天然气集气站的主要功能是从多个气井中收集天然气,通过一系列的处理过程,如加热、节流(减压)、分离(去除杂质)、增压、脱水(去除水分)和计量等,以确保气体达到规定的压力和温度标准。经过这些步骤处理过的天然气可以被输送至下游的天然气加工厂或者直接输入城市供气网络,以满足工业和居民用气的需求。由于经常使用焊接工艺对天然气集气站外输汇管进行管道连接,而焊接是一个不均匀的加热过程,故在焊缝和热影响区容易发生组织不均匀、力学性能不均匀等现象,并产生焊接缺陷。
集气站外输汇管的焊接接头部位具有较高的焊接残余应力,因此该管道很容易发生事故。研究表明,大口径管道的所有事故中由焊缝缺陷导致的故障占比为70%[1]。某气田集气站外输汇管的材料为SA234 WPB,规格为1 000 mm×40 mm(公称直径×壁厚),设计温度为60 ℃,操作温度为40 ℃,设计压力为9.5 MPa,操作压力为8.5 MPa,介质为酸性天然气,酸性天然气中含有体积分数为8%~9%的CO2和13%~15%的H2S。该管道在投入运行仅1个月后就发生泄漏现象。笔者采用宏观观察、化学成分分析、渗透检测、力学性能测试、金相检验、扫描电镜(SEM)和能谱分析等方法分析管道泄漏的原因,以避免该类问题再次发生。
1. 理化检验1.1 宏观观察现场检查发现,汇管外表面防腐层完好,无明显壁厚减薄和局部腐蚀痕迹。截取的泄漏管段宏观形貌如图1所示。由图1可知:管道内表面防腐层局部脱落,脱落区域呈层片状和鼓泡状形貌;焊缝内、外表面成形较好,无明显内凹、缺失等表面缺陷;但纵焊缝上有多条表面横向裂纹,有两条横向裂纹贯穿纵焊缝。纵焊缝上贯穿横向裂纹宏观形貌如图2所示。
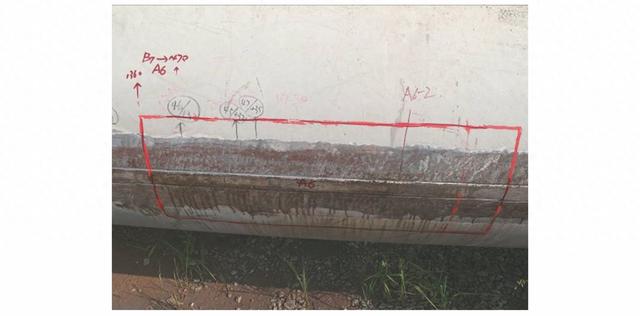
图 1 泄漏管段宏观形貌
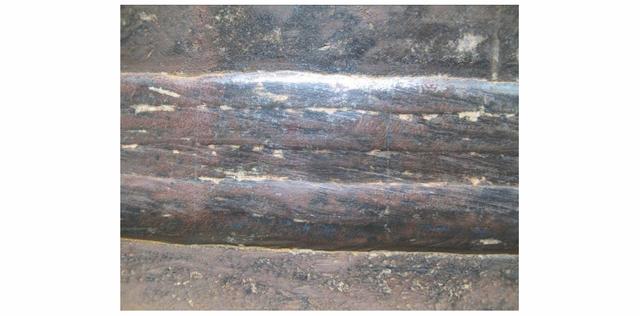
图 2 纵焊缝上贯穿横向裂纹宏观形貌
1.2 渗透检测依据NB/T 47013.5—2015 《承压设备无损检测 第5部分:渗透检测》的要求,利用渗透剂、乳化剂、清洗剂和显像剂对汇管进行渗透检测,结果如图3所示。由图3可知:汇管表面存在多条横向裂纹,裂纹较平直,无明显塑性变形,断口呈脆性断裂特征。
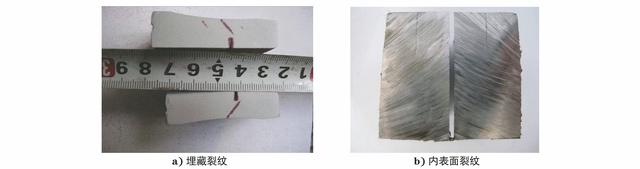
图 3 焊缝渗透检测结果
1.3 化学成分分析根据GB/T 4336—2016 《碳素钢和低合金钢 多元素含量的测定 火花放电原子发射光谱法(常规法)》,分别对汇管母材和焊缝进行化学成分分析,结果如表1所示。由表1可知:母材的化学成分符合技术要求。焊缝化学成分中的Mn元素含量超出了要求,同时焊缝中的Si元素含量要大于母材。
Table 1. 汇管母材和焊缝的化学成分分析结果
项目
质量分数
C
Si
Mn
P
S
Ni
Cr
Cu
母材实测值
0.19
0.27
1.06
0.011
0.014
0.005
0.02
0.01
焊缝内层实测值
0.06
0.65
1.82
0.025
0.011
0.06
0.03
0.23
焊缝外层实测值
0.11
0.53
1.65
0.021
0.008
0.05
0.03
0.17
技术要求
≤0.30
≥0.10
0.29~1.06
≤0.050
≤0.058
≤0.40
≤0.40
≤0.40
随着Mn元素含量的增大,材料的热导率急剧减小,线膨胀系数增大,在快速加热或冷却时,材料内部形成较大的内应力,开裂倾向性增大,淬透性增强,马氏体转变温度降低,对焊接性能有不利影响;同时Mn元素可以细化珠光体,使钢材的强度增大,延展性降低[2]。而Si元素含量的增大会降低钢材的塑性和冲击韧性,减弱钢材的抗锈蚀能力和焊接性能[3]。
1.4 力学性能测试按GB/T 228.1—2021 《金属材料 拉伸试验 第1部分:室温试验方法》和GB/T 229—2020 《金属材料 夏比摆锤冲击试验方法》的要求,对泄漏汇管进行拉伸试验和冲击试验,结果如表2所示。由表2可知:汇管母材的力学性能符合相关要求,焊缝的抗拉强度超出了相关要求的上限,母材的冲击吸收能量高于焊缝。
Table 2. 汇管的拉伸和冲击试验结果
项目
抗拉强度/MPa
屈服强度/MPa
断面收缩率/%
冲击吸收能量/J
母材实测值
522
365
26.5
180.0,212.0,244.0
焊缝实测值
660
—
—
130.0,162.0,165.0
标准值
415~585
≥240
≥17
—
根据GB/T 231.1—2018 《金属材料 布氏硬度试验 第1部分:试验方法》对泄漏汇管的硬度进行测试,结果如表3所示。由表3可知:焊缝的硬度超出了规定的上限,同时焊缝和热影响区的硬度高于母材。
Table 3. 汇管的硬度测试结果
项目
硬度
母材实测值
159,156,156
焊缝实测值
216,213,211
热影响区实测值
187,184,187
标准值
≤197
Mn、Si元素含量的增大会影响材料的力学性能,使其抗拉强度和硬度增大,冲击韧性降低,跟化学成分分析结果相对应,硬度与材料的应力有密切关系,通常应力越大,硬度越高,可间接反映该汇管焊缝以及热影响区存在应力集中的现象。
1.5 金相检验分别在母材、热影响区及焊缝的位置截取试样,将试样置于光学显微镜下观察,结果如图4所示。由图4可知:母材的显微组织为铁素体+珠光体,其中珠光体含量少,且沿铁素体晶界分布,组织细小,具有较高的强度和塑性;热影响区的显微组织为板条状马氏体、针状铁素体和贝氏体的混合组织,晶粒较为粗大;焊缝的组织为块状铁素体、先共析铁素体和珠光体的混合组织,相对于母材,焊缝局部组织比较粗大。焊缝和热影响区的局部组织粗大并存在板条状马氏体,为裂纹的形成和扩展提供了条件。
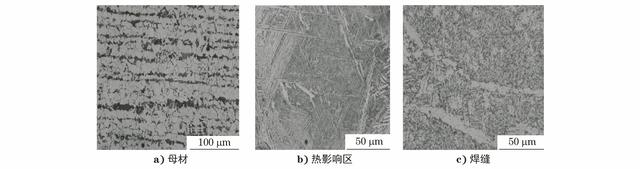
图 4 汇管的显微组织形
根据裂纹分布形态,分别对表面裂纹及埋藏裂纹的微观形貌进行观察,结果如图5所示。由图5可知:裂纹在焊缝位置,分布范围较宽,裂纹由多裂源形成微裂纹串集,带枝杈和扩展台阶,呈沿晶和穿晶混合开裂形貌特征,表面裂纹内充满腐蚀产物,呈典型的延迟裂纹形态。
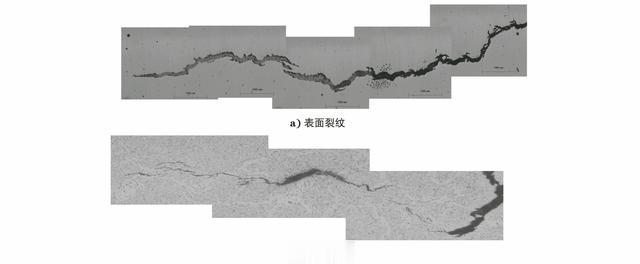
图 5 表面裂纹和埋藏裂纹微观形貌
1.6 扫描电镜和能谱分析分别沿着表面裂纹和埋藏裂纹打开管道,以裂纹面为检验面。表面裂纹和埋藏裂纹断面均有明显的方向性,呈柱状晶结晶形态,无明显塑性变形,无壁厚减薄,呈脆性断裂特征。表面裂纹横向贯穿焊缝,止裂于焊缝熔合区,断口较为平齐,无金属光泽,表面为黑色,清洗后表面为灰色并无光泽,断口表面覆盖一层致密的腐蚀产物。埋藏裂纹也为环向裂纹,位于焊缝中间,断口表面具有金属光泽,为银亮色。
在管道上埋藏裂纹处截取试样,将试样置于扫描电镜下观察,结果如图6所示。由图6可知:埋藏裂纹断口断面有河流花样,呈柱状晶结晶形态[见图6a)];在裂纹尖端及靠近内表面位置,断口呈多源启裂特征[见图6b)];启裂区有圆形和椭圆形银白色斑点,白色斑点附近没有塑性变形痕迹,圆斑区显示有从中心向四周的放射线结构,为准解理形貌,在断口上存在显微孔洞、发纹和二次裂纹,两个裂纹源的交界面存在撕裂棱,为韧窝断口,韧窝是由孔洞形核、长大和连接形成的,韧窝之间分布着大量细小的二次裂纹[见图6c)、6d)]。裂纹断口呈典型的氢脆微观断口形貌特征。
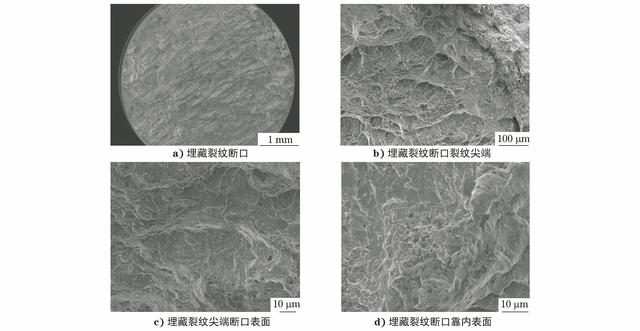
图 6 埋藏裂纹试样SEM形貌
对断口表面腐蚀产物进行能谱分析,结果如图7所示。由图7可知:断口表面含有氧、镁、硅、磷、硫、钙和铁等元素,其中硫元素含量较高,说明腐蚀产物为硫化物,腐蚀介质进入裂纹内部与金属反应,形成硫化物,附着在断口表面。
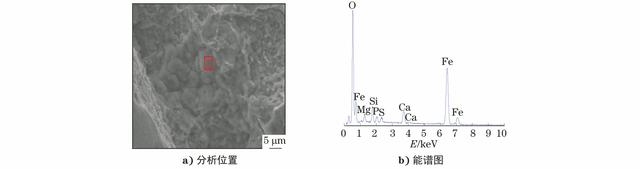
图 7 断口表面腐蚀产物能谱分析位置及能谱分析结果
2. 综合分析由上述理化检验结果可知:汇管母材的化学成分、力学性能和显微组织均符合相关要求;焊缝化学成分中Mn、Si元素含量偏高,导致焊缝处材料的拉伸性能和硬度大于母材,焊缝处显微组织为板条状马氏体,与硬度测试结果吻合;断口呈沿晶和穿晶混合开裂形貌特征,表面存在明显的鸡爪纹,具有氢脆断裂的典型特征。
氢脆是在焊接过程中,氢进入钢中的显微缺陷内[4],聚合成分子氢,当氢富集到足够的程度,会引起金属脆化、空腔表面能减小,以及空腔内压力增大,使显微缺陷扩张成裂口而形成裂纹源。由于氢的扩散,另一应力集中源形成新的裂口并扩展,两个裂纹源串集连成裂纹。这些裂纹源通常不能准确地首尾相接,所以常常带有枝叉,并且裂纹的扩展也是不连续的,由许多细小的微裂纹各自长大并连接。
氢脆的发生需要氢富集,由于汇管中介质为酸性天然气,其中有较高含量的H2S。同时在焊接过程中,高温电弧的作用将水分解成氢和氧。氢以离子状态存在,被液态金属大量吸收,随着焊缝金属的冷却,会析出氢,当冷却速率较大时,氢将以过饱和的形式存在于焊缝金属中。在焊缝金属中不可避免地存在大量晶体缺陷,如空穴、点阵空位、位错和非金属夹杂等,为氢离子的扩散和富集提供场所[5]。
焊接接头处于复杂的应力状态,是由热应力、组织转变应力与约束应力综合叠加构成的。在焊接条件下,局部快速的加热与冷却导致材料内部产生较大的温度场,引起不均匀的热应变,从而产生热应力[6]。同时,在热循环作用下,各区域的奥氏体化状态不同,引起不均匀的组织转变,各微区域不能相互协调膨胀,从而产生了相变应力。由于焊接接头的刚性约束,焊接接头金属冷却收缩受到限制,产生了约束应力。
焊缝金属快速冷却,使焊缝中形成马氏体和贝氏体,而马氏体和贝氏体对裂纹较为敏感[7]。
3. 结论与建议汇管泄漏的主要原因是焊接工艺不当,焊缝中的马氏体和贝氏体为焊缝开裂提供了条件。建议改进焊接工艺,用焊后热处理方式减小残余应力,或者在焊接前采取预热的方式将氢释放出来,也可在管道内部施加涂层、堆焊不锈钢或设置其他保护衬里,以防止该类问题再次发生。
文章来源——材料与测试网