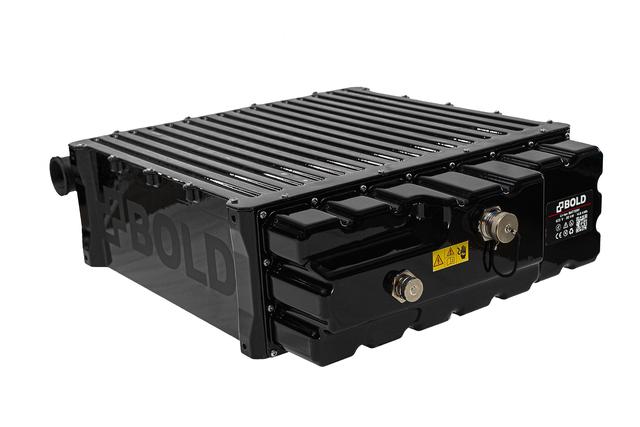
BOLDair 是一种专门的解决方案,可满足飞机中使用的电动和混合动力推进系统的独特能量存储需求。它的车身完全由复合材料制成,重量仅为 52 公斤。因此,就重量性能而言,它被认为是市场上性能最高的电池之一。来源 |大胆有价值的技术
为了通过减排实现可持续航空,电动和混合动力推进系统的开发已成为一种有前景的解决方案。在此背景下,高性能电池行业的知名企业 Bold Valuable Technology(西班牙巴塞罗那)开发了一种名为 BOLDair 的高压电池系统,专为满足电动和混合动力飞机驱动应用的独特要求而设计。它的最大电能存储容量为14.8千瓦时,标称电压为672伏,旨在成为电动常规起飞和着陆(eCTOL)、无人机和其他非管制飞机的可靠、高效的电能存储,使它们能够安全运行且零排放。
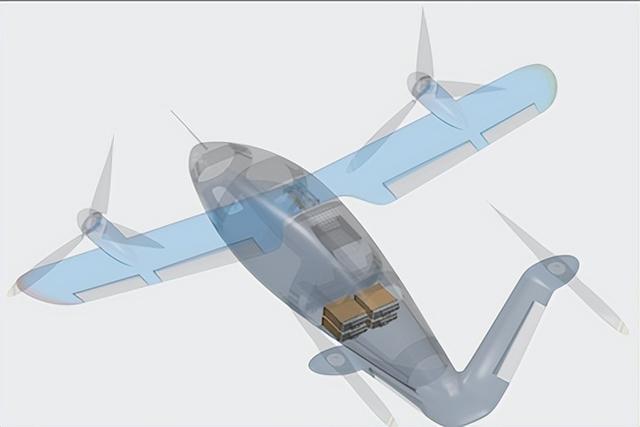
上图展示了电动常规起飞和着陆 (eCTOL)、无人机 (UAV) 和其他非管制飞机中储能系统的可能位置
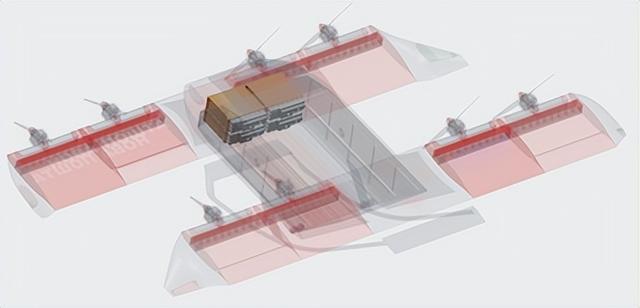
这些存储系统旨在有效地存储能量,并且可以集成到这些类型的飞机中以增强性能。
OLDair 电池重量仅为 52 公斤,比能量为每公斤 285 瓦时。这种性能是通过使用先进的复合材料和施工技术实现的。电池外壳的核心是模压成型的双层碳纤维增强聚合物 (CFRP) 单体壳,提供了坚固的框架。为了确保电池正常运行和热管理,采用了嵌入金属热桥的 CFRP 电池压缩结构。此外,玻璃纤维增强聚合物 (GFRP) 面板还可用于电气隔离。总的来说,这些复合材料结构表现出卓越的热失控传播鲁棒性,这是航空应用的一个重要特征。
电池系统设计概述BOLDair 利用了 Bold Valuable Technology 创始人丰富的复合材料工程专业知识,他们首先开始磨练技术,开发高性能赛车运动的电池系统,特别关注一级方程式混合动力总成电力存储系统。
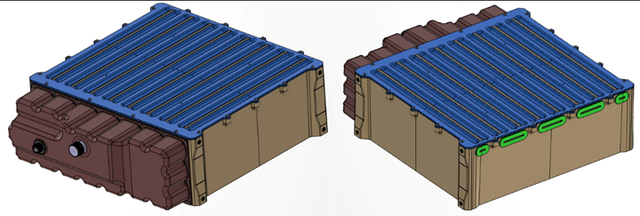
这里展示的是 BOLDair 电池系统的 CAD 渲染图,其中详细介绍了蓝色、酒红色和灰色色调的全复合结构中的独特组件。值得一提的是,位于盖子上的脊之间的灰色条带表示压缩结构。这些结构的结合是为了增强电池系统的稳定性和耐用性。
BOLDair 的技术要求非常具有挑战性,需要卓越的重力效率、广阔的操作窗口和卓越的安全功能,”Bold Valuable Technology 电气化项目经理 Oscar Crespo 说道。 “这些要求使得先进复合材料成为 BOLDair 结构的理想解决方案。”
因此,BOLDair 拥有完全复合结构,具有多种功能,包括电池压缩、电气隔离、EMC 屏蔽和热管理、振动抑制和热失控传播保护。复合材料在 BOLDair 设计中的应用展示了其在高性能环境中的多功能性和适应性,并展示了此类复合材料应用未来技术进步的潜力。
电池芯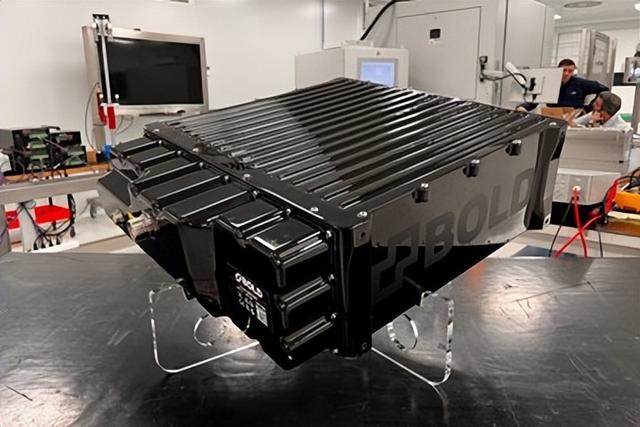
图中所示的是 BOLDair 电池系统的原型模型,旨在提供可靠且高性能的储能解决方案
电池选择是 BOLDair 电池系统开发的起点,采用高能量密度软包电池形式的锂离子 (Li-ion) 电池,具有硅和石墨阳极存储化学物质。通过添加硅掺杂,该系统的容量进一步增强,从而实现更高的充电容量和更长的电池寿命。
“软包电池格式扁平且重量轻,由多层绝缘金属层压板组成,可提供高电池组能量密度,”Crespo 强调。 “这意味着电池可以在更小的空间内存储更多的电力,使其成为飞机储能系统的理想选择。”
软包电池以其高能量密度而闻名,最终产品体积利用率高达 80%,明显高于圆柱形电池的典型效率(70-75%)。这种高能量密度导致高重量性能特征和更高的能量转换效率。
单元管理结构软包电池(包含阳极、阴极和浸没在电解质中的多孔聚合物隔膜)的最佳功能、安全性和耐用性在很大程度上依赖于保持活性材料的完整性。软包电池没有刚性外壳,因此容易受到机械应力的影响,从而可能导致内部短路、退化、电解液泄漏或热失控。此外,电池在运行过程中因气体产生或热膨胀而膨胀的趋势对层压密封件构成了重大威胁,增加了暴露于外部污染物的风险。
BOLDair 采用由 CFRP 制成的复合压缩结构,可控制软包电池在充电和放电循环期间的膨胀。该结构旨在在工作压力内均匀压缩电池区域,减轻局部应力并管理热条件,确保电池的最佳性能。
设计成果先进的复合材料使电池组的比能量达到每公斤 285 瓦时。通过采用旨在支撑软包电池的压缩结构,可以减轻软包电池对机械应力的脆弱性。外壳材料的选择和设计可实现热失控耐久性,确保电池保持完整并固定在飞机框架上。碳纤维以其高拉伸强度而闻名,每根纤维的断裂应变约为 15%。然而,当在层压板中实施时,这种应变可以降至 1.5%。加载过程中剪切应力引起的层间剪切失稳是复合材料结构失效的主要原因。
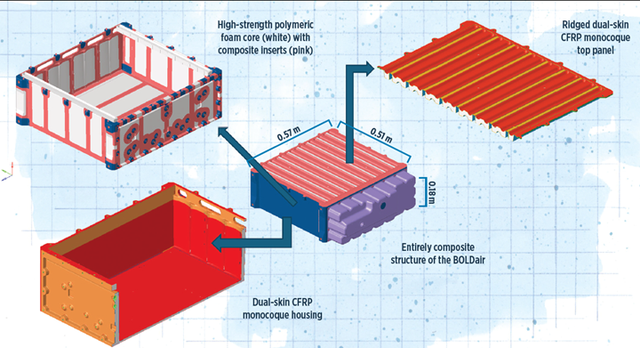
“设计具有特定应变特性的层压板以补偿剪切不稳定性对于开发在压缩下运行良好的复合材料结构至关重要,”克雷斯波指出。 “BOLDair 的细胞压缩结构通过调整纤维配置和基体特性来抵消剪切力,从而有效地解决了这个问题,从而增强了复合材料的强度并防止失效。”
值得注意的是,有效的热管理对于减轻电池内热点的形成以及抑制电池老化和故障至关重要。 BOLDair 使用由内置在复合压缩结构内部的铝翅片制成的导热桥,该导热桥接触软包电池最热的部分,并将热量从核心吸到外部,在那里可以消散到安装在高处的冷却盖中。电压区域并被动地提取到周围环境。
“碳纤维是压缩结构中使用的增强材料,由于其石墨晶体结构而具有导电性,”克雷斯波指出。 “因此,BOLDair 系统通过实施由低克重 GFRP 复合材料层和介电涂层制成的电绝缘结构来防止电池和 CFRP 结构之间的任何电流短路,从而使电池内的安装与其周围的 CFRP 压缩结构分开。 GFRP 结构不仅提供隔离作用,还提供额外的结构加固。”
BOLD空气外壳结构双层 CFRP 硬壳结构包含电池单元、GFRP 隔离和 CFRP 压缩组件,为电池提供保护。外壳的 CFRP 结构采用斜纹编织图案预浸料。这种特殊的编织在生产过程中表现出卓越的悬垂性,在应用过程中表现出显着的剪切强度,使其非常适合生产复杂的形状。
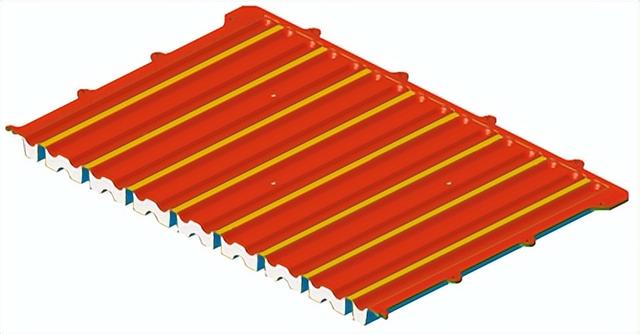
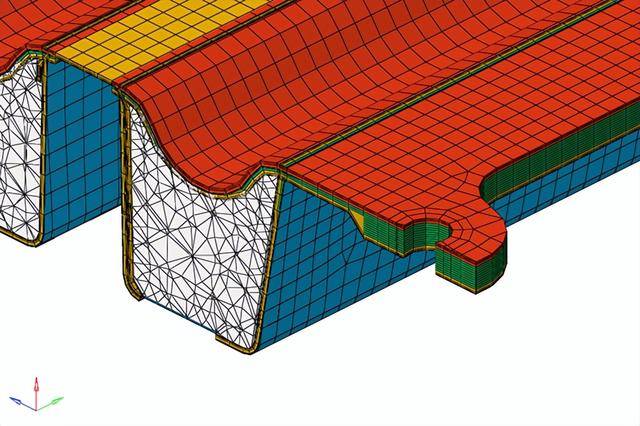
此 CAD 渲染图展示了顶部面板肋,可通过阻碍振动能量和确保高阻尼比来减少共振损伤并优化负载弹性。
准各向同性叠层结构在所有方向上均匀分布刚度特性,确保减轻重量与热性能和结构性能之间的优化平衡。当承受来自多个方向的负载条件时,这种叠层结构特别有益,因为它有助于将应变均匀地分布在层压板上,从而减少可能导致疲劳和失效的应力集中的可能性。 Crespo 强调,“外部负载将通过安装点从车辆转移到电池,因此这种类型的叠层适合将负载均匀地分布在整个外壳中。”
硬壳式外壳还在用于电气连接的连接端口周围提供了专门的支撑和密封,从而保持外壳的完整性,同时实现必要的功能。双层硬壳式 CFRP 顶部面板完善了 BOLDair 系统的外部外壳。顶部面板内精心设计的肋增强了刚度重量比并增加了固有频率,从而显着降低了共振损坏的风险。顶部面板的肋的位置和尺寸可阻止振动能量的传播,确保高阻尼比并优化结构的负载弹性。
此外,肋状设计允许在更广泛的表面积上散热。 “肋条的设计是使用有限元分析确定的,同时考虑了机械性能标准,其中考虑了电池内部压力超过其设计极限的“过压”情况,以及模拟负载条件下的重量最小化,”克雷斯波指出。
芯材BOLDair 电池外壳中的硬壳式结构由内层和外层组成,并由高强度聚合物泡沫芯材料支撑。该核心在促进两个皮肤之间的交互方面发挥着至关重要的作用,并提供附加功能。 “针对给定应用的泡沫选择很大程度上取决于特定强度的需求;它需要高抗压强度和低密度,以增加 CFRP 蒙皮之间横截面积的惯性矩,同时将重量损失降至最低。”Crespo 说道。 “此外,确保所选泡沫材料能够在相对较高的温度下运行也至关重要。”
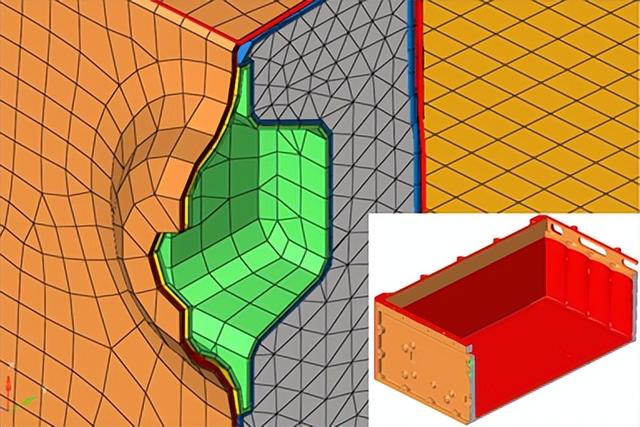
CAD 渲染图显示了 BOLDair 电池外壳内的硬壳式结构,该结构由由高强度聚合物泡沫芯材料支撑的内皮和外皮组成
复合材料嵌件嵌入整个核心并与蒙皮接合,以在应用紧固件或连接器的位置提供结构加固。插入件设计可确保载荷在复合材料结构上分布更均匀,从而减少应力集中以及由于机械载荷或振动而导致分层或失效的风险。 “界面层用于粘合嵌件和 CFRP 表皮,”Crespo 解释道。 “这些层有助于保持复合材料单体壳的结构完整性和耐用性。”
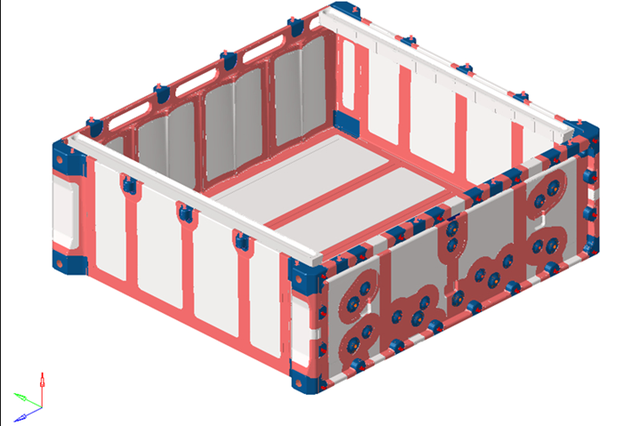
该 CAD 模型显示复合材料嵌件在何处加固芯材以及与蒙皮的界面,以在应用紧固件或连接器的位置提供结构支撑
BOLDair 的内部复合材料压缩和隔热结构采用手工铺层和高压釜固化制造。采用压缩成型技术来构造双层硬壳式外壳和盖子,从而实现精确的尺寸精度和坚固性。外壳和顶板部件是通过手动将芯材放置在各自压缩模具中的预浸料层之间而形成的。
“BOLDair 结构的每个元件中使用的预浸材料均由原生纤维材料制成,长纤维定向在层压板内部,以在其工作区域内实现最佳性能,”Crespo 强调。 “尽管该材料的确切基体成分是专有的,但碳纤维预浸料的固结处于预浸料系统的常规固结温度范围内。”
热失控遏制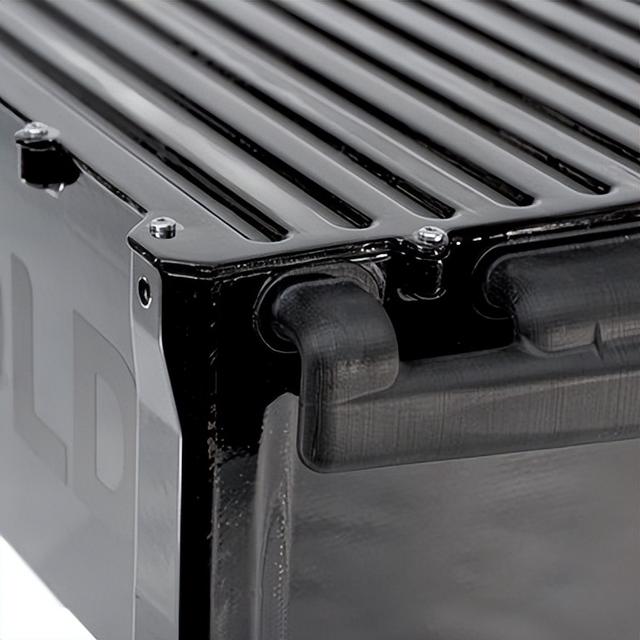
专为通风和冷却而设计的先进 3D 打印歧管已固定在 BOLDair 系统的侧面
“如果发生热失控情况,释放的能量可能相当大,”克雷斯波解释道。 “如果排气系统设计不当,这种能量的大小可能相当于爆炸。事件期间产生的火焰会引发爆燃,导致熔融金属颗粒从电池中高速喷出,导致周围结构严重磨损。”
在标准测试条件下,发生热失控的电池的破坏性是任何火焰都无法比拟的。在无法进行热管理的情况下,选择能够有效容纳释放到一个电池的能量的适当材料是防止能量传播到电池系统或周围环境中更多电池的唯一选择。
“目前,还没有既定的行业标准来验证航空驱动应用的电池组和电池组,”Crespo 解释道。 “现有的材料合规标准,即阻燃热塑性塑料的 UL 94 分类,只是一个基本的可燃性标准,不足以指定能够承受热失控事件的材料,以确保航空驱动电池的操作安全。为了解决这个问题,Bold 开发了测试和验证流程,重点是实现最佳性能和可靠性,同时减轻与热失控传播相关的风险。”
Bold 热管理系统的初始测试阶段涉及将传热分析与复合结构分析相结合的模拟。目的是研究电池应变、热管理能力和热失控发生之间的相互作用。该建模结合了电池通风和热传播的模拟,以隔离复合结构的有效配方。
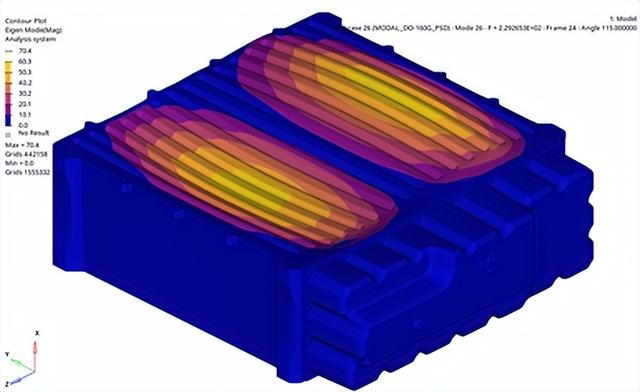
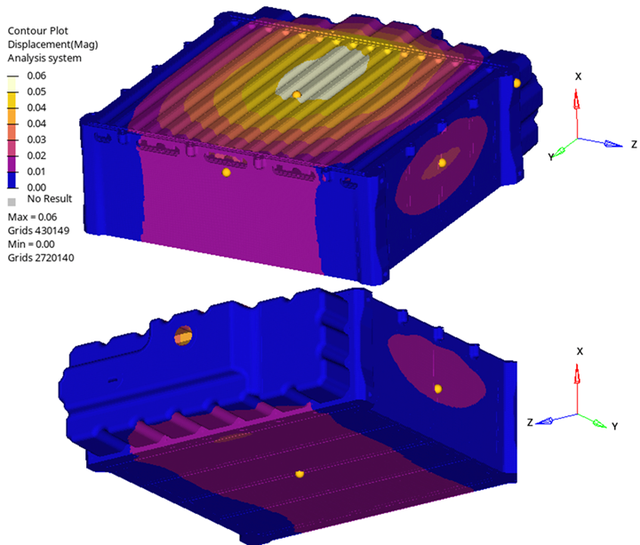
热管理模拟用于以数字方式测试 BOLDair 结构的性能。
模拟之后进行了实际测试,以验证复合材料在抑制热失控方面的功效。 “锂金属电池热失控的温度范围通常在 1200°C 至 2000°C 之间,而对于锂离子电池(如航空电池系统),通常在 600°C 至 1200°C 之间,具体取决于电池类型,”克雷斯波解释道。 “分析火包内火焰传播的路径和速度以及喷射粒子的轨迹至关重要。”
Bold 的先进复合材料配方经受 1000°C 火焰的考验,施加压力的持续时间比预期的热失控事件更长。最终的验证测试包括对电池压缩结构和复合材料外壳中使用的所选复合材料配方进行全面的热失控事件。所选复合材料成功地控制了热失控,该工艺有助于确保所选材料最适合该航空应用。
Crespo 表示:“Bold 正在努力创造一种能够承受高达 2000 °C 极端温度的复合结构,从而实现一项重大的工程壮举。” “值得注意的是,没有任何材料可以无限期地承受如此高的温度。然而,Bold 采用的测试方法旨在开发能够有效评估复合材料承受电池内热失控事件的适用性的测试方法。”
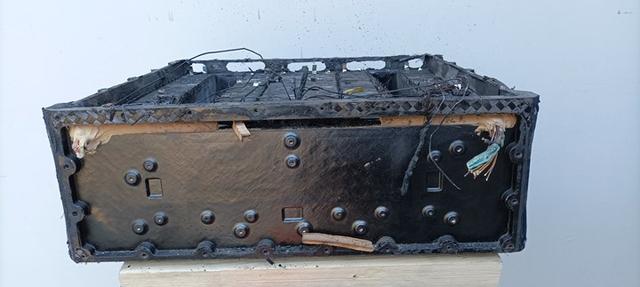
图示是热失控检查的结果之一。值得注意的是,电池组件遭受了严重损坏,而复合材料外壳却完好无损。
目前,无论是汽车还是航空航天,都没有针对电池结构热失控的既定安全法规,并且由于各种原因,目前的汽车电池测试方法被认为是不够的。 BOLDair 的外壳材料选择和设计可实现热失控耐久性,确保电池保持完整并固定在飞机框架上。与汽车不同,在热失控事件中放弃飞机并不是一种选择。 Bold 的测试能力正在与航空航天业的 AS9100 质量管理体系一起开发。 BOLDair 电池组展示了 Bold 开发的综合方法,用于评估和建立航空电池复合材料的适当材料设计和测试方法。这种创新方法对于促进制定高压电池和/或电池组材料的严格标准至关重要,其目标是确保未来高压航空驱动电池的安全性和可靠性。
无人机应用测试BOLDair 的技术已在多个应用中得到成功部署。Flying Basket (意大利博尔扎诺)是一家专门从事货物运输无人机技术的客户,已在其重型无人机中部署了 BOLDair。该公司的成立是为了解决复杂的自然和城市地形带来的物流挑战,在这些地形中,传统的运输方式往往缓慢且低效。创始人认识到无人机克服这些挑战的潜力。
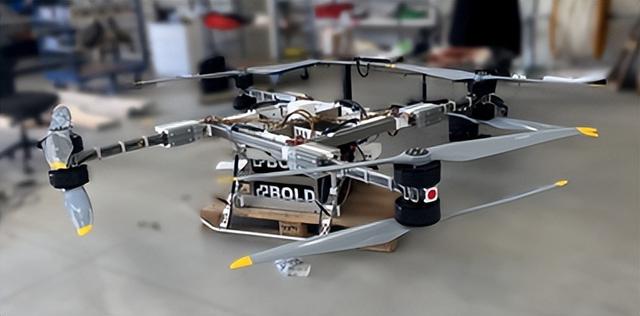
FlyingBasket 成功将 BOLDair 部署在重型无人机中。
飞篮无人机具有先进的导航系统和 100 公斤的有效负载能力,使其适用于广泛的应用,从农业物资运输和工业服务到电力线路和建筑的电缆架设。飞篮面临的重大技术挑战之一是开发一种能够在携带大量有效载荷的情况下长时间飞行的无人机。这需要具有高功率部署能力的高能量密度存储,以提供必要的耐用性、可靠性和安全性。 BOLDair 电池被证明是成功的,为公司的运输解决方案做出了贡献,并展示了无人机在物流转型方面的潜力。
Crespo 总结了 BOLDair 在航空专用电池系统中的复合材料应用:“我们与 BOLDair 的合作证明了我们致力于突破复合材料技术界限,提供更安全、更高效的航空解决方案的承诺。我们将继续完善 BOLDair 并为各种应用开发定制规格,无论是电池类型和容量还是冷却系统和操作优化。该项目不仅展示了我们的技术实力,还展示了我们对可持续发展的奉献精神,推动航空业迈向更绿色、更创新的未来。”