随着氢能产业的快速发展,大规模制备绿氢的需求日益高涨,电解水制氢装备在新应用工况下面临的技术、安全、成本挑战也愈发突出。在此形势下,现阶段国内ALK、PEM、AEM三种技术路线的代表企业均在加码迭代优化产品技术,其中AEM制氢企业的“冲刺”尤为迅猛。
10月18日,清能股份在佛山氢能展上发布HET-A1000 5MW AEM电解水制氢系统,这是截至目前全球范围内功率最大的AEM制氢系统。该系统内部的AEM电解槽单槽功率达500kW,核心材料阴离子交换膜幅宽达80cm,均为清能股份自主研发制造,并创造了行业之最(此前公开消息显示,AEM单槽功率未超过100kW,阴离子交换膜幅宽多在40~60cm)。
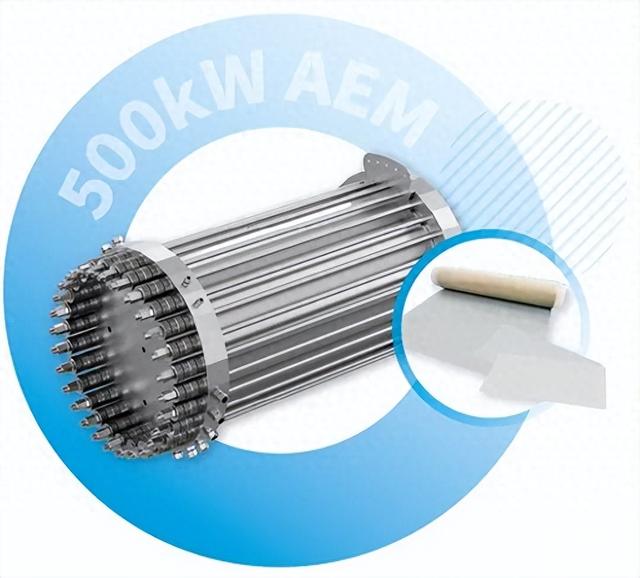
AEM比ALK拥有更快的响应速度、更高的电流密度,又因不含铂、铱等贵金属比PEM制造成本低,是结合ALK和PEM优点,在绿氢蓬勃发展当下被寄予厚望的第三代电解水制氢技术。不过,此前受制于阴离子交换膜技术成熟度低,制氢功率偏小、寿命稳定性有待提高,整个商业化推广进程不及ALK、PEM,尚未在国内大型绿氢项目中得到实际应用。
如今,清能股份推出5MW AEM制氢系统,同时引领着阴离子交换膜材料走向成熟,为AEM规模化进入大型集中式制氢市场创造了有利条件,让AEM制氢技术正以前有未有的速度加快商业化步伐。清能股份副总经理仇舯向高工氢电透露:“国内绿氢用户认可AEM制氢效率高、成本低的优势,我们已经有订单在沟通,预计明年上半年开始商业化验证。”
从膜开始,一步一个脚印地打磨技术
阴离子交换膜是AEM电解槽的核心组件,通常选用聚合物作为主要材料。在理想条件下,它能够配合非贵金属催化剂实现高电导率和大电流密度。但在实际运行中,阴离子交换膜易出现离子传导率较低和耐碱稳定性较弱等问题,进而影响AEM电解水设备的稳定性和系统寿命。
在国际市场上,小功率的AEM电解槽及由这些电解槽集成的1MW系统,是有出货及应用案例的,这在一定程度上证实了该技术路线在电解水制氢领域的商业可行性。而若要应用于新兴的大型制氢项目中,用小功率电解槽集成大系统,可能无法满足实际应用所需的性能要求,并可能导致成本高于预期、占地面积大,从而难以充分发挥AEM制氢装备天然具备的优势。
因此,AEM电解槽向大功率方向发展,阴离子交换膜幅宽就必须扩大,而这又面临很多深层次的技术挑战。在全球尚未攻破技术难关的形势下,将痛点视为机会的清能股份基于自身对核心材料微观层面的深度认知,率先从2021年开始投入大量时间精力与成本研发AEM膜,经历了多轮迭代优化,最终实现AEM膜的优秀化学及机械稳定性,能够适用于批量的商业化生产。
具体来看,基于独创的多层物理化学膜增强技术,清能股份AEM膜幅宽可达80cm,抗张强度高于65MPa,可达到其他同类产品的1.5~2倍强度,能够实现更高的耐压强度及氢氧侧气体阻隔能力;采用全饱和碳氢键树脂作为功能团基材,厚度50μm,具有优异的离子传导能力,实验室测试结果验证了同等条件下的性能、寿命均明显优于其他同类产品。
针对AEM电解槽的开发设计,清能股份将专有的AEM膜和催化剂与新颖的电极设计(采用全新开发的多孔传输层技术和高效耐用的阳极电极结构,具有高比表面积和优异的稳定性)相结合,大大提高了离子传导性和电催化效率。
最新测试结果显示,清能股份新型AEM电解槽在现有电耗基准下降低10~20%耗电量可行,具有灵活的动态响应能力,能够匹配可再生能源制氢。
“从阴离子交换膜,到催化剂、电极及电解槽设计,从小尺寸到大尺寸一步一步地做迭代优化,同步展开生产工艺的量产摸索,在整个过程中,团队付出了艰辛努力。”仇舯透露。清能股份的核心技术研发团队自2005年加入公司,具备从最核心材料开始研发设计电解产品的能力。在清能科学家的带领下,研发团队攻克了大尺寸阴离子交换膜及大功率电解槽的诸多技术难点,才有了这款在全球范围内具有革新意义的5MW AEM制氢系统,将AEM制氢技术推升一个新高度。
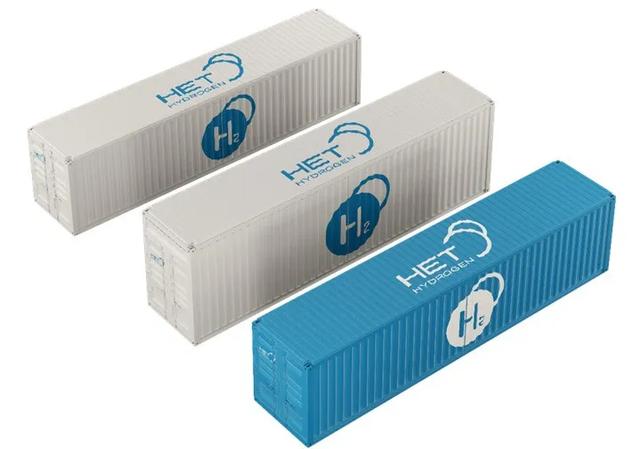
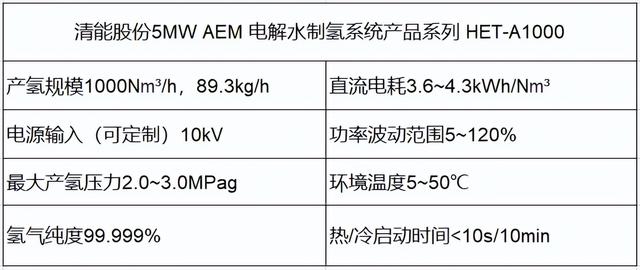
注:由于设计或制造上的必要,规格可能会有变化
清能股份5MW AEM制氢系统采用模块化设计,集成于三个40英尺集装箱,拥有便于运输、安装的优势;还可通过部署多个5MW模块化产品,扩展集成超百兆瓦级电解制氢系统,以满足更大规模的工业级绿氢需求。此外,因采用低成本、储量丰富的镍和铁材料,并具备一体化成本控制优势,其还可提供最具成本竞争力的电解槽和系统维护方案,支持设备运行超20年。
战略预判,用技术撬动商业化市场
提及清能股份,熟悉燃料电池领域的人士必定都知晓。公司成立于2003年,至今已有21年的发展历史,在国内外燃料电池市场都占有一席之地,是不折不扣的燃料电池老兵+商业化引领者。它在电解水制氢装备领域的资历也很深厚,早在2009年就开始研发PEM纯水电解装置,至今PEM电解水制氢产品累计出售5000多台,覆盖全球80多个国家。
当初清能股份为何从燃料电池延伸布局电解装置?公司在PEM电解水制氢领域有很深的研究及获得不错的产品销量后,又为何花大力气布局AEM制氢?
“我们做产品开发,都是从客户需求出发,以及我们对行业发展趋势及未来市场的判断。”仇舯表示,“当初有很多燃料电池客户向我们询问氢气获取问题,我们也深深意识到氢气来源需要重点关注,于是从小型PEM电解装置着手,逐步也推出了200标方工业级PEM电解槽。在近几年全球绿氢产业兴起的形势下,成熟的工业级PEM电解产品,配合可再生能源电力制氢,在当前有巨大的应用潜力,海外目前部署的PEM电解槽占比达到40~50%。同时我们判断AEM制氢技术更有助于未来绿电制绿氢低成本规模化发展,所以提前展开了技术攻关。”
在绿氢产业发展初期,项目实际运行以并网型为主,可以稳定提供电力,采用传统的、低成本ALK可以满足需求。由于并网电价较高,制氢经济性不强,同时也不符合绿色发展方向,离网型制氢项目将日趋增多,对电解槽灵活响应能力、电流密度要求也越来越高。ALK在顺应形势做技术迭代,但1000+标方产品还在项目验证当中。
PEM电解槽相比ALK,拥有启动时间短、响应速度快、能够与可再生能源耦合等优势,在国内绿氢项目中已经有一定比例的应用,但200+标方产品性能也需经历长久测试和验证。业界对于PEM电解槽最大忧心在于,未来一旦上量,贵金属会成为制约其大规模落地的瓶颈。
可以看到,虽然每种技术路线都在针对大规模制氢需求加快技术迭代,但大标方产品都缺乏相应的验证数据,大功率AEM制氢系统后来居上是有机会的。
经过谨慎判断多种电解水制氢技术路线发展趋势,也结合绿氢产业当下及未来发展需求,清能股份既推出了工业级PEM电解槽,也将战略目光瞄向结合ALK低成本、PEM耦合可再生能源性能更佳两种优势的AEM制氢技术,并用实际行动攻克了技术难关。
此次清能股份5MW AEM制氢系统正是AEM制氢技术革新的力证,将进一步助推绿电制氢规模化、商业化发展。“由于AEM制氢效率高于碱性,目前采用AEM系统的制氢成本已经可与碱性制氢成本直接竞争。随着未来3-5年批量化推广后,AEM系统购置成本可与碱性直接竞争,而AEM制氢成本也将显著低于碱性制氢。”仇舯预计。