21世纪人类所面临的问题主要是环境污染和资源匮乏,减少日益严重的环境污染、节约资源是新世纪的技术挑战之一[1−2]。镁是地球上第8丰富的元素,也是海水中第3丰富的元素,其在工程材料上的使用量仅次于钢铁与铝,并且镁作为最轻的金属结构材料之一,还具有高的比强度、良好的电磁屏蔽特性、良好的可加工性以及易于回收等优点[3−4]。随着镁合金生产技术的不断完善和成熟,镁合金在各个领域的应用日益广泛。然而,由于镁合金的电化学活性高,导致其耐腐蚀性较差;并且镁合金的耐磨性能也不够理想,使其一直局限于静态构件场合使用。镁合金的耐腐蚀性和耐磨性差这一问题阻碍它成为广泛应用的合金。因此,如何提高镁合金的耐腐蚀性和耐磨性是国内外学者研究的重点之一[5−9]。
表面防护技术是保护镁合金耐腐蚀和耐磨损的最有效的方法之一。目前,已经有多种方法应用于镁合金的表面防护,包括化学转化处理[10]、阳极氧化处理[11]、微弧氧化处理[12]、溶胶凝胶法[13]、电镀和化学镀[14]、气相沉积[15]等。然而这些方法都有各自的优缺点,如化学转化处理是将镁合金与处理液通过化学反应在其表面生成稳定的化合物膜,但这种工艺在处理过程中对环境的污染性较大,不符合绿色环保要求;阳极氧化处理是指在电解作用下,镁合金表面在电解质溶液中形成一层氧化膜的表面保护性技术,此工艺虽然能够大面积沉积薄膜和处理形状复杂的零件,但是其薄膜的力学性能较差。而磁控溅射作为物理气相沉积(PVD)的一种沉积方式,它能沉积耐磨、耐蚀、光学和其它各种功能薄膜,并且还具有成本低、与基片结合力强、沉积速率快以及绿色环保等优点,是其他传统技术无法媲美的[16−17]。因此,磁控溅射作为主流的镀膜技术之一,是薄膜工业化绿色发展的主要手段之一。
目前,国内外通过磁控溅射技术在镁合金表面的改性研究还多针对于不同的薄膜结构和材料展开。薄膜的结构从单层发展到多层,从一元到二元再到多元化。由于镁合金与陶瓷薄膜的结构不匹配性,导致镁合金表面的陶瓷薄膜很容易剥落。因此,研究人员试图在陶瓷薄膜与镁合金之间引入过渡层,从而形成复合涂层,过渡层主要的目的是增加膜基结合力和减少由于PVD工艺引起的孔隙率。本文综述了镁合金表面上的单层金属膜层和金属/陶瓷复合涂层的研究进展,简要地分析了不同类型膜层耐腐蚀和耐磨损性能的影响因素,并展望了磁控溅射技术在镁合金表面防护领域的发展前景。
1. 镁合金表面磁控溅射单层金属薄膜磁控溅射技术是在普通直流(射频)溅射技术的基础上发展起来的,其原理是入射粒子不断地碰撞靶材,致使靶材原子获得动能被溅射出来沉积在基片上形成薄膜[18−19]。在镁合金防护处理中,金属涂层作为保护性涂层具有导电性,可避免在电子和航空航天应用中出现静电积聚[20]。另外,在生物医学领域中,金属涂层如钛涂层与镁合金相结合可用作植入材料[21]。磁控溅射技术通过镁合金表面制备金属膜层的方法,使镁合金的耐腐蚀、耐磨损性能得到了一定的提升。目前,已有学者通过磁控溅射技术对AZ31、AZ91等镁合金表面金属防护膜层的制备展开了研究。
1.1 薄膜的耐腐蚀性在镁合金表面上涂覆耐腐蚀性较强的金属膜层可以对镁合金的耐腐蚀性起到强化作用。为此,研究人员在镁合金表面上制备了不同金属单质膜层,探究了不同单质金属膜层对镁合金耐腐蚀性的影响。涂层的微观结构是影响耐腐蚀性的关键因素。若涂层存在孔隙、裂纹等缺陷,会使腐蚀介质穿过膜层到达基体表面,从而导致原电池的形成。表1为研究人员在镁合金表面上制备不同金属涂层的组织结构。从表1中可以看出,镁合金表面上制备的所有金属涂层致密性较好,无孔隙和裂纹等明显缺陷,并且涂层均匀的涂覆在基体上。

表2比较了镁合金表面不同金属单质膜层的耐腐蚀性(Ecorr为腐蚀电位,SCE为饱和甘汞电极)。可知经磁控溅射镀金属单质膜层后的镁合金试样的腐蚀电流密度(Icorr)均低于镁合金基体,其耐腐蚀性均得到了提高。Zhang等[22]通过同一沉积条件下在AZ91镁合金表面上分别制备了Al、Ti、Zr和Hf 4种金属涂层,比较了相同厚度(5 μm)的不同金属涂层的抗腐蚀性能。结果表明Hf涂层与基体的电位差最小,并且Hf涂层的腐蚀电流密度最低;此外在盐雾试验后,结合扫描电镜发现Hf涂层表面仅有少量的腐蚀小坑,而其他金属涂层完全失去了保护作用。因此,在工艺参数相同的情况下,Hf涂层相比于Al、Ti以及Zr涂层具有优异的耐腐蚀性。另外,沈钰等[27]将铝膜在模拟体液腐蚀3和10 h后,发现铝膜在10 h以内可以保护镁合金基体不受模拟体液腐蚀,体现了铝膜具有良好的耐腐蚀性。磁控溅射镀金属膜在新型薄膜材料的选择和制备工艺方面还需进一步的探究,对镁合金表面镀金属膜的耐腐蚀性将有巨大的提升空间
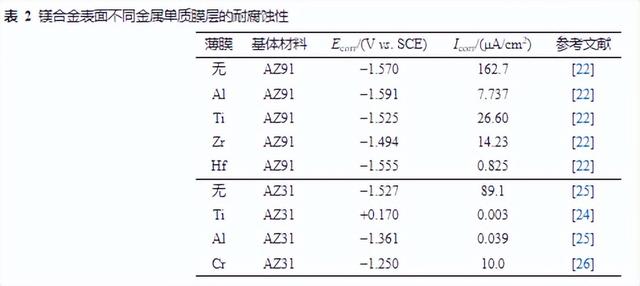
1.2 薄膜的耐磨性能对于镁合金应用于户外,耐磨损性能也显得尤为重要。如果能提高镁合金的耐磨性能,将大大扩大镁合金的应用范围。因此,研究人员在镁合金耐磨性能方面展开了大量工作。表3为镁合金表面上不同金属薄膜的耐磨损性能研究。其中Wu等[23]在镁合金表面上制备了Al和Ni膜,比较了两者的耐磨性能,发现Ni膜的硬度高于Al膜,在350 ℃+24 h高真空热处理后,铝膜与基体完全反应,形成厚度约为5 μm的反应层(Al12Mg17相)。而镍膜在350 ℃+48 h处理后,没有发现镍膜与基底的反应层。由于Al12Mg17为本质脆性相,所以热处理后导致临界载荷值急剧下降。并且在滑动磨损试验中,Ni膜的磨损率明显小于Al膜,这就意味着Ni膜比Al膜具有更好的耐磨性。魏琦等[28]在镁合金表面溅射铝膜,发现溅射时间为1 h的铝膜粒子比溅射时间为50 min的铝膜粒子更加细小且分布均匀,并且平整度也要优于溅射50 min的铝膜,更加有利于铝膜与基体的结合。李忠厚等[24]在镁合金表面上制备了单层钛膜,使其耐磨性大大提高。王振林等[29]通过磁控溅射在镁合金表面上制备了铝膜,发现铝膜与基体之间存在过渡层,并且铝膜的表面硬度、弹性模量随深度的增加而递减。综上,在镁合金表面磁控溅射金属薄膜的耐磨研究中,Ti膜具有良好的耐磨性,Ni膜的耐磨性优于Al膜。并且涂层的耐磨性受工艺参数、热处理等因素的影响较大。所以,在制备薄膜时,应综合分析各项因素,从而制备出性能优良的薄膜。
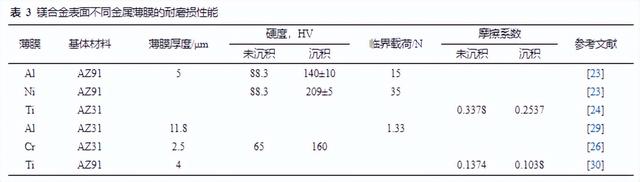
磁控溅射的主要工艺参数有:溅射功率、溅射时间、溅射气压、温度、偏压等。工艺参数主要是影响薄膜的厚度、膜层结构以及薄膜与基体的结合力等。增加一定的溅射时间可提高薄膜的厚度和结合力,薄膜的耐腐蚀性略有增强;但时间过长,会导致膜基结合力下降,从而影响其性能。提高偏压有利于提高薄膜的致密度,但过高的偏压会导致耐腐蚀性下降。适当的增加温度可提高薄膜的耐腐蚀性,但过高的温度会导致薄膜的厚度降低。因此,探索适当的工艺参数对提高薄膜的质量和性能尤为重要。
在耐腐蚀性方面,研究人员探究了不同工艺参数对其耐腐蚀性的影响。如图1所示,Zhang等[25]采用了不同的溅射时间(120、150和300 min)在AZ31镁合金表面上制备了铝膜,研究了不同的溅射时间对耐腐蚀性的影响。结果表明当溅射时间从120增加到150 min时,由于膜厚和临界载荷的增加,腐蚀电位略有增加,但当溅射时间增加到300 min后,膜厚和临界载荷显著增加,腐蚀电位比裸镁合金大136 mV。同时,腐蚀电流密度也降低了两个数量级。这可能是由于随着溅射时间的不断增加,铝膜层增厚,在增厚的过程中,填补了铝膜生长过程中的孔隙、裂纹等缺陷,更能有效地保护镁合金基体。Wu等[26]研究了偏压对涂层性能的影响,如图2所示,利用不同偏压(0、−50、−150和−250 V)在镁合金表面上制备了铬涂层,发现增加偏压可使铬涂层的表面结构更加致密;在−150 V偏压下铬涂层的腐蚀电位最高,而在−250 V偏压下铬涂层的腐蚀电位最低。结合扫描电镜来看,偏压为−250 V时的铬涂层比偏压为0、50和−150 V时的铬涂层更致密、更光滑,但其腐蚀电位较低。研究人员分析其原因可能是涂层与基体的结合力差,腐蚀坑膨胀率高所致。张岩[31]还研究了不同温度(350、400和450 ℃)对铝层的耐腐蚀性的影响,发现350和450 ℃时试样的腐蚀电位均得到了提高,并且腐蚀电流密度也下降了一个数量级;但是在400 ℃时试样的腐蚀电位降低了100 mV,腐蚀电流密度增加了0.115 mA/cm2。研究人员认为造成这个原因的情况可能是在400 ℃的条件下,铝层和过渡层的微观结构呈柱状晶形式,在晶间发生腐蚀。
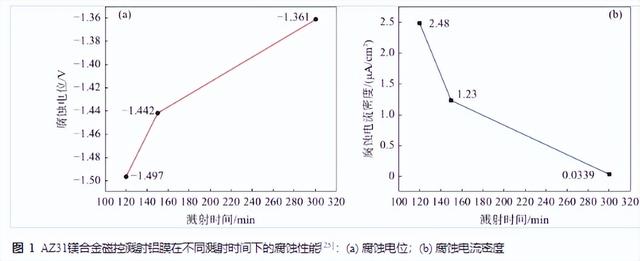
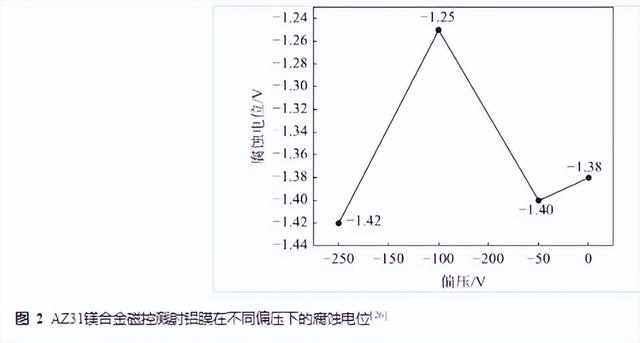
在耐磨性方面,研究人员探究了工艺参数与耐磨性能之间的联系。如李丽等[30]利用磁控溅射技术在镁合金表面上沉积了钛膜,探究了溅射时间与膜基结合力之间的关系,如图3所示,当溅射时间从1增加到6 min时,钛膜与基体的结合能力逐渐增大。但是当溅射时间增加到6 min后,其结合强度急剧下降。其原因可能是溅射时间太长,导致工作温度过高,使粒子碰撞能力增强,轰击试样表面,最终导致膜层呈龟裂和不致密状态,从而导致膜基结合能力下降。

Wu等[26]讨论了偏压对磁控溅射铬膜的影响,如图4所示,改变偏压对涂层样品的显微硬度没有明显影响,但是相对于基体而言,AZ31的表面显微硬度由于铬镀层的形成而大大提高。张津等[32]在镁合金表面上制备了膜厚大约为10 μm的铝膜,研究了不同衬底温度(室温、100 ℃和200 ℃)下铝涂层的力学性能。发现随着衬底温度的升高,铝膜的厚度以及临界附着力均随之下降;在衬底温度为室温+无加热后处理的情况下,铝膜的厚度最大,加热后处理使铝膜在生长过程中发生动态再结晶,从而影响薄膜的厚度;室温条件下,一次性沉积和分段方式沉积铝膜的临界附着力相当,均比施加衬底温度100 ℃、200 ℃和加热后处理的铝膜高,这表明了室温溅射铝膜的膜基结合力最好[32]。
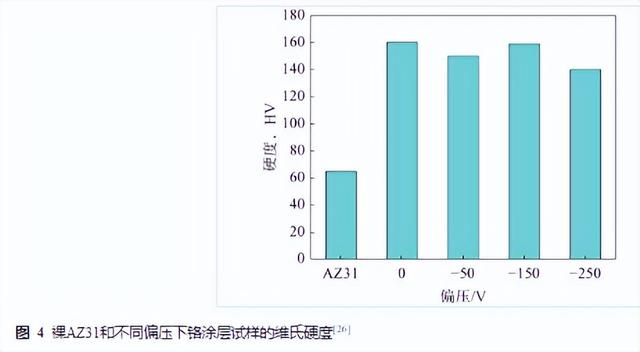
2. 镁合金表面磁控溅射金属/陶瓷复合涂层由于工业的快速发展,对机械零件也提出了更高的要求,对相应材料的性能要求也越来越高,比如耐高温、耐磨损、抗腐蚀等[33]。由于陶瓷材料具有金属材料难以比拟的耐腐蚀性和耐磨性,将金属和陶瓷材料结合涂覆在镁合金表面上,不但能够提高镁合金的耐腐蚀性和耐磨性,而且能解决陶瓷材料与镁合金基体的匹配性问题,因此金属/陶瓷复合涂层一直是研究的热点。金属/陶瓷复合涂层作为双类型涂层结构体系由金属层和陶瓷层组成。金属层作为过渡层在金属/陶瓷复合涂层结构中充当陶瓷层与镁合金基体的连接介质,其主要目的是增加陶瓷层与镁合金基体的结合强度、降低涂层的孔隙率,以保证陶瓷涂层的功能,从而提高其性能。由于金属/陶瓷复合涂层的结构与性能易受金属过渡层和制备工艺等其他因素的影响,因此研究人员对此进行了相关研究。
2.1 金属过渡层对复合涂层组织结构的影响金属过渡层对金属/陶瓷复合涂层的生长有着重要的影响,它决定了复合涂层的结合强度、致密性和残余应力等。表4为利用磁控溅射技术在镁合金表面制备金属/陶瓷复合涂层的及组织结构。从表4中可以看出,复合涂层的制备还存在较多孔洞等明显缺陷,尤其是金属过渡层。黄佳木等[34]利用磁控溅射技术在镁合金表面上分别制备了Al/SiNx、Ti/SiNx、Zr/SiNx复合涂层,结果表明金属过渡层(Al、Ti和Zr)表面存在较小的孔缺陷,在生长过程中,小孔缺陷不能被溅射出的离子完全填充,因而导致复合涂层的致密性降低。李海涛[35]采用非平衡反应磁控溅射技术在镁合金表面上制备了Ti/TiN/TiCxN1−x复合涂层,研究了不同厚度的过渡层Ti对复合涂层残余应力的影响,发现陶瓷TiN层与金属Ti层之间存在物理参数的不匹配,使得刚开始沉积的TiN层表面较为粗糙,随着沉积的进行,过渡层Ti的厚度增加,位错应力也就越大,从而导致残余应力变大。夏登福等[36]通过室温磁控溅射技术在镁合金表面沉积了Ti/SiC/DLC复合涂层,发现过渡层Ti与陶瓷层中的Si元素、基体中的Mg均发生明显扩散,过渡层与陶瓷层、基体呈现良好的冶金结合。丁泽良等[37]用磁控溅射工艺在镁合金表面上制备了TaO涂层和Mg/TaO复合涂层,结果表明过渡层Mg的引入使得Mg/TaO复合涂层的表面平整度优于TaO涂层,同时也有利于陶瓷层TaO在其表面均匀成核,形成致密涂层。由以上可以看出,过渡层的引入可提高复合涂层与基体的结合强度,降低过渡层缺陷有利于复合涂层质量的改善及性能的提高。

2.2 金属过渡层对复合涂层耐蚀耐磨性能的影响金属/陶瓷复合涂层的耐腐蚀性受金属过渡层的影响较大。在金属/陶瓷复合涂层的保护机制中,当外层陶瓷失效后,涂层能否有效地保护基体取决于过渡层的材料性质、微观结构和过渡层与基体的结合强度等。因此,除了表面陶瓷涂层外,过渡金属层也起着重要的作用。表5为利用磁控溅射技术在镁合金表面制备金属/陶瓷复合涂层的耐腐蚀性。从表5中不难发现,涂覆金属/陶瓷复合涂层的镁合金试样的耐腐蚀性相对于镁合金基体而言得到了显著的提升。吴国松等[40−41]比较了在同种沉积条件下AZ31镁合金表面上Al2O3/Al和Al2O3/Ti 2种复合涂层的耐腐蚀性,发现Al2O3/Al膜的腐蚀电流密度远远低于Al2O3/Ti膜。其原因是腐蚀介质可通过涂层缺陷与基体接触,导致金属过渡层与基体构成腐蚀电池。由于过渡层Al表面能形成一层致密的氧化铝,与陶瓷层Al2O3匹配较好,因而Al2O3/Al复合涂层不易被破坏。此外浸泡试验结果表明浸泡2 h后的Al2O3/Ti膜试样表面已经遭受多处腐蚀,蚀坑较深,而沉积Al2O3/Al膜的试样表面受腐蚀程度要小于Al2O3/Ti膜试样。因此,Al2O3/Al涂层的耐腐蚀性优于Al2O3/Ti涂层。同时,该学者在模拟生理环境下研究了中间层(Ti、Al)对复合涂层耐腐蚀性的影响,发现Ti中间层加速了镁合金的腐蚀速率,铝中间层的加入使AlOxNy涂层的表面力学性能得到了较小的提高,但可以有效地阻止腐蚀。结果表明铝中间层优于钛中间层[38]。
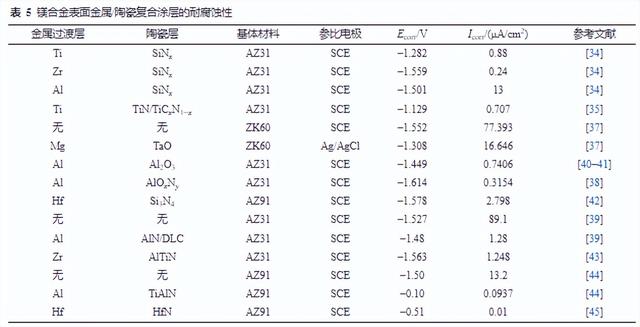
金属/陶瓷复合涂层中的金属过渡层除了充当良好的结合介质外,还应具备一定的承载作用,这样可进一步提高复合涂层的整体耐磨性能。表6列举了关于镁合金表面磁控溅射金属/陶瓷复合涂层的耐磨损性能。许晓静等[46]利用室温磁控溅射技术在镁合金表面上制备了Ti/SiC/CNx复合涂层,表明金属过渡层Ti对复合涂层的高抗磨性能起了一定的作用。这是因为金属钛层使得涂层与基材之间存在良好的界面结合,并且能够对陶瓷层提供更好的支撑,以避免基体过软而发生破裂。丁泽良等[37]用磁控溅射工艺在镁合金表面上制备了Mg/TaO复合涂层,发现过渡层Mg的引入使涂基系统的材料性质和晶体结构均呈梯度变化,有效地降低了陶瓷层TaO与镁合金基体的界面应力,提高了涂基系统的结合力。黄佳木等[34]在镁合金表面上沉积了SiNx陶瓷涂层和Zr(Al,Ti)–SiNx复合涂层,发现复合涂层与镁合金的附着力优于SiNx陶瓷涂层,表明金属过渡层能够增加复合涂层与基体的附着力。并且Al/SiNx复合涂层的附着力为2级,Ti/SiNx复合涂层的附着力为1级,说明金属Ti过渡层对于提高膜基结合力的强度要优于Al。Wu等[40]比较了同种沉积条件下AZ31镁合金表面上Al2O3/Al和Al2O3/Ti 2种复合薄膜,发现与Al2O3/Al薄膜相比,Al2O3/Ti薄膜提高了基体的硬度,这主要是由于钛层间结合良好,显微硬度较高。同时该学者[41]也在AZ31镁合金表面上分别制备了AlOxNy/Ti、AlOxNy/Al薄膜,结果表明AlOxNy/Al的表面硬度和弹性模量小于AlOxNy/Ti,表明在耐磨性能方面,钛作为中间层要优于铝中间层。
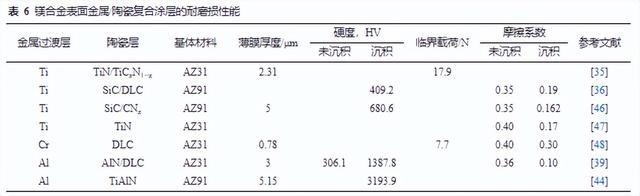
综上所述,金属过渡层能够有效地克服复合涂层与镁合金基体的不匹配性问题;能够兼具膜层成分,减少涂层缺陷,增加膜基间的结合强度,从而可大幅度提高复合涂层的耐蚀耐磨性能。金属/陶瓷复合涂层中,金属作为过渡层,在耐腐蚀性方面,铝过渡层优于钛过渡层;在耐磨性方面,钛过渡层优于铝过渡层。
2.3 工艺参数及其他因素对复合涂层的影响工艺参数对金属/陶瓷复合涂层耐腐蚀性方面的报道甚少。张德秋等[47]利用磁控溅射分别在不同Ar/N2流量比(11:2~11:5)下于镁合金基底上制备Ti/TiN复合涂层,结果表明随着Ar/N2流量比值的增大,镁合金试样的腐蚀电位得到了提高。其中试样的Ar/N2流量比为11:2时,腐蚀电位提高的程度最为明显,表现出最佳的耐腐蚀性。Dai等[48]通过改变Ar/CH4的流量比,分析了不同Cr原子分数(2.34%~31.5%)对Cr/DLC复合涂层耐腐蚀性的影响。实验数据结果表明不同Ar/CH4流量比下的Cr/DLC膜的AZ31均表现出比裸AZ31更高的腐蚀电流密度,这表明Cr/DLC膜不能提高镁合金的耐腐蚀性。分析其原因是由于镁合金薄膜的厚度缺陷中形成了电偶电池。
在耐磨性方面,李海涛[35]探究了不同基体偏压对力学性能方面的影响。如图5所示,随着偏压的增加,膜基结合力和薄膜厚度均呈现先增大后减小的趋势。当偏压为45 V时,此时薄膜的结合力和厚度最大,这主要是由于随着偏压的增加,沉积粒子的能量增加,从而使粒子具有较高的沉积速率和较强的吸附力。但是负偏压超过45 V时,结合力和厚度均出现下降的趋势,这是因为粒子能量过高,形成反溅射,导致薄膜厚度减小;同时高能量的粒子也会造成基体温度上升,使得薄膜与基体之间的热应力增大,从而使得结合力减小。与此同时,该学者还研究了不同溅射电流(0.30、0.35、0.40、0.45、0.50 A)对薄膜性能方面的影响,发现随着电流的增大,薄膜厚度增大,而结合力是增大后减小。另外,气体流量比对涂层性能也是一个很重要的参数,张德秋等[47]通过改变Ar/N2流量比研究了Ti/TiN复合薄膜对耐磨性的影响。如图6所示,不同Ar/N2流量比的涂层样品相对于镁合金基体都有效地降低了摩擦功,提高了镁合金的耐磨性。其中Ar/N2流量比为11:2时,摩擦系数最低,并且薄膜与基体结合程度最好,其耐磨性最佳。综上所述,适当的气体流量比有助于提高金属/陶瓷复合涂层的耐蚀耐磨性能。过高的偏压和溅射电流不利于复合涂层与基体的结合。
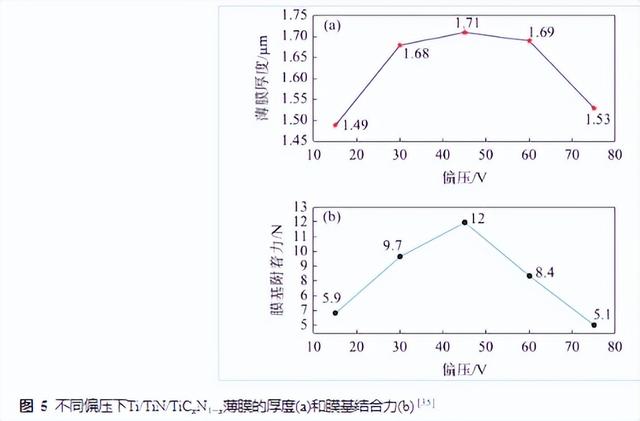
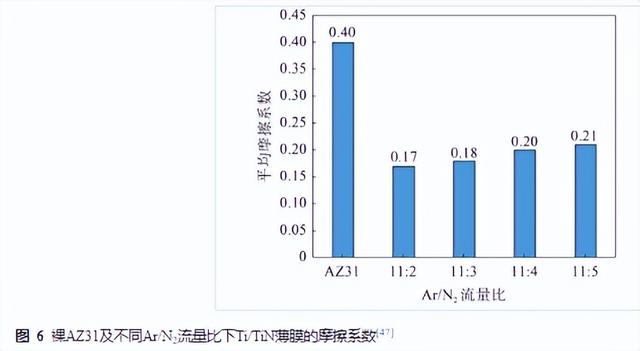
金属/陶瓷复合涂层的耐腐蚀性除了与工艺参数有关,还与其他因素有关,比如膜层层数、退火处理等因素。李海涛[35]等讨论了不同退火温度对AZ31镁合金磁控溅射Ti/TiN/TiCxN1−x复合涂层的耐腐蚀性。如图7所示,随着退火温度的升高,薄膜向着电位电势增大和电流密度减小的方向移动。相对于基体而言,退火处理的薄膜的耐腐蚀性均有所提高,其中300 ℃退火的薄膜的耐腐蚀性最佳。Zhang等[42]采用磁控溅射法在AZ91镁合金表面上沉积了不同交替层数(n=1、2、10、20)的Hf/Si3N4复合涂层。如图8所示,不同交替层数的Hf/Si3N4涂层相对于镁合金基体而言,其耐腐蚀性均得到了显著的提升。随着交替层数的增加,Hf/Si3N4涂层逐渐向低腐蚀电流密度方向移动。但是当层数n=20时,腐蚀电流密度进行了反弹,其原因主要是由于Hf子层的细化导致晶界的显著负面影响,从而导致孔隙率略有增加。
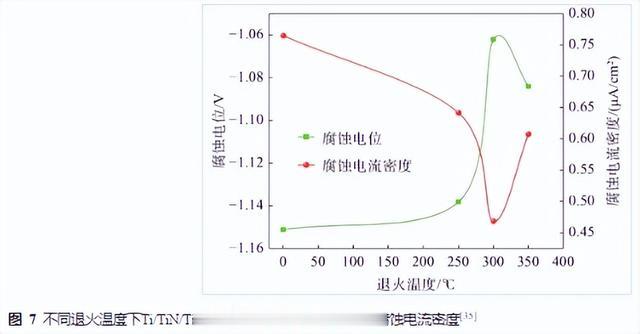

3. 结束语在利用磁控溅射技术制备金属和金属/陶瓷薄膜的研究中,虽然不同的实验设备和实验条件对实验结果存在一定的影响,但实验参数对薄膜的影响规律大体一致。溅射时间越长薄膜越厚,但溅射时间过长会导致结合强度下降,可通过改变合适的偏压来提高薄膜与基体结合力,但过高的偏压会致使薄膜的耐腐蚀性下降。适当的增加温度可提高薄膜的耐腐蚀性,但过高的温度会导致薄膜的厚度降低。适当的气体流量比有助于提高金属/陶瓷复合涂层的耐蚀耐磨性能。金属/陶瓷复合涂层中过渡层Al层在耐腐蚀性方面要优于Ti层,过渡层Ti层在耐磨性方面要优于Al层。目前,磁控溅射金属/陶瓷复合薄膜与镁合金基体在结合和性能稳定方面仍有不足。因此,未来对镁合金表面磁控溅射金属/陶瓷复合薄膜的研究还需集中在以下3个方面:
(1)国内外对于镁合金表面磁控溅射金属/陶瓷复合薄膜的研究主要集中在单一工艺参数和薄膜材料选择上,对于工艺参数优化和金属过渡层与陶瓷的界面相互作用机制还比较欠缺。因此,对于制备工艺方面,应合理优化工艺参数,得出工艺参数的最佳配合;深入研究金属层与陶瓷层其相互作用的沉积机理,建立有效的沉积模型,从而制备出性能更加稳定优良的金属/陶瓷复合薄膜。
(2)由于腐蚀过程非常复杂,因此未来可通过BP人工神经网络算法对薄膜的耐腐蚀性能进行预测,通过建立腐蚀环境介质、薄膜的组织结构与其耐腐蚀性之间的关系,来评价不同类型薄膜在腐蚀介质中的腐蚀程度和腐蚀速率,评估薄膜的长期保护性。
(3)由于磁控溅射制备的薄膜会不可避免的存在孔隙等缺陷,会直接影响薄膜的耐腐蚀性能。为此,可通过掺杂的方式来提高薄膜的致密度,从而增强其薄膜的耐腐蚀性能。
文章来源——金属世界