功率器件封装用纳米浆料制备及其烧结性能研究进展
杨 帆 杭春进 田艳红
(哈尔滨工业大学先进焊接与连接国家重点实验室)
摘 要:
随着 SiC、GaN 等第三代半导体在大功率器件上的应用,功率器件的工作温度可达到 300 ℃,传统 Sn 基无铅钎料因为熔点低及钎焊温度高等原因无法满足要求。纳米浆料因其可以实现低温烧结、高温服役的特性吸引了国内外研究者的青睐。从纳米颗粒的合成、纳米浆料的制备、烧结性能以及可靠性等方面综述国内外纳米浆料的研究进展,同时对纳米浆料研究中存在的问题提出一些建议。
1 引言
随着第三代半导体材料的应用,功率器件工作温度可达 300 ℃ [1] ,这对封装材料提出了更高的要求。传统 SnPb 钎料熔点低 [2] ,不满足功率器件的工作要求,而且 Pb 有毒,对人体有害而被禁止使用。应用于电子封装高温领域的高 Pb(质量分数大于 85%) 钎料,如95Pb5Sn、90Pb10Sn 等,熔点达到 300 ℃,虽然在RoSH 指令中得到豁免 [4-5] ,但其固相线温度低于300 ℃仍不能应用于功率器件的封装。目前应用于微波器件、LD 等大功率高温器件的封装材料是 Au-Sn、Au-Ge,熔点高,具有较好的抗蠕变性能和耐腐蚀性,但 Au 基合金具有脆性,成本高 [6-7] ,应用有限,因而寻求应用于功率器件封装的连接材料成为国内外研究者的热点。由于纳米尺寸效应,金属颗粒达到纳米尺寸时,烧结温度远低于金属材料的熔点,可以实现低温烧结、高温服役。目前纳米浆料的研究主要集中在Cu、Ag、Cu@Ag 等。本文对纳米浆料的纳米颗粒合成、浆料的制备、烧结性能以及可靠性等方面的研究进展进行综述,为今后纳米浆料的进一步研究及应用提供参考。
2 纳米颗粒合成及浆料制备
2.1 Cu 纳米颗粒合成及浆料制备
Cu 纳米颗粒因价格低廉且具有良好的导热性、导电性以及不易发生电迁移等优点而被广泛应用于电子封装领域,因而 Cu 纳米浆料成为电子互连材料研究中的一个热点。日本茨城大学 KOBAYASHI 等 [8] 采用水合肼还原氯化铜,柠檬酸为稳定剂,防止 Cu 氧化,通入氮气,反应 3 h,清洗、离心,在真空中烘干,得到 Cu 纳米颗粒。柠檬酸浓度影响颗粒大小,浓度从 0增加到 1.5×10 -3 mol/L 时,颗粒尺寸从 44 nm±15 nm 增长到 149 nm±27 nm,因为浓度高,增强溶液中的离子强度,导致初期形成的 Cu 核发生聚集。水合肼浓度也影响颗粒大小,浓度从 0.2 mol/L 增大到 1.0 mol/L 时,Cu 纳米颗粒的尺寸却从 79 nm±23 nm 减小到 65 nm±19 nm,因为浓度高,反应快,初期形成 Cu 核数量多。同时发现,柠檬酸和水合肼浓度高不会出现氧化。KOBAYASHI [9] 等还采用水合肼分别还原氯化铜、硝酸铜、醋酸铜,合成颗粒尺寸分别是 64 nm±16 nm、55 nm±15 nm、54 nm±15 nm,因为前两者是强酸盐,溶液中的离子强度高,在颗粒生成的时候就开始发生聚集。作者还发现不同摩尔浓度的水合肼还原醋酸铜,合成的颗粒尺寸无变化。韩国首尔大学 LEE 等 [10] 使用异丙醇胺作为稳定剂,因为它同时含有羟基和氨基,可以更有效地包覆 Cu 颗粒,合成过程及 Cu 纳米颗粒如图 1 所示,提高水合肼注射速度,可合成小到 10 nm的 Cu 颗粒。
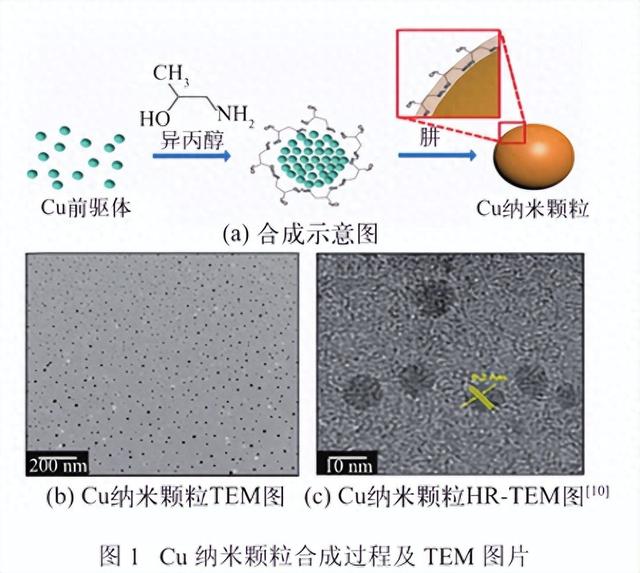
清华大学 YAN 等 [11] 采用多元醇法合成 Cu 纳米颗粒,将硼氢化钠和 PVP 加入到乙二醇中,加热到90 ℃,再加入硝酸铜,溶液颜色从蓝色变成红褐色,反应结束,进行清洗、离心,合成颗粒尺寸为 20~110 nm,如图 2 所示,可以看出颗粒有圆球型和多面体形状,表面有一层有机物,通过 XPS 确定是 PVP,可以有效防止颗粒团聚。华中科技大学 LI 等 [12] 用硫酸铜替代硝酸铜,合成颗粒尺寸在 40~80 nm,将其与丁醇按质量比13∶7 混合制备浆料。LI 等 [13] 还研究用维生素 C 还原Cu(OH) 2 ,颗粒尺寸为 80~120 nm,较之前颗粒尺寸大,与 n-甲基-2-吡咯烷酮按质量比 7∶3 混合搅拌制备浆料。华中科技大学 CHENG 等 [14] 也采用相同方法,制备的颗粒尺寸达到 140 nm,但可能由于反应温度较低,反应慢,Cu 核形成较少。为了合成更小的 Cu 纳米颗粒,Li 等 [15] 将含有醋酸铜和异丙醇胺的乙二醇溶液进行冰浴,再将水合肼加入到乙二醇溶液中,反应 12 h,溶液呈现暗红色,经过清洗、离心得到 Cu 纳米颗粒,发现最小颗粒尺寸为 5 nm,但团聚现象明显,而且出现氧化现象。为了得到更纯净的 Cu 纳米颗粒,哈尔滨工业大学 LIU 等[16]通过多元醇法合成 Cu 纳米颗粒(30 nm),将合成的颗粒加入到含有甲酸的无水乙醇溶液中,浸泡 10~30 min,再进行清洗、离心,发现离心液偏蓝色,说明合成的 Cu 纳米颗粒发生氧化,甲酸可去除氧化铜。延世大学 JEONG 等 [17] 发现当 PVP 摩尔质量越大时,Cu 纳米颗粒表面的氧化层厚度由 3.1 nm减小到 1.6 nm,说明 PVP 具有阻碍氧化的作用。大阪大学 GAO 等采用一步法合成 Cu 纳米颗粒,将PVP、Cu(OH) 2 、硫化钠按一定比例加入 1,3 丙二醇中,加热到 190 ℃,反应 90 min,清洗、离心得到 Cu 颗粒,颗粒尺寸较大,在 200~1000 nm,所得 Cu 颗粒与聚乙二醇按质量比 1∶0.15 混合,制备浆料。
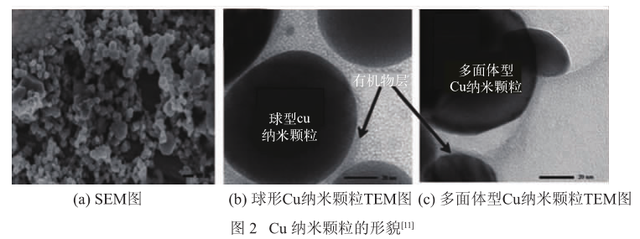
目前 Cu 纳米浆料尚处在研究探索阶段,距离应用还有很多需要解决的问题。首先要解决的就是氧化的问题,合成 Cu 纳米颗粒的过程需要在无氧的条件下,这会增加成本,即使采用多元醇法,用 PVP、柠檬酸等作为包覆剂也不免被氧化,合成过程中加热更容易导致 Cu 颗粒被氧化,而且在制备浆料时,应注意有机物要适量添加以及该有机物的熔点要低,不然影响烧结效果。
2.2 Ag 纳米颗粒合成及浆料制备
由于 Cu 纳米颗粒容易氧化,制备的 Cu 纳米浆料不易保存,因而其研究受到限制。Ag 纳米颗粒同样具有优良的导电导热性能,因而 Ag 纳米浆料作为一种新型的绿色无铅封装材料受到研究者的青睐。哈尔滨工业大学 QIU 等 [19] 采用硼氢化钠还原硝酸银,发现PVP 和温度影响 Ag 纳米颗粒大小,当 AgNO 3 /PVP 质量比例为 1∶4 时,Ag 纳米颗粒最小,在 20~35 nm,当PVP 占比过高,Ag 纳米颗粒表面的有机物层就越厚,Ag 纳米颗粒之间发生接触,导致颗粒团聚,因此 PVP要适量。温度影响了反应速率,当温度为 30 ℃时,Ag纳米颗粒无团聚现象,同时颗粒达到最小(22.4 nm),温度低时可能不发生反应,温度过高时,Ag 成核的速率小于长大速率,合成的颗粒较大。而哈尔滨工业大学 LI 等 [20] 将柠檬酸钠和硫化铁的混合还原性溶液加入到硝酸银溶液中,合成尺寸较小的 Ag 纳米(10 nm)颗粒,如图 3(a)所示。图 3(b)是平均尺寸为 50 nm 的Ag 纳米颗粒,先将硝酸银溶液边搅拌边加热到沸腾,之后将柠檬酸钠溶液加入硝酸银溶液中,继续加热1 h,再将溶液冷却到 20 ℃,经过清洗、离心得到。将合成的较小尺寸的 Ag 纳米颗粒与较大尺寸的 Ag 纳米颗粒按质量比 2∶1 混合,再溶于硝酸钠溶液中进行超声,之后离心、清洗,重复两次得到 Ag 纳米浆料。清华大学 YAN 等 [21] 采用多元醇法合成 Ag 纳米颗粒时,需要将含有 PVP 的乙二醇溶液加热到 160 ℃,将含有硝酸银的乙二醇溶液也加热到 160 ℃,之后将前者加入
到后者进行反应,合成颗粒尺寸达到 100 nm。清华大学 ZOU 等 [22] 将柠檬酸钠加入到温度为 80 ℃的硝酸银溶液中,再将溶液加热至 90 ℃继续反应 1 h,冷却,清洗、离心,得到平均尺寸为 45.4 nm 的 Ag 颗粒。马来西亚理科大学 TAN 等 [23] 将尺寸分别为 40 nm±10 nm 和50 nm±10 nm 的 Ag 和 Cu 纳米颗粒与有机粘结剂、溶剂按一定比例混合制备纳米浆料。
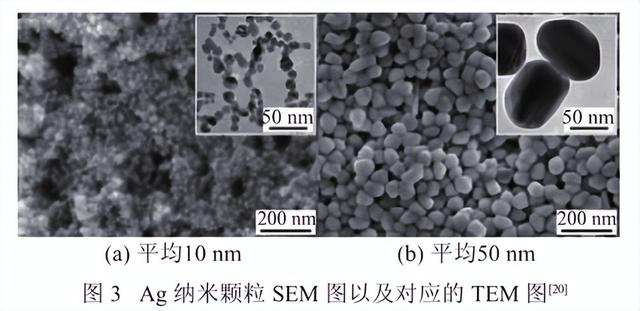
相对于 Cu 纳米颗粒,Ag 纳米颗粒的合成比较简单,合成的颗粒也比较小而均匀,但包覆剂厚度的控制以及 Ag 纳米颗粒形貌和尺寸的可控制备还需进一步研究。相比商业上应用较广的日本京瓷株式会社的纳米浆料而言,中国在大规模生产和制备方面还有一定的距离,尤其是烧结后的服役可靠性尚需系统研究。
2.3 Cu@Ag 核壳纳米颗粒合成及浆料制备
研究者发现 Cu@Ag 纳米浆料能克服 Cu 纳米浆料氧化和 Ag 纳米浆料电迁移的问题。哈尔滨工业大学田艳红等 [24] 采用多元醇法合成 Cu@Ag 纳米颗粒,将 PVP 和硼氢化钠溶解在二乙二醇中,之后将硫酸铜溶液注入前者中,清洗、离心得到 Cu 纳米颗粒。通过添加氢氧化铵调节好 pH 的硝酸银溶液加入到含有Cu 纳米颗粒的水溶液中反应 5 min,用稀盐酸清洗,去除多余的 PVP,颗粒平均尺寸约为 50 nm,XRD 测试未发现有氧化现象,之后与二乙二醇按质量比 6∶1 混合,在 60 ℃下加热挥发多余的溶剂得到 Cu@Ag 核壳纳米颗粒浆料。武汉理工大学 ZHAO 等 [25] 发现不同的Cu/Ag 摩尔比影响颗粒尺寸,当 Cu/Ag 摩尔为 1∶1 时,Cu@Ag 颗粒尺寸最小,在 100~150 nm。台湾大叶大学PENG 等 [26] 发现改变柠檬酸钠 /Ag 的摩尔比可以控制颗粒的大小、形貌,随着柠檬酸钠 /Ag 的摩尔比例增大,部分包覆变为完全包覆,而且颗粒近似球型或六角形。PENG等 [27] 还发现当柠檬酸钠/Cu和柠檬酸钠/Ag的摩尔比例分别为 0.25/1、8/1 时,Cu 颗粒表面有一层致密的 Ag 层,但尺寸达到微米级。台湾成功大学CHEN 等 [28] 合成的 Cu@Ag 颗粒尺寸也是微米以上,形状不规则,分散性尚需改进。台湾科技大学 TSAI等 [29]合成的 Cu@Ag 纳米颗粒,平均尺寸为 25 nm,且分布均匀。广东工业大学 CAO 等 [30] 将尺寸为 3 μm 的 Cu颗粒分散在稀盐酸中,去除 Cu 颗粒表面氧化物,再将乙酰丙酮加入到硝酸银溶液中,之后加入到处理后的Cu 颗粒溶液中,反应 30 min,最后得到的 Cu@Ag 颗粒尺寸还是微米级的。韩国地球科学与矿产资源研究所 HAI 等 [31] 采用同样的方法,使用更大的 Cu 颗粒,最后合成的 Cu@Ag 核壳颗粒更大,且Cu 颗粒表面并不是完全被 Ag 颗粒包裹。
韩国科学技术院研究者 LEE 等 [32] 在 235 ℃下将乙酰丙酮铜进行分解,得到 Cu 颗粒,再将硝酸银溶液加入到 Cu 溶液中,加热到 80 ℃,反应 2 h 后,进行清洗、离心,真空干燥,得到 Cu@Ag 核壳纳米颗粒,如图4 所示,尺寸为 13.5 nm,均匀、分散性好。捷克马萨里克大学 SOPOU譒EK 等 [33-34] 采用同样的方法,得到的颗粒 更 小 且 分 散 也 均 匀 。 以 色 列 希 伯 来 大 学GROUCHKO 等 [35] 用水合肼还原硝酸铜,再将 Ag+ 溶液加入到刚合成的 Cu 纳米颗粒溶液中反应,得到 Cu核 40 nm、Ag 层 2 nm 的 Cu@Ag 核壳纳米颗粒。韩国原子能研究所 KIM 等 [36] 将仪器、设备结合在一起,进行一步法合成 Cu@Ag 纳米颗粒,其实质还是先“生产”Cu 纳米颗粒,再进行置换反应,得到 Cu@Ag 纳米颗粒,产量较大,但设备多,还需通氩气,成本高,合成的颗粒尺寸较大,达到 900 nm。日本九州大学 TSUJI等 [37] 采用加热醋酸铜溶液,使其受热分解制备 Cu 颗粒,再进行置换反应合成尺寸为 80 nm 的 Cu@Ag 核壳纳米颗粒,如图 5 所示,红色代表 Cu,绿色代表 Ag,有些 Cu 颗粒未被包裹。

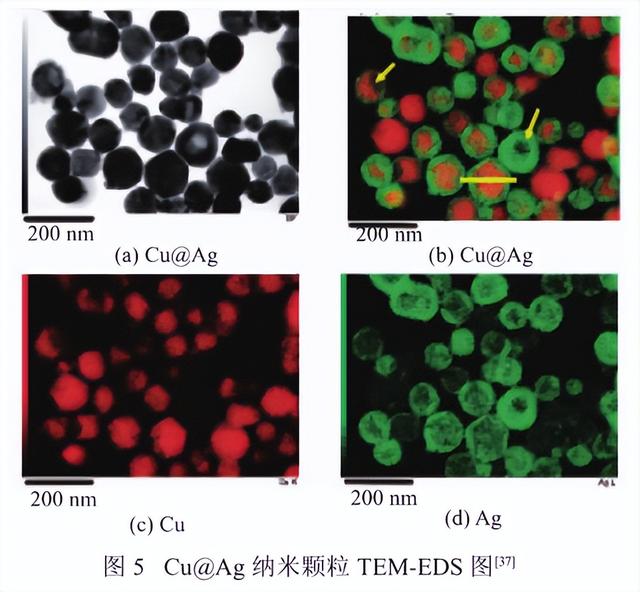
哈尔滨工业大学研究者还合成了其他金属纳米颗粒,例如 ZHONG 等 [38] 将氯化铜和四氯化锡混合溶液加入到还原性溶液中,合成 Cu 6 Sn 5 纳米颗粒,发现不同的表面活性剂和温度影响颗粒的大小,如图 6 所示,当使用 CTAB[(C 16 H 33 )N(CH 3 ) 3 Br]作为表面活性剂、反应温度在 10 ℃时,合成的 Cu 6 Sn 5 纳米颗粒最小为6.4 nm,通过 DSC 测试,其熔点 180 ℃也是最低。哈尔滨工业大学 LIU 等 [39] 采用柠檬酸作为分散剂,利用硼
氢化钠的强还原性,将含有硝酸铜和硝酸银的混合溶液还原,创造性地合成 Ag-Cu 共溶体纳米颗粒,尺寸小到 5 nm,XRD 显示了 5 个 Ag 的峰值、4 个 Cu 的峰值,未发现其他峰,说明 Ag-Cu 共溶体纳米颗粒具有抗氧化性。哈尔滨工业大学 CHEN 等[40]将尺寸为30 μm 的 Cu 颗粒加入到含有氯化亚锡的溶液中,反应 3 h,得到 Cu@Sn 核壳颗粒,主要是利用在回流焊时 Sn 与 Cu 形成 IMC,实现较强的键合。
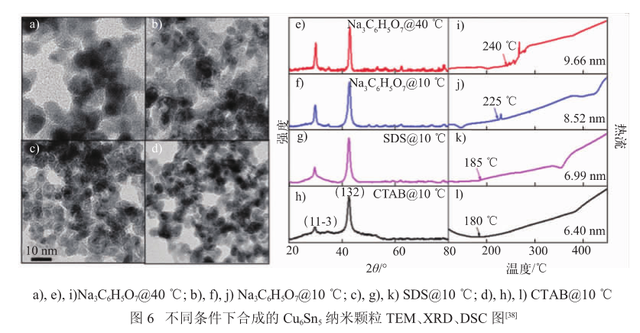
3 纳米浆料烧结接头性能研究
抗氧化性、机械强度、导电性等是评价纳米浆料接头可靠性的重要参数。华中科技大学 LI 等 [13] 发现在空气中存储 30 天后 Cu 纳米浆料才出现了些许氧化的现象,说明包覆在 Cu 纳米颗粒表面的 PVP 阻碍了Cu 纳米颗粒的氧化。大阪大学 NISHIKAWA 等 [41] 在15 MPa 不同温度下烧结 300 s 键合 Cu-Cu,发现随着烧结温度的升高,剪切强度变大,当烧结温度达到320 ℃及以上时,在氮气中烧结后得到的剪切强度明显优于在空气中,因为当温度逐渐升高后,包覆剂分解,无法起到防氧化的作用,但氮气氛围保护 Cu 纳米颗粒不被氧化,而空气不行。作者又在不同温度下预热 300 s,之后在 15 MPa、400 ℃下烧结 300 s,当预热温度小于 227 ℃时,剪切强度变化不明显,当预热温度增大后,剪切强度却下降了。这是由于在预热时,Cu 纳米颗粒已经发生了烧结,导致颗粒尺寸变大,后面无法烧结或者烧结性变差,从而致使剪切强度下降。大阪大学 YAMAKAWA 等 [42] 也是采用热压方式,发现在真空中预热温度越高,剪切强度越大,接近 50 MPa,在空气中结果却相反,因为在空气中预热时,Cu 颗粒发生氧化。作者还发现随着温度的升高,剪切强度增大,在压强 0~15 MPa 时,随着压强增大,剪切强度增大更快 , 因 而 可 以 适 当 增 加 烧 结 压 强 。 茨 城 大 学KOBAYASHI 等 [8] 在 400 ℃、1.2 MPa 下的 H 2 中对 Cu纳米浆料 (71 nm±14 nm) 进行烧结,剪切强度达到28.6 MPa,还原气氛也能提高烧结效果。哈尔滨工业大学田艳红等 [43] 采用脉冲电流对 Cu 纳米浆料进行快速烧结,发现电流强度越大,获得的剪切强度也越大,同样的对 Cu@Ag 纳米浆料进行脉冲电流烧结 [44] ,得到同样的结果,经过微观组织观察发现,电流强度大,激发的能量高,从而使得纳米浆料烧结充分,组织致密,剪切强度也就越大,而且在相同电流下,Cu@Ag 纳米浆料获得更大的剪切强度,可能是因为 Cu@Ag 表面的 Ag 纳米颗粒更小,更容易烧结。哈尔滨工业大学LIU 等 [16] 发现经过甲酸处理的 Cu 纳米浆料获得的剪切强度远大于未经甲酸处理的,在 320 ℃、10 MPa 下烧结 5 min,剪切强度达到 51.7 MPa,电阻率最低为3.16 μΩ·cm,说明经过甲酸处理后,Cu 纳米颗粒的性能得到提高,主要是甲酸祛除了 Cu 表面的氧化物。韩国延世大学 WOO 等 [45] 发现经过甲酸和草酸处理后,电阻率变化近乎相同,而柠檬酸处理后的结果明显不如前两者,如图 7 所示,观察显微组织后发现,前两者烧结后虽有孔洞,但颗粒之间都实现了有效的烧结,而柠檬酸处理后的 Cu 纳米颗粒烧结后出现大量的孔洞,而且有许多孤立的颗粒,导致导电性差。华中科技大学 LI 等 [46] 采用低压(0.98 MPa)烧结,发现剪切强度随着烧结温度的升高而增大,图 8 为样品的剖视图,从图 8(a)可以看出,150 ℃烧结后有较大的空洞出现,经过 300 ℃烧结后,几乎无孔洞出现,键合致密。日本丰田中央实验室 WATANABE 等[47]在 Cu 纳米颗粒(150~200 nm) 中添加质量分数 5 %的 Cu-Ni 纳米颗粒(~20 nm) 制备混合浆料,发现当 Cu 基板上镀上一层40 nm 的 Ni 层时,剪切强度达到 15 MPa,可能是因为Cu 和 Ni 在固态可以互溶,实现较强的键合。


哈尔滨工业大学 WANG 等 [48] 采用 Ag 纳米浆料(20 nm)进行 Cu-Cu 无压键合,分别在 150 ℃和 200 ℃下烧结 20 min,剪切强度为 17 MPa 和 25 MPa。后来WANG 等 [49] 发现包裹 Ag 纳米颗粒的有机物对烧结过程影响很大,因而对有机物层进行减薄处理,剪切强
度也提高到 25 MPa 和 60 MPa。田艳红等 [50] 开发了SnAgCu 纳米焊膏,在 230 ℃加热 SnAgCu 纳米钎料键合 Cu-Cu,发现压力在 0~10 N 时,压力越大,剪切强度越大,主要是因为加热时压力小,大量气体汇聚在钎料表面,IMC 和纳米钎料之间有大量气孔存在,导致接头强度下降;相反,加热时压力大,可以排除更多的气体,使得组织致密,减小缺陷,从而使剪切强度增大。哈尔滨工业大学 HU 等 [51] 发现在 Ag 纳米浆料(50 nm)中添加 SiC 纳米颗粒(40 nm)可以提高其性能,添加 0.5% SiC 的浆料在 275 ℃下烧结 50 s 后获得最大剪切强度,为 74.1 MPa。天津大学 QI 等 [52] 采用 Ag纳米浆料进行大面积焊接时发现会有大概率出现孔洞,主要是因为阻碍了其中的有机物挥发,因而在制备 Ag 纳米浆料时应控制有机物层的厚度。天津大学MEI 等 [53] 发现与传统的热压烧结相比,电流辅助烧结时间更短,在 8.25 kA 下烧结 100 ms,其剪切强度达到100MPa,微观组织致密,没有孔洞。天津大学 MEI 等 [54] 还对绝缘栅双极型晶体管(IGBT)进行封装,其剪切强度达到了 20 MPa。LI 等 [55] 采用不同的 Ag 颗粒(20~100 nm 和 1~5 μm)混合而成的浆料进行无压烧结,随着温度的升高,其组织越致密,因而剪切强度也随着温度的升高而增大,300 ℃下烧结强度达到 58 MPa。LU 等 [56] 研究电压、温度等对 Ag 纳米浆料电迁移的影响,在高压下,阴极处的银会以树枝晶状向着另一极生长,当电流超过 1 mA 后,出现短路。随着电压和温度的增加,短路时间减少。韩国成均馆大学 KIM 等 [57]测试 Ag 纳米浆料在不同温度下的电阻率,发现在最 高温度 300 ℃下烧结后,其电阻率最小达到2.86 μΩ·cm。同时采用水滴法研究 Ag 的电迁移现象,如图 9 所示,分别采用电压 3 V、6 V、9 V,在阴极处生长出枝晶状,向着另一极生长,电压越高,电迁移时间越短,温度越高,电迁移时间越短。另外 NOH 等 [58] 研究时发现,300 ℃烧结后电阻率为 5 μΩ·cm,比前面最小的电阻率大。
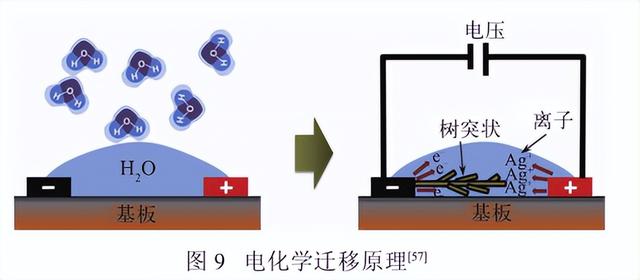
加拿大滑铁卢大学 HU 等 [59] 采用 Ag 纳米浆料连接 Cu 线和 Cu 焊盘,为获得较强的连接强度,施加5 MPa 辅助压强,随着烧结温度的升高,拉伸强度逐渐增大。清华大学 YAN 等 [21] 采用 Cu-Ag 纳米混合浆料将铜线和铜板连接,在 10 MPa、120 ℃下烧结,几乎没有键合的迹象,当温度升高,Cu 占比例越高的浆料剪切强度越大,可能是由于 Cu 颗粒尺寸小,且与 Cu 线、基板之间更易扩散。而马来西亚理工大学 TAN 等 [23] 发现随着 Cu 颗粒的比重增加,剪切力一直下降,可能是Cu 颗粒的增加导致出现更多的孔洞,而孔洞是裂纹开始以及延伸的首要原因。大阪大学 MORISADA 等 [60]也发现混合的 Ag-Cu 纳米浆料中 Cu 纳米颗粒越多,烧结越不完全,出现的孔洞越多,可能是在烧结过程中Cu 颗粒发生氧化。
华中科技大学 YU 等 [61] 发现 Cu@Ag 纳米颗粒在350 ℃下烧结后,电阻率为 27.1 μΩ·cm,而 Cu 的电阻率为 49.4 μΩ·cm,说明 Cu@Ag 纳米颗粒的导电性强。哈尔滨工业大学 JI 等 [62] 发现 Cu@Ag 纳米浆料在180 ℃下分别进行超声辅助烧结和热压烧结,超声辅助烧结后剪切强度远远高于热压烧结,原因是超声辅助烧结时其内部温度已不是设定的温度,达到 300 ℃以上,且超声加速了原子扩散,因而实现了更加致密的键合。
纳米浆料性能研究中,虽然 Cu 纳米颗粒表面被有机物包覆,但 Cu 纳米浆料的抗氧化性能还有待提高,而且想获得较强的键合强度,需要高压、高温以及无氧环境,这大大增加了成本。Ag 纳米浆料可以实现无压、低温烧结,但获得的接头一般强度不高,孔隙率难以控制。Ag 纳米浆料虽然具有较好的导电性,但电迁移问题严重。因此纳米浆料在服役过程中的可靠性需要进一步深入系统研究。
4 纳米浆料烧结接头可靠性研究
华中科技大学 LI 等 [46] 将采用 Cu 纳米浆料键合的Cu-Cu 放在 150 ℃下老化 200 h,经过微观组织分析,老化前和老化后微观组织相差无几,上、下基板连接致密,很少有孔洞之类的缺陷,而老化后强度略微增大一些,可能是老化温度不高、时间不长,但会进一步促进浆料与基板之间的原子扩散。哈尔滨工业大学田艳红等 [63] 采用动态电阻在线监测的方法,研究通电老化(1×10 4 A/cm 2 、150 ℃) 对 Ag 纳米浆料可靠性的影响,发现随着时间的延长,Ag 钎料基体孔隙率逐渐减小,粒径逐渐增大。而通电一天后,阴极处有细微的裂纹出现,电阻变化不明显,通电 5 天后出现断断续续的裂纹,有的部分宽度扩展到 1 μm,电阻已经出现明显的增大,说明裂纹对焊点的可靠性影响很严重,之后焊点几乎全部都是在通电老化 7 天时发生失效,出现断路。经过分析说明经过长时间的老化以及电迁移,阴极处的 Ag 原子在电子风力的作用下发生迁移,出现孔洞,逐渐演变成裂纹,电阻变大,最后断裂,此实验能够准确监测到焊点失效的时间,具有重要的实际意义。哈尔滨工业大学 YANG 等 [64] 在 Ag 纳米浆料中添加了微小的 Ag 片状颗粒,结果在不同温度下烧结后的剪切强度都是最大的,在经过 500 次和 1000 次热冲击(-50~150 ℃)后,所有样品的剪切强度下降,而添加微小的 Ag 片状颗粒的浆料剪切强度仍然最好,说明添加微小的 Ag 片状颗粒可以提高纳米 Ag 浆料对热冲击的抗性。而哈尔滨工业大学 HU 等 [51] 则是在 Ag 纳米浆料中添加 SiC 颗粒(40 nm),经过 275 ℃烧结后,将样品再进行热冲击(-50~150 ℃)实验,经过 1000 次热冲击后,剪切强度略有下降,而添加 2% SiC 的浆料在经过 1000 次热冲击后,剪切强度却明显增大,从46.6 MPa 增长到 87.1 MPa,说明 SiC 的添加可以提高Ag 纳米浆料抗热冲击的能力。
天津大学 LI 等 [65] 采用 Ag 纳米浆料封装大功率LED 模块,发现经过 1000 个热循环(-40~150 ℃)后,剪切强度已从 28.7 MPa 下降了 77.7%,主要是由热循环过程中产生的交变剪切应变引起的,从微观组织看,随着热循环次数的增加,焊点中出现的孔洞也越来越多。进行高温高湿(85℃/85%R.H)实验时发现,经过 1000 h 的存储后,剪切强度略微下降,说明高温高湿对 Ag 纳米焊点的影响远小于热冲击。LI 等 [66] 还研究了剪切应变速率、温度等对 Ag 纳米浆料剪切力的影响,发现在不同剪切应变速率、相同温度下,焊点表现出相同特点的剪切应力曲线,当应变速率越高时,应变硬化越明显,随着温度的升高,这种趋势愈加明显。清华大学 ZHAO 等 [67] 采用 Ag 纳米浆料键合 SiC芯片和 Cu 基板,研究在高温(350 ℃)存储时焊点中孔隙的变化,一开始出现 1~2 μm 任意形状的孔隙,当进行高温存储后,当存储时间小于 400 h,一些孔隙会缩小消失,存储时间大于 400 h,一些大的孔隙在增长,靠近 SiC 芯片附近的孔隙增长,而靠近基板附近的却降低。清华大学 ZHANG 等 [68] 同样采用 Ag 纳米浆料键合SiC 芯片和 Cu 基板,之后进行高温(350 ℃)存储,发现
样品在存储 200 h 后剪切强度有所增大,观察组织发现孔隙在减少,说明前期的存储会减少孔隙,使得键合更致密;继续存储,从 200 h 至 1500 h,剪切强度一直下降,这与孔隙率一直增大有关。
5 结论
目前纳米浆料的研究已经取得了长足的进展,但是我国在纳米浆料的大规模生产和高可靠应用方面还有很长的路要走。尤其是在当今国际形势下,实现电子材料国产可替代已经势在必行。在纳米浆料制备方面,不仅需要考虑成本问题,还需要考虑形貌尺寸的可控制备,以及烧结过程中的温度和压力要求,开发高质量烧结技术成为目前急需解决的问题。另外,在高可靠应用方面,不仅需要解决烧结过程中的致密性问题、多级互连过程中的温度控制问题,还需要解决多能量场作用下及极限环境服役过程中的电迁移及性能退化问题,因此需要加强对纳米浆料烧结接头可靠性方面系统和深入的研究,以便实现在大功率芯片封装、射频器件封装以及系统级封装等更多领域的高可靠应用。