奥氏体不锈钢具有优良的耐高温和耐腐蚀性能,广泛应用于医药、化工等领域,在材料出厂前,一般需要对其进行固溶化处理,以获得单一的奥氏体组织。如果经过固溶处理后奥氏体不锈钢材料不合格,就很容易发生晶粒长大、敏化等材料劣化损伤,而且奥氏体不锈钢压力容器等设备在制造过程中也会受热成形、焊接、消应力热处理等加工工艺的影响而发生晶间敏化,最终导致材料在腐蚀介质中发生晶间腐蚀[1-2]。金相检验是评定奥氏体晶粒度的常用方法,晶间敏化的检测主要是采用对模拟试样进行加速腐蚀试验后的金相检验方法[3],或采用与正常材料的腐蚀电流密度及自腐蚀电位差异来表征[4]。在实际工作中,人们关注更多的是奥氏体不锈钢材料的监督检验材料是否错用,化学成分是否符合标准要求等,而对于材料热处理是否合格、热作业过程中是否存在材质劣化等关注较少。
超声检测和硬度测试是材料检测和性能表征的两种基本方法,具有快速、方便等优点,被广泛应用于一线生产领域的材料内部缺陷检测和表面力学性能测试,而且随着研究的深入,其应用领域也在不断扩大,如利用线性超声对不锈钢晶粒尺寸[5]、敏化程度[6-7]、疲劳和棘轮损伤进行评价等[8],利用非线性声学效应对304不锈钢晶粒尺寸进行检测和腐蚀敏感性进行评价[9-10]、Super304H中的早期晶间腐蚀检测[11]、304和304L不锈钢的敏化评价[12],利用显微硬度指标表征不同热处理工艺下不锈钢的晶粒度、相变程度、元素分布等诱导的综合效应等[13-15]。然而,上述研究对超声和硬度等方法的测试条件、使用环境有较高要求,鲁棒性较差,难以满足生产使用现场便捷、快速应用的要求。笔者对比研究了不同热处理状态下奥氏体不锈钢的里氏硬度、超声信号特征和显微组织之间的关系,建立了基于D-S证据理论的奥氏体不锈钢热劣化评价模型,为该类材料的现场材料监督和评价提供了新的思路。
1. 试验材料与方法1.1 试验材料及其化学成分试样的材料为304奥氏体不锈钢,试样尺寸为70 mm×70 mm×20 mm(长度×宽度×高度),该材料在20 ℃时密度为7.93 g/cm3,常温下的纵波声速为5 700~5 800 m/s[16](纵波声速与材料的密度、弹性模量、泊松比等有关)。用原子发射光谱仪对试样进行化学成分分析,结果如表1所示。由表1可知:试样的化学成分符合GB/T 20878—2007 《不锈钢和耐热钢 牌号及化学成分》的要求。对A组试样进行固溶处理(1 050 ℃保温30 min,然后空冷至室温),对B组试样进行敏化处理(1 050 ℃保温30 min,降温至450 ℃并保温2 h,然后空冷至室温),C组试样为未进行任何处理的铸态304不锈钢,3组试样宏观形貌如图1所示。
Table 1. 304奥氏体不锈钢化学成分分析结果
项目
质量分数
C
Si
Mn
P
S
Ni
Cr
Mo
Co
Cu
V
N
实测值
0.035 9
0.424
1.12
0.031 1
0.007 4
8.21
18.25
0.047 8
0.216
0.063 1
0.078 7
0.092 4
标准值
0.030
1.00
2.00
0.045
0.030
8.00~12.00
18.00~20.00
—
—
—
—
—
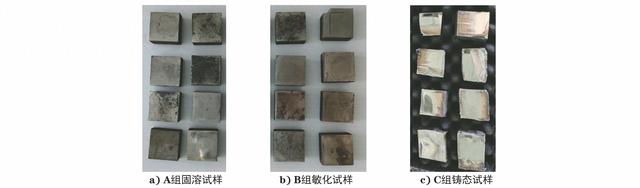
图 1 3组试样宏观形貌
1.2 硬度测试方法硬度测试仪器为高精度便携式里氏硬度计(型号为PROCEQ EQUOTIP 550 Leeb),该硬度计可以快速测试金属材料的表面硬度,依据GB/T 17394.1—2014 《金属材料 里氏硬度试验 第1部分:试验方法》分别对A、B和C这3组试样进行不少于6次的硬度测试,计算各组试样硬度的算术平均值和标准差。
1.3 超声检测方法采用超声波检测仪和中心频率为5 MHz、直径为5 mm的单晶直探头对试样进行超声检测,超声信号激发脉冲宽度为50 ns,信号采样频率为100 MHz;对试样表面进行机械打磨,得到平整的金属光泽面,采用水作为耦合剂,探头上放置金属块,以保持恒定的探头压紧力,信号增益均为15 dB,记录超声A扫信号的从初始波到不少于4次底面反射波的射频波形数据。
1.4 金相检验及扫描电镜分析方法将试样机械打磨、抛光后,依据GB/T 4334—2020 《金属和合金的腐蚀 奥氏体及铁素体-奥氏体(双相)不锈钢晶间腐蚀试验方法》,用体积分数为10%的草酸溶液对试样进行电解腐蚀,然后将试样置于光学显微镜及扫描电镜下观察。
2. 试验结果与分析2.1 金相检验及扫描电镜(SEM)分析结果A组固溶试样的显微组织形貌如图2所示。由图2可知:A组试样材料为单一的奥氏体相,可以观察到孪晶,晶界形态为Ⅰ类阶梯组织,平均晶粒度约为5.0级。
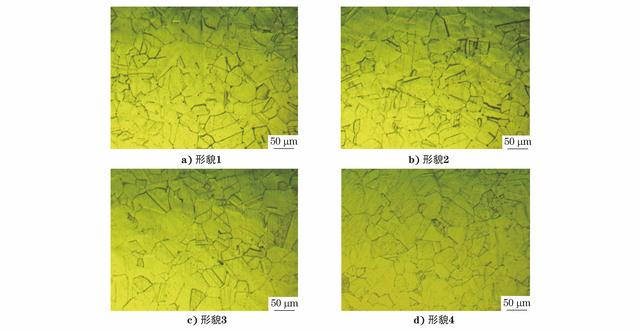
图 2 A组固溶试样的显微组织形貌
B组敏化试样的显微组织形貌如图3所示。由图3可知:B组试样材料为单一的奥氏体相,平均晶粒度约为4.5级,晶界较粗大,呈网状分布,有碳化物析出,晶界形态为II类混合组织。
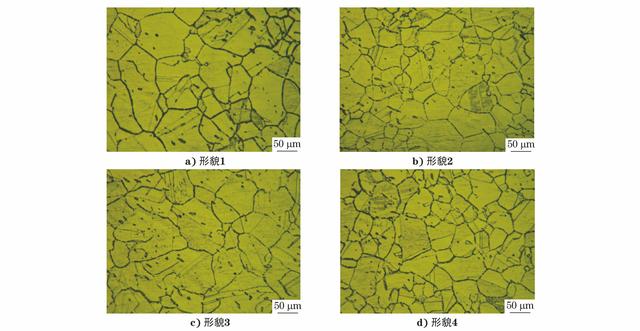
图 3 B组敏化试样的显微组织形
对试样B进行扫描电镜分析,结果如图4所示。分别对晶界及晶粒进行能谱分析,结果如表2所示,可看出敏化处理后的奥氏体晶界析出物富含Cr元素,这种富Cr化合物沿晶界沉淀,会导致正常晶界区域中Cr离子浓度的降低,形成“贫铬区”,在腐蚀介质的作用下,晶界区域优先溶解而产生晶间腐蚀[17]。
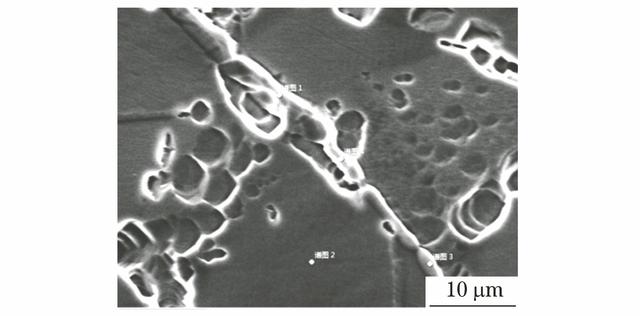
图 4 试样B晶界区域SEM形貌
Table 2. 试样B的能谱分析结果
分析位置
质量分数
Cr
Mn
Fe
Ni
谱图1(晶界)
24.57
0.98
70.29
4.16
谱图2(晶内)
19.52
1.23
70.79
8.46
谱图3(晶界)
25.51
0.88
68.82
4.79
谱图4(晶界)
25.52
0.94
68.95
4.59
C组铸态试样的显微组织形貌如图5所示。由图5可知:C组试样的显微组织主要为奥氏体+铁素体,在奥氏体晶粒内部和晶界上分布着骨骼状铁素体相,且部分呈网状分布,晶界形态为四类游离铁素体组织。
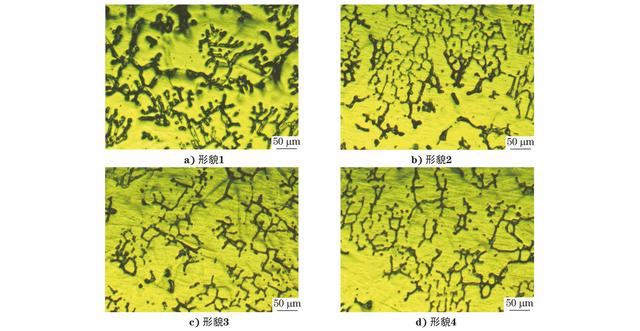
图 5 C组铸态试样的显微组织形貌
2.2 里氏硬度测试3组试样里氏硬度的随机测试结果如图6所示。由图6可知:测试次数较少时,结果的重现性较差,当测试次数大于10次时,硬度平均值及标准差均趋于稳定,重现性较好。在进行16次硬度测试的条件下,3组试样的硬度分别为374,382,325 HLD,标准差分别为4.7,8.3,19.6 HLD,可看出B组试样的硬度比A组试样增大了2.1%,而硬度标准差却是A组试样的1.77倍,C组试样的硬度比A组试样降低了13.1%,而硬度标准差却是C组试样的4倍,硬度标准差的变化最明显。这是因为:在高温敏化过程中,晶粒的长大趋势和晶界析出碳化物对晶界的钉扎效应并存[18-19],两种相互制衡效应使B组敏化试样的里氏硬度增大,但增大得不明显;同时在热应力和相变应力的互相作用下,B组敏化试样的组织及应力分布均匀性被破坏,在宏观上表现为硬度不均匀,标准差增大;C组铸态试样中存在大量的铁素体且分布极不均匀,这种组织的极度不均匀性会导致其不同区域的力学性能不同,硬度标准差显著增大。
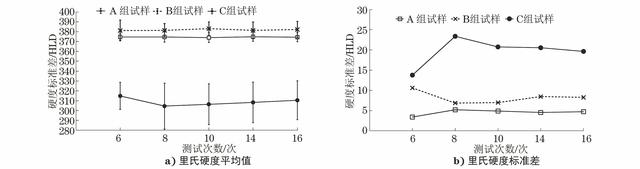
图 6 3组试样里氏硬度的随机测试结果
硬度标准差S反映了同一组奥氏体不锈钢试样内硬度测量值的离散度,可以对其热处理状态进行表征,但对于硬度基础值或表面状态不同的材料,直接采用硬度标准差会引起误判。为解决硬度平均值相差悬殊材料的硬度表征问题,引入硬度离散率指标Vs,对标准差S进行标准化,如式(1)所示。
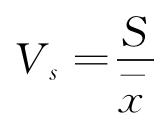
(1)
式中:S为试样的样本标准差;为硬度平均值。
3组试样的里氏硬度离散率曲线如图7所示。由图7可知:A、B、C组试样的里氏硬度离散率平均值分别为1.3%,2.2%和6.3%,明显表征了铸态、固溶态、敏化态的材料状态变化。
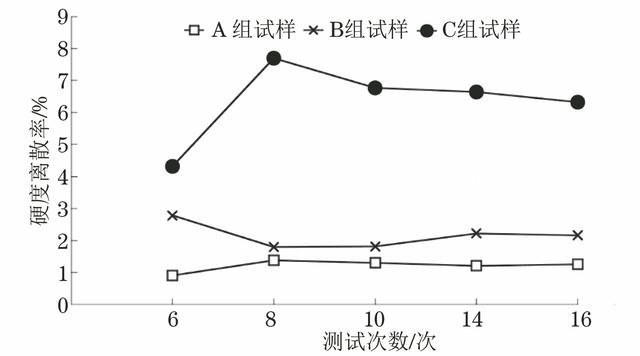
图 7 3组试样的里氏硬度离散率曲线
2.3 超声检测3组试样的超声检测A扫信号如图8所示。由图8可知:A、B组试样回波信号经过6次反射之后的底波信号已衰减到噪声背底水平,利用前4次的底波反射信号可得到A、B组试样的超声衰减系数分别为230.77 dB/m和 254.98 dB/m,可看出敏化后试样的纵波衰减系数会增大,这与文献[6-7]的试验结果基本一致;C组试样回波信号仅存在1次底面反射波,信号严重衰减,这是因为粗大的奥氏体晶粒和铁素体枝晶对超声波的严重衰减效应,根据这个特性,可以对铸态不锈钢进行鉴别。
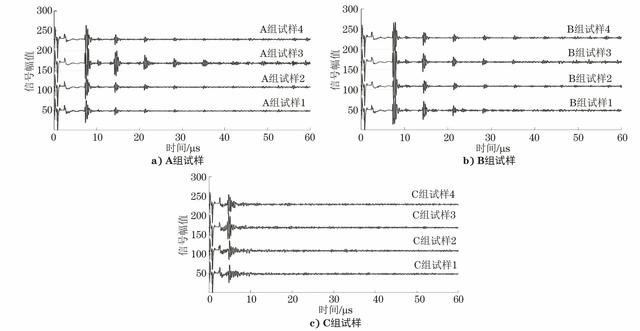
图 8 3组试样的超声检测A扫信号
考虑到在实际应用中试样的表面粗糙度、探头的耦合情况以及试样厚度等误差因素,以及奥氏体基础晶粒尺度的影响,利用超声回波信号的时域信息或超声衰减系数较难区分正常固溶处理的试样和敏化试样[20]。对A组试样的回波信号进行傅里叶频谱分析,结果如图9a)所示,频谱整体上主要集中在1,3,5,7 MHz附近,且3 MHz附近的频谱宽度最大,局部呈周期性的振荡现象。为了消除初始波信号的影响,对信号初始段5 μs时的回波信号进行剥离,结果如图9b)所示,可看出剥离后的频谱宽度在1 MHz附近有所减小,而在其他位置基本保持不变。
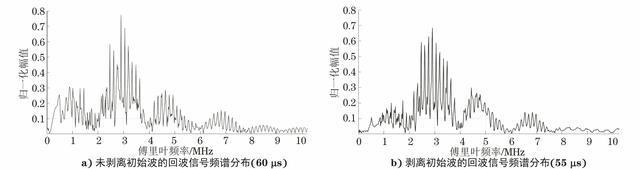
图 9 A组试样的超声回波信号傅里叶频谱分布
图10为B、C组试样的超声回波信号傅里叶频谱分布。由图10可知:两个回波信号都已进行了初始波剥离,B组试样与A组试样的基本频谱波形相似,频谱最大幅值也相近,但5 MHz和7 MHz等较高频谱段的频谱分布差异明显;铸态C组试样的频谱没有明显的波峰集中,且频谱最大幅值较小,反映了粗大晶粒对入射超声波的强烈散射作用。
图 10 B组和C组试样的超声回波信号傅里叶频谱分布
在频率为0~8 MHz时,根据式(2)分别计算每1 MHz频谱段内的能量分布。
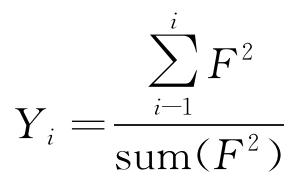
(2)
式中:F为傅里叶频谱幅值;sum(F2)为0~8 MHz的频谱能量之和;Yi为第i个频谱段的频谱能量占比率,i=1,2,3,4,5,6,7,8。
0~8 MHz频谱段能量分布如图11所示。由图11可知:当频率为0~1 MHz时,3组试样的能量占比分别为1.6%,1.0%和7.6%,C组试样的能量占比最高;当频率为2~3 MHz时,3组试样的能量占比分别为40.9%,49.3%和42.1%,占比分别达到各自的最大值,其中B组试样的能量占比最高,但其标准差也最大;当频率为6~7 MHz时,3组试样的能量占比分别为1.3%,0.7%和0.9%,固溶态A组试样的能量占比最高。
图 11 0~8 MHz频谱段能量分布
采用频谱能量下降比指标DYi=max(Y)/Yi表示第i频谱段能量相对于最高频谱段能量的下降比,0~8 MHz频谱能量下降比如图12所示。由图12可知:当频率为0~1 MHz时,3组试样的DY1指标分别为25.6,49.3,5.5,可明显区分出试样C;当频率为6~7 MHz时,DY7指标分别为31.5,70.4,46.8,可区分出试样B。
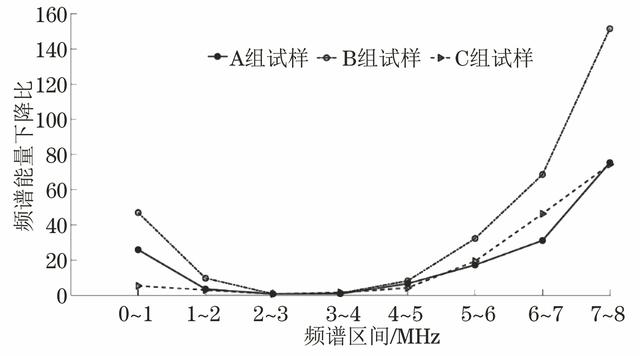
图 12 0~8 MHz频谱能量下降比
通过上述分析,可以发现超声回波信号的时域特征和频域特征都可以用来表征奥氏体不锈钢的材料状况,但表征的灵敏度和侧重点不同。超声信号的波幅信息对晶粒尺寸比较敏感,且易受试样表面粗糙度、探头耦合情况、工件厚度误差等因素的影响;超声信号的频谱能量呈多峰分布,而且最大峰值在3 MHz附近,低于探头的中心频率5 MHz;与正常固溶态试样A相比,铸造态试样C的超声低频段能量占比增大,有整体向低频段偏移的趋势,与指标DY1密切相关,而敏化态试样B的高频段能量占比降低,与指标DY7密切相关。结合前文的金相检验、SEM和能谱分析结果可知,上述现象产生的原因是粗大晶粒和晶界析出物对信号中高频分量的抑制。
3. D-S证据理论信息融合里氏硬度测试结果和超声检测结果分别从不同方面反映了奥氏体不锈钢的材料状况,但都存在一定的局限性,甚至在某些情况下存在信息冲突。D-S证据理论是一种多信息融合及决策的方法,能有效解决信息缺失和不准确性引起的不确定性,一般由辨识框架、基本概率分配、合成规则等组成[21]。辨识框架为不确定性事件A的所有可能性集合,记作Θ={A1, A2,…,AN},基本概率分配函数m(A)如式(3)所示。
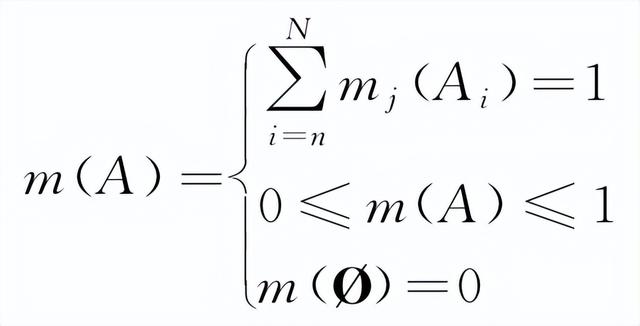
(3)
式中:mj(Ai)为证据体mj对事件Ai的支持度;N为不确定性事件A的个数;m(∅)为证据体m对空集∅的支持度。
D-S证据理论的核心策略是采用Dempster规则对事件Ai的M个独立证据体m的基本概率分配进行组合,如式(4)所示[22-23]。

(4)
式(4)中K为证据冲突因子,计算公式如式(5)所示。

(5)
根据是否需要对材料进行复验,把奥氏体不锈钢划分为材料合格A1和材料复验A2(包括敏化和晶粒异常粗大)两种状态事件,则识别框架Θ={A1, A2 }。证据体m={m1, m2, m3}, 分别对应硬度离散率Vs、低频谱能量下降比指标DY1、高频谱能量下降比指标DY7,根据试验统计分析结果构造基本概率分配函数,如式(6)~(8)所示。
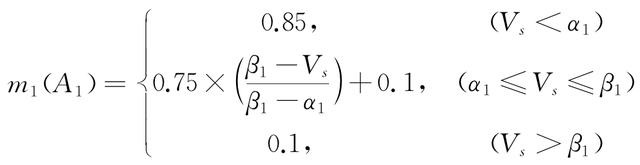
(6)
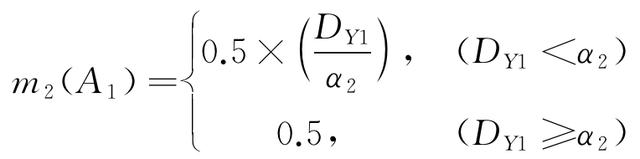
(7)
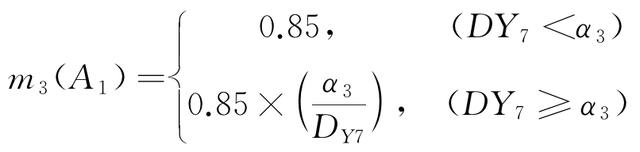
(8)
式(6)中的Vs与A1呈负相关,阈值α1、β1分别取值为0.015,0.06;式(7)中DY1与A2呈正相关,如前文所述DY1对晶粒粗大类材料劣化反应灵敏,阈值α2取值为25;式(8)中DY7与A2呈负相关,阈值α3取值为30。
根据式(4)计算A1的融合概率为

(9)

(10)
M(A1)代表了Vs、DY1、DY7指标的融合结果,考虑到评价的准确度、可信度以及复验成本,将M(A1 )的阈值设置为0.85,即当M(A1 )不小于0.85时,材料的综合评价结果为合格,当M(A1 )小于0.85时,材料需要通过金相检验等方法进行复验。10个试样的D-S证据理论融合模型评价结果如表3所示,其中试样1~3为铸态样,试样4~6为敏化样,试样7~10为固溶样,可以看出单一指标证据在某些试样上置信度不高,甚至相互冲突,经融合后评价结果的置信度得到提高,融合评价结果的正确率为100%。
Table 3. 10个试样的D-S证据理论融合模型评价结果
试样编号
m1/Vs
m2/DY1
m3/DY7
m1(A1)
m2(A1)
m3(A1)
M(A1)
融合评价
1
0.058
5.42
46.69
0.133
0.11
0.55
0.022
复验
2
0.079
6.23
62.20
0.100
0.12
0.41
0.011
复验
3
0.052
4.98
37.36
0.233
0.10
0.68
0.067
复验
4
0.018
46.76
83.86
0.800
0.50
0.30
0.636
复验
5
0.023
50.85
100.40
0.717
0.50
0.25
0.463
复验
6
0.019
43.40
68.61
0.783
0.50
0.37
0.681
复验
7
0.017
21.10
37.87
0.817
0.42
0.67
0.870
合格
8
0.012
27.76
29.41
0.850
0.50
0.85
0.970
合格
9
0.016
31.66
27.92
0.833
0.50
0.85
0.966
合格
10
0.008
26.05
40.39
0.850
0.50
0.63
0.907
合格
4 结论
(1) 里氏硬度离散率与奥氏体不锈钢材料的热处理状态高度相关,正常固溶态材料的里氏硬度离散率小于1.5%,而当材料存在敏化或铸态组织时,硬度离散率会显著增大。
(2) 奥氏体不锈钢超声回波信号的频谱呈多峰分布,与正常固溶态材料相比,铸态材料超声回波信号的低频谱段能量占比增大,敏化态材料的高频谱段能量占比降低。
(3) 采用D-S证据理论对硬度离散率、超声回波信号的低频谱能量下降比和高频谱能量下降比等3个特征指标进行融合,融合指标可有效降低单一指标在材料评价上的不确定性,解决指标之间的相互冲突问题,显著提高奥氏体不锈钢材料快速评价结果的置信度。
文章来源——材料与测试网