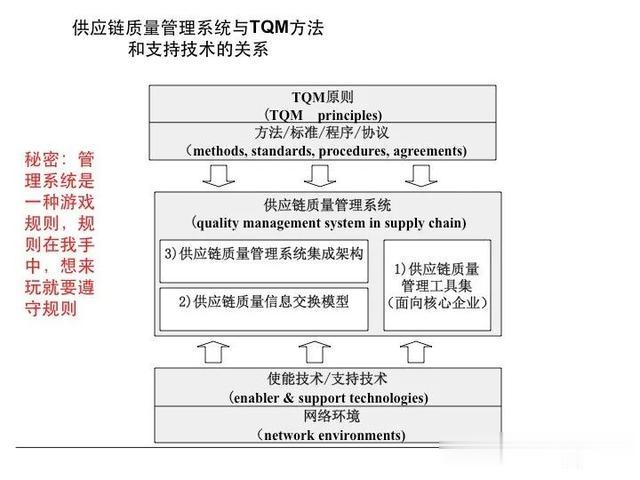
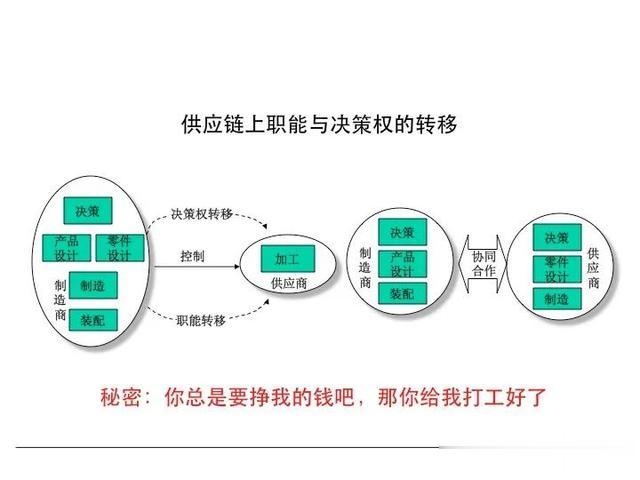
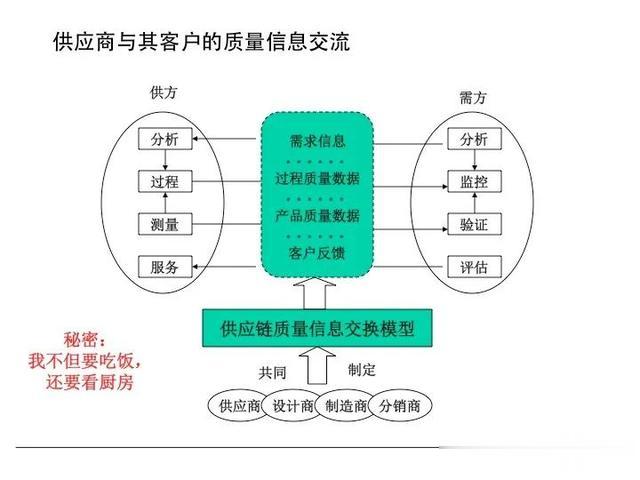
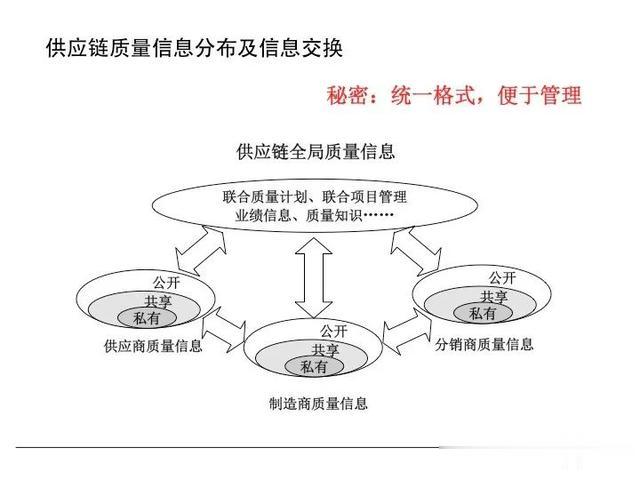
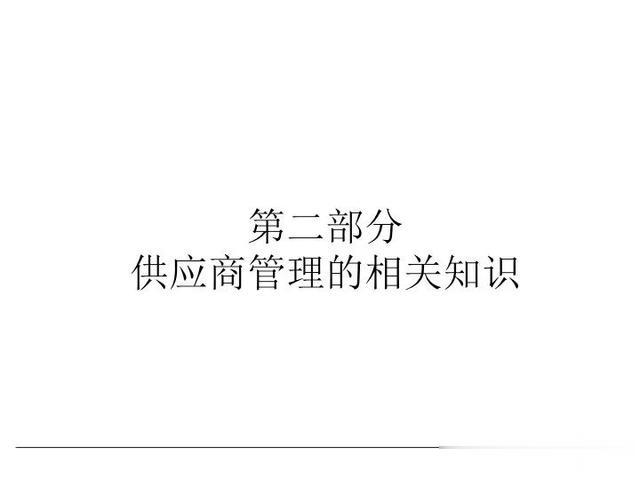
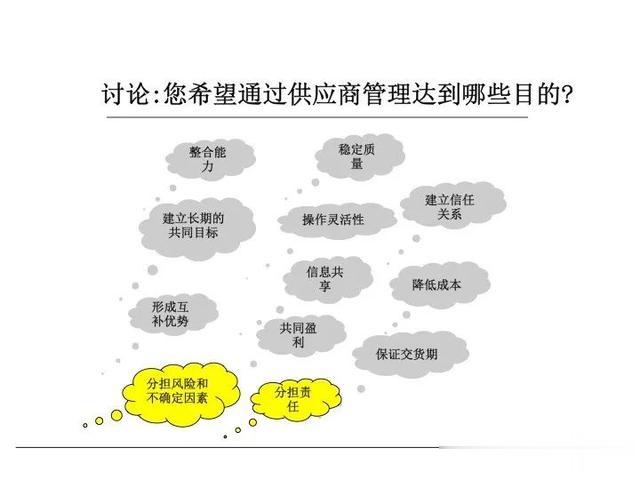
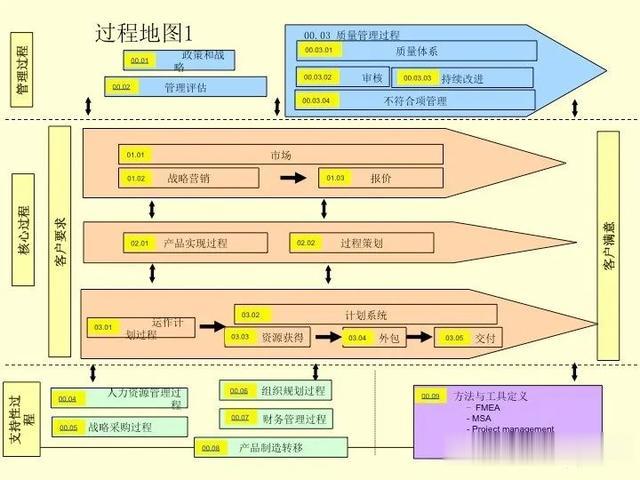
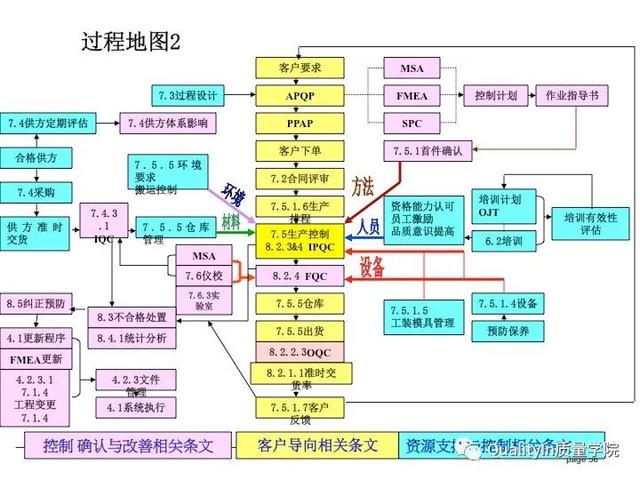
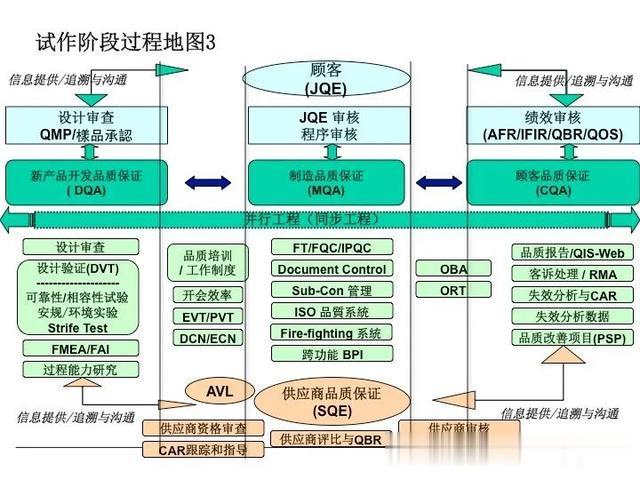
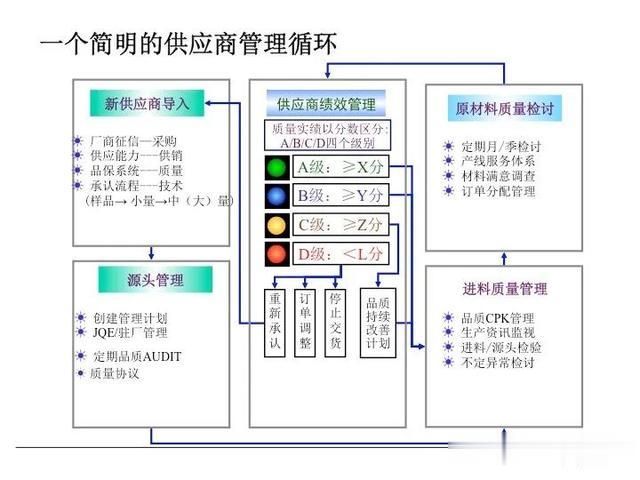
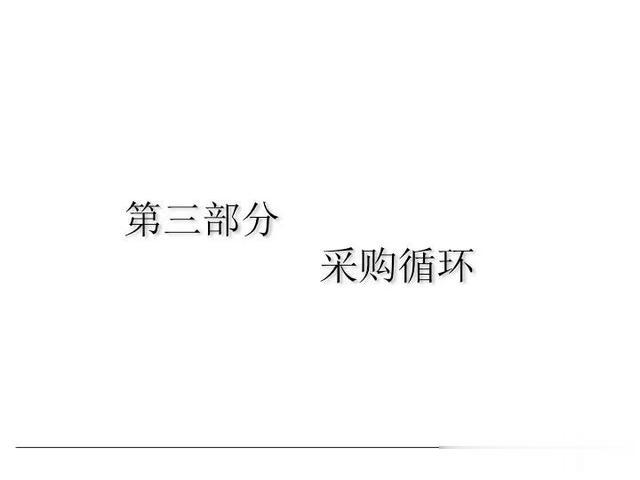
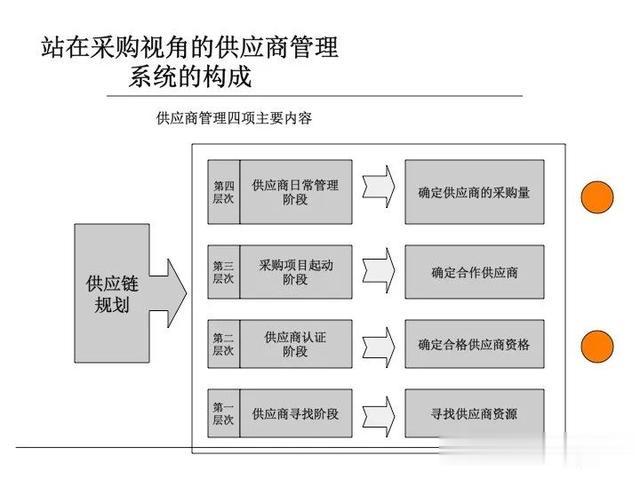
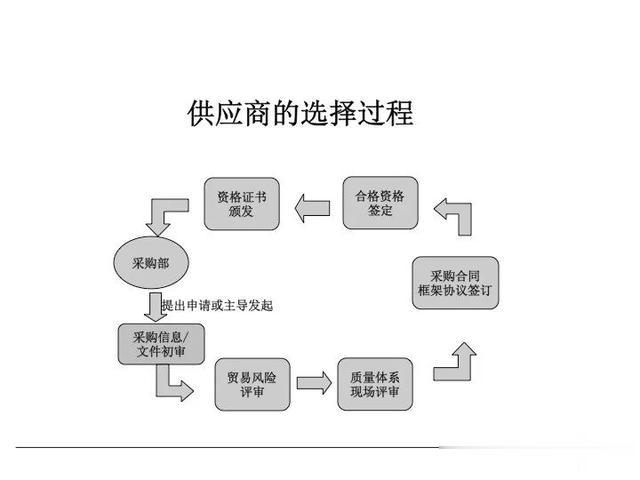
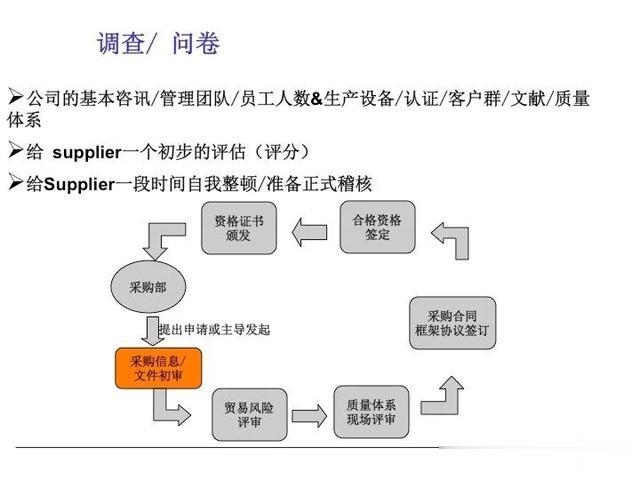

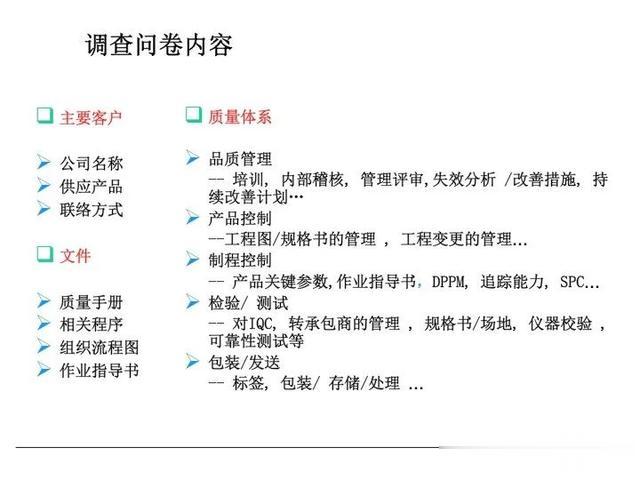
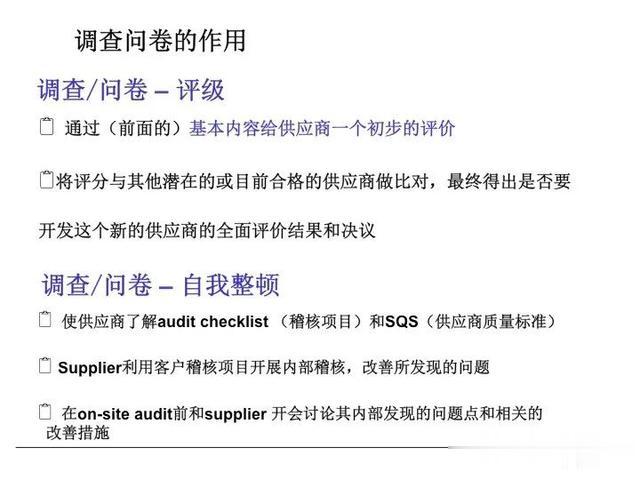
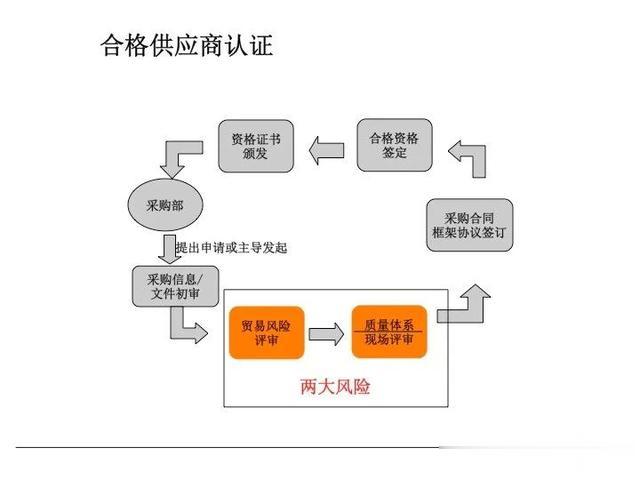
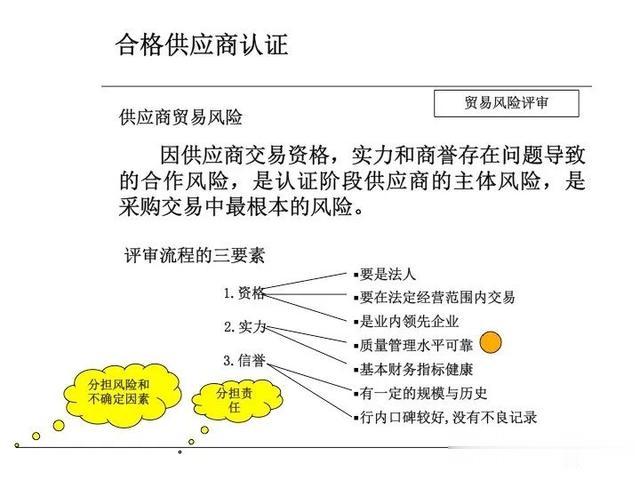
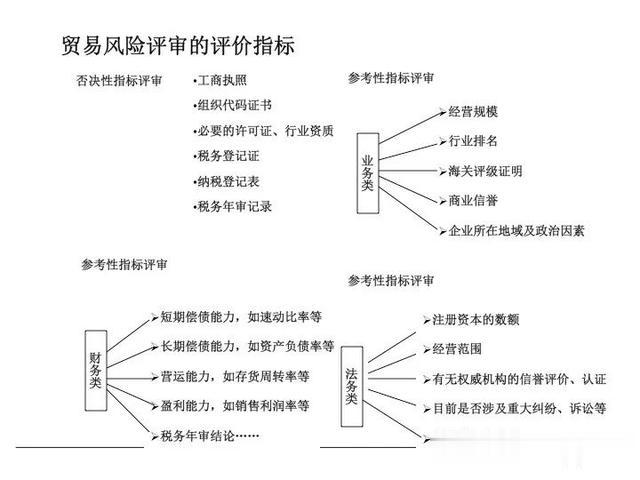
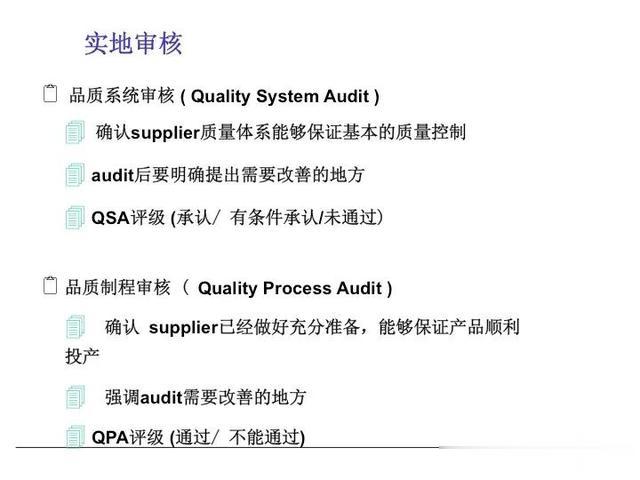
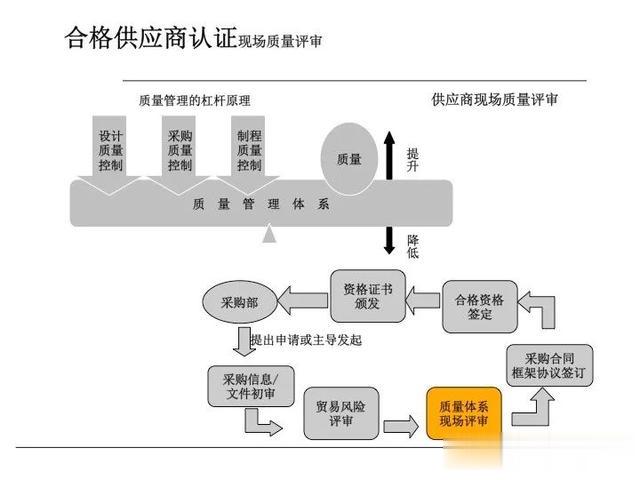
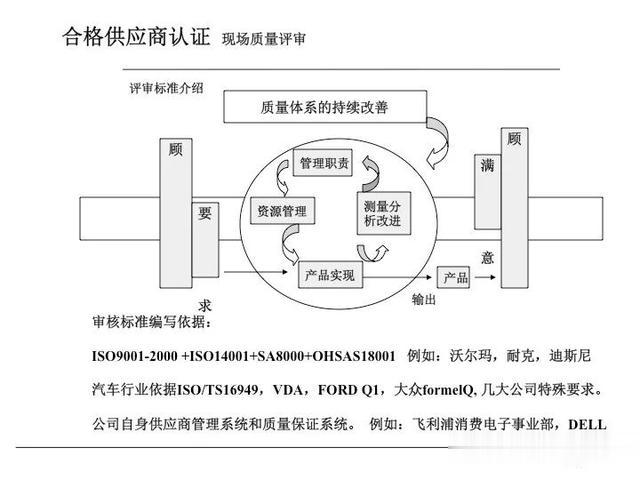
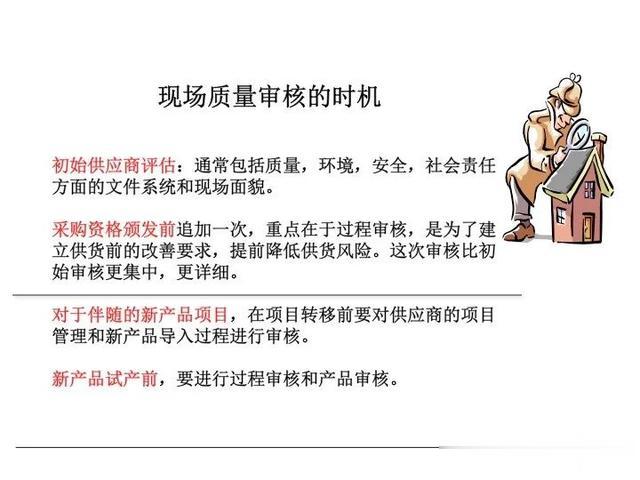
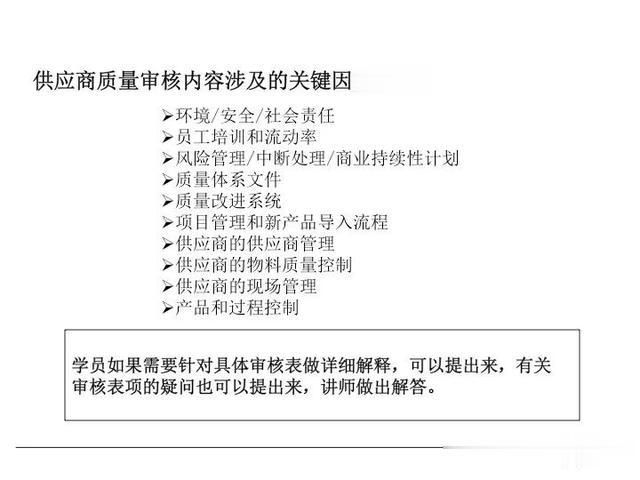
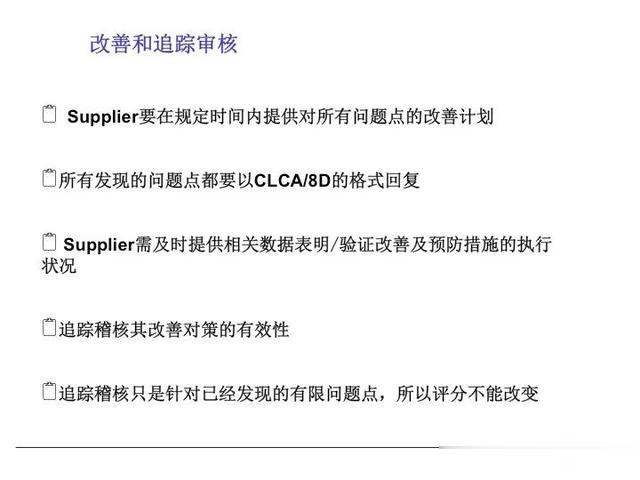
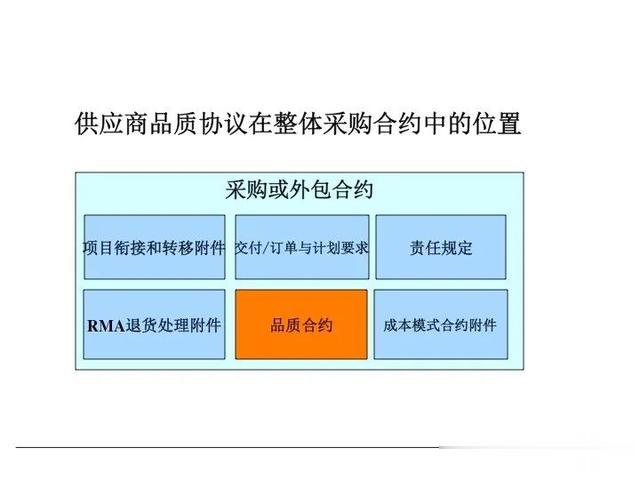
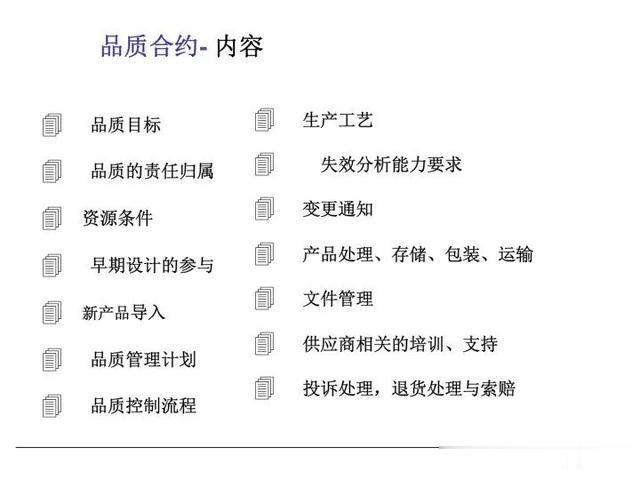

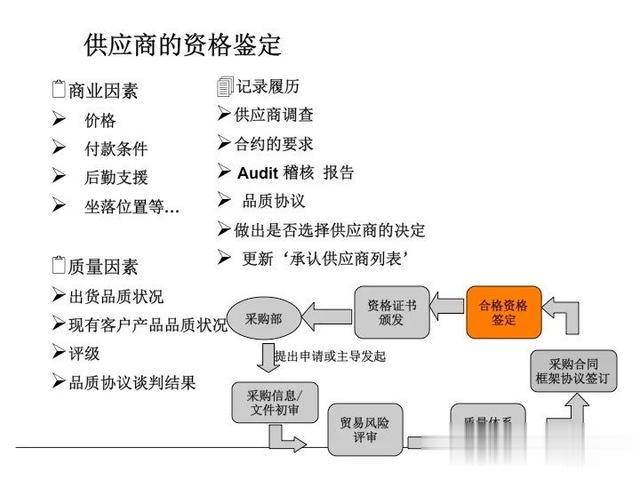
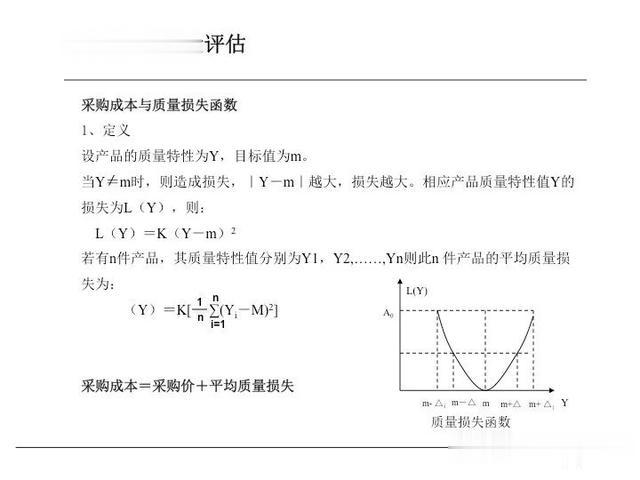
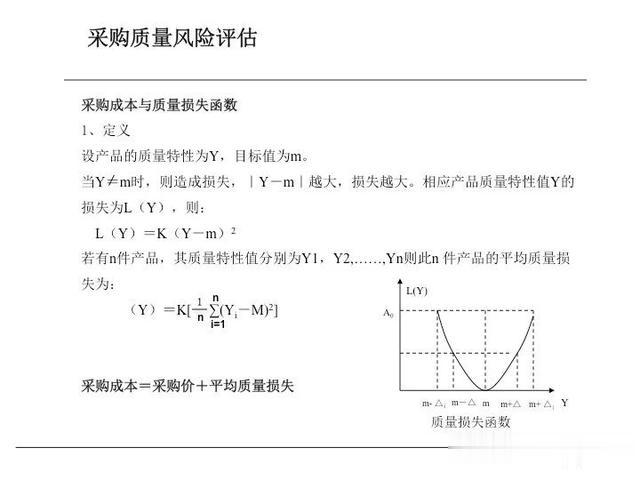
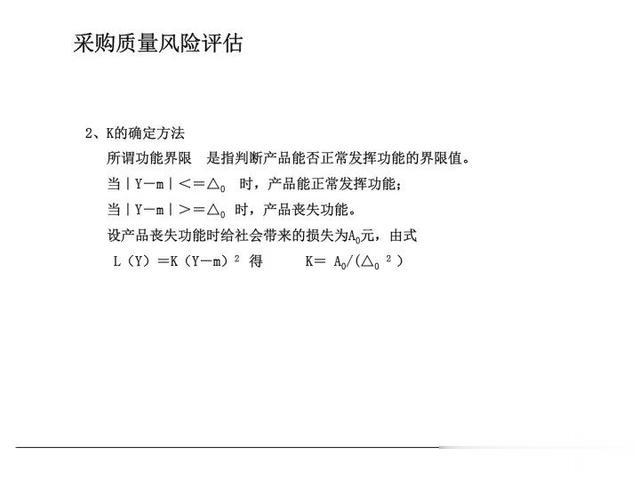
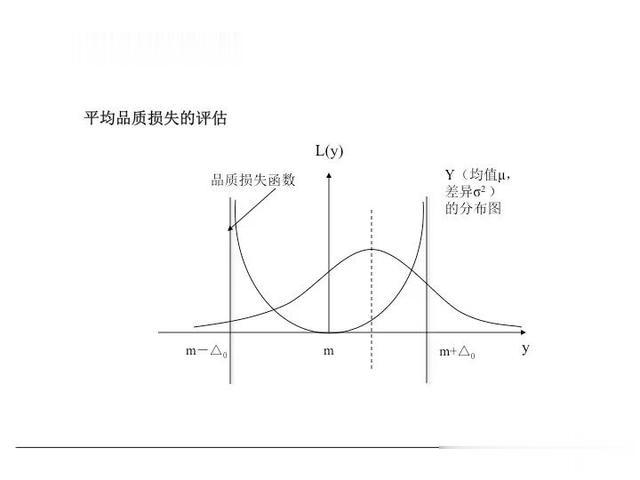
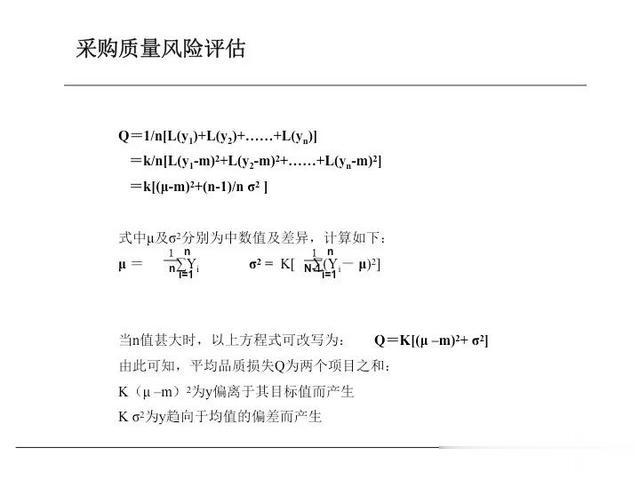
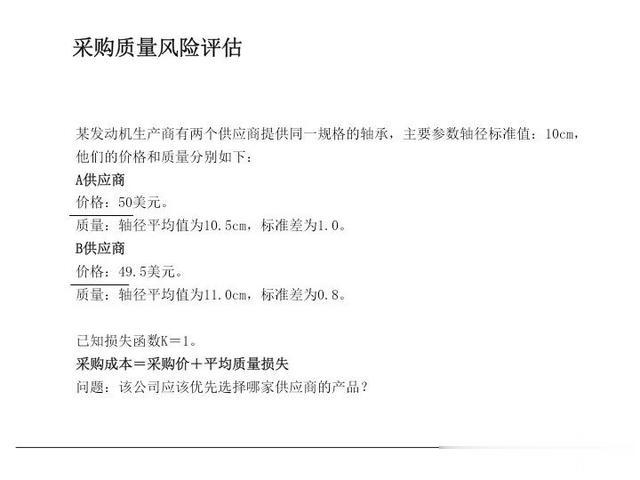
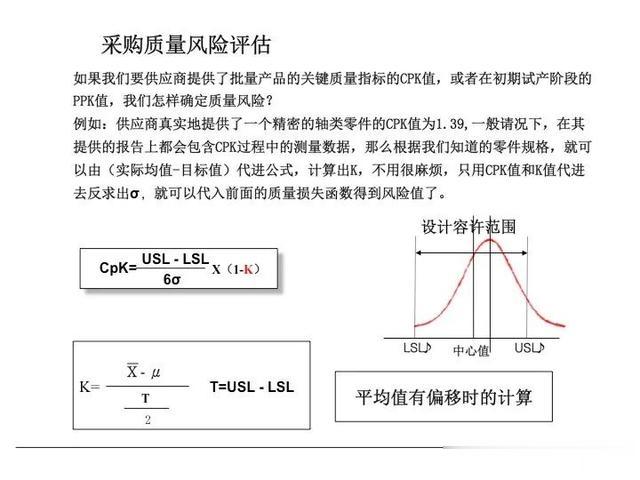
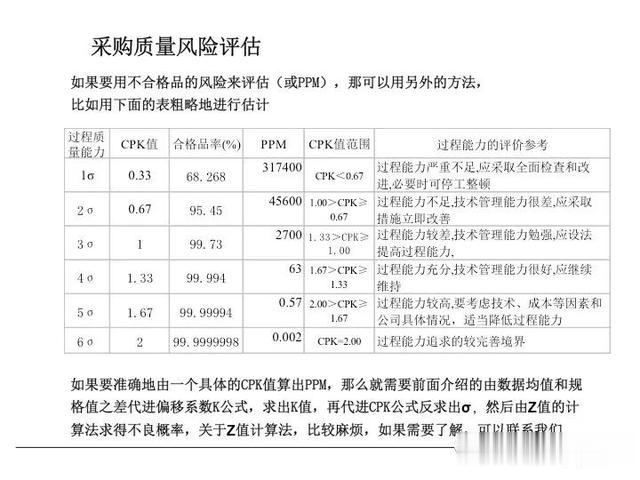
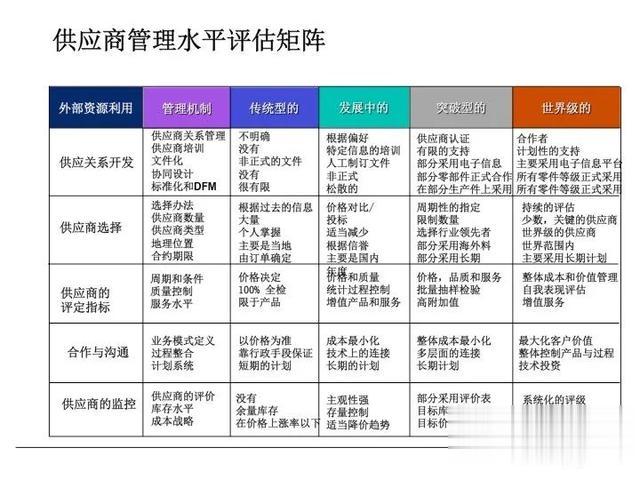
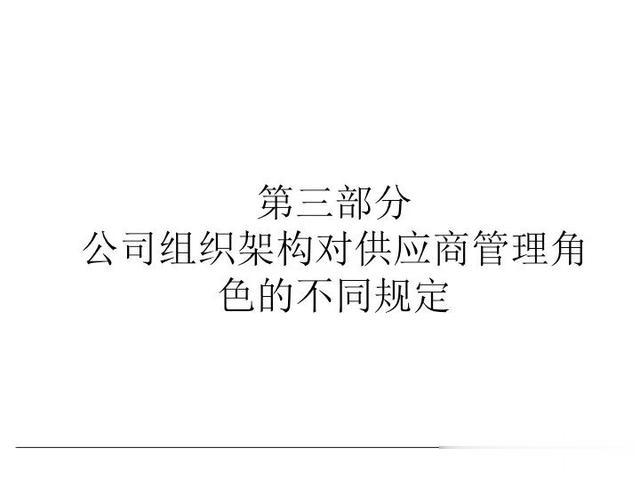
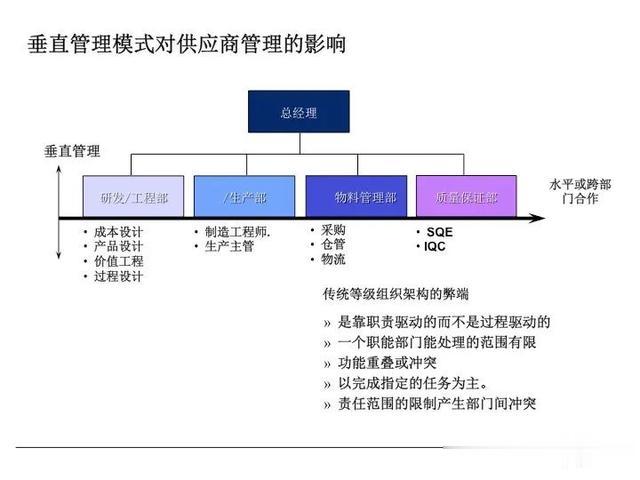
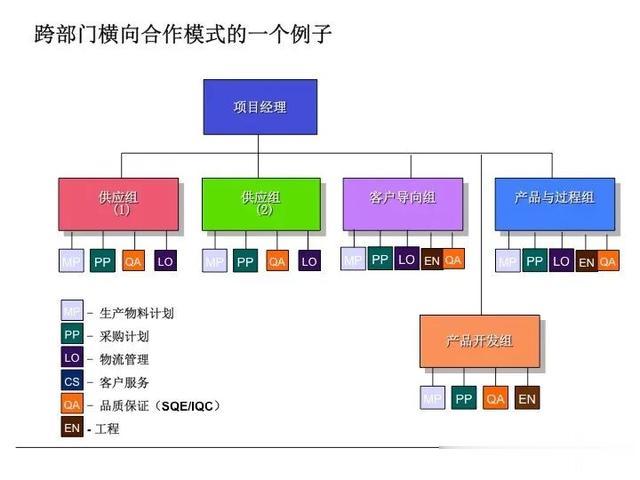
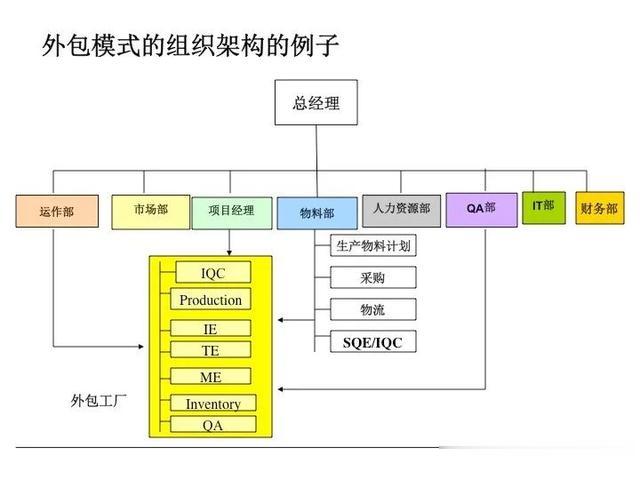
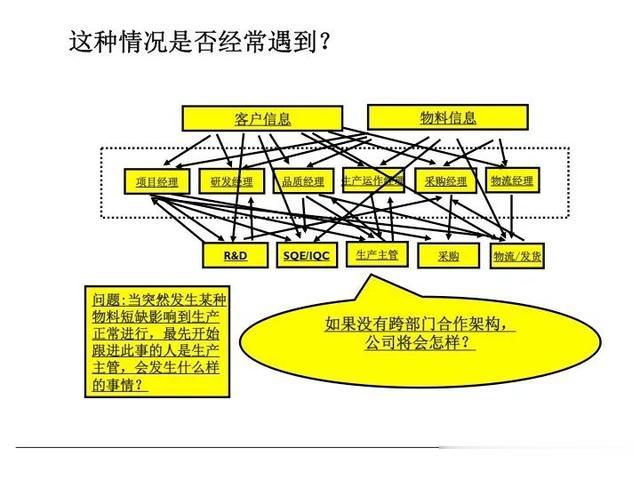
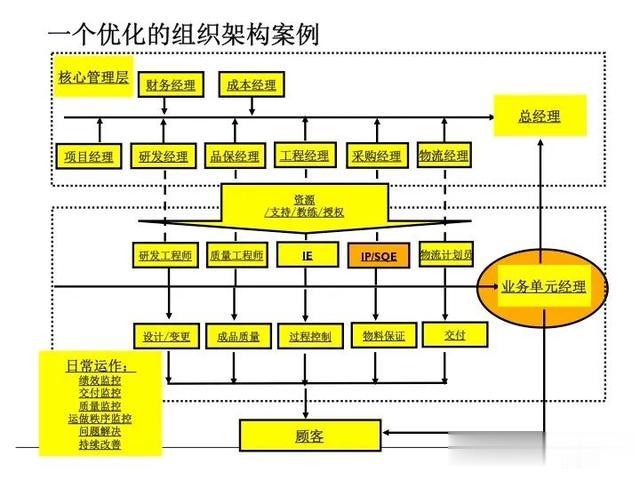
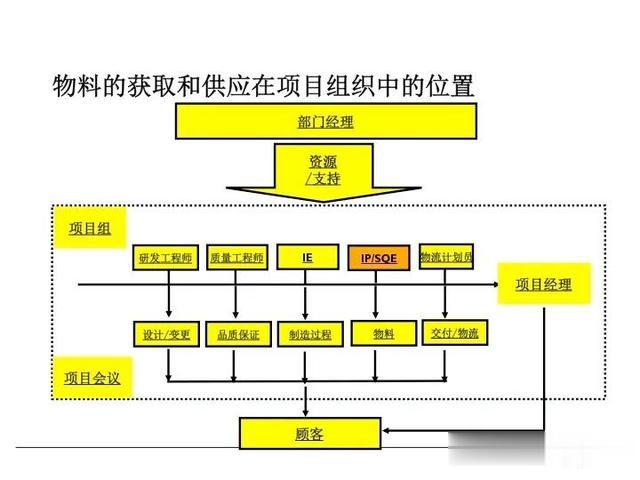
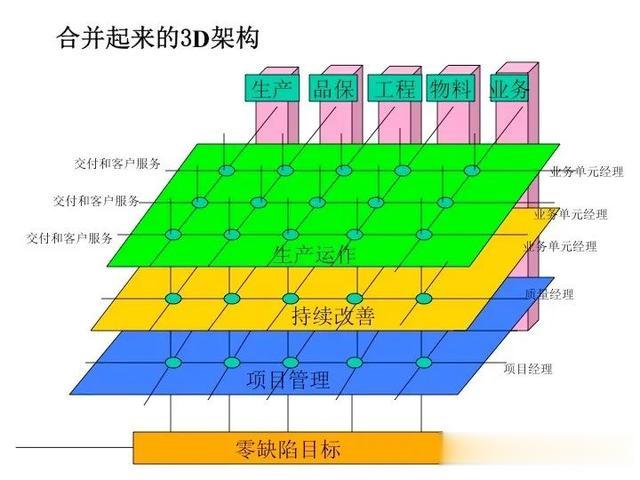
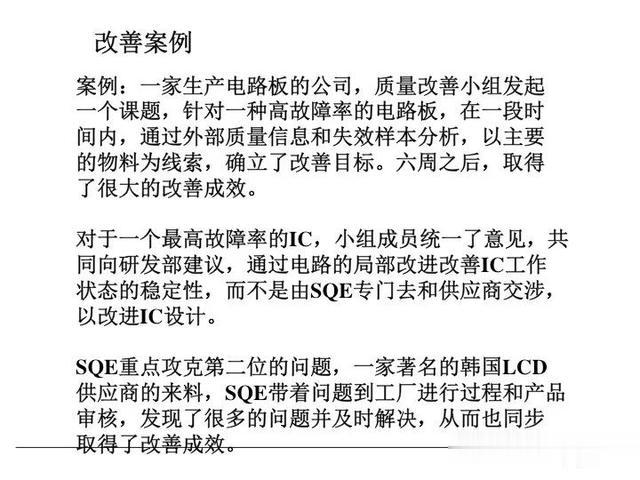

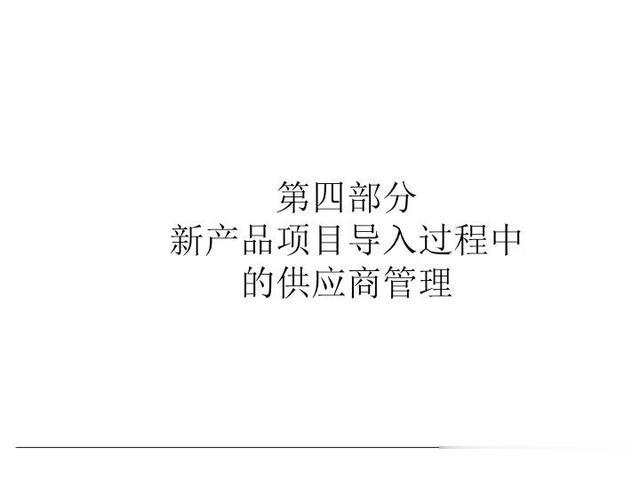
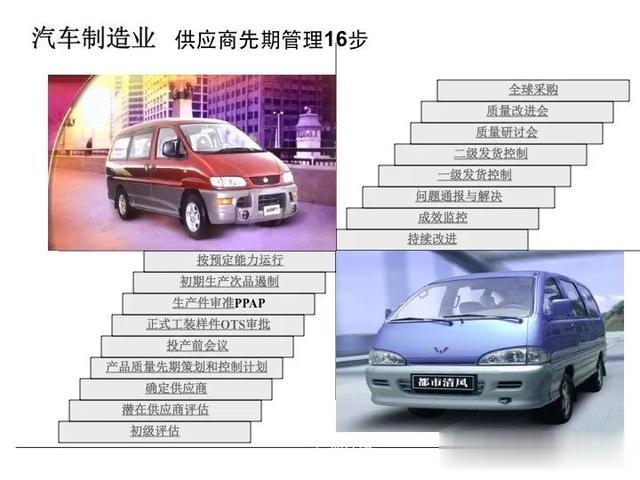
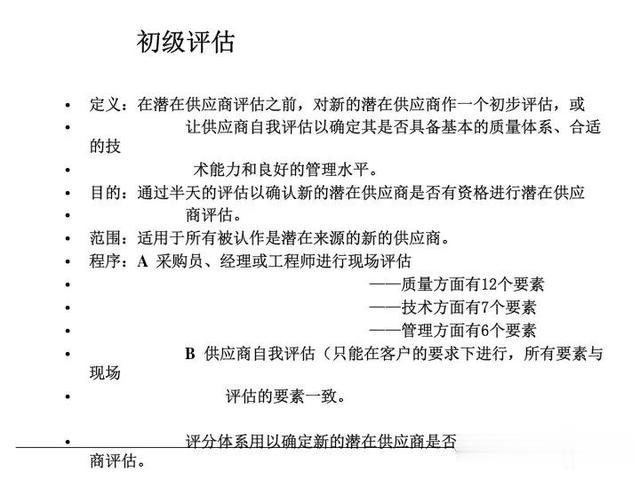
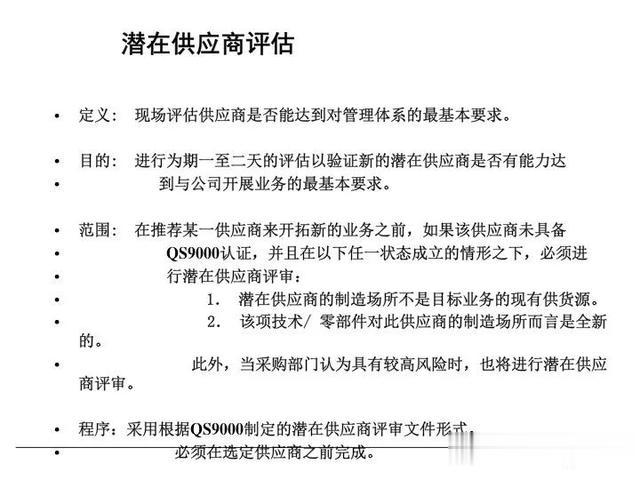
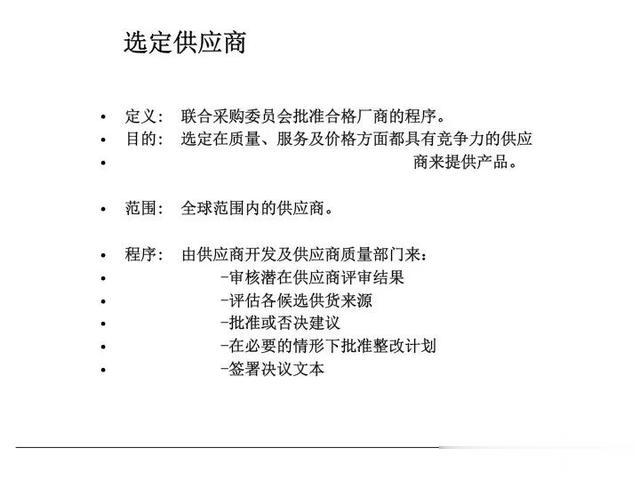
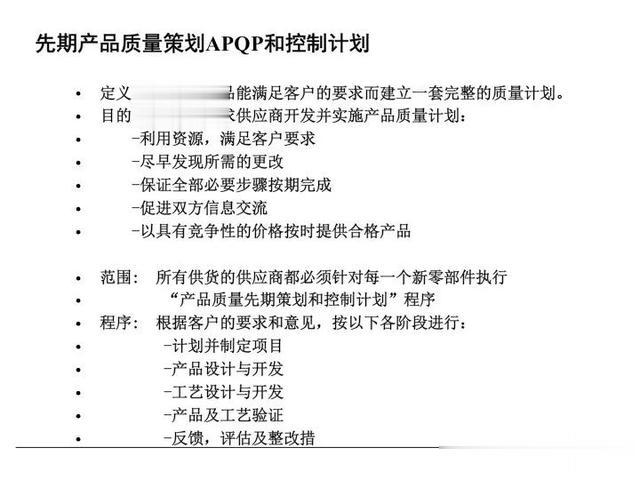
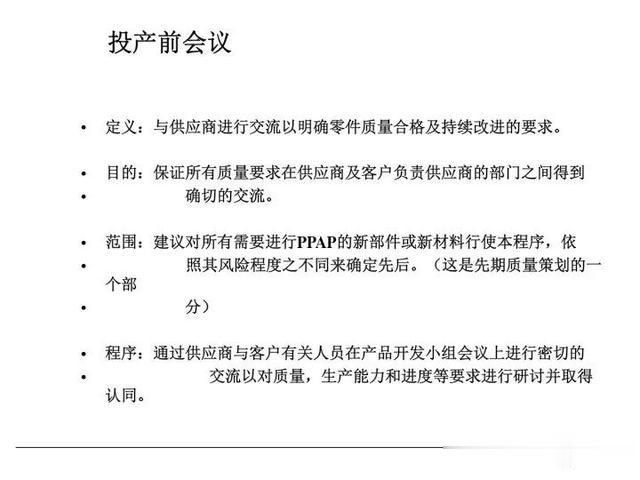
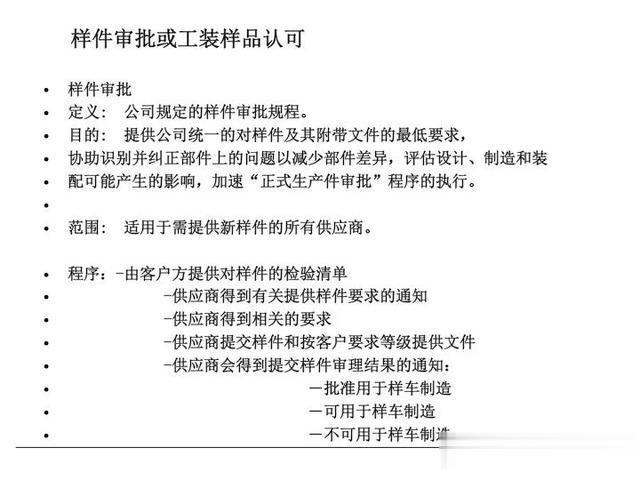
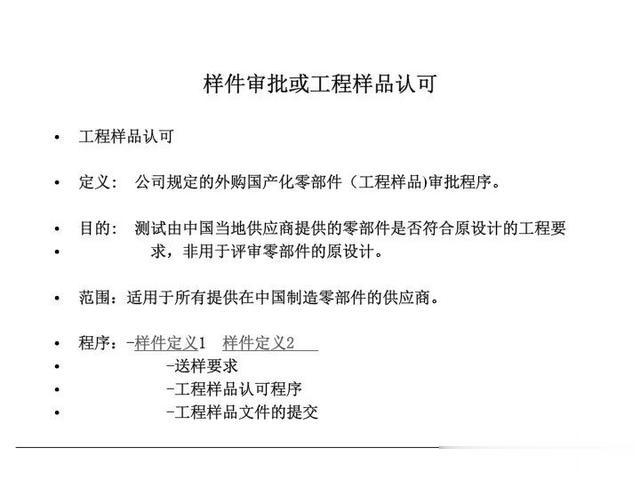

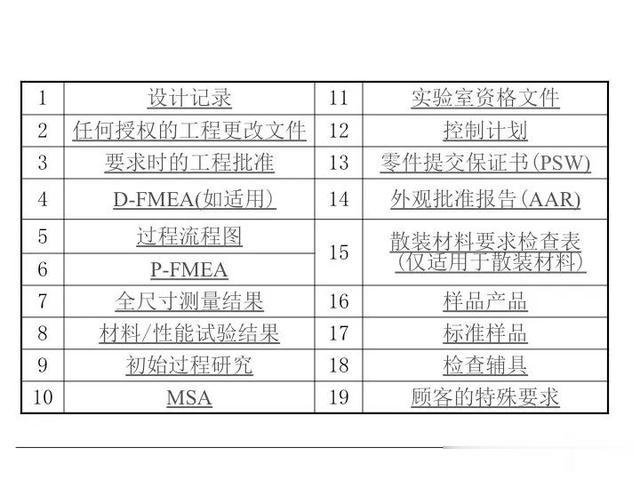
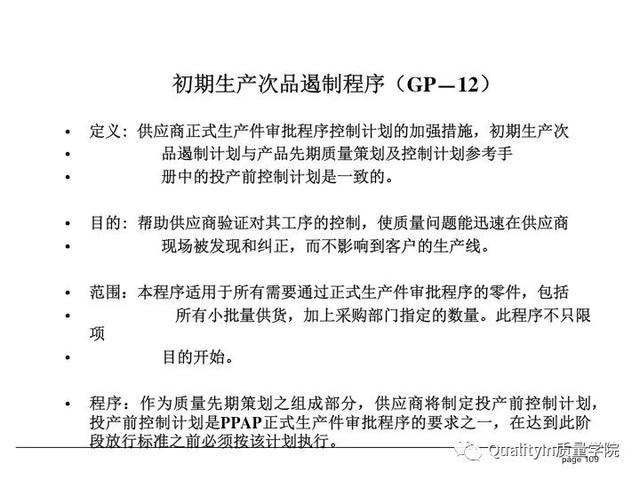
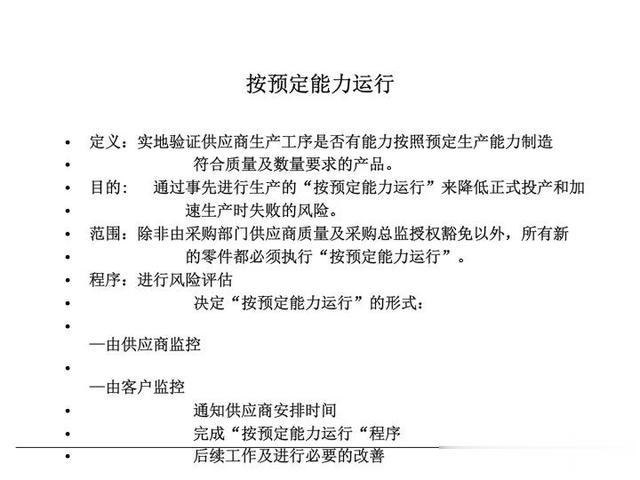
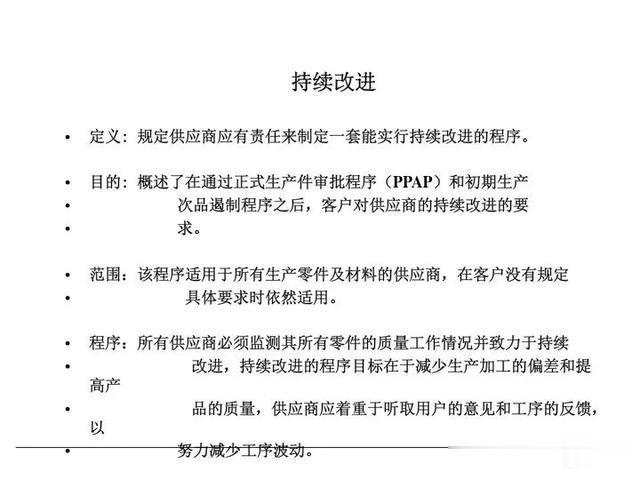
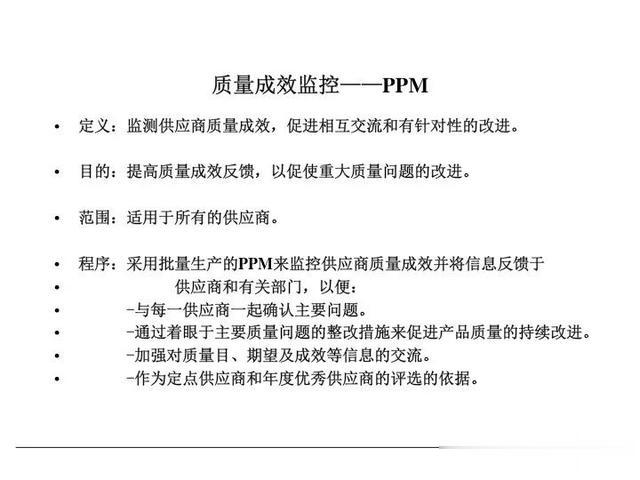
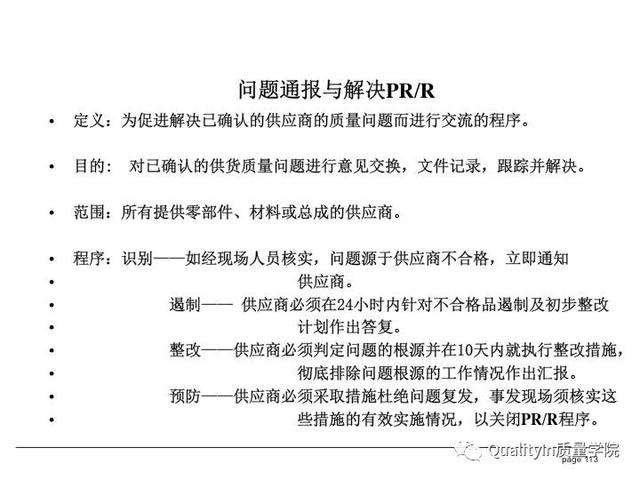
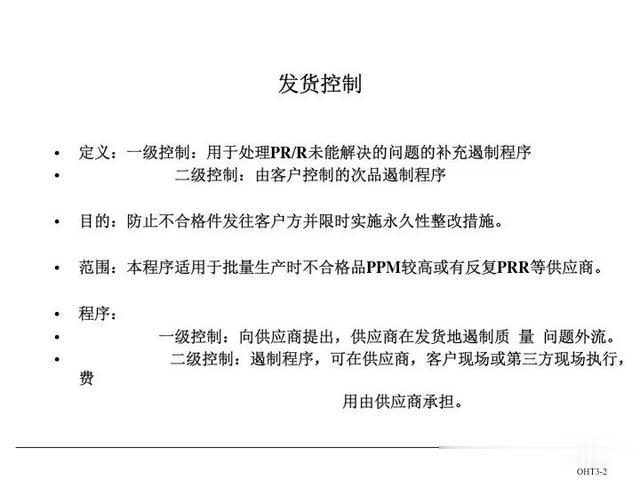
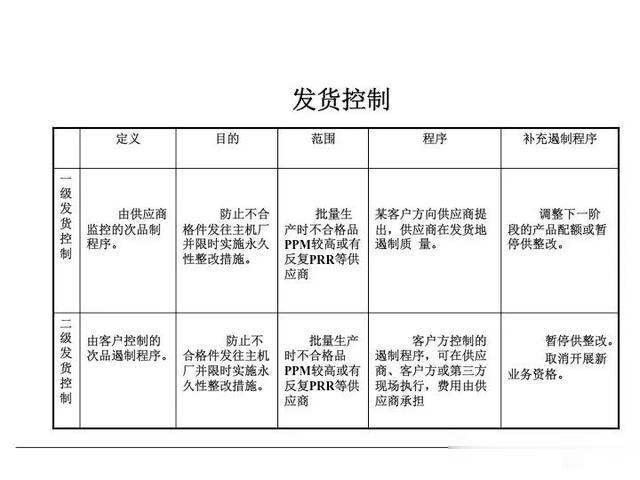
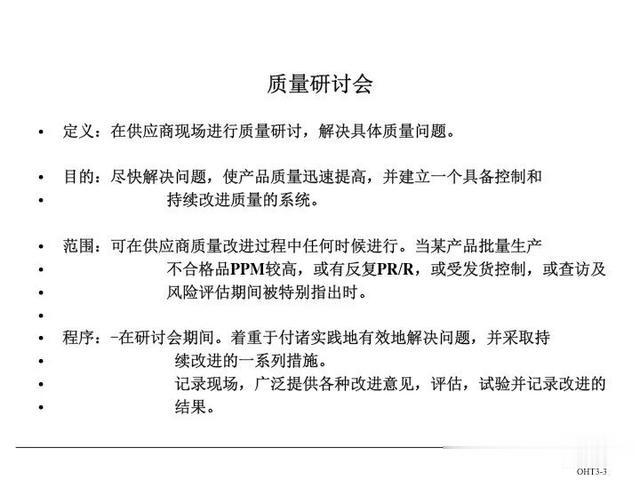
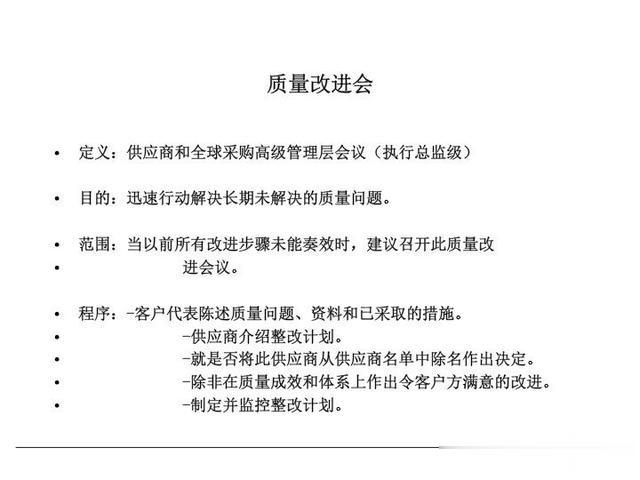
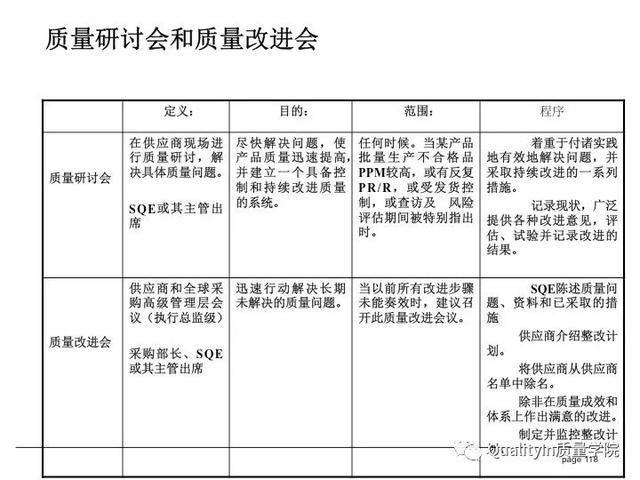
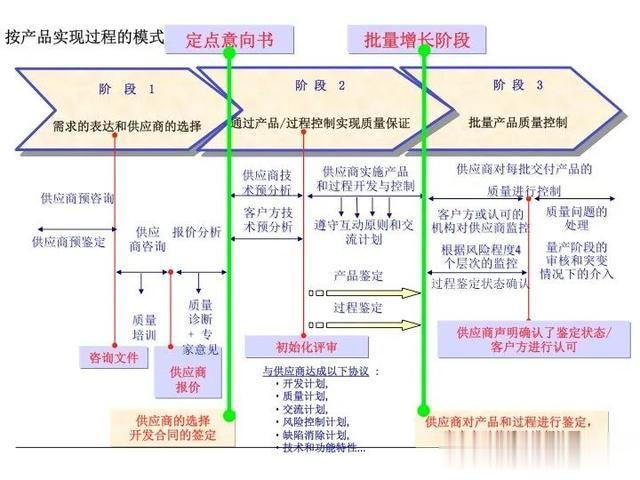
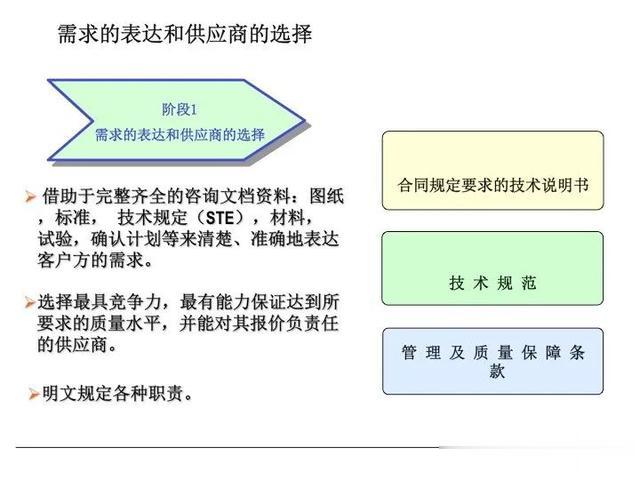
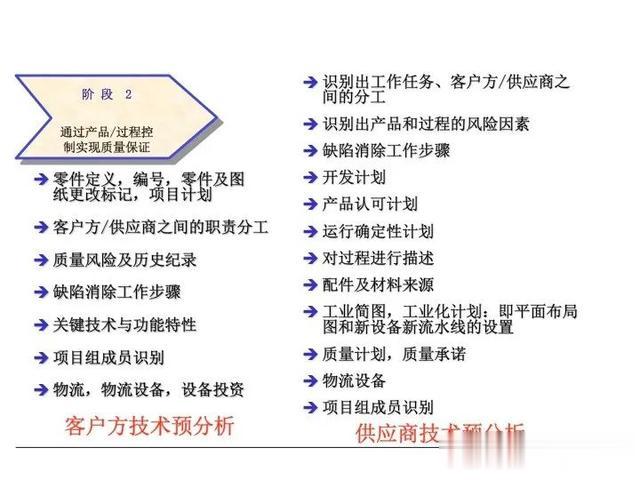

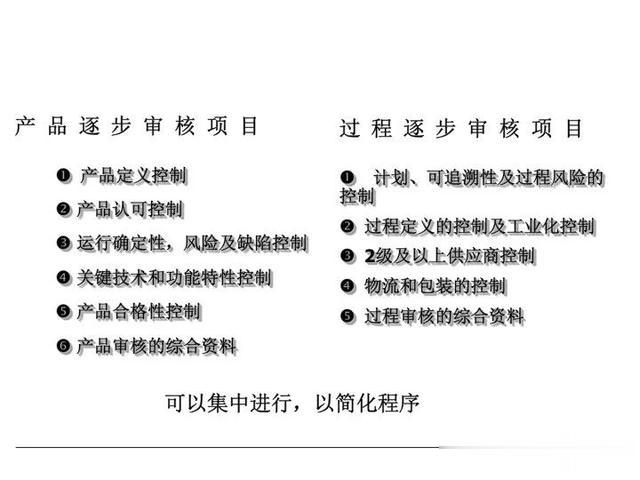
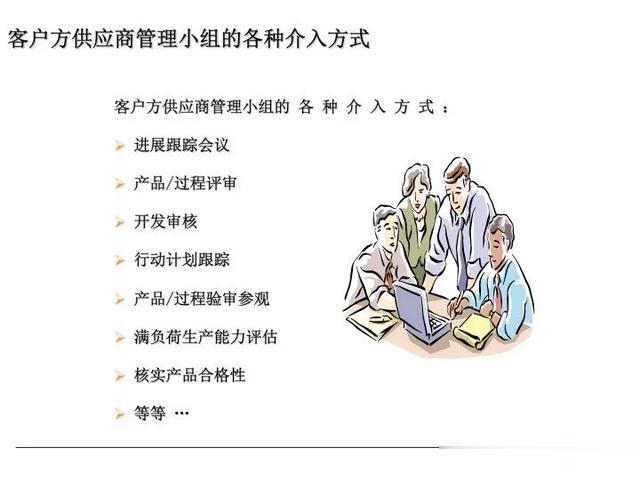
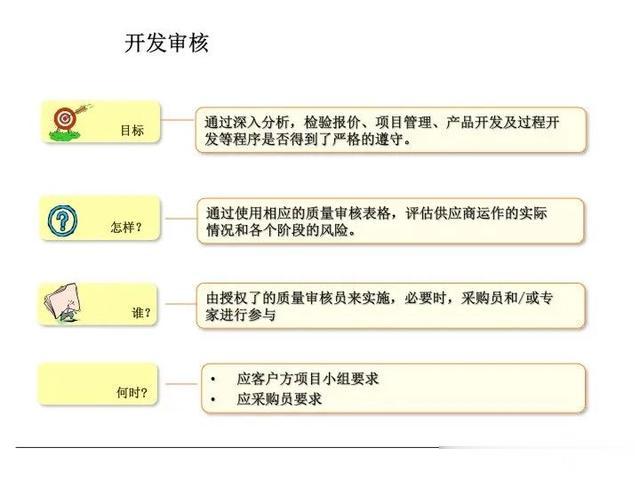
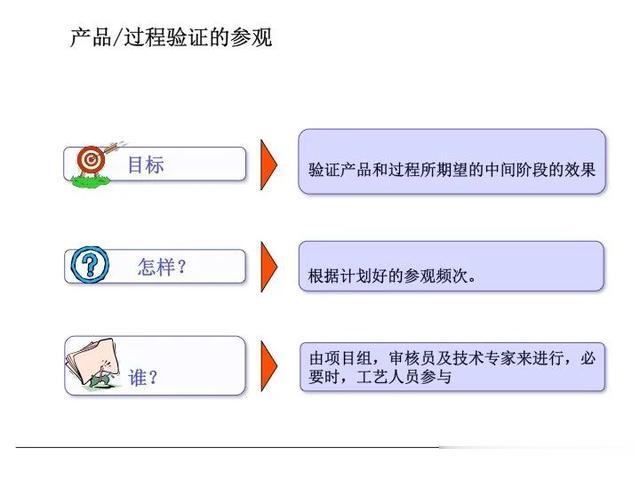
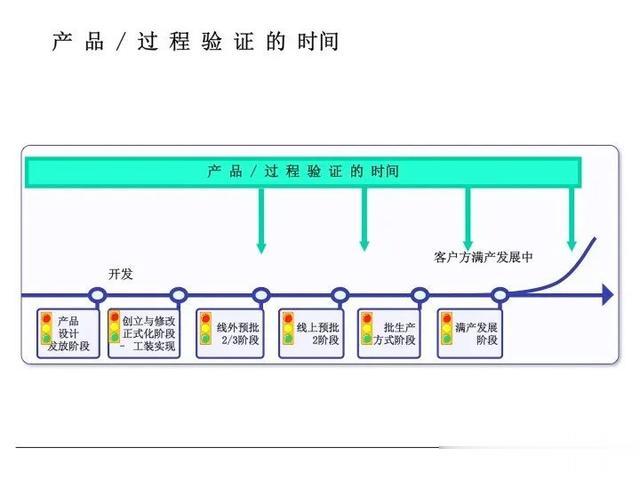
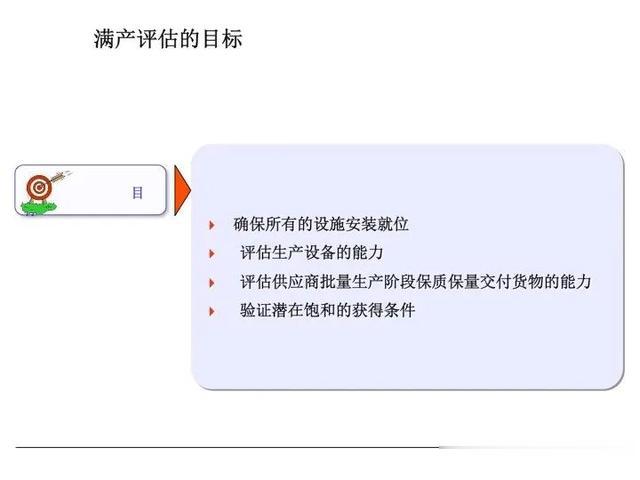
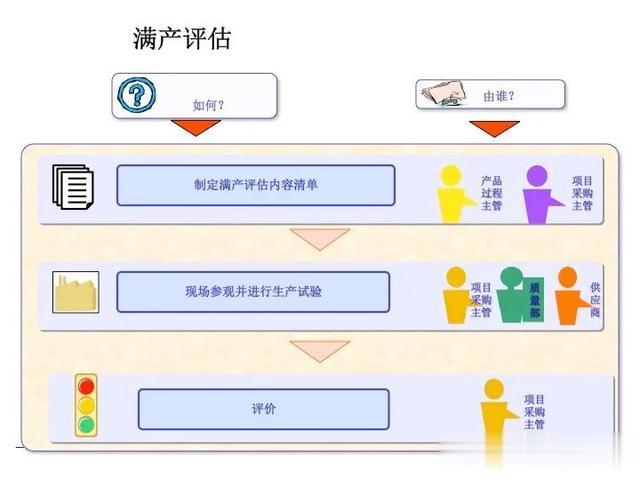
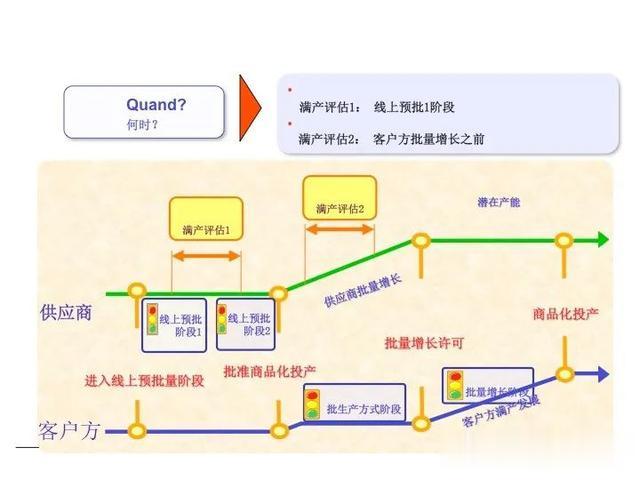
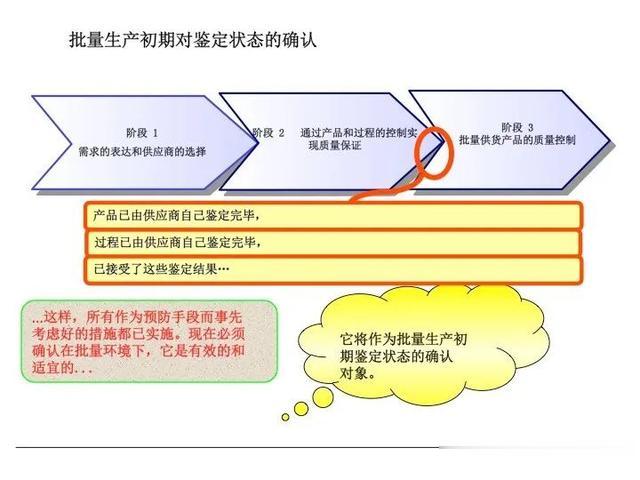
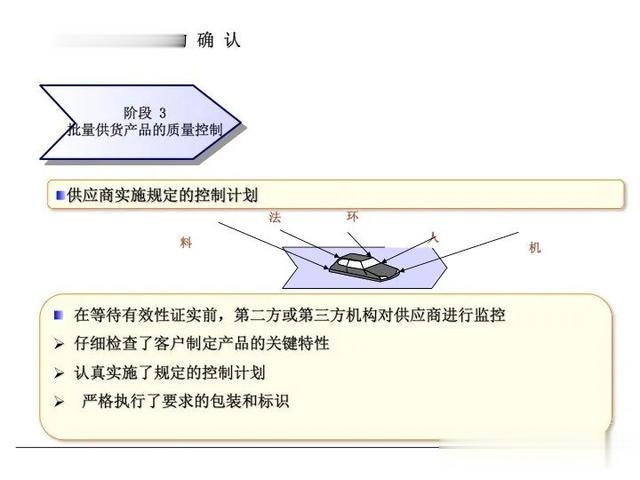
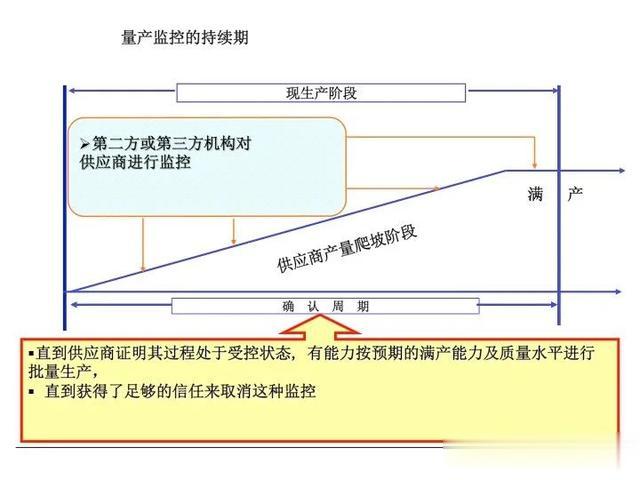
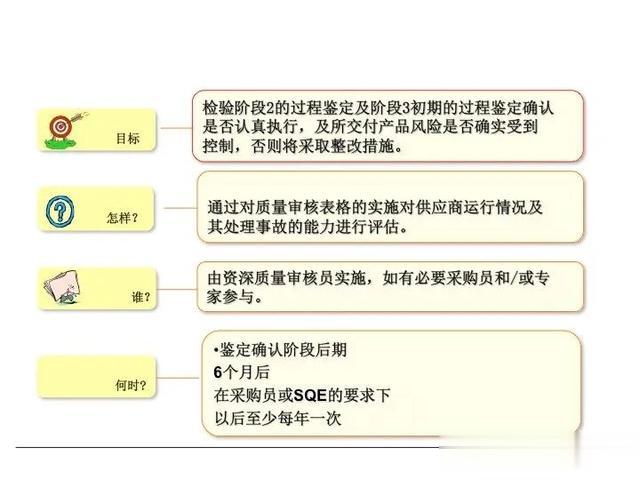
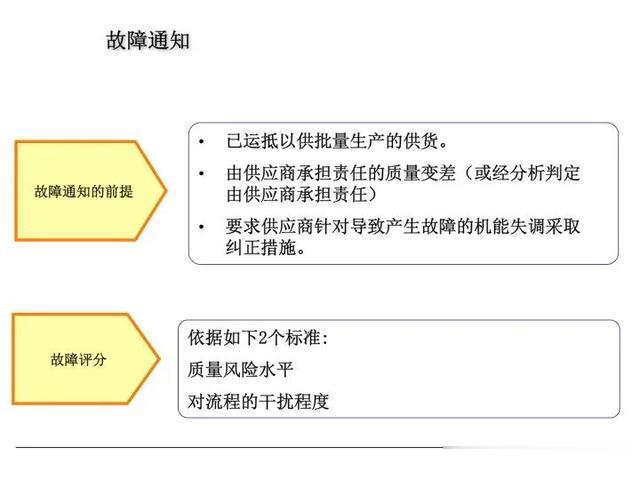
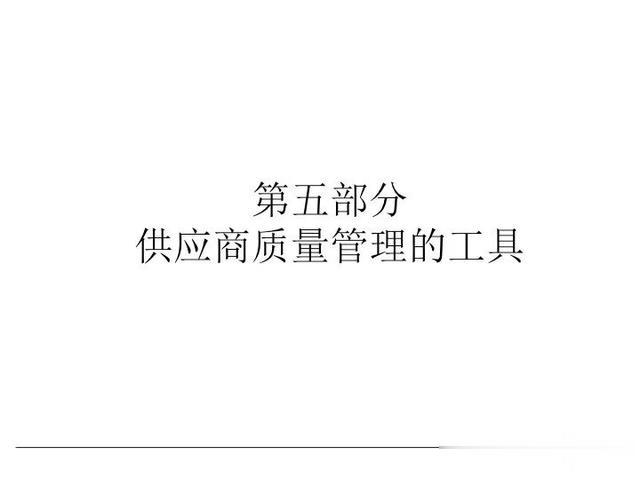
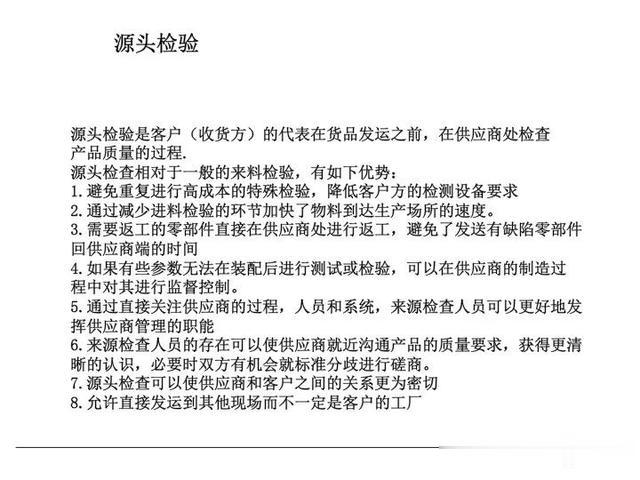
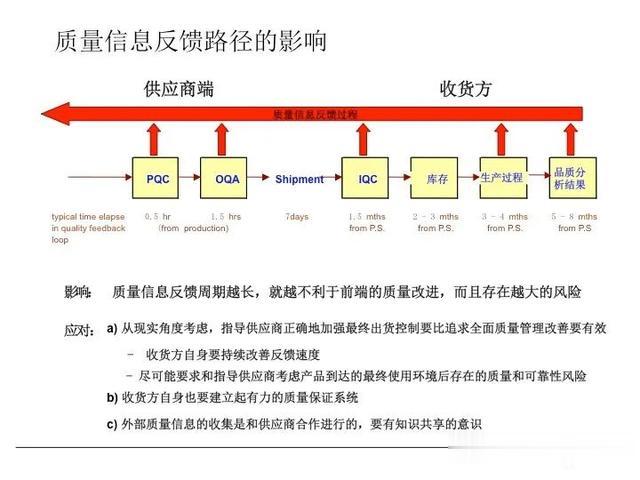
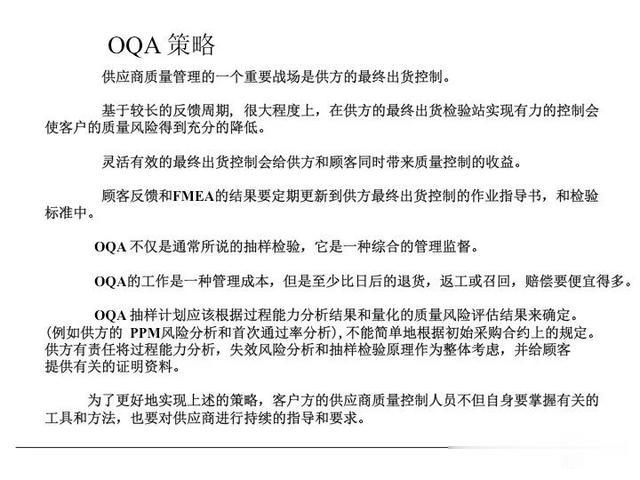
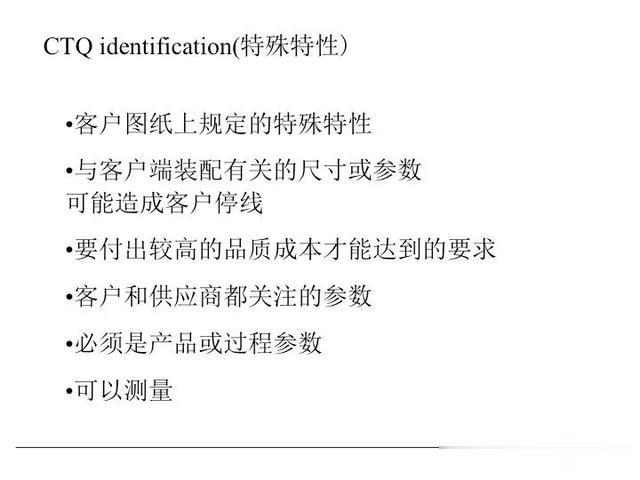
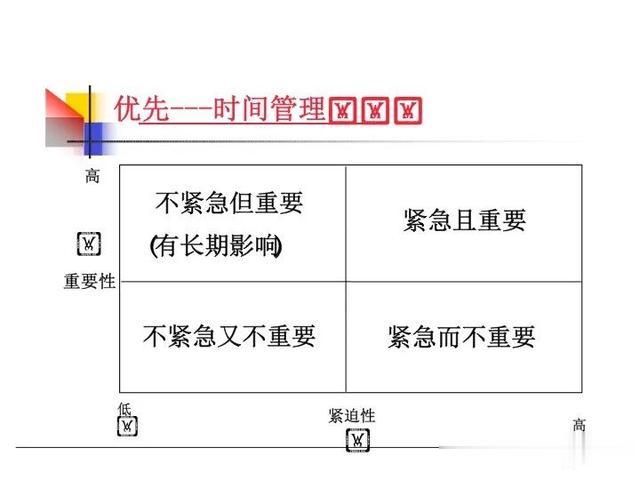
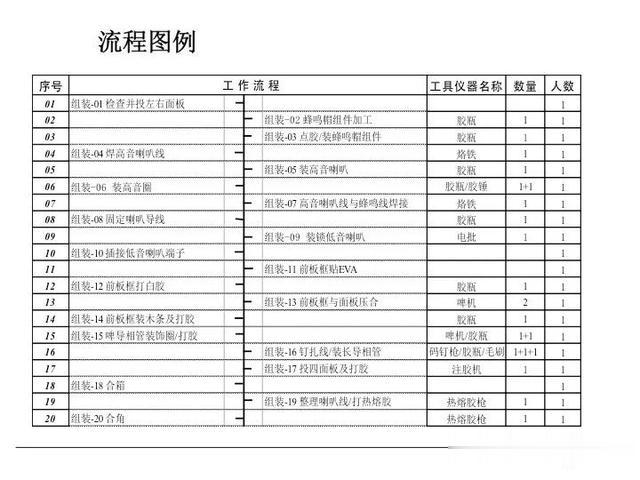


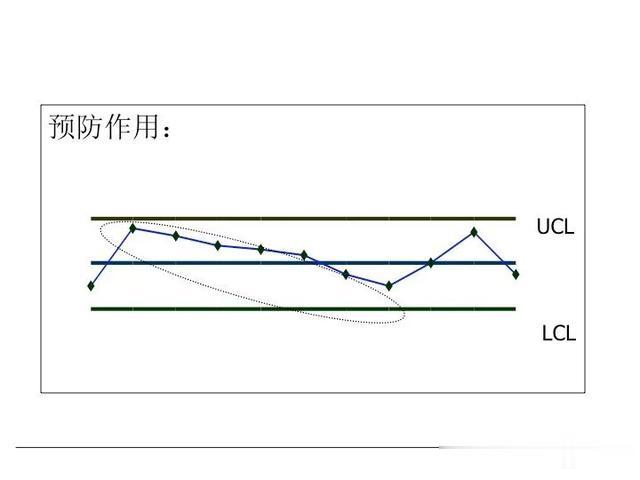
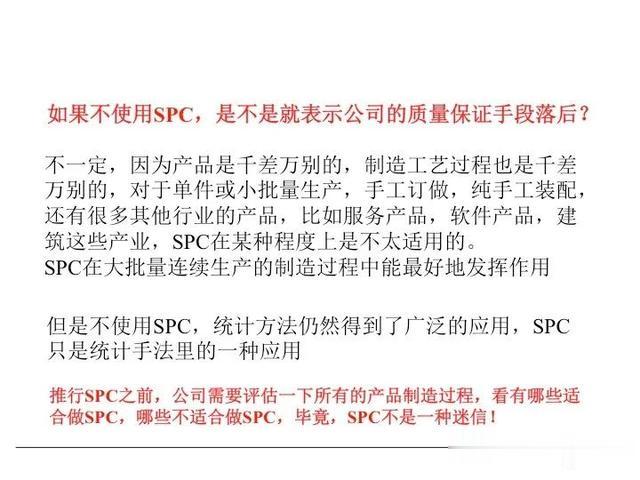
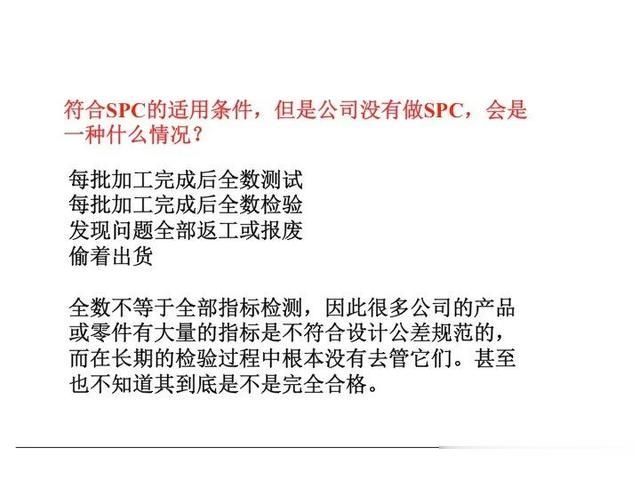
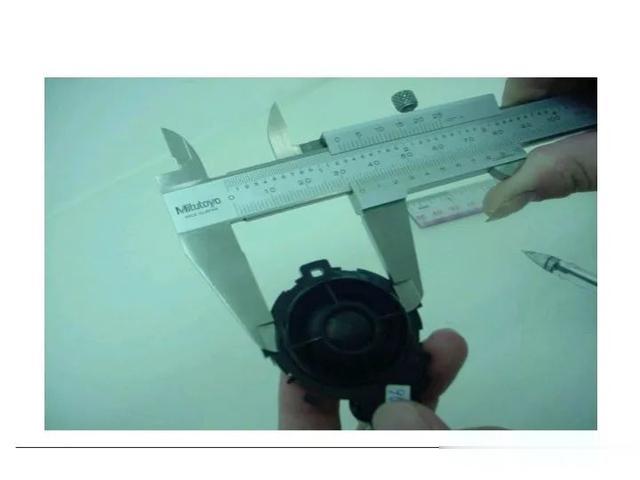
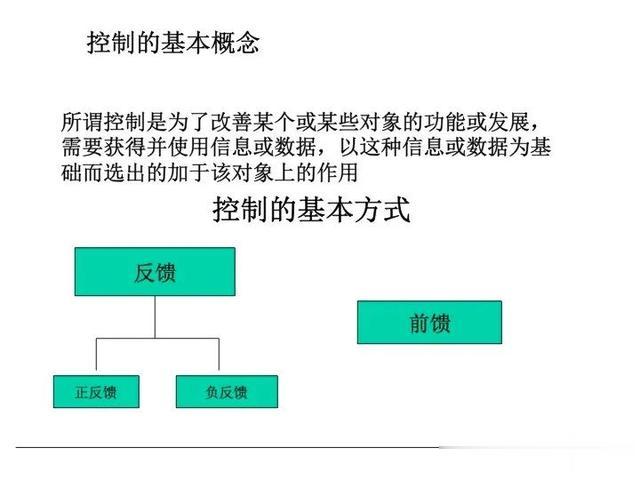
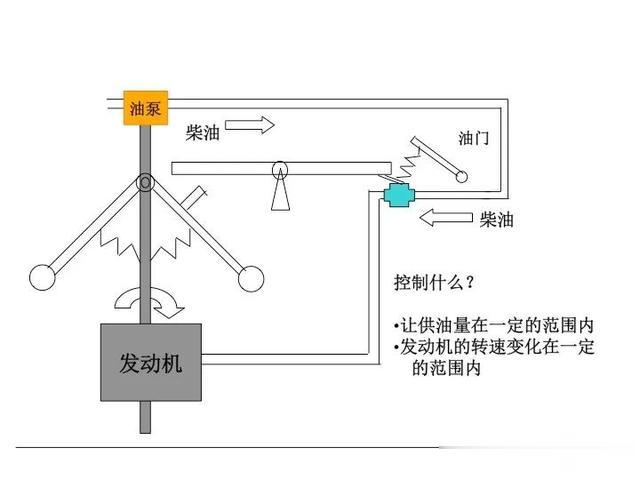
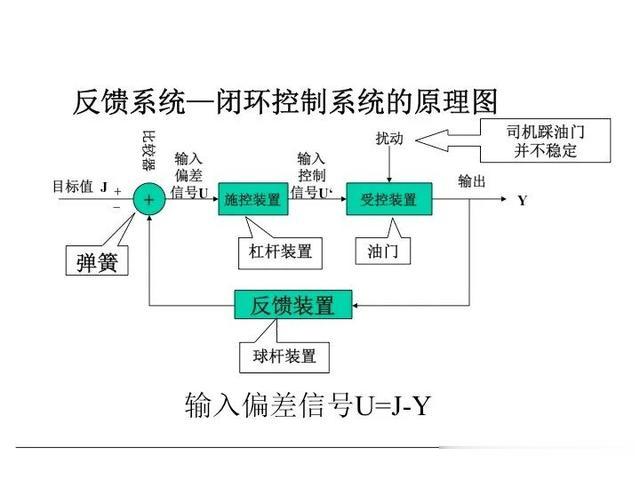
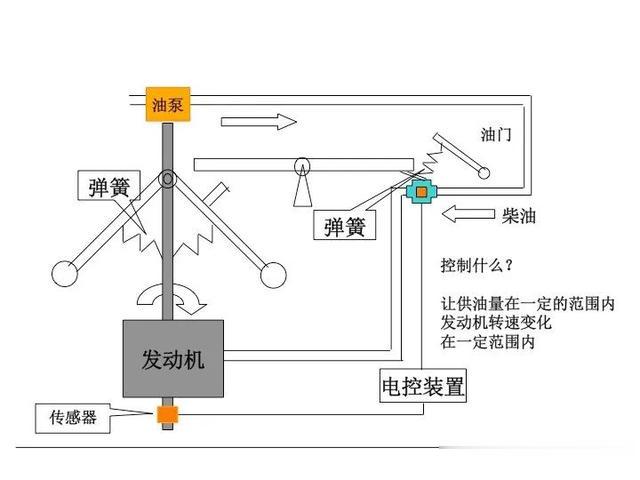
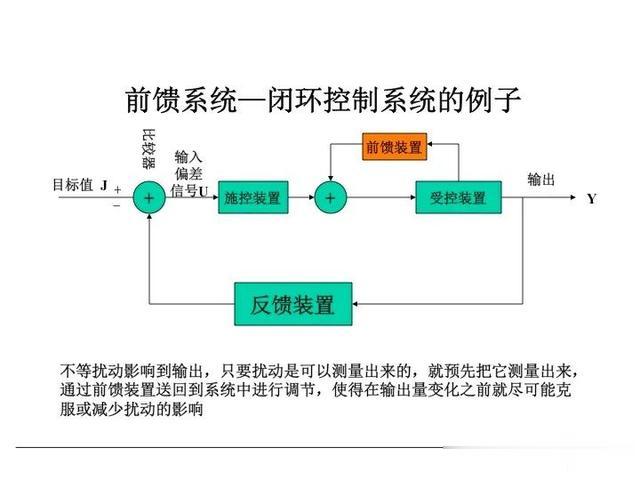
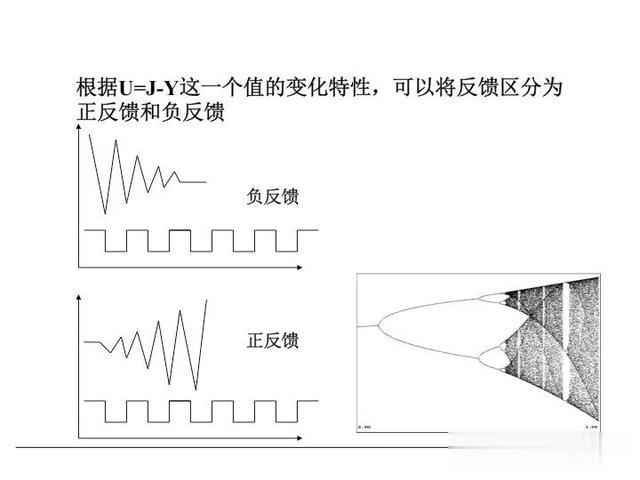
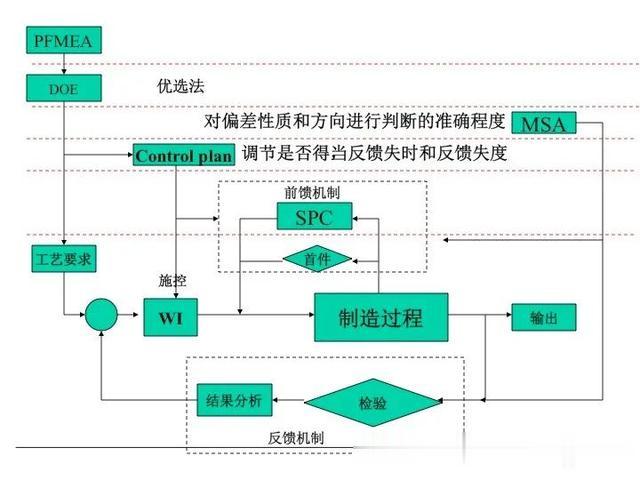
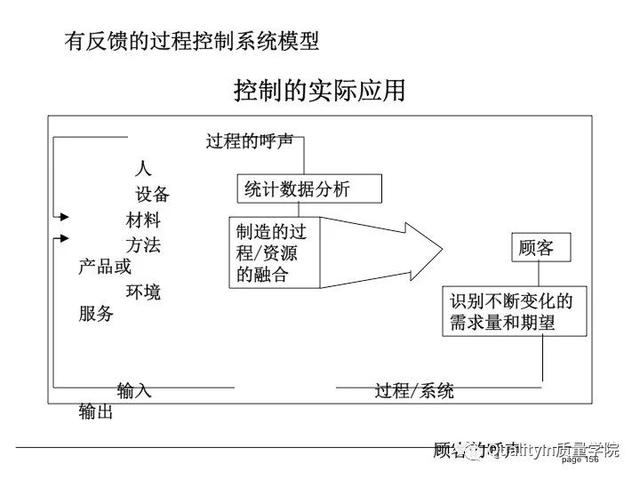
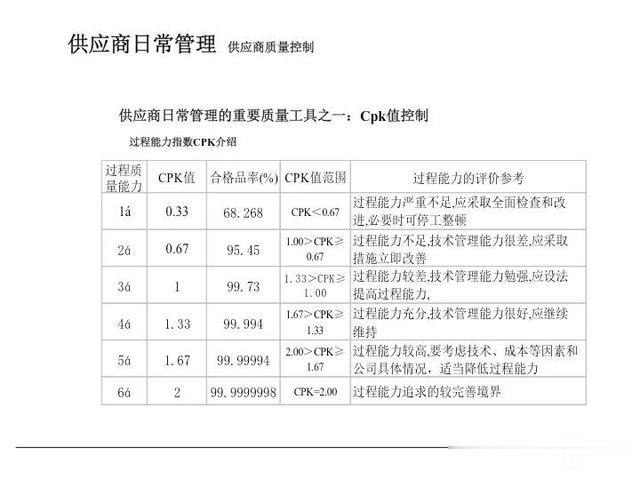
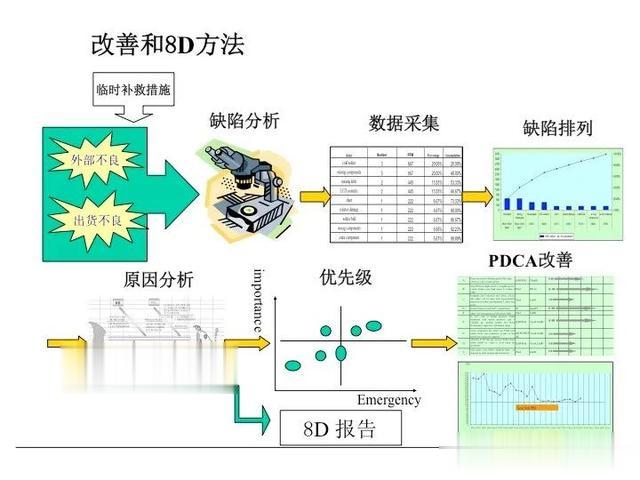
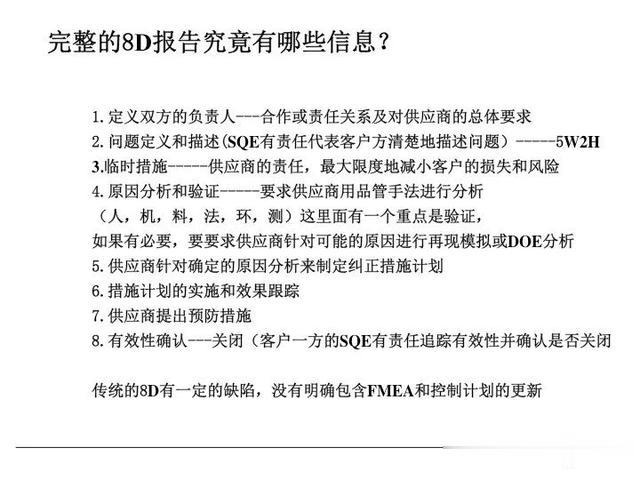
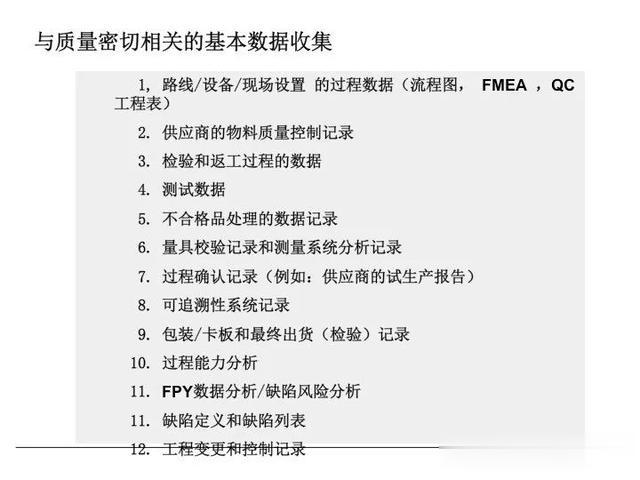
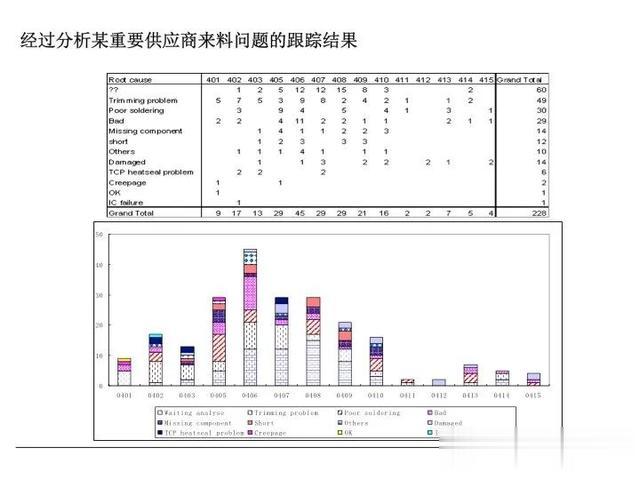
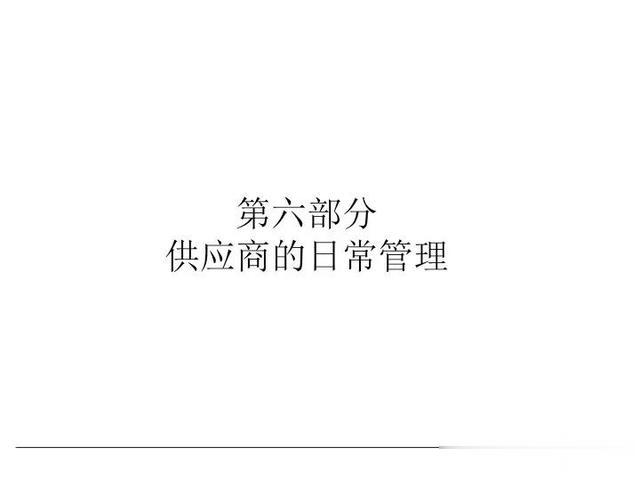
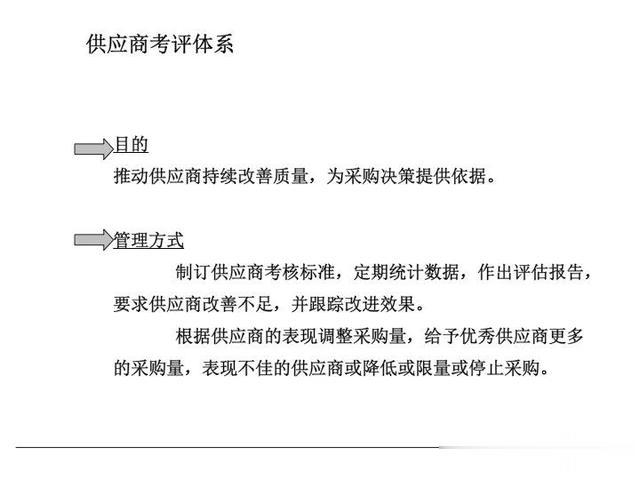
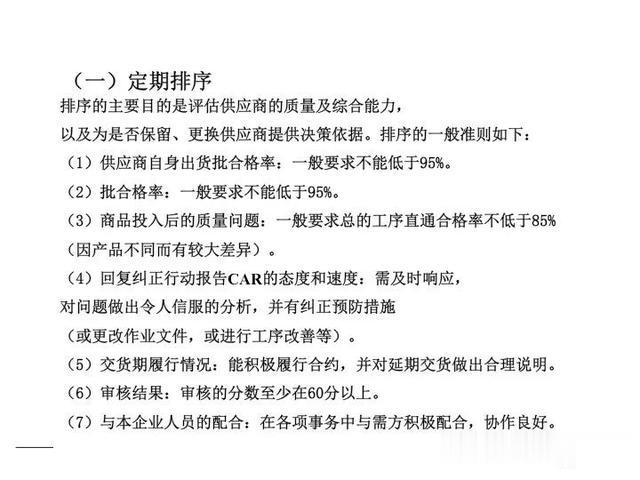
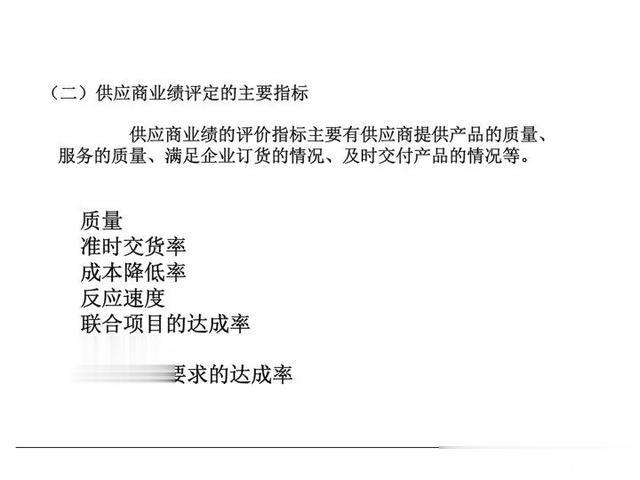
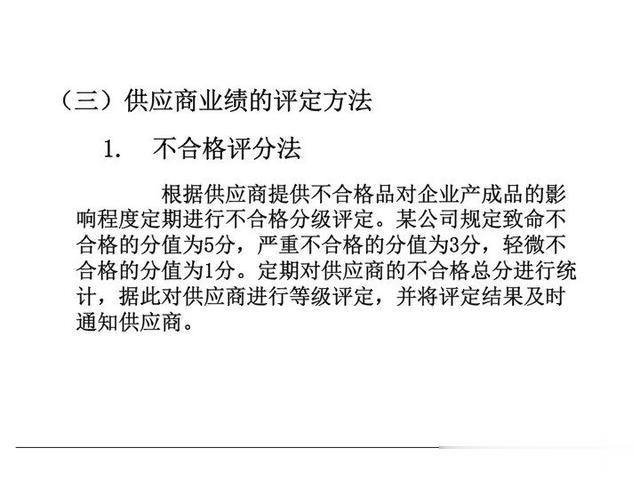
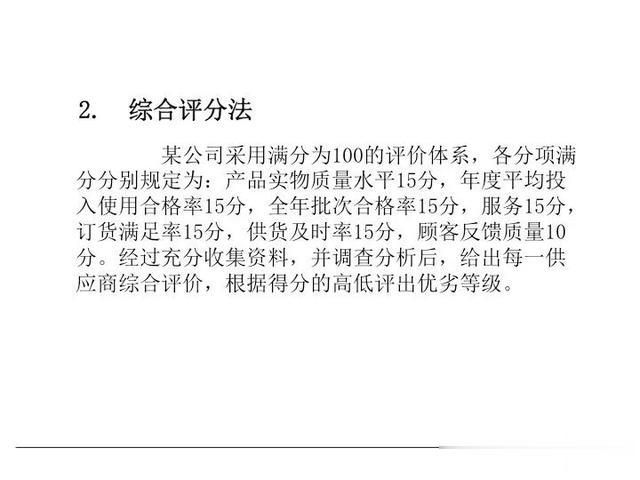
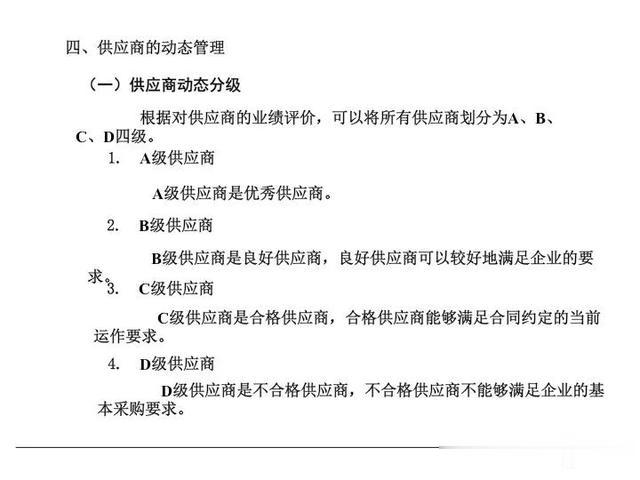
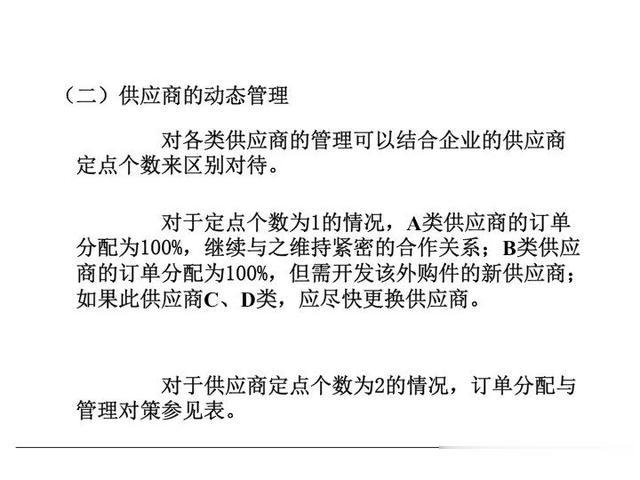
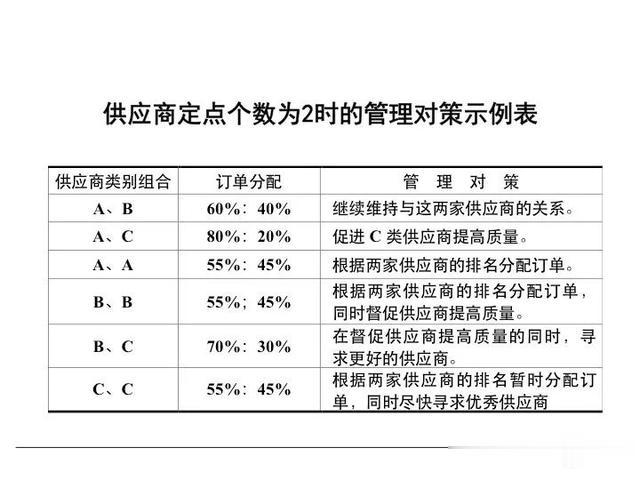

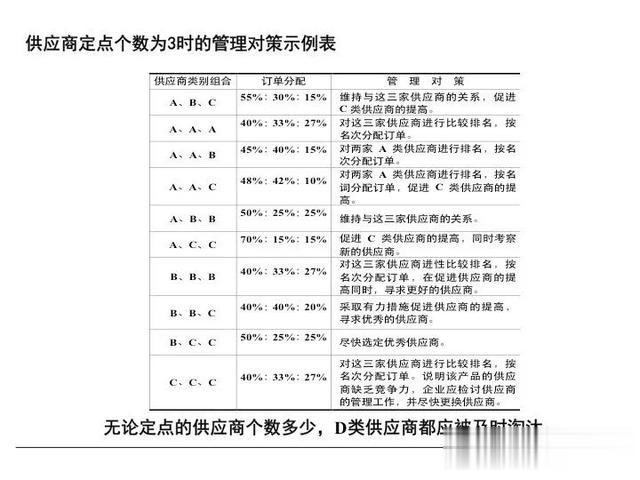
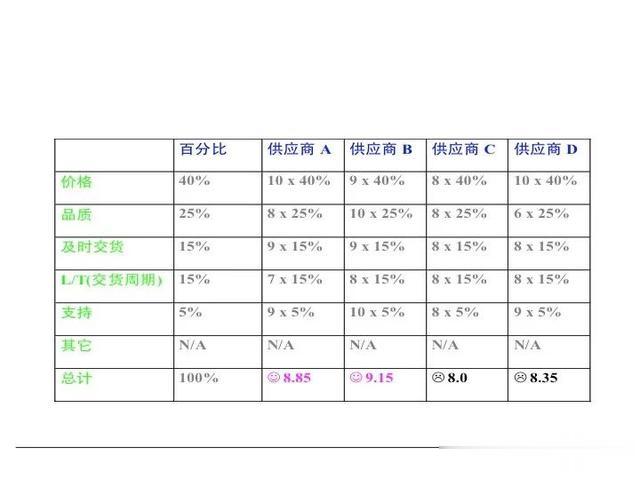
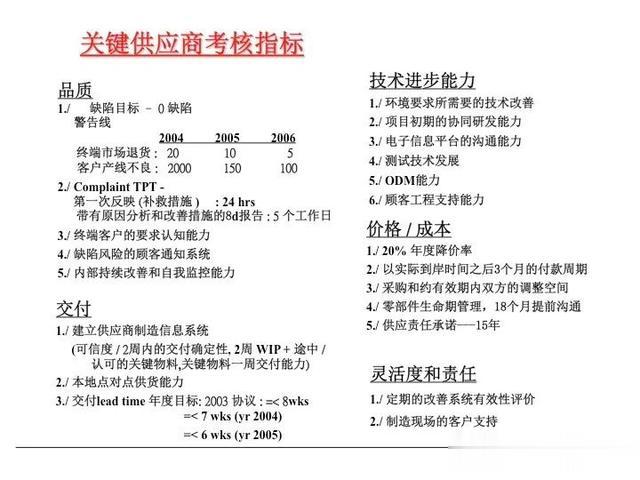
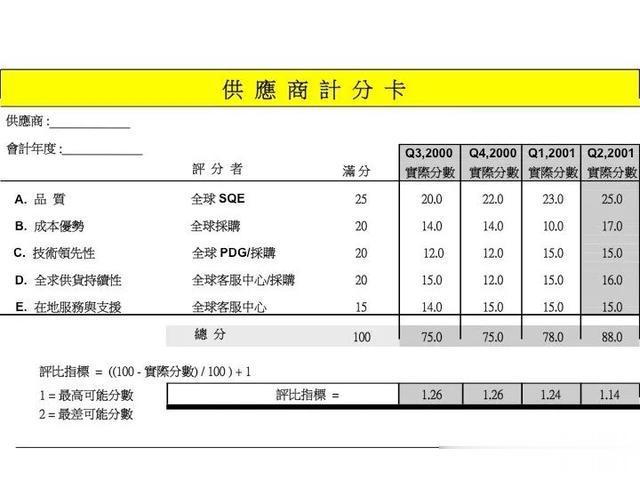
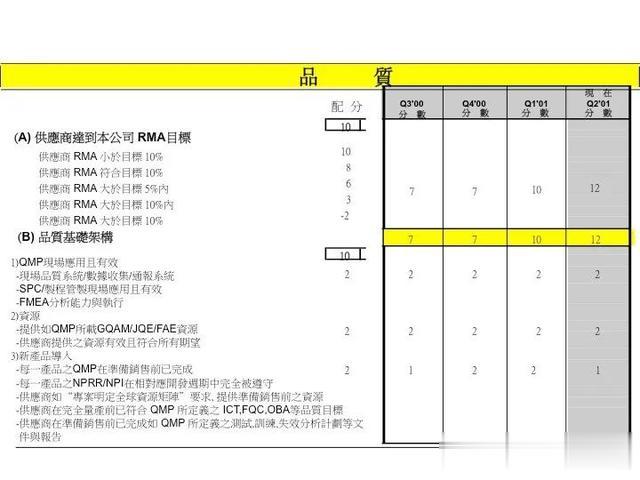
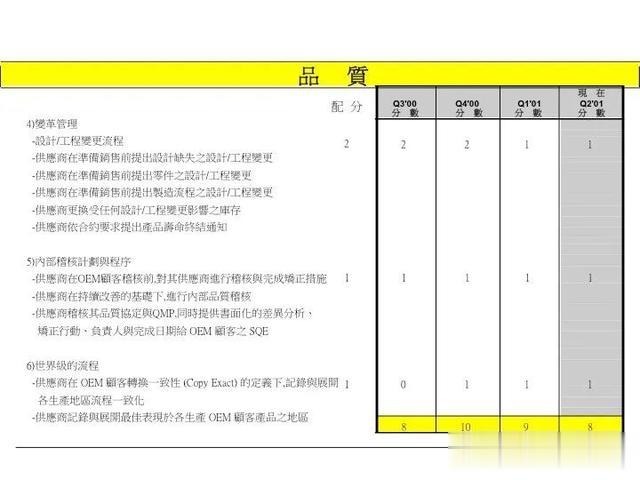
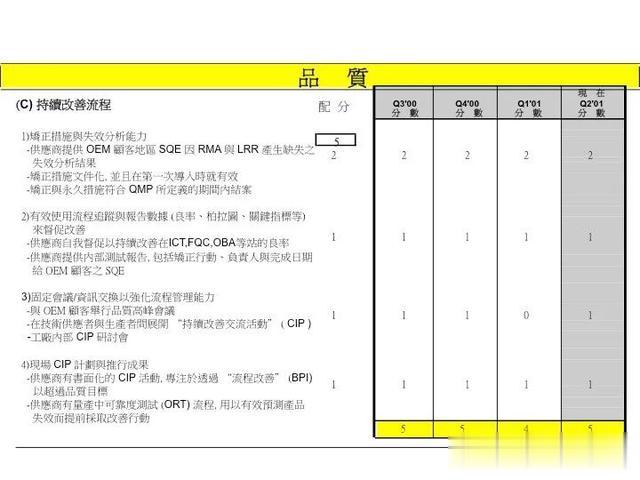
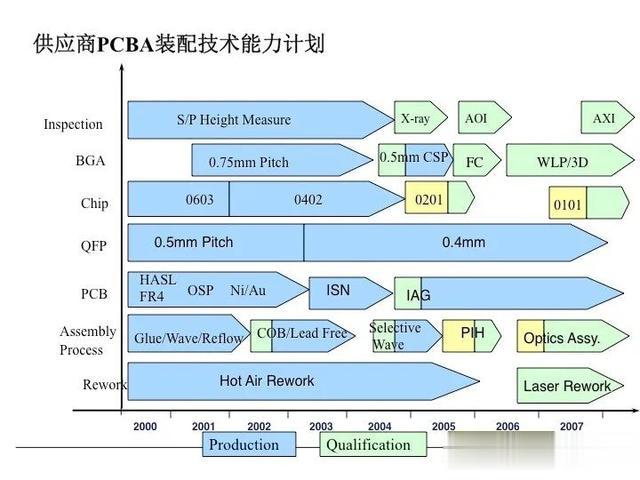
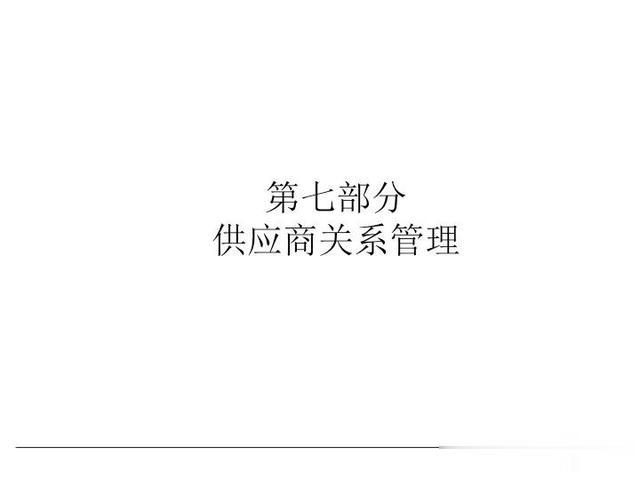
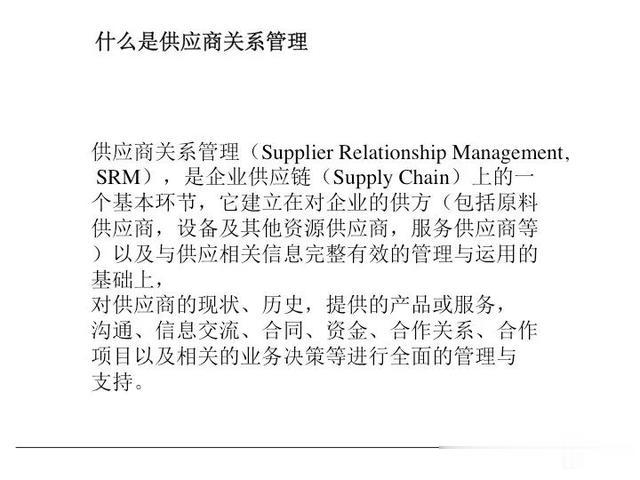
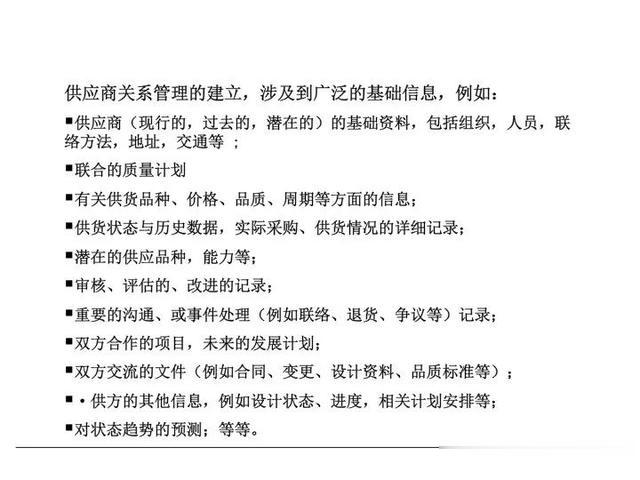
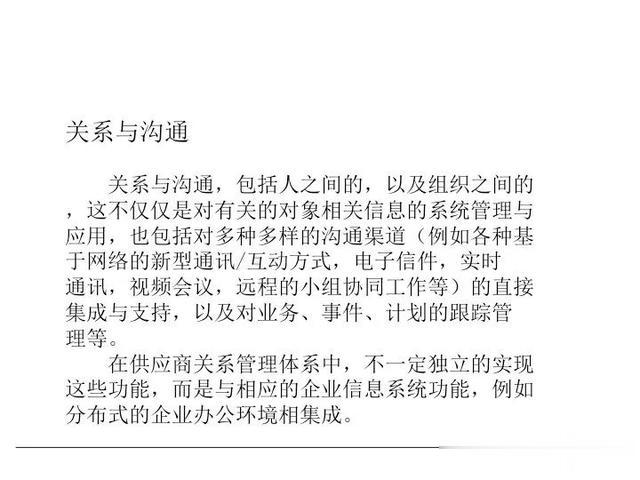
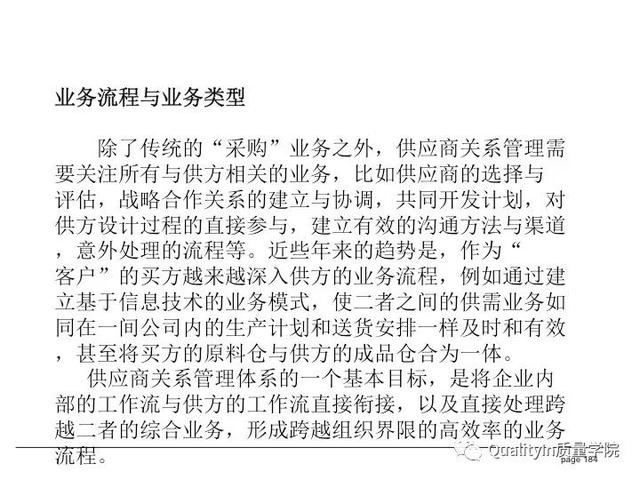
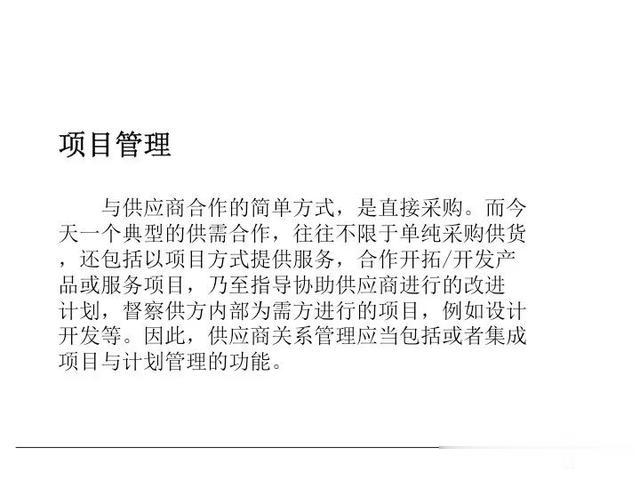
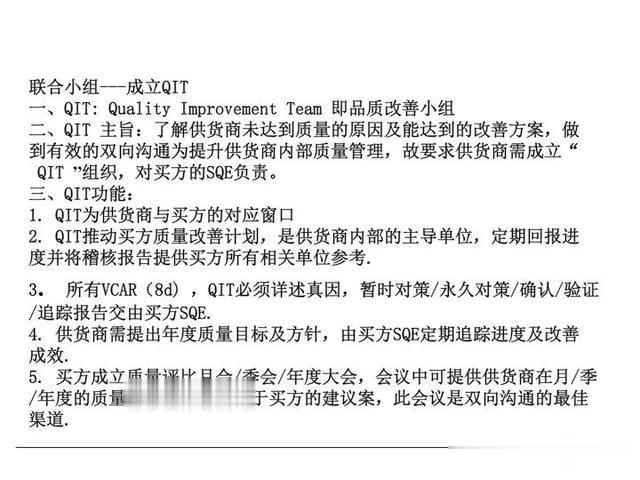
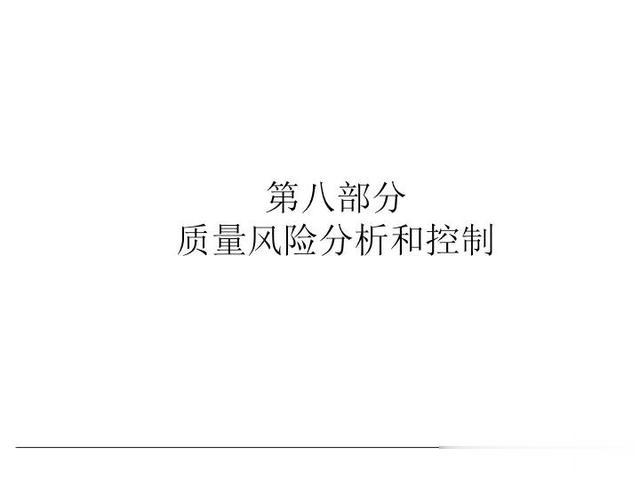
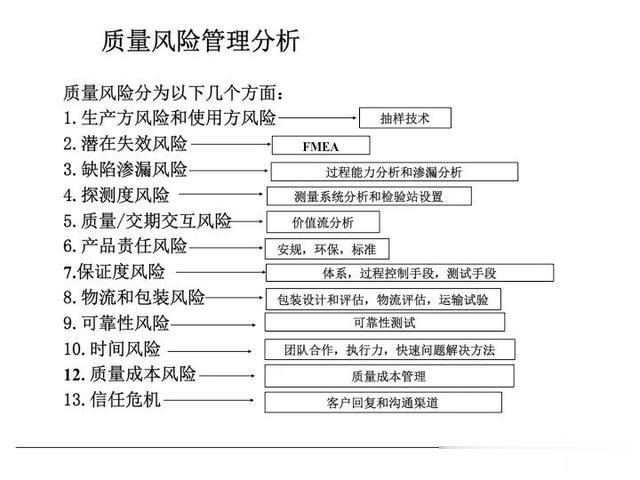
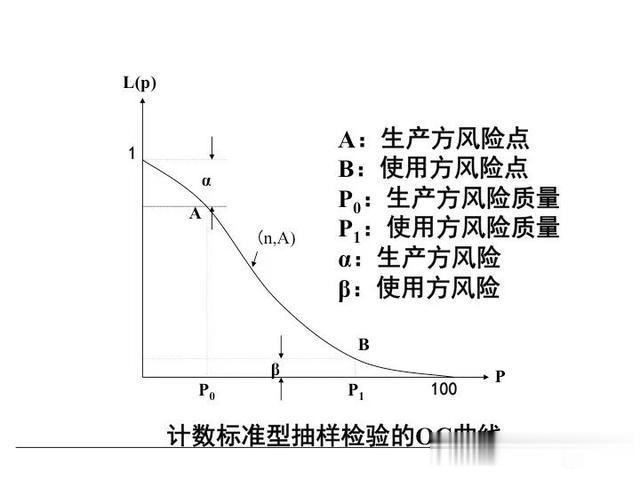
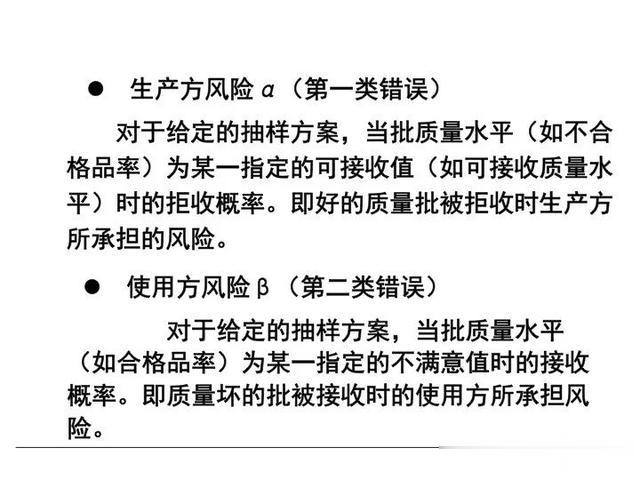
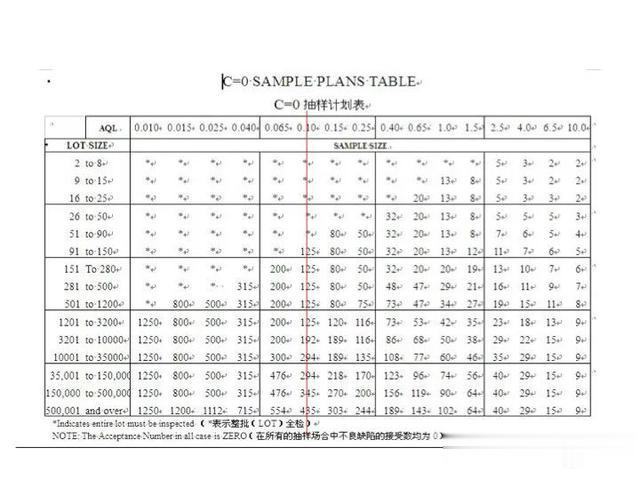
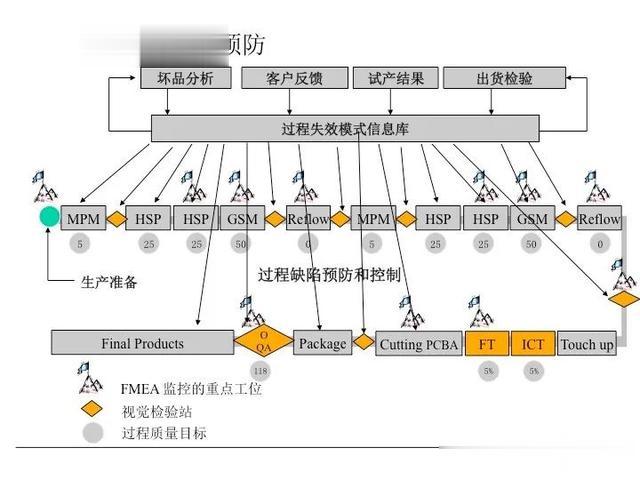
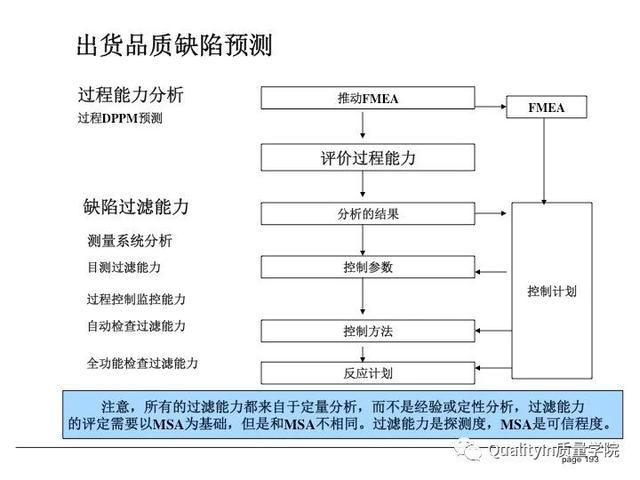
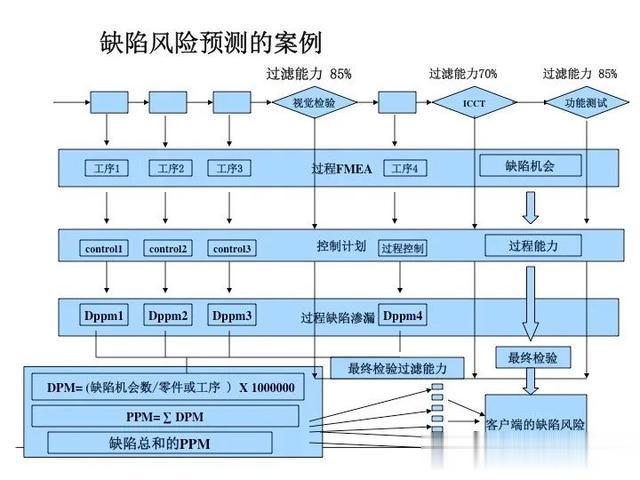
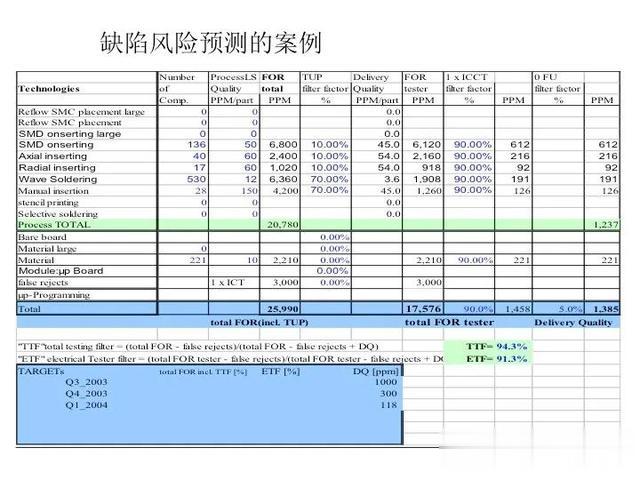
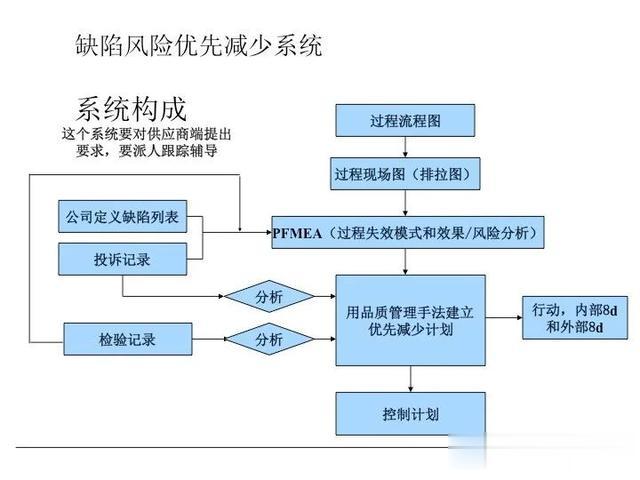
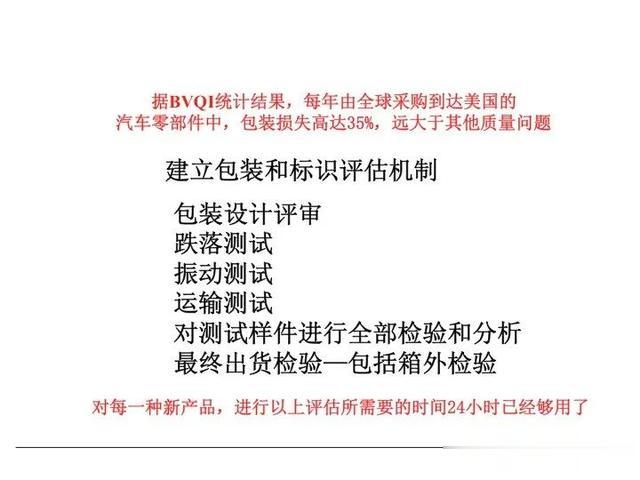
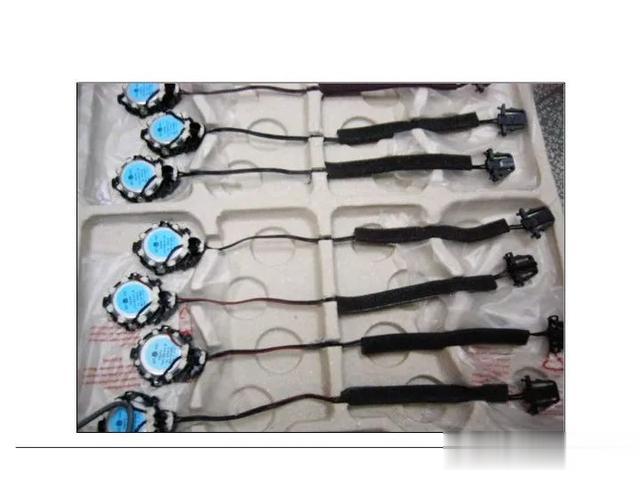
更多专业质量文章,请访问QualityIn质量学院官网www.quality-in.com
One More Thing
「全价值链质量工具实操知识」明星家族产品
每个人都值得拥有的质量知识宝典
随时学习,指导工作!
▼▼▼
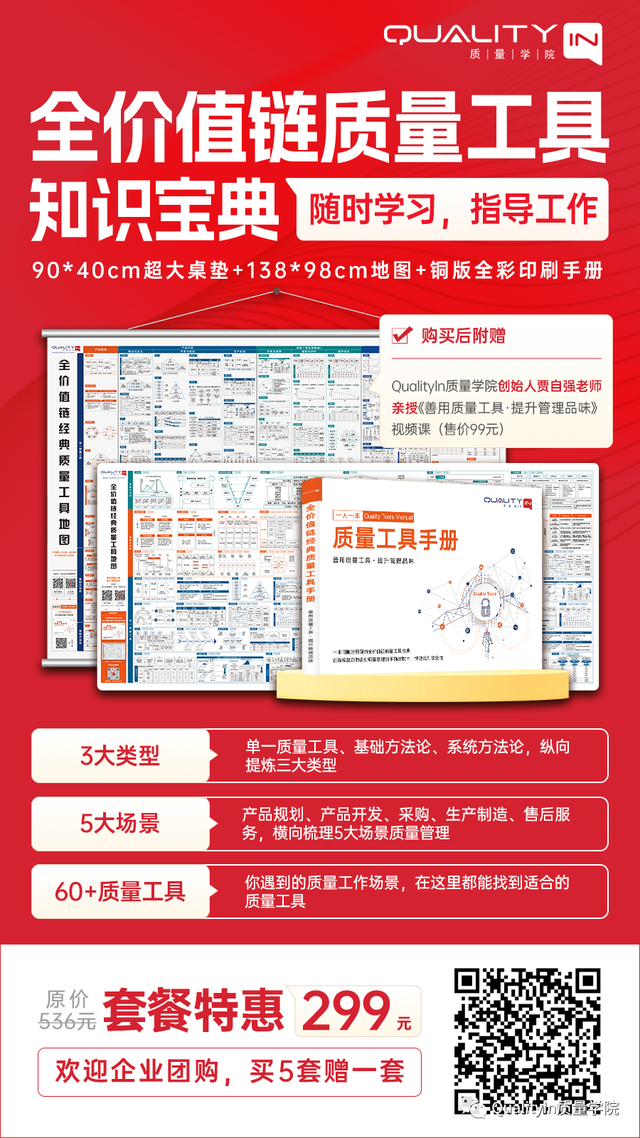