金锡合金熔封中的焊料内溢控制
肖汉武 陈婷 颜炎洪 何晟
(无锡中微高科电子有限公司 宜兴吉泰电子有限公司)
摘要:
金锡合金熔封是气密封装的主要封帽技术之一,焊料内溢是金锡合金熔封过程中的普遍现象。焊料内溢会缩小键合引线与盖板的间距,严重的甚至会引起短路,偶尔也会导致粒子碰撞噪声检测 (PIND) 试验不合格。讨论了焊料内溢产生的原因,并从密封设计、封帽夹具、盖板镀层等方面提出了内溢控制措施。
1 引言
金锡合金焊料因其优异的焊接性能,被广泛应用于集成电路高可靠气密封装中,如芯片共晶焊接和镀金盖板的气密封帽。金锡合金作为一种用于气密封装的焊接材料,有着极佳的密封性能和密封合格率。相较于平行缝焊气密封帽工艺,金锡焊料熔封工艺在密封合格率及可靠性方面有明显的优势,其密封合格率通常在 99.5%以上,此外在抗盐雾耐蚀能力方面也有更好的表现。然而采用金锡合金熔封结构的器件普遍存在焊料内溢现象,在焊接过程中金锡焊料在盖板内侧出现无规则的铺展,甚至呈现泪滴状,焊料内溢严重时会伸展至封装芯腔的键合引线上方。可通过 X 射线探测金锡焊料内溢现象,或者通过开盖方式进行确认。
严重的焊料内溢会给器件的可靠性带来隐患,在粒子碰撞噪声检测(PIND)试验中某些金锡合金熔封器件的失效多与金锡焊料的多余物相关[1],特别是器件在 PIND 筛选试验过程中,部分内溢焊料在冲击脉冲的振动作用下有可能脱离盖板落入封装内腔,形成可移动的多余物。可移动的多余物有可能直接导致内部互连短路或降低相邻 I/O 间的绝缘电阻,造成器件功能失效或电性能异常;大尺寸的多余物有可能损伤器件的内部引线,增加内部引线开路的风险。有研究表明,形成金锡焊料多余物的原因有熔封过程中因有机物沾污导致的焊料飞溅[2]、装片焊接材料的卷曲多余凸起[3],此外金锡焊料多余物的另一个重要来源为焊料内溢。因此,封装过程中对金锡焊料内溢现象进行有效控制是降低 PIND 失效率的一个重要途径。
近年来,国内有关金锡熔封方面的研究主要集中在焊接界面的空洞形成原因及其控制方法,而金锡熔封工艺中较常见的焊料内溢问题并没有引起足够的关注。本文从封装结构设计、密封工艺、盖板结构、镀层等方面对焊料内溢的形成原因及控制方法进行了研究,并取得了一定的改善效果。
2 焊料内溢形成原因
2.1 焊料内溢缺陷
典型的采用金锡合金焊料熔封的封装结构如图 1所示。
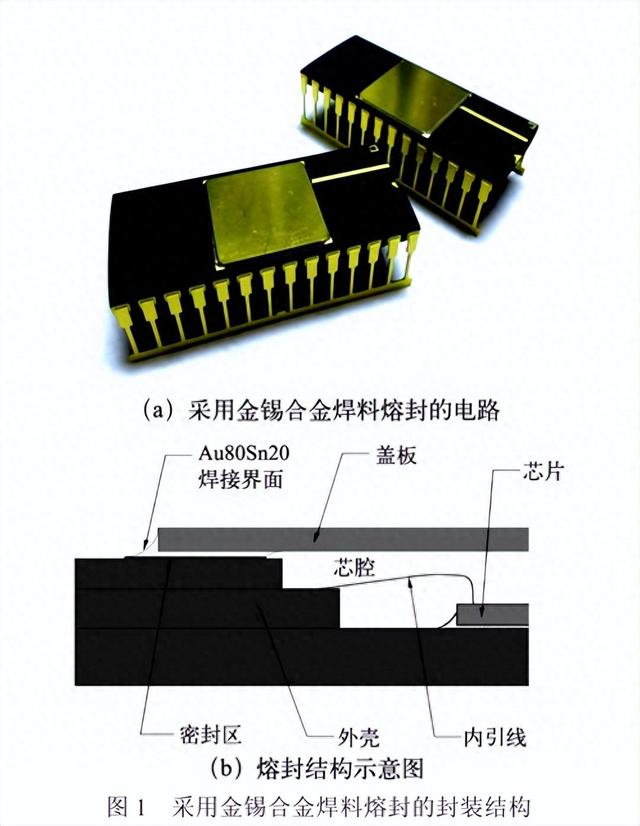
通过点焊方式将金锡焊料预固定在镀金盖板上。在盖板上方施加一定的压力,金锡焊料熔化后沿着陶瓷外壳的金属化密封区、镀金盖板及其之间的缝隙流动,最终在盖板周围形成一个完整、均匀、连续且具有弯月面外形的密封界面。理想状态下的盖板内侧焊料应均匀、连续地铺展,但实际的焊料铺展并不连续、均匀,往往为不规则甚至呈泪滴状铺展,并延伸至芯腔键合指的上方。这种芯腔键合指上方的焊料铺展现象即为焊料内溢。焊料内溢现象如图 2 所示。
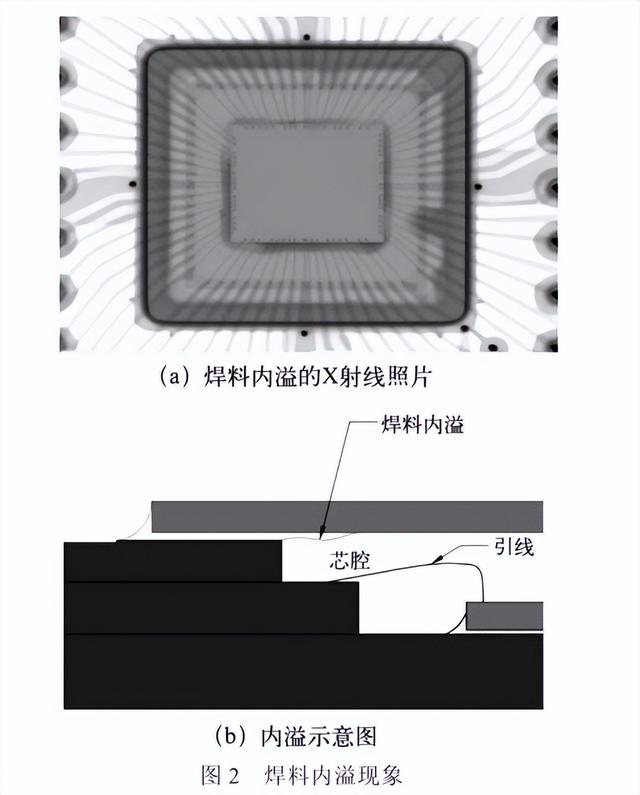
2.2 焊料内溢形成机理
金锡焊料 Au80Sn20 在不低于 280 ℃的高温下开始熔化,熔融焊料沿着密封区的方向流动,同时向密封区的内侧、外侧铺展。向外溢出的焊料向密封区外侧的金属化表面及盖板边缘表面 2 个方向同时铺展,形成弯月面的密封界面,这就是所谓的焊料外溢。过度的焊料外溢则呈现出类似反浸润的密封界面,比较严重的情况是焊料铺展至盖板表面的上边缘,形成焊料爬盖。焊料沿陶瓷外壳密封区的内侧铺展时,其流动会受到密封区宽度的限制,但盖板一侧的内侧流动却不受限制。
铅锡类低温焊料在镀金层界面上迅速铺展,金锡焊料 Au80Sn20 在熔化状态下的流动性相对较差,焊料的铺展范围较小。为了获得较好的焊接界面,金锡焊料 Au80Sn20 在熔封时,需在盖板上方施加足够的压力,压力不足时容易在焊接界面形成空洞。在熔封过程中施加压力的方式通常有 2 种,一种是重力块施压,一种是通过具有弹簧结构的夹子在盖板上施加压力。由于金锡焊料 Au80Sn20 熔封时所需的压力在数十克力以上,受到尺寸限制,重力块的施压方式一般只适用于尺寸较小的器件,如盖板尺寸小于 3mm×3mm 的器件。大多数器件都采用具有弹簧结构的夹子来提供夹持力,熔封时使用的典型的弹簧夹子如图3 所示。其采用耐高温的 304 不锈钢等制作,夹持力一般有 1 磅(约 450 g)、1.5 磅(约 680 g)、2 磅(约 907 g)等。为改善焊接界面的空洞现象,有时会采用多个夹子一起夹持的施压方式(如图 4 所示)。多个夹子的夹持提供了足够大的焊接压力,但焊料表面实际承受的压力并不均匀,尤其当外壳密封区的平面度较大时,这种压力的均匀性更差。

按照 GJB 1420B—2011 规定[4],金属化密封区或金属密封区的平面度须小于 50 μm,焊料环的厚度通常为 50 μm。当平面度较大时,在某个区域的焊料与密封区之间会存在较大的间隙。在夹子的夹持力作用下,位于间隙较大处的焊料受到的压力较小,相反,位于间隙较小处的焊料受到的压力很大,出现压力不均匀的现象。当焊料熔化时,焊料在受到较大压力的区域迅速铺展,在受到压力较小的区域则很难铺展。由于焊料外溢时,焊料沿密封区外侧金属化表面及盖板侧壁金属化表面 2 个方向铺展,侧壁金属化表面的高度对焊料的上爬有明显的限制作用,同时外壳密封区的外侧与盖板外侧的间隙(俗称留白区)通常小于盖板厚度,其同样起到限制焊料流动的作用,因此焊料外溢受到 2 方面的限制。当 2 个金属化表面镀层均匀、洁净时,焊料外溢均匀、连续,形成一个较完美的弯月形界面。而焊料向密封区内侧流动时,由于盖板内侧为全镀金区,焊料沿内侧方向的流动不再受到限制。盖板受到的压力越大,焊料向内侧铺展越多。由于没有侧向的限制,焊料的流动仅发生在盖板表面,加上压力不均匀的因素,还会出现焊料聚集、呈现球状的现象。这是焊料内溢的主要原因。
通过观察可知,当芯片采用共晶焊接方式时,同样的封装几乎很少出现焊料内溢,这是因为采用共晶焊工艺的器件其封装内腔几乎不存在有机气体等的释放,盖板内外 2 侧的焊接气氛很接近。采用高温导电胶装片的器件,在熔封过程中导电胶会释放部分有机气体及少量氧气,使得熔融态焊料的表面张力增大,进而导致焊料的不规则流动。这是采用高温导电胶装片的器件中出现 焊料内溢现象的一 个重要原因。
3 焊料内溢的危害
当密封器件中出现焊料内溢时,可能在盖板内侧出现焊料聚集。当焊料聚集的高度较大时,盖板与内引线之间的间隙变小,表现为内部目检不合格。除外观不良外,焊料内溢的主要危害是增加了器件内部金属多余物的形成概率。金属多余物的直接危害是造成芯片内部的短路。当多余物正好落在 2 个相邻键合指的间隙中时,2 者之间的绝缘距离缩短,漏电电流有可能增大。具体表现为 PIND 失效和与内引线短接导致的短路。
3.1 不符合内部目检标准要求
按照 GJB 548C—2021 方法 的 2010.2 内 部 目 检(单片电路)规定[5]:对于 B 级器件,键合内引线与封帽封接平面之间的距离须小于引线直径;对于 S 级器件,该距离须小于引线直径的 2 倍。在实际生产过程中的内控标准较之更加严格。
某些器件由于尺寸的限制,整体厚度较小,封帽平面与引线之间的设计距离偏小。当焊料出现内溢后,金属盖板与键合引线之间的间隙更小,容易出现不满足标准要求的情况。
3.2 PIND 失效
由于焊料内溢,部分金锡焊料进入封装腔体上方的盖板周围。与外壳密封区的焊料相比,此区域的焊料处于悬空状态。在 PIND 试验过程中,高频振动使得内溢的焊料随着盖板发生轻微的位移。经过反复的上下振动,脆性的金锡焊料在反复的高频振动下出现局部脱落,形成可移动的金属多余物,PIND 试验中的金锡焊料多余物如图 5 所示。
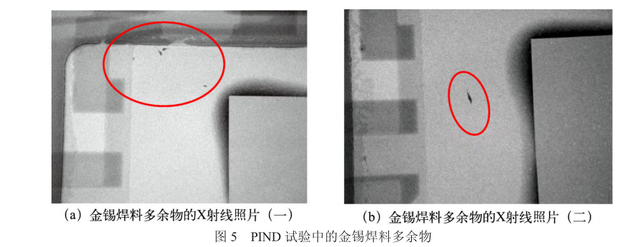
3.3 与内引线短接
焊料内溢严重时呈现泪滴状,内溢焊料在盖板内侧聚集形成一定高度的焊料球。某些采用多层键合指结构的外壳,由于顶层键合指的台阶高度较小,盖板平面与键合丝的间隙偏小。一旦聚集的焊料球高度超过键合指的台阶高度时,熔融的焊料接触到某根键合丝,就会包裹丝线形成短接。
图 6 为焊料内溢导致的内引线短接的照片,其中内溢的焊料完全覆盖键合指区域,键合焊点被金锡焊料完全包裹,盖板与该引线短接,导致功能失效。该样品在开盖过程中甚至还出现键合指从外壳端脱落的现象。
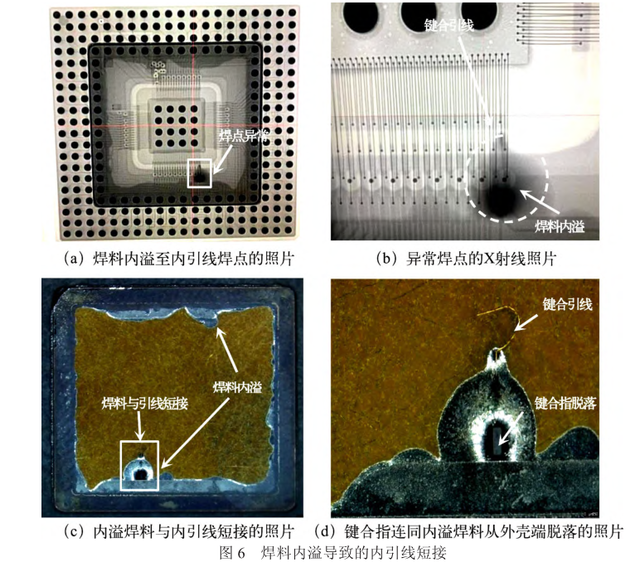
4 焊料内溢的控制措施
针对焊料内溢的形成机制,从密封设计、封帽夹具、焊接限流设计以及采用预熔焊料盖板等方面进行了改善试验。
4.1 外壳密封区与焊环结构尺寸的匹配性设计
一些电路发生 PIND 失效的主要原因为外壳密封区的尺寸与盖板尺寸不匹配,即盖板焊料内径的尺寸偏小,甚至焊料内径小于密封区内径。如某款 PIND 失效产品的盖板焊料内径的边长比密封区内径的边长小 0.38 mm,即盖板内侧的 2 边有 0.30 mm 左右的焊料伸入到外壳键合指的上方。对该盖板焊料的尺寸进行更改,更改后的焊料内径比密封区内 径 增 大 了0.20~0.50 mm,焊料环与密封区的匹配性设计实例如图 7 所示。优化后的盖板在封帽后焊料内溢明显减少,PIND 失效问题得以解决。
封装设计中外壳密封区尺寸与盖板尺寸不匹配往往是由于设计人员选用了通用尺寸的盖板,而非根据外壳密封区尺寸设计与之相匹配的盖板。因此,在封装设计评审中必须对外壳与盖板的匹配性进行仔细评估,必要时应定制尺寸匹配的盖板。
外壳与盖板的匹配性设计可参考以下规则:
(1)避免密封区内侧与芯腔平齐。当尺寸允许时,外壳密封区的内径应尽量大于腔体的外径,即密封金属化区的内侧与腔体的内边缘保留明显间隙。间隙越大,焊料内溢进入腔体上方的可能性越小。
(2)盖板焊料的内径须大于密封区的内径,焊料内径越大,焊料内溢越少,但焊料内径过大时,焊料密封区的宽度减小,产生焊接空洞的风险增大。将焊料内侧 边缘 与 密 封 区内 侧 边缘 的间 隙 控制 在 0.10~0.25 mm 较合适。
(3)盖板内径须小于密封区外径,将盖板边缘与密封区外侧边缘的间隙控制在 0.10~0.25 mm。当间隙小于 0.10 mm 时,焊料可能会流淌至盖板表面,即产生爬盖问题。
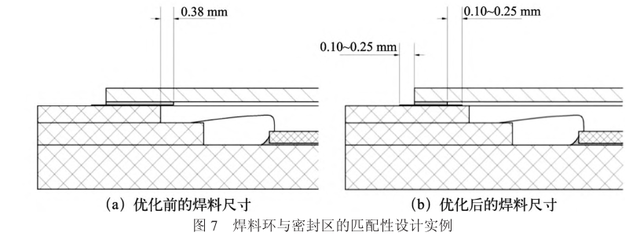
4.2 密封工艺优化
绝大部分陶瓷外壳的密封区为金属化焊环结构而非金属焊环结构。陶瓷外壳在烧结过程中不可避免地存在翘曲现象(尤其是大尺寸外壳)。金属化密封区的平面度有可能超过 0.04 mm,而金属盖板的平面度很小,因此盖板与密封区接触时四周的间隙并不均匀。焊料受力不均匀会直接导致焊料内溢。在金锡熔封过程中,为减少密封区的空洞通常会加大盖板夹持力。通过增加夹子的夹持力虽然可改善焊料的铺展能 力并减少空洞,却会带来 PIND 失效和焊料爬盖问题[6]。
为避免夹持力的局部集中,本文设计了一种专用的垫片,垫片通过多个间断的接触面而非整个周边与盖板接触,封帽夹子的夹持力通过垫片的多个接触面分散在盖板四周,使得盖板四周受力更为均匀。
针对不同尺寸的盖板,设计了不同数量的接触面垫片。盖板的尺寸越大,接触面的数量越多。实践证明,这种垫片对改善密封区平面度较大的外壳的焊料内溢效果明显。
图 8 为具有 16 个接触面的封帽垫片示意图。垫片上间断分布的接触面避免了整体接触时的局部压强过大问题,虽然总的接触面积变小,但实际的压力分布却更加均匀。
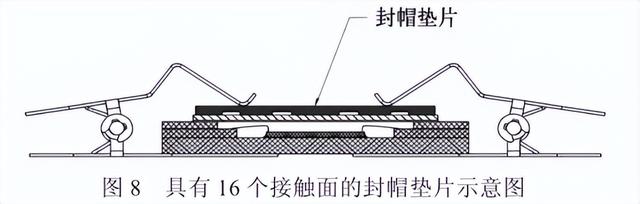
此外,针对焊料内径尺寸与外壳内腔尺寸非常接近的器件,在封帽过程中采用器件倒置方式,在焊料内溢过程中,可以减少熔融焊料在重力作用下形成的焊料聚集高度,降低与内引线短接的风险。
4.3 局部镀金
如第 2 节所述,出现焊料内溢是因为盖板内侧为全镀金的镀层结构,焊料熔化时受到不均匀的压力驱动,并且只能在镀金层界面流淌、铺展。因此限制焊料的流动区域或路径,可以达到控制焊料内溢的目的。
限制焊料的流动主要有 3 种实现方式:(1)选择性局部镀金技术;(2)镀层激光熔蚀技术;(3)非金属盖板的局部金属化技术。
选择性局部镀金是指盖板的上表面、四周的侧壁、焊料封接区均采用镀金表层,盖板的下表面内侧采用镀镍表层,图 9 为局部镀金示意图。由于金锡焊料在镀镍层表面的铺展远不及镀金层,焊料向盖板内侧的流动受到镍镀层的阻挡,可以较大程度减少焊料内溢。也可以选择仅在盖板四周的侧壁、焊料封接区镀金,其他表面为镀镍结构。
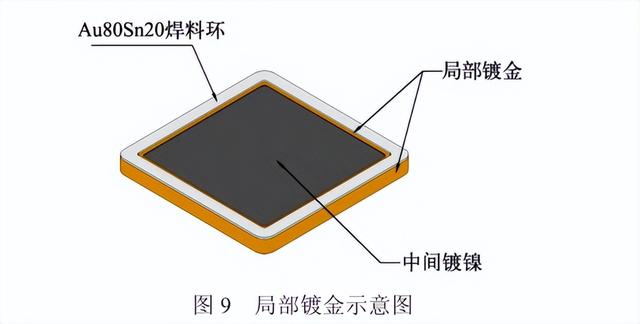
镀层激光熔蚀技术是盖板采用标准的全镀金结构,通过激光在焊料内侧边缘形成一个具有一定宽度的限制区,该区域表面的金层被高能激光熔蚀暴露出镍镀层,具有一定宽度的镍镀层构成了金锡焊料的内溢阻挡层。这是日立金属公司开发的“EX-lid”方案,其初衷是减少金锡焊料的用量,在减少焊料厚度的同时也可以减少焊料内溢。激光熔蚀形成的焊料内溢阻挡层如图 10(a)所示,EX-lid 在封帽前其焊料内侧边缘有一个明显的激光熔蚀区,该区域表面的镀金层被激光去除,暴露出的底部镍镀层表面同样存在熔蚀现象。熔封开盖后的盖板形貌如图 10(b)所示,可以看出,激光熔蚀区的焊料浸润较差,焊料内溢很少。
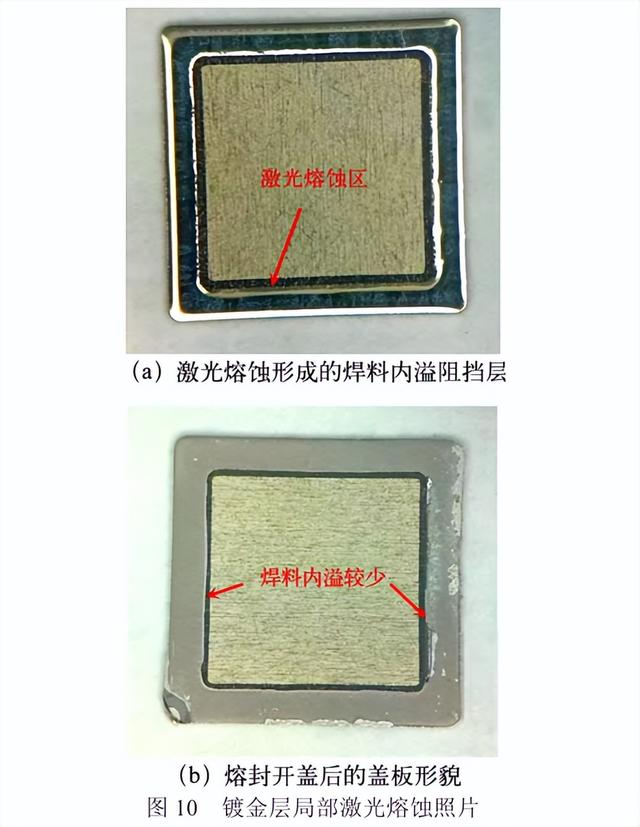
非金属盖板的局部金属化技术是盖板基材选用陶瓷等材料,盖板封接区金属化部分为镀金层结构,使焊料不能流淌到封接区外。相较于金属盖板,陶瓷盖板需进行表面金属化,工艺较复杂,成本上并无优势,且抗冲击强度、接地屏蔽性能等不及金属盖板,其厚度较厚,应用远不及金属盖板广泛。
4.4 预熔焊料盖板
采用预熔焊料盖板是改善焊料内溢的另一个有效措施。在受控环境中将金锡焊料预熔在盖板上,然后检查焊料流淌情况。预熔盖板如图 11 所示。
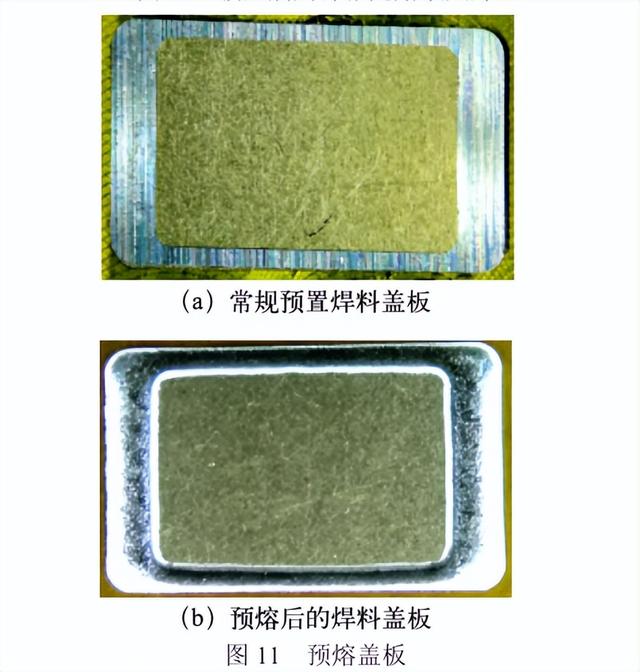
焊料在预熔时,其内侧已形成一个均匀的焊接周界。在封帽过程中,预熔焊料盖板的金锡焊料再次熔化时,焊料流淌受到一定程度的约束,其流动性不及常规焊料,焊料内溢减缓。比较一款陶瓷双列直插外壳(CDIP)在采用不同盖板进行熔封时的差别,图 12为预置焊料盖板与预熔焊料盖板的 X 射线照片,从图12(b)可以看出,预熔焊料盖板的焊料内溢明显比预置焊料盖板少,少量焊料内溢区的颜色较浅,说明内溢焊料的厚度很薄。
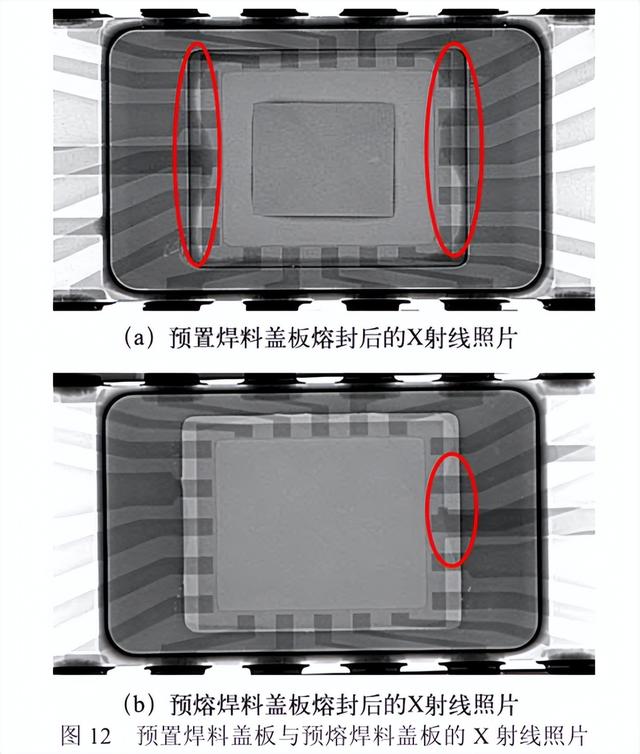
4.5 装片工艺的选择
尽量选择非有机材料装片的方式进行芯片连接,如采用共晶焊装片。若必须采用导电胶粘接工艺时,须对导电胶进行充分固化,如在较高的温度下进行固化,以减少封帽过程中导电胶中有机物的挥发。与采用高温导电胶装片的方式相比,采用共晶焊装片器件的焊料内溢明显减少,采用金锡焊料共晶焊装片器件的封接区焊接形貌如图 13 所示,可以看出,焊料的内侧边缘较整齐,焊料内溢很少。
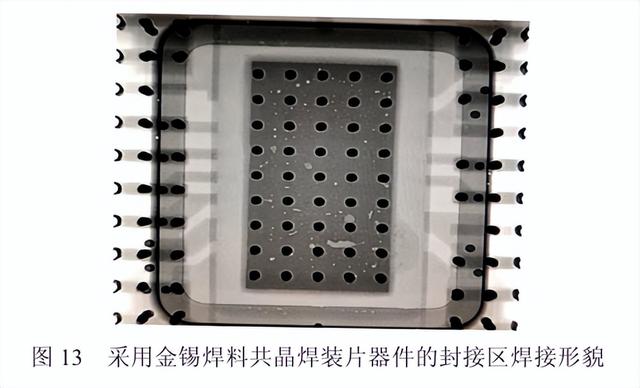
5 结论
盖板内侧为全镀金结构、在熔封过程中盖板受力不均匀是合金熔封中焊料内溢形成的 2 个主要原因,而焊料环尺寸与密封区尺寸不匹配则是引起焊料内溢的另一个重要原因,导电胶装片工艺会促使焊料内溢的产生。
通过盖板(焊料环)与密封区的结构匹配性设计、优化密封工艺(如优化夹具设计及采用倒置封帽等)、采用预熔焊料盖板、盖板局部镀金或限制焊料内侧流淌的位置等方式,可有效抑制焊料内溢的产生,有效控制盖板与引线的间距并减少 PIND 失效。
预熔焊料盖板在微小尺寸的声表面波器件、晶体振荡器等器件中应用普遍,但在高可靠集成电路封装中的应用才刚开始。目前本研究团队已完成工艺评估,随着用户对封装器件良率(如筛选 PIND 合格率)、可靠性等方面的要求不断提高,鉴于预熔焊料、局部镀金技术在控制焊料内溢上的优势,可以预计国内对预熔焊料盖板、局部镀金盖板将会出现较大的需求,因此有必要在预熔焊料的成分调整、预熔工艺控制、密封设计以及产品标准化等方面开展更深入的研究,以尽快实现其工程应用。