企业是推动国家发展的主要载体,而企业管理是企业发展的核心要素[1]。近年来,企业根据高质量发展需求大力推行精益化管理模式,构建了特大型现代钢铁企业精益化管理体系,实现了对企业生产的质量、效益、人才等核心要素的全面管控,有效提升了企业的生产效率和运营质量。本文展示了以实战探索出的一套以“精益为基、品质为线、经济为果”的精益化钢铁企业管理模式,全过程突出“成本、效率、品质”特性,提升钢铁企业管理思维、方法和工具的时代性、价值性、重生力和应用力。
1. 企业管理的深度作用和变革急迫1.1 对于国民经济发展的作用企业管理对于国民经济发展的稳定起着至关重要的作用。一个高效、透明、公正的企业管理体系能够有效地减少内部腐败和权力滥用,提高资源配置的效率和公平性,为经济的快速发展提供坚实的基础[2]。通过科学的管理理念和方法,企业可以更好地规划和实施各项经营活动,提高生产效率和产品质量,增强市场竞争力。这样,企业能够更好地满足市场需求,为国民经济稳定发展提供有力支持。
1.2 对于企业持续发展和高质量生存的作用企业管理对于企业的持续发展和高质量生存起着关键作用。企业管理是对企业的各个方面进行计划、组织、领导和控制,以实现企业目标的过程[3]。企业管理能够提高企业的效率和生产力,即通过合理的规划和组织,促使企业的各个部门和员工更加协同地工作,减少浪费和重复劳动,提高生产效率和质量。企业管理能够提高企业的利润和竞争力,即通过有效的成本控制和质量管理,降低成本,提高产品质量和市场占有率,从而获得更高的利润和竞争优势。企业管理能够促进企业的可持续发展,即通过对企业资源的合理配置和环境保护的重视,保证企业的长期发展和可持续性。精益化管理的核心是以最少的资金、人力和时间等资源投入,创造出更高的价值,推动企业高质量可持续发展。
1.3 对于钢铁企业涅槃重生的作用企业管理对于钢铁企业涅槃重生起到决定性作用。近年来,受国内疫情和国际形势的影响,钢铁行业基本处于盈亏边缘,钢铁市场需求增速放缓,钢铁行业生存能力受到了严峻挑战。资源合理使用将是所有钢铁企业生存与发展的最后法宝,成为了“压死骆驼的最后稻草”。追其根本原因是企业管理的思维、方法及工具落后于企业发展的需求,无法激发企业活力、动力,因此,企业资源的有效管理将是改革的核心工作[4−5],也是钢铁企业推动发展的基础工作。
2. 钢铁企业精益化管理可行路线目前钢铁行业整体处于发展低谷,如何通过企业精益化管理提升企业的盈利水平和竞争力尤为迫切。随着钢铁行业的发展,国内重点钢铁企业的产品逐步迈向多样化,下游客户包括建筑、汽车、家电、机械等行业,不同客户对产品质量提出了不同的要求,为满足客户的个性化需要,要求钢铁企业进行产品类型的精益化管理。随着国家产业政策的不断调整,钢铁行业逐渐由增量发展转变为存量优化,致使企业需要通过精益化管理对现有资源进行优化配置,实现降本增效和竞争力提升[3]。本文以鞍钢股份有限公司鲅鱼圈钢铁分公司(简称分公司)精益实践为例,通过挖掘精益化管理对企业经营管理的促进作用,探索出具有精益化属性的企业经营新模式,最终形成以精益推动钢铁企业管理升级的最佳可行路线,进而实现“以思想引领模式,以模式推动发展”的管理创新变革。
2.1 精益化管理对钢铁企业的根本意义从2008年至今,在助力鞍山钢铁经济效益显著增长的同时,分公司自身的管理方法逐步出现发展劣势。主要表现为六个方面,一是工作机制逐渐不利于激发职工活力;二是生产制造资源逐渐不助力效益增长;三是作业流程逐渐不促进效率提升;四是设备功能逐渐不保障生产稳定;五是班组经营效益逐渐不加速企业发展;六是企业现代治理逐渐不利于企业开拓创新。剖析精益化管理,追其根本含义就是“凡事做精,万行为省”,即用最少的成本投入,为企业创造最大的经济利益,最终实现企业的长久发展。基于此,精益理念与企业发展是一一对应的,精益化管理具备解决上述六个根本问题的能力,进而推动分公司经营能力再次实现质的飞跃。
2.2 精益化管理在钢铁企业中的基本融点以“效率、效益”为原则,“抓经营本质,行发展方法”这是精益化管理融于钢铁企业的基本思路[6−7]。即以精益把控钢铁企业两大核心(“以精益管好人”与“以精益管好事”)要素,从里自外,从深入浅推动精益与钢铁企业的经营理念、管理体制、工作机制融合,并按“夯基础、增品质、提效益”三步环节,逐步促进钢铁企业管理理念、方法、工具演变为精益化管理理念、方法、工具,最终形成精益化管理为根基的新企业经营新模式。
2.2.1 管好人管好人主要表现在提升职工企业责任。钢铁生产工序多、流程长,是典型的人员密集型产业,大型钢铁联合企业工人数量众多、管理层级多,如果没有统一的思想和认知,将难以高效率开展各项工作。企业管理中“管好人”的根本目标是“提升职工的创造能力,推动企业发展创造最大的效益”。在生产过程中实现“管好人”的具体方式主要有两个提升。一是提升思想,即将职工生存思想与企业发展理念捆绑在一起,打造“企业兴、职工安,企业甩、职工危”的企业、职工生存共同体。二是提升能力,将职工收入高度与企业效益额度捆绑在一起,形成“企业丰、职工收,企业贫、职工穷”的企业、职工利益共同体。
2.2.2 管好事管好事主要表现在提高企业经营品质。我国钢铁企业多为长流程钢企,具有工序链条长、产线数量多、部门设置复杂和管理难度大的问题,做好企业发展战略规划,建立健全企业制度体系,通过将精益化管理的各项措施嵌套到企业的制度体系中,依靠强制性义务的约束和保障性权利的激励,确保精益化管理的落地见效。企业管理中“管好事”的根本目标是“提升职工的行为质量,建立企业效益创造最短的时间”。在生产过程中实现“管好事”的具体方法主要有三个规范。一是规范操作,即精简操作动作、标注操作数值,实现操作价值提升;二是规范流程,即消除业务冗余、优化流程环节,实现流程价值提升;三是规范管理,即改善体系架构、调整管理方式,实现管理价值提升。
3. 全面推进钢铁企业精益化管理具体实施流程长、工序多是特大型钢铁联合企业的共同特点,在给企业管理工作带来挑战的同时,也是企业实施精益化管理深入挖掘各工序价值的潜力所在,做好不同工序精益管理工作能够为企业带来客观的效益。以分公司为实践对象,锚定企业核心,应用精益思维贯穿钢铁企业管理运营始终,有效构建出具有可行性、价值性、实用性的管理理念、方法、工具,有效推动钢铁企业中的企业管理从传统化向精益化升级。
3.1 构建精益化管理体系,全面打牢管理升级基础聚焦企业构成核心要素(人、财、物),结合企业实际情况着重从组织、专业、资源三个方面实施分解定位,最终构建出具有企业特色的精益化管理的体系架构。如图1,按照分公司“效率一流、品牌一流和生态一流”的发展路径,结合优秀钢铁企业竞争力分析,构建运营效率能力、组织运转能力、人力经营能力、市场竞争能力、科技创新能力及和谐发展能力六个维度,对应盈利水平、资产效率、机构职能、智能管理、人员效率、企业文化等12个关键要素的规划指标框架。同时,为实现规划横向的高效协同和纵向的上下贯通,对照规划指标框架编制形成了13个分公司层面分解规划和8个事业部层面的支撑子规划,最终有效保证规划精准落地。
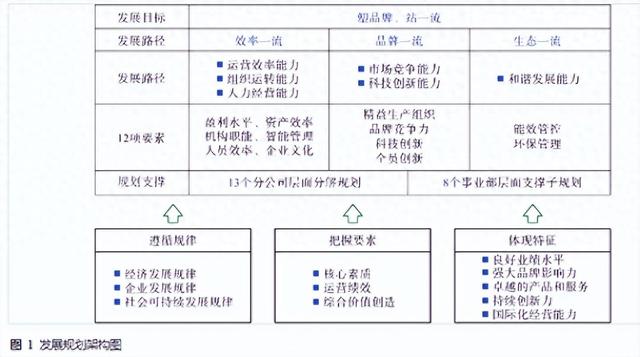
将组织效能与资源价值有机结合,即从原有的“管理扁平化、专业集中化、运行一体化”的市场化组织模式拓展到“设计价值、实施价值、落实价值”的精益化组织边界[8]。其中,以精益理念为依据,重组管理资源构建组织机构,明确各专业中的精益管理重点职责、工作要素及行为标准;构建精益化的经营绩效、组织绩效、岗位绩效评价体系,以实际数据标定效益高度、评价数值、评价范围;制定精益化的工作机制,明确各专业精益管理工作内容、行为路线及作业流程。
3.1.2 专业变革确定精益思维、方法、工具与各专业工作的融合点,并将其作为推进精益化管理的专属工作,进而实现精益化管理的有序运行[9−10]。例如,以周期、品质为精益化生产的专属工作,围绕产品制造,将所有操作行为从规范性,提升到价值性;以精准、稳定为精益化设备的专属工作,围绕设备监测,将点检、维修、预防实施一体化提升,确保对生产效率及产品质量的有效保障。
3.1.3 资源变革从资源与市场、资源与企业两个联动实施精益化升级,通过畅通资源价值多维度的提升渠道,推进从“资源专用→废物处置”的两级管理向“资源专用→价值再造→销售盈利”的三维管理迈进。例如,工业耐火材料,其材料符合冶炼需求,将剩余废物材料改造为其它需求材料,其从“花钱处理生产废物”转变为“改造价值销售盈利”,最终达到了价值资源零出厂。
3.2 精益化管理具体方法连接企业核心要素、对接各专业工作实际,构建“现场、生产、设备、成本、班组”五个具体方位及五个实效方法,全面践行精益落地,有效推动精益化管理显形见效。
3.2.1 精益微模构建“精益微模”工作方法,提升现场管理。脏、乱、差的现场工作环境会直接降低职工的工作热情和工作效率,导致企业价值创造能力下滑[11]。针对钢铁区域广、设备多而大、改善资源调配困难等问题,选取条件好、改善点多的微观区域(或生产平台、设备群体)作为模型,并根据模型特点有针对性、有重点的导入目视化和红牌作战等精益工具,聚拢资源全力打造具有高度安全性、舒适性的工作现场。
建立以排查、立标、导入、立案、实施、验证为环节的现场改善工作流程:确定微模对象及改善目标,并在现有的基础上完善形成《现场改善方案及标准》;由各专业人员建立改善团队、明确分工,按方案实施改善;以区域工作人员为评价人,从标准和体验两个方面进行改善效果评估;提炼精益现场成果,固化为常态化工作方法。另外,结合改善成本和难度,按不投入、少投入、有价值投入、战略投入顺序确定方案,杜绝精益本身造成资源浪费。
3.2.2 三维编织构建“三维编织”工作方法,提升生产管理。生产效率和工序成本是企业经营根本。针对“钢铁制造是连续性、大循环生产形式,流程环环相扣,任何一个节点干预都会影响整体效益”的情况,建立精益点(指标)、精益线(流程)和精益面(区域)的立体工作模式,重点导入项目、价值分析等精益工具,对现有短板、管理工具和生产方法实施优化提升,全力打造一条节拍紧凑、作业标准、产品高质的生产流程。
精益点(指标),即利用三级对标(自身、内部、行业)确定现有缺陷或短板,导入创新项目精益工具,按照“二八”原则分析主因,并制定措施实施攻关改善。其中,立项要有针对性,能够切实弥补缺陷、提升短板;对项目成果要标准验证,公式要数值化;提炼项目中的动作行为,形成常态化作业行为。
3.2.3 突击立标构建“突击立标”工作方法,提升设备管理。设备是企业生产最有力的支撑,是影响生产制造与服务质量的重要因素[12]。针对“设备密封无法探测内部、故障无规律无法定期维修、区域覆盖广但作业活动相近或相同”等特点,分公司充分考虑正常与异常两种状态,有效抓住机遇搞突击、抓住实体打攻关,将计划变为现实,将预期变为实际,有序优化设备自主保全机制。即在正常下,抓住关键设备,利用EMBP(Event management best practice)等精益管理工具,提升点检精准;在异常中,提前谋划,集中资源,利用检修或停机时间开展精益6S工作。
对于正常状态,与生产区域联动,选取设备单体或群体实施设备行为改善、目视优化,构建点检标准与点检动作零距离模式(标准贴在设备本身),大幅度取消点检时间、降低点检技术难度、提升点检质量;对于异常状态,以作业计划为依据,与职能部门联动,掌握近期生产动态,提前做好设备改善方案,从时间、空间上抓住检修、抢修、改造等便于改善的时机,有效将方案变为成果。
3.2.4 减耗增值构建“减耗增值”工作方法,提升成本管理。资源是企业生产和生存的根本,成本控制将是企业一项持久性工作[13]。针对“企业各个作业活动均有资源浪费”的状态,分公司以“一切皆可降”的意识,融合各专业精益管理工作与精益创新项目等内容,采取“全力压低消耗的底线,竭力抬高价值的顶值”的方法,彻底消除没有价值的资源消耗或赋予产品新的价值高度。
一方面利用创新项目、价值分析等精益工具,以项目或专业精益管理的方式降低资源消耗,与生产、设备、现场融合,借其改善完成降本;另一方面回收资源,改造为新产品或新原料,并通过自主销售和回收利用方式实现二次创效,既激发职工自主意识,提升自身技能,又通过改造、修补、回收等方式减少废物排放,实现价值再生。另外,建立效益验证公式,剔除精益本身的资源投入,精准评价精益降本额度。
3.2.5 微观多元构建“微观多元”工作方法,提升班组管理。班组是企业最基础的经营主体,是企业所有效益、文化的育成源地。针对“企业班组权利丢失、活力停滞、责任低迷”的表象,分公司借用目视看板等精益工具,全面推动班组向技能型、创新型、质量型、效益型、和谐型方向健康发展,真正将班组打造为最基础、最核心的创效、管理、成本微观单元。开启微观经营时代,增添鞍钢宪法新内涵,具有变革性、典范性。
从身份、权限、业务上实施精益化管理,一是“逆流管理”,建立责任清单,利用改革纵深授权,将安全、生产、质量、人员、设备、成本、环境等七大权限中的部分权限从专业科室下移至班组,分别将指令输出、成绩评价的管理端、专业端转换为生产端,真正做到“办公椅搬到现场,指挥棒放到一线”,实现“被你”管理到“自己”管理的转变;二是“流程再造”,建立工作清单,以“提效、减量”的原则,通过建立看板、改善行为、优化操作等方式有效降低劳动负荷,将班组长从生产旋涡转移到管理平台,充分调动一线职工积极参加企业经营管理。
4. 钢铁企业精益化管理变革成效经过在分公司全范围的践行,有效提升分公司企业管理基础水平,从效益、品质、效能三个方面助力分公司经营进一步提高。
4.1 经济效益显著增长经分公司财务部门组织评审,输出了《精益化管理对企业经济效益增长的统计报告》,给出了“2021年至2022年,精益化管理确实对分公司盈利贡献了巨大推力,并建议持续运行”的认定。两年累计实现降本增效2.01亿元,有效助力了2021年经营利润取得历史新高。2022年,面临国内外严峻的市场环境依然保持盈利,最终达到6.5亿元。分公司建立了《电力最大需量精益化控制方案》,全年实现降本757.6万元,助力吨钢系统降本达到133元;建立了《粗苯工艺精益模型》,粗苯收率提高7%,直接经济效益310余万元。建立了《常规产品精益工艺流程模式》,精简了4个钢种的生产工艺流程,工序吨钢成本降低42元。另外,建立了《精益化人力资源分流使用方案》,核减岗位人员453人,全员实物劳动生产率提升15%。
4.2 经营品质持续提升经分公司专业职能部门联合认证,分别输出了《专业精益化运行品质提升的验证报告》,得出了“2021年至2022年,实施精益化专业管理,切实提升了专业在‘行为、流程、工艺’等方面的能力提升,有效发挥了专业质量对企业发展支撑作用”的结论。其中,提升生产、设备、成本等各专业指标126项,完善各类标准68个,修订工作制度5项,优化作业行为410个。对标自身、企业及行业,各类生产指标达到历史最好水平34项、达到鞍钢集团同级单位最好水平41项、达到行业领先水平51项。设备检修中心系统优化检修流程,实现检修时间准确率95%以上,检修质量合格率达到99.82%;热轧部打造产品质量高端化,优化硅钢凸度控制方法,质量合格率从91.4%提升到96.4%,实现单项创效120余万元;质检计量中心板材实验室实施精益化布局设计、装备自动化升级、参量数字化变革、流程信息化再造、系统智能化管控,压缩制样时间15 min(原制样时间40 min,提升效率62.5%),提升作业量60%、精准率50%、开坯能力50%,降低成本损耗3%、工作负荷80%。
4.3 管理模式全面推广通过两年的精益化管理实践,分公司构建了以制度、组织、机制、推广、评价为基础,以提升效率、效益为中心的全面精益化管理,真正将精益化管理工作从“点式运行”转变为“体式运营”,实现了精益化管理工作标准化、持续化、常态化。在全国钢铁行业内,率先系统性践行了沿海钢铁基地精益化管理工作模式,并被鞍山钢铁集团有限公司其他单位广泛学习,被本钢集团有限公司借鉴运用。另外,鲅鱼圈钢铁公司的全面精益化管理模式被中国冶金报5次报道,并荣获2023年度辽宁省企业管理现代化创新成果一等奖,2023年度冶金行业、国家级企业管理现代化创新成果二等奖。
5. 结束语将精益化管理的理念运用到企业管理当中,不仅给企业带来新的发展和变化,更是持续落实治企安邦的有效方法。但在施行精益化管理的过程中,也要求管理者清楚精益化管理的内核和概念。从而正确地将精益化管理理念融入进企业管理当中,使得企业运转体系更为合理,工作人员的效率更高,而不是让精益化管理浮于表面,显于形式。总之,以精益推动企业管理变革,是促进企业管理水平有质增长的必经途径,是构建现代特色企业管理不可缺少的重要环节。
文章来源——金属世界