导语:
精益化管理是生产现场管理的一个良方,主要就是要落实“细节管理”和“持续改善”这两大理念。在深刻理解“细节决定成败”的理念和了解应用PDCA循环进行“持续改善”的方法之后,就要用更具体的方法与工具来落实精益化管理。
利器一:5S管理,夯实现场精益化管理的基础。
(一)5S就是整理、整顿、清扫、清洁、素养五个项目,简称5S。
没有实施5S的工厂,触目可及地就可感受到现场的脏乱,例如地板粘着垃圾、油渍或切屑等,日久就形成污黑的一层,零件与箱子乱摆放,起重机或台车在狭窄的空间里游走。再如,好不容易导进的最新式设备也未加维护,经过数个月之后,也变成了不良的机械,要使用的工夹具、计测器也不知道放在何处等等,显现了脏污与零乱的景象。员工在作业中显得松松垮垮,规定的事项,也只有起初两三天遵守而已。改变这样工厂的面貌,实施5S活动最为适合。
(二)5S的定义与目的:
1S-整理 定义:区分要与不要的东西,现场除了要用的东西以外,一切都不放置。一个概略的判定原则,是将未来30天内,用不着的任何东西都可移出现场。
目的:将"空间"腾出来活用
2S-整顿 定义:要的东西依三定原则(定品、定量、定位)摆放整齐,明确数量,明确标识。
目的:不浪费"时间"找东西
3S-清扫 定义:清除现场内的脏污,并防止污染的发生
目的:消除"脏污",保持现场干净、明亮
4S-清洁 定义:将上面3S实施的做法制度化,规范化,维持其成果
目的:通过制度化来维持成果
5S-素养 定义:培养文明礼貌习惯,按规定行事,养成良好的工作习惯
目的:提升"人的品质",成为对任何工作都讲究认真的人
(三)5S的五大效用
①5S是最佳推销员:被顾客称赞为干净整洁的工厂、对这样的工厂有信心,乐于下订单于口碑相传,会有很多人来工厂参观学习 整洁明朗的环境,会使大家希望到这样的厂工作
②5S是节约家: 降低很多不必要的材料以及工具的浪费减少"寻找"的浪费,节省很多宝贵的时间 ·能降低工时,提高效率;
③5S对安全有保障: 宽广明亮,视野开阔的工作现场,所有物资一目了然;遵守堆积限制,危险处一目了然;走道明确,不会造成杂乱情形而影响工作的顺畅。
④5S是标准化的推动者
规范现场作业,大家都正确的按照规定执行任务,程序稳定,带来品质稳定,成本也安定。⑤5S形成令人满意的职场
明亮、清洁的工作场所,员工动手做改善、有成就感,造就现场全体人员进行改善的气氛。
(四)5S管理的综合效果
1、整理
将现场需要的东西与不需要的东西分开,把不必要的东西处理掉。如撤去不需要的设备、管线、工具、模型和个人物品等。
2、整顿
把要用的东西,根据使用频度分别放置,使常用的东西能及时、准确地取出,保持必要时马上能使用的状态和谁都能了解的状态。如放置场所与通道的标志、放置物品及其管理者的标志等。
3、清扫
去除现场的脏物、垃圾、污点,经常清扫、检查,形成制度,采取根治污物的对策。如彻底改善设备漏水、漏油、漏气以及易落下灰尘等状况。
4、清洁
企业、现场、岗位、设备时时保持干净状态,保持环境卫生。如定期进行卫生、安全检查,采取防止污染、噪声和震动的对策,使现场明亮化。
5、素养
要加强修养,美化身心,做到心灵美、行为美。人人养成良好的习惯,自觉遵守和执行各种规章制度和标准。
(五)5S推行步骤:
1.成立推行组织;
2.拟定推行方针及目标;
3.拟定工作计划及实施方法;
4.活动前的教育宣传造势;
5.推进实施;
6.活动评比办法确定;
7.检查、评比及奖惩;
8.检讨与修正;
9.纳入定期管理活动中。
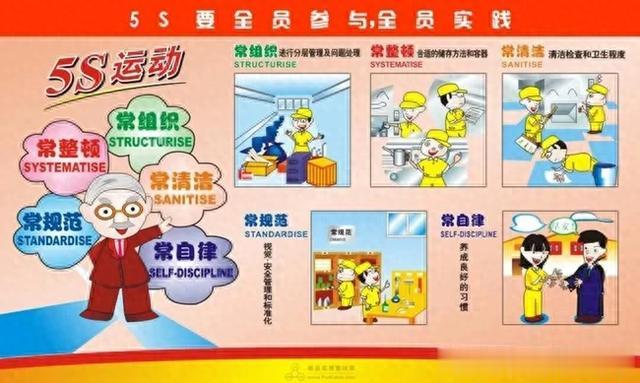
利器二:可视化管理,打造一目了然的精益化现场。
可视化管理,一句话解释:将需管理的对象用一目了然的方式来体现。
可视化管理也称为:目视管理、一目了然管理、一眼即知的管理、看得见的管理。
可视化标准,就是将可视化对象的符号或(和)图形的设计输出,用规格、材质、色彩、字体、图例、实例等方式来具体表述,以实现可视化管理的标准化。
可视化管理的作用:
1、迅速快捷地传递信号
2、想要管理的地方一目了然
3、易知正常与否,谁都能指出正常与否
4、从远处就能辨认出正常与异常
5、形象、直观地将潜在问题和浪费显现出来,任何人使用都同样方便,任命人都容易遵守,容易更改
6、有助于把作业场所变得整洁明亮
7、有助于维持安全愉快的工作环境
8、客观、公正、透明化,有助于统一认识,提高士气
9、营造员工和客户满意的场所
10、明确告知应用做什么,做到早期发现异常情况,使检查有效
11、防止人为失误或遗漏并始终维持正常状态
12、通过视觉,使问题点和浪费现象容易暴露,事先消除各类隐患和浪费。
可视化管理目的:
①明确告知应该做什么,做到早期发现异常情况,使检查有效;
②防止人为失误或遗漏,并始终维持正常状态;
③通过视觉,使问题点和浪费现象容易暴露,事先预防和消除各种隐患和浪费。
可视化管理的原则:
①视觉化:彻底标示、标识,进行色彩管理;
②透明化:将需要看到的被遮隐的地方显露出来,情报也如此;
③界限化:即标示管理界限,标示正常与异常的定量界限,使之一目了然。
进行可视化管理检查的十个要点:
1、在远处也清楚可见吗?
2、需要加强管理的部位标示了没有?
3、好坏状态任何人都能指正吗?
4、任何人都能使用并使用方便吗?
5、任何人都能遵守并对出错时能及时纠正吗?
6、使用可视化道具能增添现场的明亮整洁吗?
7、是否按“(模拟)道具→设置→(模拟)使用”顺序进行?
8、有不足点时是否进行改善﹑直到(模拟)道具符合要求位置?
9、没有不足点时耐久性材料制作/设置/使用了吗?
10、可视化与公司标准一致吗?
利器三:TPM全员生产维护,实现设备“零故障”。
全员生产维护是以提高设备综合效率为目标,以全系统的预防维修为过程,全体人员参与为基础的设备保养和维修管理体系。
TPM活动由“设备保全”、“质量保全”、“个别改进”、“事务改进”、“环境保全”、“人才培养”这6个方面组成,对企业进行全方位的改进。
(一) TPM五大要素:
1、致力于设备综合效率最大化的目标;
2、在设备一生建立彻底的预防维修体制;
3、由各个部门共同推行;
4、涉及每个雇员,从最高管理者到现场工人;
5、通过动机管理,即自主的小组活动来推进。
(二) TPM的具体含义:
1.以追求生产系统效率(综合效率)的极限为目标,实现设备的综合管理效率即OEE的持续改进;
2.从意识改变到使用各种有效的手段,构筑能防止所有灾害、不良、浪费的体系,最终构成“零”灾害、“零”不良、“零”浪费的体系;
3.从生产部门开始实施,逐渐发展到开发、管理等所有部门;
4.从最高领导到一线作业者,全员参与。
(三)开展TPM的八大支柱:
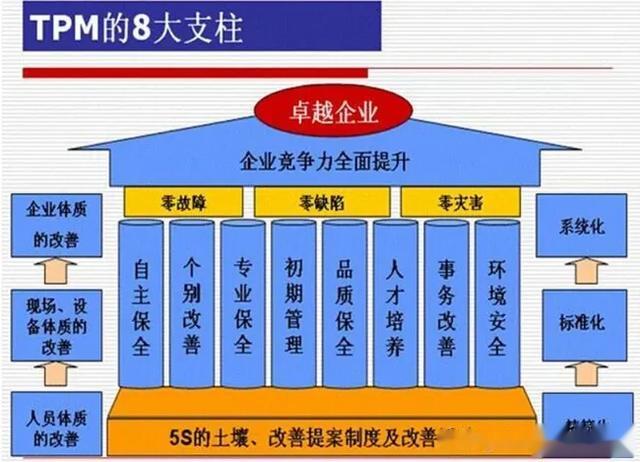
(四)TPM的主要特点
1、全效率:指设备寿命周期费用评价和设备综合效率。
2、全系统:指生产维修系统的各个方面都要包括在内。即是PM、MP、CM、 BM等都要包含。
3、全员参加:指设备的计划、使用、维修等所有部门都要参加,尤其注重的是操作者的自主小组活动。
利器四:防错法(防呆法),实现产品质量“零缺陷”。
(一)防呆法:其义即是防止呆笨的人做错事。连愚笨的人也不会做错事的设计方法,故又称为愚巧法。
(二)防呆装置:为了实现生产合格率100%的目标,必须在模具、工装夹具方面多用脑筋,添置防止不合格品发生的设备,这就是防呆装置。
(三)防呆装置的作用:
首先,使任何的错误,绝不会发生。其次,使错误发生的机会减至最低程度。
1.具有即使有人为疏忽也不会发生错误的构造──不需要注意力。
2.具有外行人来做也不会错的构造──不需要经验与直觉
3 具有不管是谁或在何时工作都不会出差错的构造──不需要专门知识与高度的技能。
(四)防呆装置的种类:
① 出现操作失误物品就装不上工装夹具。
② 物品不符合规格,机器就不会加工。
③ 出现操作失误,机器就不会加工。
④ 自动修正操作失误、动作失误,然后开始加工。
⑤ 在后工序检查出前工序不合格,前工序停止操作。
⑥ 作业上如有遗漏,后工序停止动作。
(五)实施“防呆法”的基本原则:
1.使作业的动作轻松
难于观察、难拿、难动等作业即变得难做,变得易疲劳而发生失误。区分颜色使得容易看,或放大标示,或加上把手使得容易拿,或使用搬运器具使动作轻松。
2.使作业不要技能与直觉
需要高度技能与直觉的作业,容易发生失误.考虑治具及工具,进行机械化,使新进人员或支持人员也能做不出错的作业。
3.使作业不会有危险
因不安全或不安定而会给人或产品带来危险时,加以改善使之不会有危险。如果马虎行之或勉强行之而发生危险时,设法装设无法马虎或无法勉强的装置。
4.使作业不依赖感官
依赖像眼睛、耳朵、感触等感官进行作业时,容易发生误。制作治具或使之机械化,减少用人的感官来判断的作业。如果一定要依赖感官的作业,设法使之能做二重三重的判断。
(六)推行防呆法的实施步骤
【步骤1】发现人为疏忽
【步骤2】设定目标
【步骤3】调查人为疏忽的原因
【步骤4】提出防错法的改善方案
【步骤5】实施改善方案
【步骤6】确认活动成果。
【步骤7】维持管制状态。
(七)“防呆法”原理
1、基本原理:
(1)排除化:剔除会造成错误的要因。
(2)替代化:利用更确实的方法来代替。
(3)容易化:使作业变得更容易、更合适、更独特,或共同性以减低失败。
(4)异常检出:虽然已经有不良或错误现象,但在下一制程中,能将之检出,以减少或剔除其危害性。
(5)缓和影响:作业失败的影响在其波及的过程中,用方法使其缓和或吸收。
2、应用原理:
(1)断根原理:将会造成错误的原因从根本上排除掉,使绝不发生错误。
(2)保险原理:用二个以上的动作必需共同或依序执行才能完成工作。
(3)自动原理:以各种光学、电学、力学、机构学、化学等原理来限制某些动作的执行或不执行,以避免错误之发生。
(4)相符原理:用检核是否相符合的动作,来防止错误的发生。
(5)顺序原理:避免工作的顺序或流程前后倒置,可依编号顺序排列,可以减少或避免错误的发生。
(6)隔离原理:以分隔不同区域的方式,来达到保获某些地区,使其不能造成危险或错误的现象发生。隔离原理亦称保获原理。
(7)复制原理:同一件工作,如需做二次以上,最好采用“复制”方式来达成,省时又不错误.
(8)层别原理:以线条的粗细或形状加以区别;以不同之颜色来代表不同的意义或工作的内容。
(9)警告原理:有不正常的现象发生,能以声光或其它方式显示出各种“警告”的讯号,以避免错误的发生。
(10)缓和原理:以各种方法来减少错误发生后所造成的损害,虽然不能完全排除错误的发生,但是可以降低其损害的程度。
利器五:KYT危险预知训练,实现人员“零事故”。
1、什么是KYT活动?
KYT活动是针对生产的特点和作业工艺的全过程,以其危险性为对象,以作业班组为基本组织形式而开展的一项安全教育和训练活动,它是一种全员性的“自我管理”活动,目的是控制作业过程中的危险,预测和预防可能发生的事故。
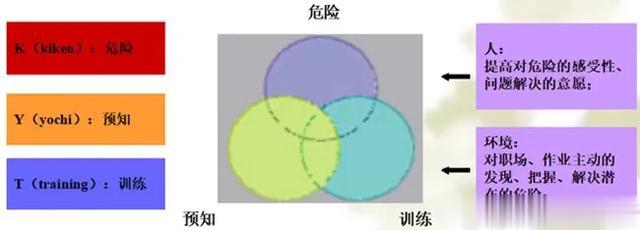
2、KYT活动中的4R是什么?
1R:潜在着怎样的危险? 找出危险(把握现状)
2R:主要的危险是什么? 找出危险的关键点(本质追究)
3R:如果是你该怎么办? 对策是什么?(制定对策)
4R:我们这样去做吧! 确定目标(目标设定)
利器六:动作经济原则,提升现场作业效率。
动作经济原则包含如下4个基本原则:
①减少动作数量。
②同时使用身体的各个部位。
③缩短动作距离。
④尽量使动作轻松舒适。
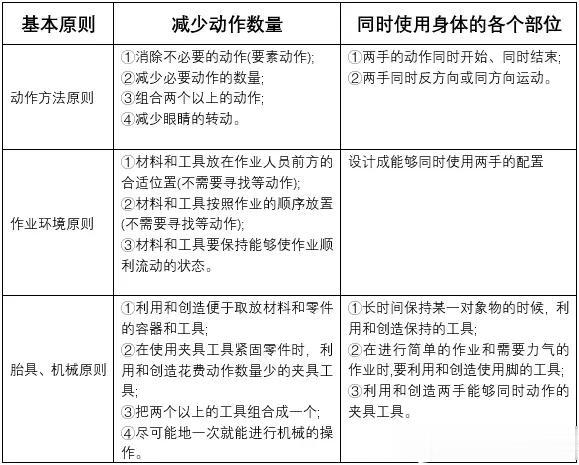
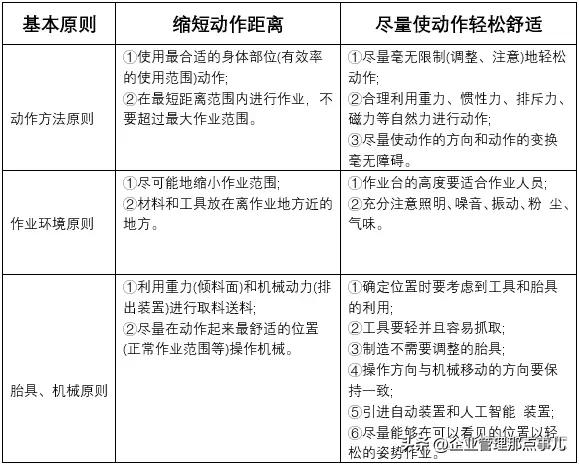
利器七:OEC管理,实现日常管控的精益化。
(一)管理内涵
O—Overall 全方位。
E—(1)Everyone 每人;
(2)Everything 每件事;
(3)Everyday 每天。
C—(1)Control 控制;
(2 ) Clear 清理。
“OEC”管理法也可表示为:日事日毕 日清日高。即:每天的工作每天完成,每天工作要清理并要每天有所提高。
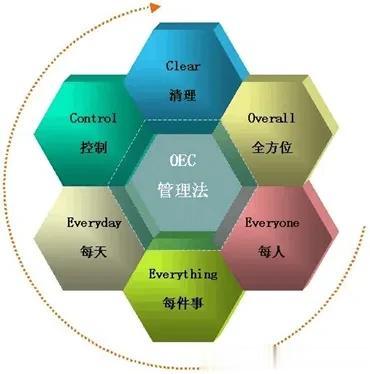
(二)管理体系
“OEC”管理法由三个体系构成: 目标体系→日清体系→激励机制。
首先确立目标;日清是完成目标的基础工作;日清的结果必须与正负激励挂钩才有效。
这实际上是一个目标管理体系,总目标是“日高”,即企业管理水平和企业综合素质水平以及员工个人素质持续提高,而其基础是“日清”,即使得企业日常工作的每一件事都达到有序状态和受控状态。达到“日高”的目的和巩固“日清”的基础又是通过在每天的日常工作中,全面控制企业里每个人、每件事的具体行为过程而达到的。
OEC管理法始终贯穿着PDCA循环,通过设定目标、设计达到这些目标的具体措施和方法——付诸实施——检查、纠正和改进计划及修正目标,从而使日常工作中每件事都处于受控状态,并达到持续提高的目的。
(三) 基本方法:
分别是日清工作法和区域管理法。
日清工作法包括三方面的内容,即:当日工作当日清、班中控制班后清、员工自清为主组织清理为辅。
区域管理法亦称定置管理法,即依据生产及工作对现场的要求,为便于生产或工作,按照工艺要求或工作要求将区域进行功能划分,并用专门的区域线进行标识,指定专门的区域作为专门用途的场所。在该场所内留下必要的,去除多余的或不必要的,留下的按工艺或工作最便利的要求摆放整齐。
(四) 基本原则:
一是闭环原则,即凡事都要讲究善始善终,都必须有一个PDCA循环(即:计划-实施-检查-总结)的过程,达到螺旋式上升的目的;
二是比较分析原则,纵向与自己的过去比,横向与同行业比、与同类企业比、与相关部门比、与其他员工比,认识到没有比较就没有发展的道理;
三是不断优化的原则,根据木桶理论,找出薄弱项,并及时整改,以期提高全系统的水平。
利器八:精益生产,精益化的生产制造。
一、 精益生产(Lean Production)是一种以减少生产过程中的浪费为核心,通过优化生产流程,提高生产效率和质量的生产管理模式。精益生产主张去除生产过程中的浪费,包括时间浪费、人力浪费、物料浪费、能源浪费等等,从而达到节约成本和提高生产效率的目的。
二、 精益生产的原则
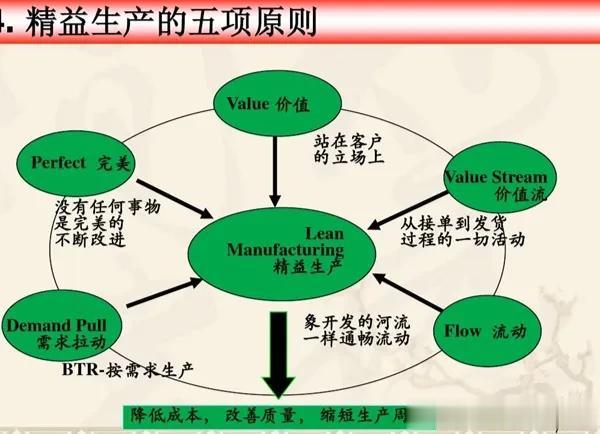
三、精益生产的四个特点:
1 消除一切浪费,追求精益求精
精益生产的特点是消除一切浪费,追求精益求精和不断改善。去掉生产环节中一切无用的东西,每个工人及其岗位的安排原则是必须增值,撤除一切不增值的岗位。
2 强调人的作用,发挥人的潜力
精益生产方式把工作任务和责任最大限度地转移到直接为产品增值的工人身上。而且任务分到小组,由小组内的工人协作承担。要求工人精通多种工作,减少不直接增值的工人,并加大工人对生产的自主权。当生产线发生故障,工人有权自主决定停机,查找原因,做出决策。小组协同工作使工人工作的范围扩大,激发了工人对工作的兴趣和创新精神,更有利于精益生产的推行。
3 零浪费目标
精益生产则认为库存是企业的"祸害",其主要理由是:
①库存提高了经营的成本;
②库存掩盖了企业的问题。
生产中的无效劳动和提前进入库存的过剩劳动都是浪费。为杜绝这些浪费,精益生产方式要求毫不留情地撤掉不直接为产品增值的环节和工作岗位。
4 追求完美,永不满足
精益生产方式则把"无止境地追求完美"作为经营目标,追求在产品质量、成本和服务方面的不断完善。这一思想是区别于大量生产方式的重要特征,也是精益生产走向成功的精神动力。准时化生产方式(JIT)和不断改进流程(CIP)是精益生产追求完美的思想体现。
四、企业如何实现精益生产?
1、建立全员参与的文化
建立全员参与的文化,使每个员工都能够全程参与到生产流程中,发挥其智慧和创造力。通过提高员工参与的积极性和投入度,从而实现生产效率和质量的提升。
2、识别和消除浪费
企业应当对生产过程进行全面的分析和识别,找出生产过程中存在的浪费,包括时间浪费、物料浪费等等。然后采取相应的措施,消除这些浪费,提高生产效率和质量。
3、优化生产流程
企业应当将生产过程划分为一个个小步骤,优化每个步骤,从而提高整个生产流程的效率和稳定性。通过优化生产流程,企业可以实现节约成本和提高生产效率的目的。
4、进行持续改进
精益生产主张进行持续改进,不断优化生产过程,从而实现效率和质量的提升。企业应当定期进行生产流程分析和评估,找出不足之处,并采取相应的措施进行改进。
5、培养员工技能
企业应当注重员工的技能培养,提高员工的专业技能和素质水平。通过不断提高员工的技能和素质,从而提高员工的生产效率和质量。
总之,精益管理是一种以客户为中心、追求高效率、持续改进的管理方法。
它通过消除浪费、提高质量和效率,实现企业的长期成功。精益管理需要全员参与,需要一系列的工具和技术的支持。只有全员参与,才能实现精益管理的目标。
(全文完)