新能源车用 IGBT 模块封装技术研究
贺 坚
(株洲中车时代半导体有限公司)
摘要:
我国新能源汽车的关键零部件对外依赖程度较高,特别是在 IGBT 模块芯片方面,与先进国家技术实力相比,我国还存在明显差距。因此,相关行业人员应深入研究 IGBT 技术,推动 IGBT 技术快速进步,以使我国新能源汽车真正摆脱外国芯片。先分析新能源汽车产业现状,并指出新能源车用 IGBT 模块封装技术特征,再重点探究技术的应用与发展,以期为相关行业人员提供参考。
0 引言
在汽车领域,新能源汽车是未来发展方向,其优势在于能减少排放量,与我国节能减排的号召相适应。为推动新能源汽车产业发展,我国制定了许多优惠政策。但分析我国新能源汽车产业发展情况发现,我国新能源汽车生产需要采用部分进口零部件,尤其是 IGBT 模块,这 是 我 国新能源汽车产业发展受限的关键。 基于此,相关行业人员应深入研究新能源车用 IGBT 模块封装技术,以推动 IG-BT 技术与新能源汽车产业同步发展。
1 新能源汽车产业现状
现阶段在全球节能减排领域,新能源汽车属于重要产业,其在许多汽车大国得到重点扶持。为促进新能源汽车产业发展,我国也出台了一系列利好政策,如补贴政策、税收优惠政策、不限行政策、不限购政策、免费停车政策等。2022 年,我国新能源汽车销量超过 500 万辆,市场处于爆炸式增长状态,成为新能源汽车产销大国。 但我国新能源汽车的关键零部件对外依赖度较高,特别是在以 IGBT 模块为主的车用芯片领域,与先进国家相比,我国技术实力还存在较大差距。 在汽车成本中,IGBT 模块占比较大,例如,国产 A00 级纯电动汽车,其电驱动系统成本占比大约为 11%, 而在电控系统中,IGBT 模 块 成 本 又 占比 44%左右,如图 1 所示。 由此可知,IGBT 模块成本大概占据汽车整体成本的 5%。目前,我国致力于发展 IGBT 技术,以推动国产新能源汽车真正使用上中国芯片[1]。
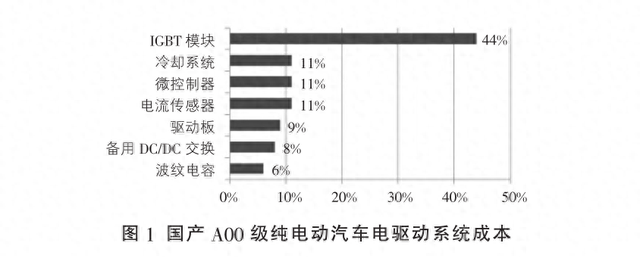
2 新能源车用 IGBT 模块封装技术特征
2.1 IGBT 模块
IGBT 模块属于一种模块化半导体产品,其由 2 个部分组成,即绝缘栅双极型晶体管芯片和续流二极管芯片。通过封装构成的 IGBT 模块能在许多设备上直接使用,如变频器设备、UPS 不间断电源设备。 IGBT 模块的应用优势较多,其安装便捷、能稳定散热和有效节能。 在节能环保理念深 入推进的背景下,IGBT 模块的应用愈发广泛。 同时,在能源变换与传输系统中,IGBT 模块属于核心元件,与 CPU类似,目前在新能源装备领域应用较多。
2.2 IGBT 模块封装技术
IGBT 模块封装技术主要包括焊接式和压接式 2 类。应用焊接技术时,通常有 2 种形式,即平面封装和引线键合互联。 底板也有 2 种功能,其一是对上部模块起到支撑的功能,其二是在运动情况下起到支持上部模块散热的功能。底板主要安装在最底部,其四周连接两侧与外壳,具有保护内部构件的作用。同时,电极、基板与内部半导体芯片之间以焊接形式相连,待电极上部与外部连接完成后,可在内部倒入硅凝胶,发挥隔绝空气的作用,以免内部半导体暴露在空气中而受到腐蚀。 此外,加入硅凝胶还能实现抗震效果。由于在单片功率芯片的情况下,汽车能源需求难以满足,所以通常会采用并联多个芯片的方式,将其放置在同一基板上,再通过并联多个基板的方式,以提高功率、扩大容量。
与传统汽车相比,新能源汽车在驱动方式上存在较大不同,其主要包括电动驱动、混合动力驱动、燃料与电力融合驱动 3 种驱动方式。新能源汽车无论是在功率密度方面,还是在驱动效率方面,都具有较高要求。首先,在新能源汽车运行过程中,尤其是启动频次较多的情况下,流过 IGBT模块的电流会急剧增长,产生较高的温度。同时,在新能源汽车放置较长时间后将其启动,IGBT 模块温度也会 出现变化,进而影响其使用寿命。其次,当启动驱动方式主要为永磁同步驱动的新能源汽车时,会难免发生电机堵转的问题,流经 IGBT 模块的电流也会急剧增长,在 局 部 位置 形成高温,因而要求具备较高的散热能力。再次,新能源汽车运行在凹凸不平的道路上会出现颠簸,此时 IGBT 模块会受到振动,所以新能源汽车在引线端子上也有较高要求,要求其具备良好的机械性能。 最后,新能源汽车的车身尺寸是固定的,而在固定尺寸要求下,不仅要保证 IGBT模块功能,也要保证其质量,需要在此基础上逐渐加大功率密度,尽可能降低空间占用[2]。
3 新能源车用 IGBT 模块封装技术的应用与发展
在 IGBT 模块生产中,封装技术较为关键。 模块封装是在集成半导体分立器件的基础上,在模块内部完成封装,并实现多种功能,包括机械支撑、散热通路以及外部环境保护等。 IGBT 模块内部通常包含半导体芯片、散热基板、键合线、功率引出端子、焊接层以及封装管壳等多层结构材料。 为提高电流承载能力,半导体芯片往往以并联形式连接,并基于引线键合的方式在芯片上表面实现电气互连,基于焊接的方式使芯片下表面与绝缘陶瓷衬板相连。典型焊接式 IGBT 模块结构如图 2 所示。
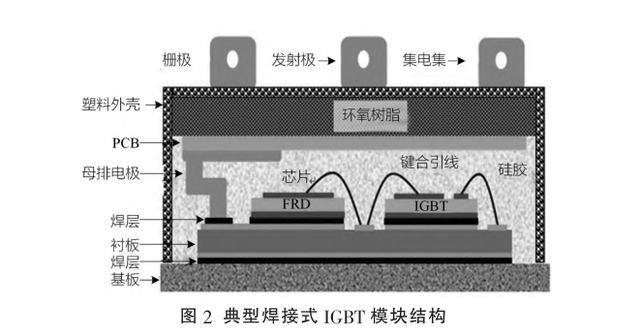
有关研究证实,当 IGBT 模块处于高温、高压状态时,芯片表面键合线与焊层内部较易产生疲劳失效。通常情况下,1 个 IGBT 模块从生产到投入市场要经过 9 道工艺,包括贴片、焊接、等离子清洗、键合等。其中,封装技术的重点在于焊接与键合。
3.1 焊接技术
为使 IGBT 模块具备较强的导热性能,在焊接芯片与DBC 基板时,应确保焊接质量。目前,软钎焊接属于 主流技术,而未来预计将发展为低温连接技术。
3.1.1 软钎焊接技术
在 IGBT 模块的封装过程中,软钎焊接技术被广泛采用。这项技术主要利用真空回流焊接技术连接各种电气元件,如半导体芯片、陶瓷衬板和基板等。 在软钎焊 接过程中,常 用的 焊料 包括 AnSn、SnPb、PbSnAg 等 ,焊料 可以 以焊膏或焊片的形式使用。 使用焊膏焊接时,需要使用助焊剂,并在焊接完成后进行清洗处理,这种方式容易受到 潮湿环境的影响。相比之下,使用焊片焊接通常无需助焊剂,焊接完成后也不需要清洗,焊层更均匀,但这种方法所需的焊接设备较为复杂,焊接时需要使用特制的夹具来定位焊片和焊接件。 现阶段软钎焊接技术发展趋于成熟,在模块封装过程的应用较为广泛。 但与进口模块相比,国产模块在一致性与可靠性上还存在一定差距,这也是国产新能源汽车企业不使用国产模块的根本所在。
3.1.2 低温连接技术
SiC 模块出现后对焊接技术的要求更严格,需要有效提高焊接工艺可靠性,所以开始运用低温连接技术,其代表工艺为银烧结工艺。 与软钎焊接技术相比,该技术具有显著的应用优势。 应用低温连接技术时,其连接层具有 2 个特性,即较高热导率和电导率。以银为例,由于银的熔点在900 ℃以上,所以针对银烧结层,最 高 工作 温 度可 控 制 在700 ℃左右。与普通焊层相比,银烧结层厚度较薄,仅为普通焊层的 50%~80%左右,而且与普通软钎焊层相比,银烧结层的电导率、热导率更高,高出 5 倍左右,所以银烧结层既具有良好的功率循环能力,也具有良好的温度循环能力。但这项技术的实施难度较大,加之设备、银粉成本较高,需要精确设定工艺参数,因而阻碍着技术商业化发展进 程 。国 外 先 进 汽 车 企 业 (如 英 飞 凌 、三 菱 )已 在部 分 IGBT 模块焊接过程运用低温银烧结工艺,我国目前也在努力实现低温连接技术的规模化应用[3]。
3.2 键合技术
IGBT 模块内部存在许多并联连接的芯片,其上方发射级与二极管芯片阳极连接,两者连接方式以引线键合为主。同时,半导体芯片、绝缘衬板以及个别功率端子的连接也采用键合线形式,并通过引线键合作用形成完整的电路结构。 因此,在 IGBT 模块电流回路中,键合线尤为关键,其能起到有效连接的作用。 现阶段 IGBT 模块内部的键合线种类较多,包括铜线、铝线、铝包铜心线等。
3.2.1 铝线键合
铝线键合工艺的应用较为广泛,其根本原因在于应用成本较低,这也是铝线键合工艺的突出优势。 但铝线也存在不足之处,如热学特性较差、导电性能较差等,尤其在热碰撞性能上,铝线与半导体芯片之间难以匹配,会出现热应力聚集,导致键合线开裂和 IGBT 模块失效。 通过优化铝 键 合 线 形 状 、完 善键 合 工 艺 参 数等 方式 ,能 提升 IGBT模块的可靠性,但提升程度也受限。 将铝键合线模块应用于部分高功率新能源车辆电驱动系统中,通常难以满足要求。目前,铝线键合工艺已在我国模块封装中使用,与国外工艺相比,并未出现明显的技术差距。
3.2.2 铜线键合
与铝线相比,铜线的力学特性、热学特性以及电学特性更优。基于铜线键合方式,可使键合工艺的可靠性更强,尤其是在功率密度较高、散热效率较高的功率模块上采用铜线键合方式,能显著提升功率循环能力。因此,其在未来有望成为典型技术形式。铝线键合性能与铜线键合性能之间的区别如表 1 所列。
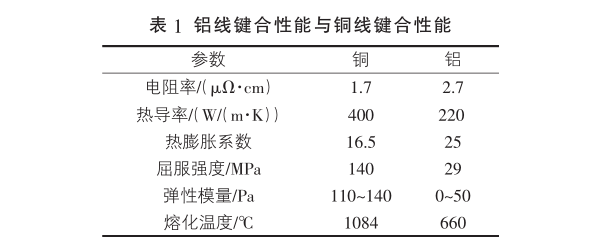
由表 1 可知,与铝线相比,铜线的功率循环能力能高出 10 倍左右,但因半导体芯片表面的金属化层会对铜线键合的应用造成影响,铜键合线无法与以铝金属化层为基础的半导体芯片良好匹配。为使半导体芯片表面适应铜线键合,往往要采取铜金属化处理措施,如运用化学电镀方式、物理气相沉积方式等来实现,这增加了工艺的复杂性。同时,与铝相比,铜的硬度和杨氏模量都较大,为保证键合效果,对超声能量的要求更高,而这难免损伤超薄型 IGBT芯片,甚至可能导致芯片内部的元胞结构直接被损坏。 目前,铜线键合技术已在国外部分汽车企业的高性能模块中使用,而我国主要应用功率较低、性能较低的模块,并未广泛使用铜线键合工艺。 因此,为推动国产模块性能高质量发展,应攻克键合技术难点问题,将国外先进技术壁垒打破[4]。
通过分析模块封装工艺的 2 大关键技术(即焊接技术与键合技术)可知,在目前的 IGBT 模块领域中,我国模块封装企业在技术上还存在一定不足。在国产模块的制造过程中,由于难以实现对质量的有效控制,国产模块无论是一致性还是可靠性都较差。 只有在 A00 级纯电动车这种低端汽车生产中,才会选择国产模块,而高端新能源汽车,目前对国产模块并不信任。 因此,现阶段一方面应优化IGBT模块制造工艺,采用先进技术,如离子注入技术、精细光刻技术等,通过缩小芯片尺寸、硅片尺寸,促进硅片切割利用率提升,降低 IGBT 模块制造成本;另一方面 应 优化 模 块封装技术,在芯片技术成熟发展的背景下,芯片工作温度会逐渐升高、热功率密度会逐渐加大,所以需要不断改进IGBT 模块封装技术,以提升芯片焊接的可靠性,降低热阻。例如,无绑 定线键合、双面 冷 却 、集 成 电 流 与 温 度 传 感器等不仅能提高 IGBT 模块的功率循环频次,还能有效降低引线电感。
4 结语
为突破销量,我国模块封装产业还应努力积累技术实力,在深入研究新能源车用 IGBT 模块封装技术的基础上,生产性能更高的 IGBT 模块。 同时,我 国新能源汽车企业也应信任、支持国产模块。对于模块封装企业而言,应掌握模块封装焊接技术、键合技术,推动自身转型,实现高端化发展。