【化工科技装备大发展】系列-820
这是一个记录石油化工装备发展历史和取得成就的有趣系列合集
欢迎大家分享点评讨论交流,
回顾历史
分享成就
展望未来
为化工装备现代化鼓劲加油
------------------------------------
B型LNG燃料舱LNG(液化天然气)是一种清洁、高效、安全的能源,是未来能源结构的重要组成部分。LNG双燃料集装箱船是一种利用LNG作为主要燃料的船舶,具有节能减排、降低运营成本、符合国际环保要求等优点。LNG双燃料集装箱船的核心设备是LNG燃料舱,它负责储存和输送LNG燃料,保证船舶的正常运行。
目前,世界上主要有三种类型的LNG燃料舱,分别是A型、B型和C型。其中,B型燃料舱是一种自支撑的球形或椭球形的压力容器,具有容量利用率高、建造更灵活、安全性能好等特点。B型燃料舱的设计和建造是一项高技术难度的工程,对于提升中国造船业的技术水平和国际竞争力具有重要意义。
大连自主设计建造单舱世界最大13000立方米B型LNG燃料舱完工2024年1月10日,中国船舶大连造船装备公司建造的单舱世界最大13000立方米B型LNG燃料舱完工交付。标志着大连造船已完全具备B型舱自主研发设计和建造能力,大大提升大连造船在该领域的全球竞争力。
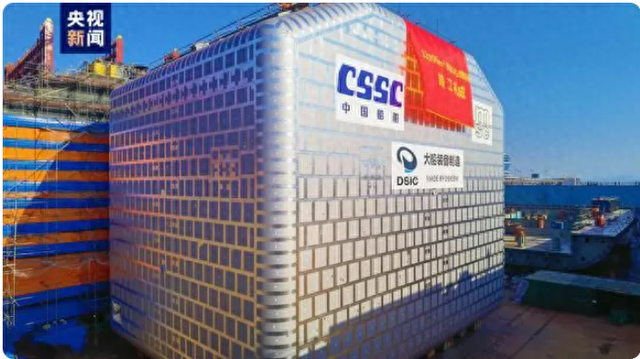
该B型LNG燃料舱是大连造船为地中海航运建造的LNG双燃料动力16000TEU集装箱船核心设备,每船配套一个独立B型舱,此次交付的是该系列船B型舱的首舱。
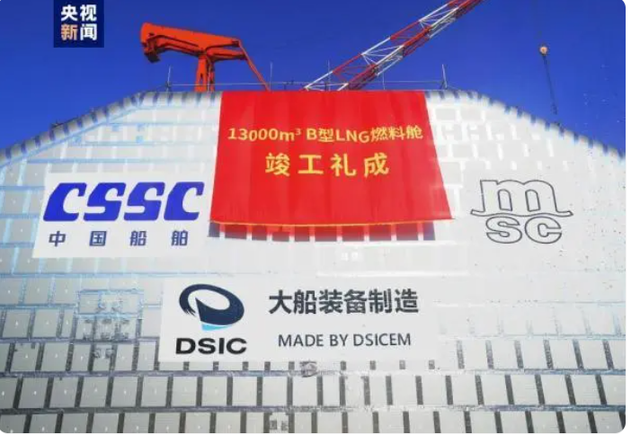
该舱由大连造船自主设计、自主建造,具有完全自主知识产权,舱容13000立方米,主体材料为NV9Ni/a钢,入DNV船级社,是大连造船在完成C型LNG储罐产业化后在LNG储舱建造关键技术上的又一重大突破,也是大连造船在船用LNG装备产业发展上的一个重要里程碑。
全球最大B型LNG燃料舱用上“河钢造”近日,中国船舶大连造船装备公司建造的单舱世界最大13000立方米B型LNG燃料舱完工交付。在该项目建设中,河钢集团舞钢公司5000余吨高端宽厚板用于燃料舱制造。
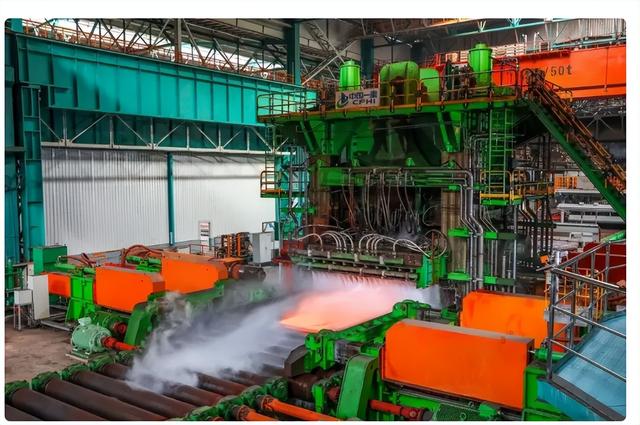
在对接客户需求过程中,舞钢针对“项目旨在树立新一代绿色环保船型的行业新标杆,对集装箱船用燃料仓制造用材料的选用十分严苛”的实际,充分发挥自身技术优势,在优化升级原有技术基础上,不断创新钢板工艺设计,为客户专业定制满足其差异化需求的特种钢板。保供过程中,舞钢严格钢板质量管控,优化生产流程,保障了产品焊接性、韧性良好,且实现了提前交付。经客户加工使用,产品不仅满足了项目超低温环境下的各项性能要求,还便于加工制造,获得客户高度认可。
建造历程2023年4月,大船重工建造的全球最大13000立方米LNG B型液货舱项目开工。
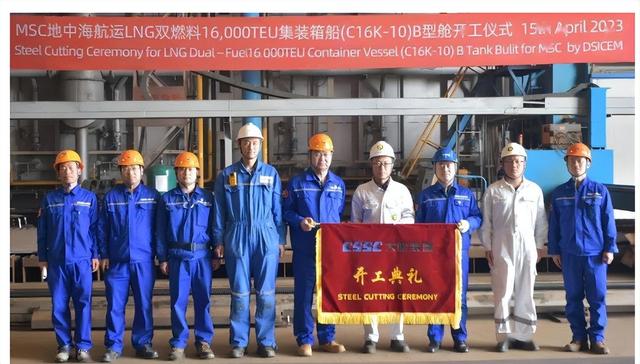
本次开工建造LNG B型舱是用于LNG双燃料16000TEU集装箱船系列船的船用B型液货舱,每船配套一台独立B型舱,该系列共计8台套。由大连造船设计院设计,具有完全自主知识产权,舱容13000立方米,设计温度-163°C,设计压力0.7Bar,主体壳体材料为NV9Ni/a钢,内部管路为316L钢,入DNV船级社。相较于传统C型罐,B型舱具有舱容利用率高、设计灵活多样等优点。
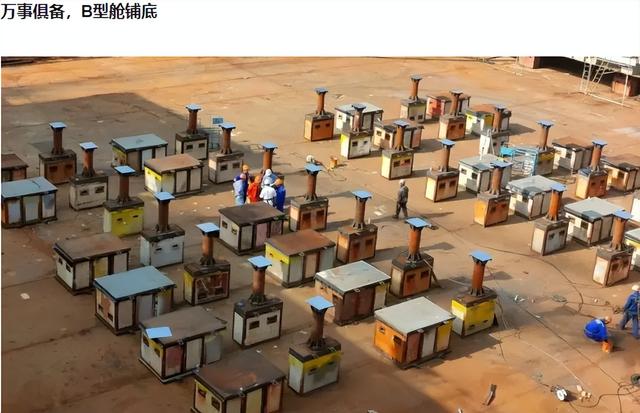
为建造13000立方米LNG B型液货舱,大船装备与设计院、生产管理部、项目组联合组建项目团队,依托大连造船强大生产力,结合大船装备现有场地布局,现已完成B型舱分段划分、合拢、内部舾装平台、管路系统布置等详细设计工作,攻克了关键节点的焊接工艺及分段合拢的精度控制程序等,确保了项目顺利进行。
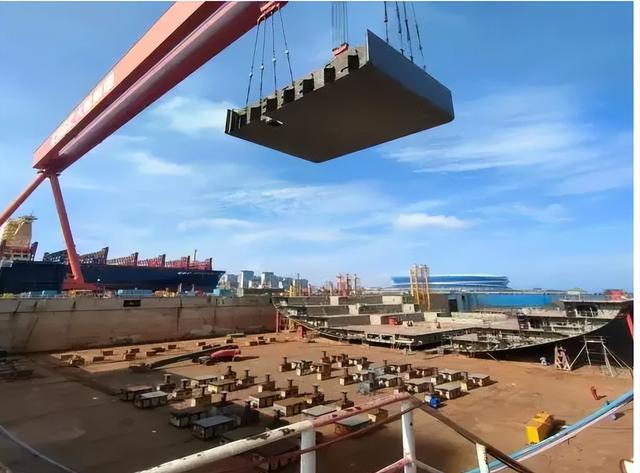
为确保首舱的成功建造,大船装备组建了一支素质过硬、敢于创新的B型舱专项技术攻关团队,先后组织完成了从下料、分段建造、总段合拢、压木安装、强度试验、绝缘安装、运输吊装等全流程策划书,编制作业工艺指导文件50余份。
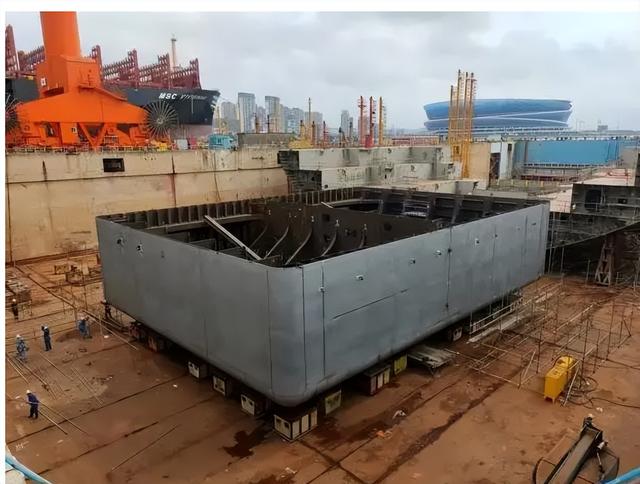
通过试板焊接、模拟构件加工、模拟舱建造等建造工艺攻关与技术验证,攻克了B型舱9Ni钢高效焊、精度控制、建造质量控制等一系列关键技术,完成焊接工艺评定86项,通过大量试验及实际建造验证,实现了国产化焊材在实际建造中的首次应用,打破国外9Ni焊材在中国市场的垄断地位,具有里程碑意义。
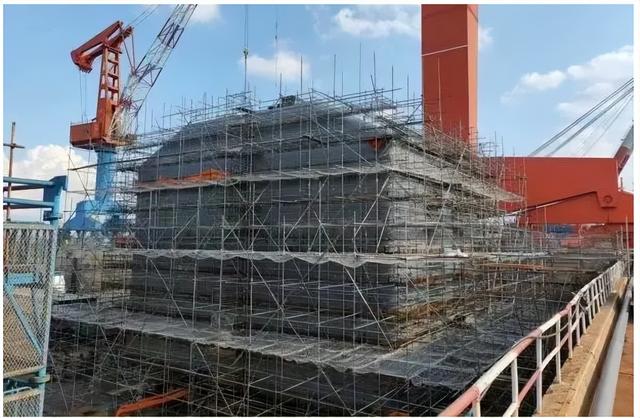
首个B型舱是在坞内建造,后期进行水压试验。
第一台全球最大B型LNG燃料舱采用3600吨大型海吊一次性安装到位2024年3月初,由大连造船自主设计的全球最大B型LNG燃料舱顺利吊运安装结束,本次吊装作业采用3600吨大型海吊一次性安装到位,全程实际用时约29小时,相比原定计划提前9.5小时完成全过程吊装作业。

该B型舱重量约为1150吨,长22米、宽29.24米、高28.55米,舱容为13000立方米,单舱世界最大。
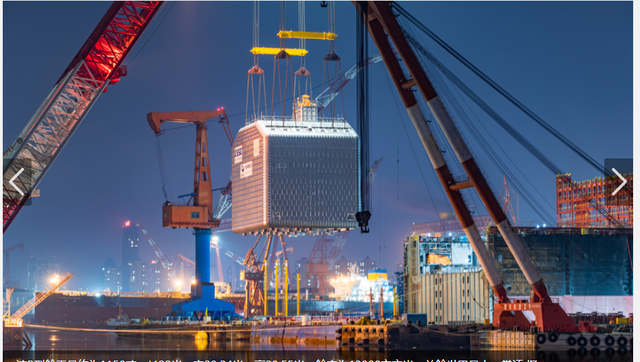
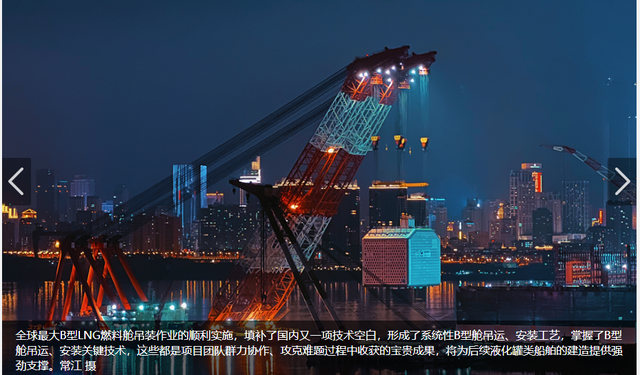
节省1000万,双车联吊安装全球最大B型LNG燃料舱
2024年5月底。由中国船舶大连造船自主设计的全球最大B型LNG燃料舱(以下简称“B型舱”)吊装作业在中船(天津)船舶制造有限公司(以下简称“中船天津”)顺利完成。本次吊装作业采用两台800吨大型龙门吊一次性安装到位。据了解,B型舱是燃料储存设备,用于储存超低温液态天然气(-163℃LNG)。本次全球最大B型舱采用双车联吊,在国内属首次。
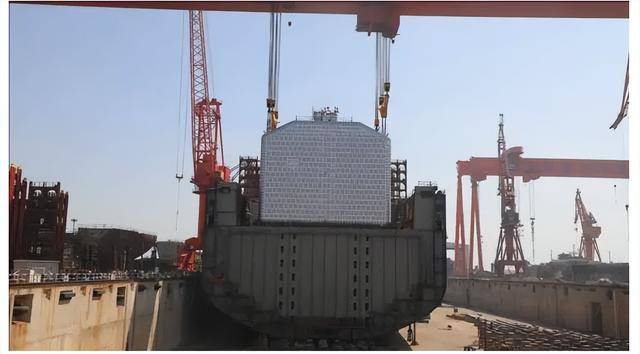
为确保吊装工作按期顺利完成,中船天津生产管理部项目组联合中国船舶大连造船设计院、设计部、总装制造部、质量安全部、生产保障部等部门成立专项项目团队,对B型舱采用两台800吨大型龙门吊抬吊方案开展多轮会议交流。自2024年1月起,项目团队联合开展多轮“四首四新”评审,对B型舱开展全面工艺技术论证和安全论证,在吊装作业前组织模拟吊重下吊杠平度检测、模拟吊重下双车联吊演练等,为全球最大B型舱的成功吊装奠定坚实基础。
本次双车联吊过程中,中船天津需要克服吊点位置紧张、两台800吨大型龙门吊需联吊状态进行大车行走、整体吊装重量要求极度精准等严峻挑战。为此,中船天津设计部整体设计了多达12份工艺方案。
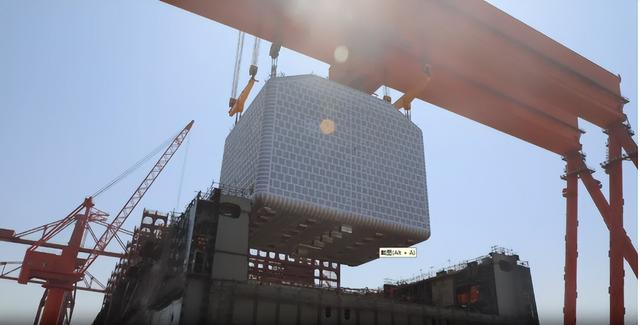
本次吊装相比海吊、云轨车配合施工模式,单船可节省海吊租赁作业等费用近1000万元,极大降低了生产成本。B型舱双车联吊作业的顺利实施,填补了国内又一项技术空白,形成了系统性B型舱吊运、安装工艺“说明书”,为后续液化罐类船舶的建造提供强劲支撑。
大连船舶重工集团装备制造有限公司大连船舶重工集团装备制造有限公司(简称大船集团装备公司)是由大连船舶重工集团有限公司独资成立的全资子公司,于2009年12月17日注册成立。
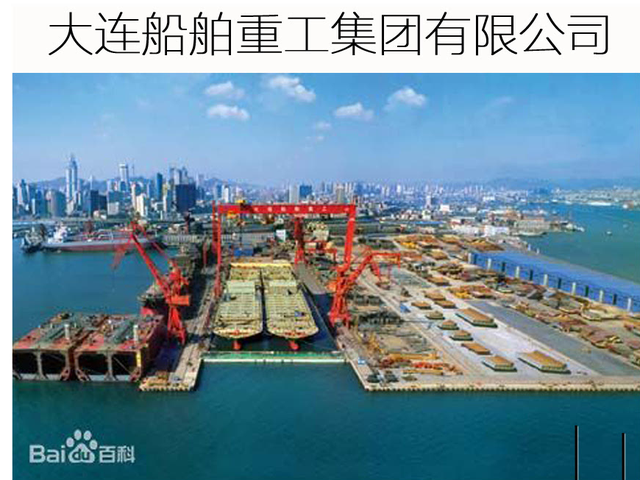
作为大船集团重工产业的代表,大船集团装备公司将努力建设成为重工领域国内领先,国际一流的知名骨干企业;具有大型成套设备加工制造能力的重型装备制造商和供应商;具有大型项目总包能力和管理能力的工程管理公司;打造 “大船”品牌重工产品、拥有自主知识产权的高新技术企业。
大船集团装备公司秉承大船集团多元化发展的战略,确定了核电装备、锅炉压力容器、海水淡化、大型工业装备、大型起重设备和港口机械、建筑钢结构、风电、节能环保装备、船舶与海洋工程装备等八大重工产业的目标领域产品。以自行研发、引进、合资等多种形式开展与国内外具有实力的大公司的合作。
在生产资源上,以锅压、邮政码头区域为主体的内部建造基地及外部建造基地,总作业面积约17万平方米,其中厂房面积约6万平方米。年钢料切割能力达到6万吨,年加工制作能力超过5万吨,具有各种大型重工装备的自生产设计、钢料切割、铆焊制作、机械加工,到组装试验、码头装船、安装调试的工程技术实力。可整合的集团相关资源和社会资源,充分发挥各自的优势,更增强了重工装备制造的实力。
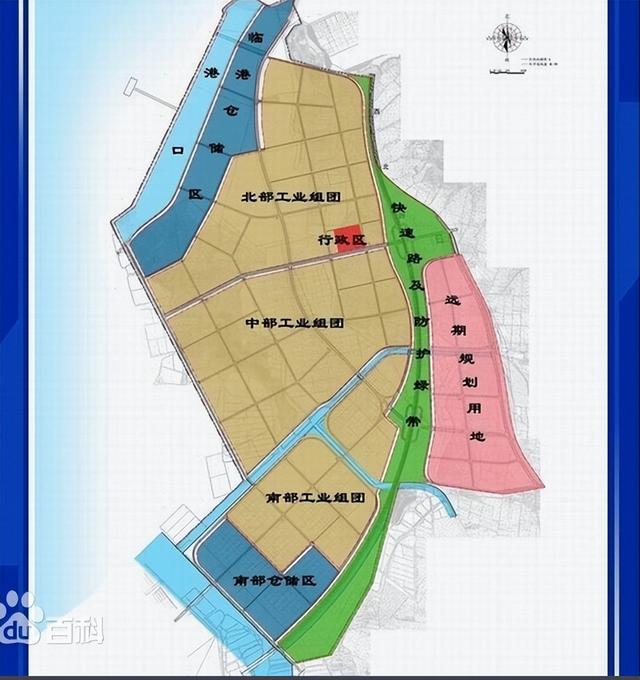
正在建设中的三十里堡临港工业区50万平方米重工产业基地,交通运输条件优越。沈大高速公路、哈大公路、长大铁路、滨海路等交通动脉临境贯穿南北,新基地的海岸线长350米,将建设714米码头,吃水深度为-7米。建成后的重工基地场区设钢料加工间、不锈钢加工间、海水淡化制造间、锅炉压力容器制造间、建筑钢结构制造间、大型工业装备制造间、风电钢结构制造车间、模块制造车间、结构制造车间、涂装厂房以及露天作业场地;将拥有各种吨位的起重设备、8000吨油压机、压型专用压型模具、加热炉、焊接设备、数控切割机、龙门切割机、卷板机等先进设备,完全满足目标产业领域的建造需求。
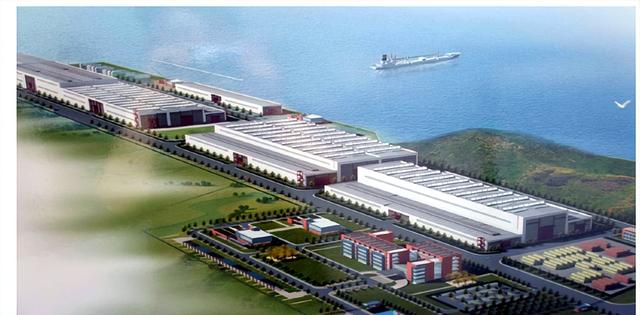
大船集团装备公司秉承了大连船舶重工多年来丰富的技术及建造经验,拥有100余人的研发技术团队在各产业专家的带领下,各产业领域都取得了突破性的进展;所承接的各产业目标产品还可以依托大连船舶重工船研所进行设计工作,具备较强各种产品的详细设计能力和生产设计能力。
大船集团装备公司拥有完善的质量安全管理体系,全面贯彻“精心设计、精细管理、精工建造、精诚服务、精益求精”的质量要求,广大员工在“关爱生命,绿色造船”的旗帜下创造和享受着安全健康的生产工作环境。
在“追求卓越,腾飞重工”的理念下,大船集团装备公司致力于不断拓宽重工产业领域,为提高中国装备制造水平做出贡献。