
文|正经的烧杯
编辑|正经的烧杯
«——【·前言·】——»
在钢结构桥梁施工中,需要在桁段运往现场前在钢结构制造厂进行试拼装,来确保杆件制造精度及拼装匹配度满足规范、设计要求。
试拼装是钢桁梁出厂前重要的环节,需要对多个桁段进行拼装连接,并对节段立体尺寸进行全面检验。试拼装工序需要运用与现场施工几乎相同的机械设备、足够大的场地、足够的人工和工时。
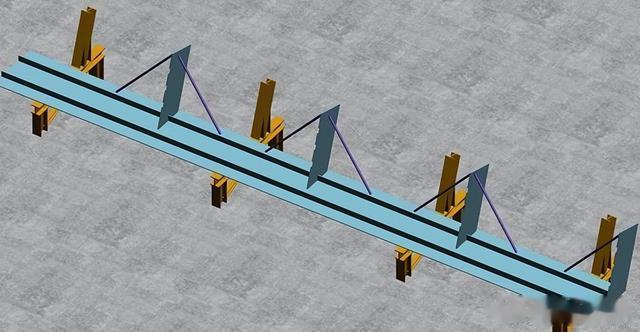
试拼装完成后还需要对桁段或者杆件进行拆卸,运往工程现场,提升项目整体成本。同时试拼装主要目的是验证桁段栓接部位的拼装性,但是仅靠全站仪针对部分点位的测量难以精准获取所有杆件位姿及极边孔距,进行拼装线形评估。
近年来模型技术和三维扫描技术迅速发展,在工程领域具备了图像数字化处理、构件精准测量、逆向建模技术和计算机模拟分析能力。
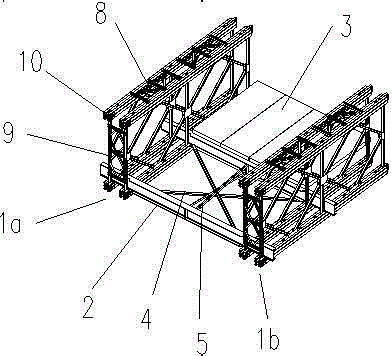
但是国外鲜有针对特大桥钢桁梁的拼装研究,国内针对桥梁的数字化拼装也处于起步阶段,2020年某公司以钢将梁为对象,分析数字化虚拟预拼装的基本原理,并进行了方案设计,在钢拱桥的拱肋控制上进行了尝试。
对于栓接结构桥梁钢桁梁而言,既需要考虑杆件散拼后的形位特征,又需要获取孔群信息,仅靠单一尺度的点云采集设备难以兼顾大尺度、高精度的需求。
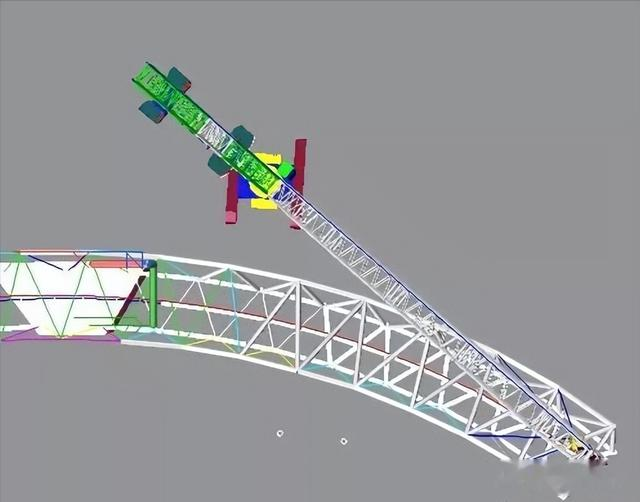
同时现有软件缺乏针对桥梁的点云处理算法,大型钢桁梁数字化拼装整体技术路线并未形成体系,亟需结合工程需求进行深入研究。
以实际工程项目为依托,针对大型钢桁梁结构的桁段拼装,提出一种基于三维激光扫描结合摄影测量的多尺度点云逆向模型建立及数字化拼装方法。
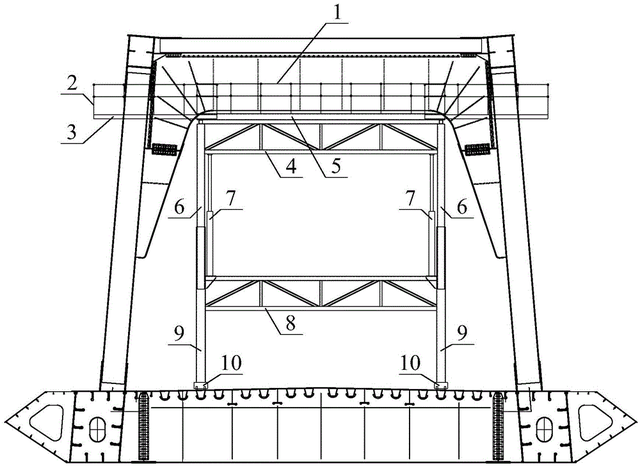
对钢桁梁进行实地扫描并撰写算法对多尺度点云模型拟合处理,结合自主研发拼装算法软件进行拼装模拟;验证分析数字化拼装在实际施工过程中的运用精度及可行性。
«——【·数字化虚拟拼装技术路线·】——»
工程背景:本文以某双层斜拉特大钢桁梁桥为例进行研究。该桥上层为高速公路,下层为城际铁路和普通公路。主桁采用“N”形结构,钢桁梁采用两桁结构,两片主桁中心间距为35.0m,标准节间长度14.0m。
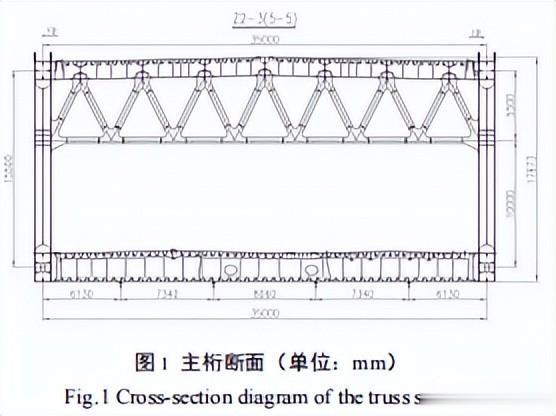
桁梁的上下弦杆布置与线路纵坡平行,竖杆与纵坡垂直。主梁采用双层板桁组合结构,标准桁段Z2-3(5-5)横断面如图1所示。桁段间弦杆采用高栓连接,弦杆和腹杆采用焊接加高栓连接,单个桁段的桁片如图2所示。
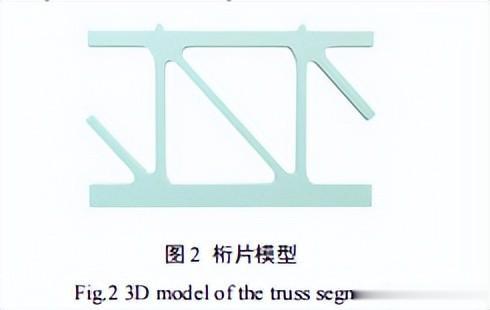
依托该项目对桥梁主跨桁段进行现场数据采集及实验,研究桁段数字化虚拟拼装关键技术在实际项目中的应用可行性。
大型钢桁梁数字化拼装整体流程:数字化拼装整体技术路线主要分为两个部分,首先解决逆向模型的建立,其次进行桁段拼装效果评估。
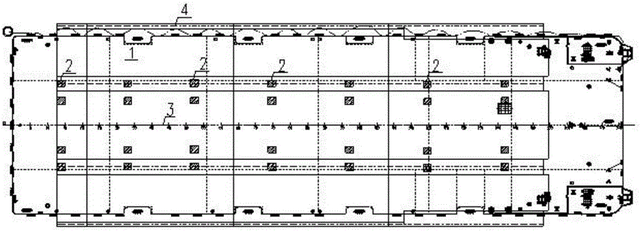
桥梁钢桁结构尺寸大,精度控制要求高,因此为反映钢桁梁桁段尺寸及螺栓孔空间位置关系,采用多种设备组合测量。
针对孔群采用近距离精细化扫描,桁梁整体采用轮廓扫描,将两种不同尺度的扫描模型进行拟合,将获取的精细化孔群模型匹配至桁段,构建含有精准尺寸及孔群信息的桁段逆向模型,技术路线如图3所示。
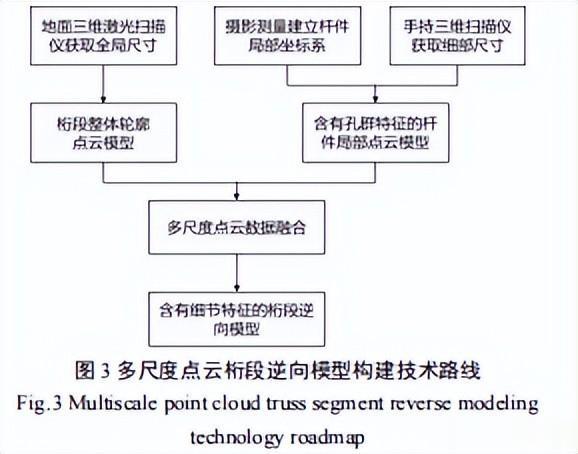
获取桁段逆向模型后,即可与设计BIM模型进行拼装误差分析,评估散件拼装效果,不满足形位要求时提供修正指导,调整完成后,通过研发点云精简算法,将孔群轮廓、杆件轮廓及轴线等核心数据进行提取,选取桁段拼装特征点。
用特征点进行点对点的位置匹配运算,通过轮廓线与轴线评估拼装匹配度和线性,解决点云数据量大无法直接运算的难点。最终通过研发基于图形引擎的可视化拼装程序对桁段拼装的效果及误差进行可视化展示。技术路线如图4所示。

«——【·杆件及桁段多尺度点云获取方法·】——»
通常采用全站仪结合反光标靶进行测量,难以通过测量点位反映桁段整体位姿及线形。为能够获取完整的构件模型进行虚拟预拼装,研究FaroFocus150Plus基站式扫描、DreiDTek手持式扫描仪对于本桥桁梁的测量方法。
FaroFocus150Plus基站式三维激光扫描由激光扫描仪和数码相机组成,其作业架站方式与全站仪作业类似。基站式三维激光扫描可对特定目标区域数据进行快速采集,再通过处理采集数据建立目标区域的三维模型。
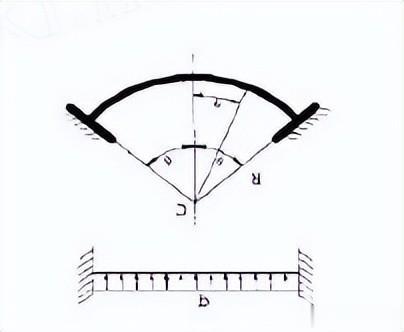
通过公共区域的扫描对不同测站采集的数据进行融合,从而建立目标区域的三维坐标信息。扫描仪可以实现水平360°、垂直180°的扫描范围设置。
扫描仪参数设置及设站方法对被测物点云模型精度有着决定性的影响。分辨率设置决定了点间距,提高分辨率会增加扫描点的个数并且会减小点间距,质量设置的越高,在扫描区域扫描仪会采集物体上更加集中的点。
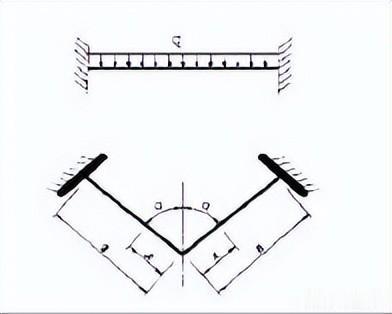
质量设置会影响测量速率、降噪水平,以及扫描仪的扫描范围。为保证扫描精度的同时提升效率,针对同一杆件,在同样的设站位置下分别采用:方案一,分辨率1,4倍质量;方案二,分辨率1/2,4倍质量;方案三,分辨率1,2倍质量;方案四,分辨率1/2,2倍质量,4种参数进行扫描,分析模型精度,其中方案二、四扫描模型如图5所示。
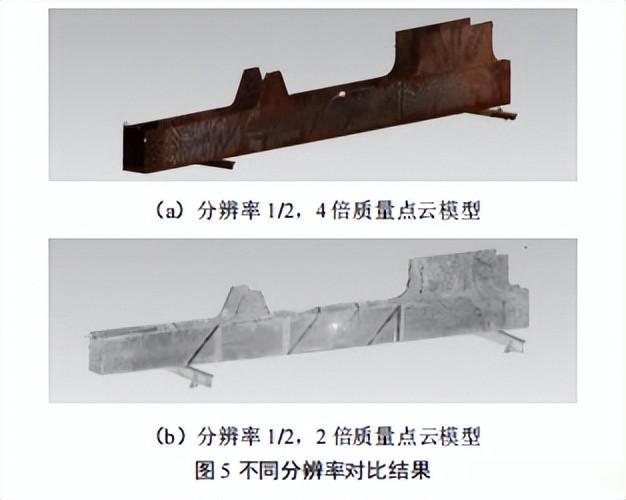
分辨率和扫描质量将综合影响点的数量、间距及扫描时长,结果如表1所示。
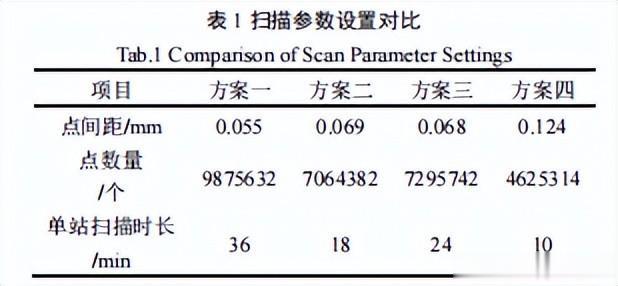
方案一模型整体精细程度最高,但扫描耗时长。对于方案二和三,获取的模型质量相近,均能具备清晰轮廓。
提高扫描质量能够对被测物进行往复扫描,将点云聚焦于被测物;提高分辨率则会对整个扫描区域内所有物体进行扫描。
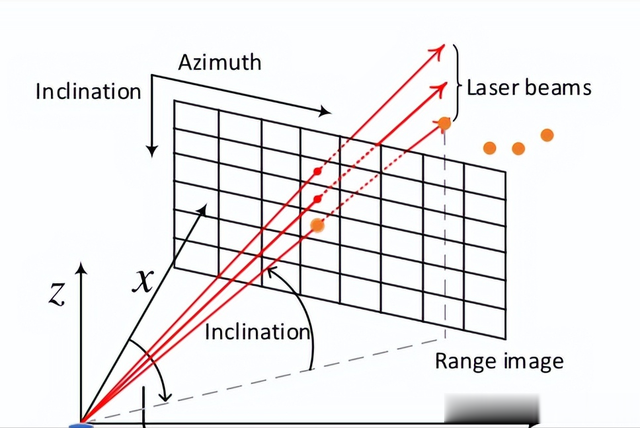
切除周围环境和杂物后两种方案中被测物点云数量相近且方案二扫描用时短。对于构件扫描增加扫描站数将提高目标整体点云数量,对于关键部位多角度设站也可以提升轮廓清晰度。
因此选择方案二作为测量方案。设6站扫描的杆件点云如图6所示,杆件轮廓清晰,但是孔群处较为模糊,无法准确识别孔外径。
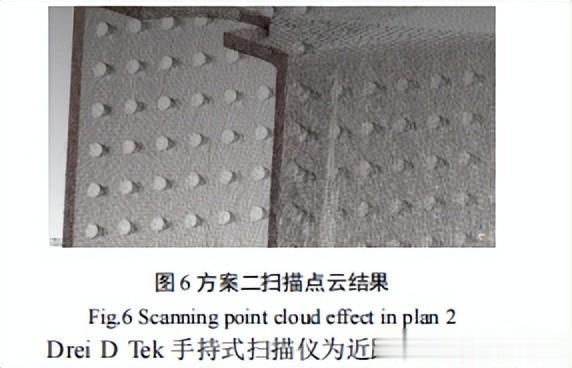
DreiDTek手持式扫描仪为近距离手持扫描设备,通过对孔群等细部进行扫描,获取精细化的点云模型。
扫描仪工作原理基于三角测距法,手持式激光扫描仪具备激光发射器与接收器,且两者之间的基线长度为定值,通过照射到被测物表面返回时激光的角度和距离来定位被测物表面点的坐标。
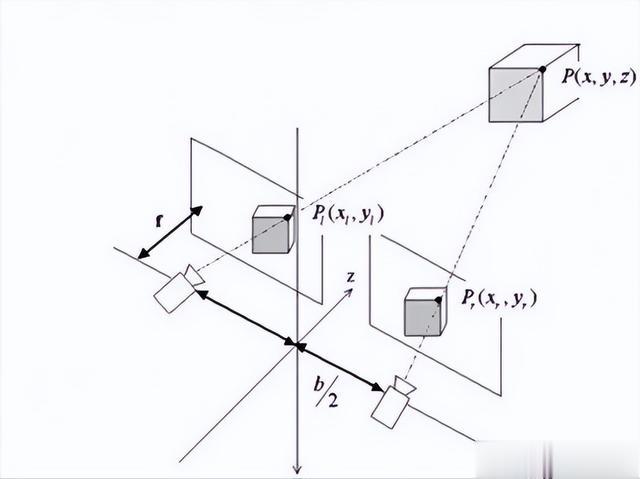
因此通过该设备多束激光多角度入射,可以快速重构被测物表面,实现逆向模型采集。扫描前需要采用编码点对被测结构进行粘贴,编码点作为唯一坐标用于扫描过程的坐标定位。
拼接板及桁段端头节点板孔群体积小于3m3,可以用扫描仪直接进行采集,扫描过程及获取模型如图7所示,所有孔轮廓清晰且可以在厚度方向上拟合圆柱。
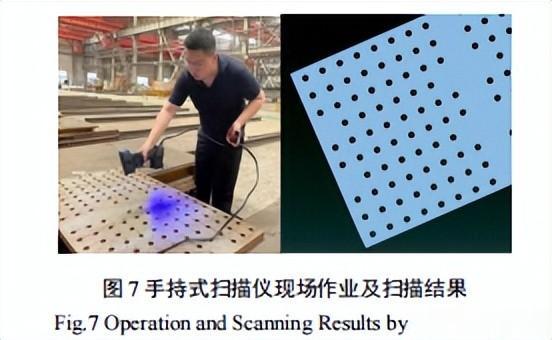
该设备仪器精度为0.020mm+0.0150mm/m,为验证扫描精度,挑选4个孔进行游标卡尺测量校核,运用游标卡尺测量3次,结果如表2所示。
通过模型测量出的孔径与游标卡尺测量值误差在微米级,精度满足孔群分析及栓接计算匹配精度要求。手持扫描设备具有一定的使用条件,需要有线作业并连接计算机进行实时模拟,适合在室内环境进行工作。
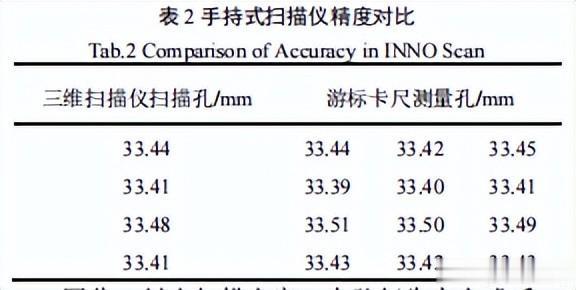
因此制定扫描方案,在弦杆生产完成后,于厂房内运用手持式扫描仪采集弦杆端头及拼接板扫描,获取带有孔群的端头精细化模型。在弦杆完成桁段拼装后,于存放场运用基站式扫描仪对整个桁段模型进行扫描。
«——【·逆向模型构建及特征点提取方法研究·】——»
确定扫描方案后,针对桥梁35m×14m×13m标准桁段A2、A3进行数据采集。在弦杆生产完成后对弦杆端头孔群以及对应的拼接板进行手持式扫描。扫描结果如图8所示。

桁段拼装完成后进行基站式扫描。以A2桁段为例,设12站进行扫描,设站布置如图9所示。
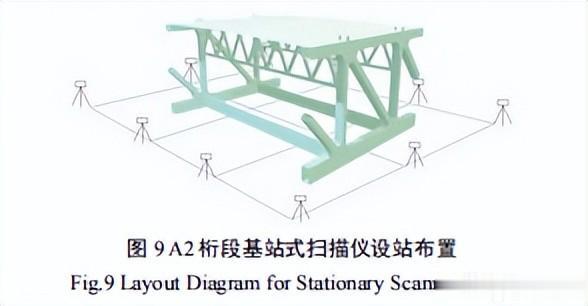
扫描完成后对模型进行切割去噪,总点数为126752542个,点云模型如图10所示。
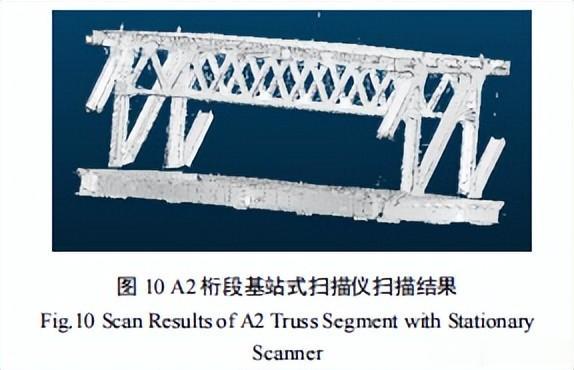
获取点云模型后,需要对获取的点云数据进行拟合,将弦杆端部精细化模型拟合至桁段整体模型的相应位置,形成带有孔群参数的逆向模型。该逆向模型能够反映出弦杆的空间位置,并且可以将孔群坐标进行提取,用于匹配计算。
«——【·基于桁段特征点的拼装算法研究·】——»
由于桁段逆向点云模型体量过大,无法将所有的点用作桁段匹配计算。因此采用降维的思路,将桁段中部分孔群的中心点作为特征点进行提取。
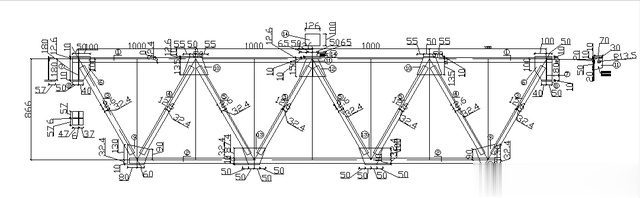
在一个孔群节点板内将用于制造定位的四个边角位置的栓孔中心坐标选择为特征点。通过手持式扫描仪获取的所有栓孔中心坐标的相对位置关系为确定值,因此拼装完成确定特征点在空间中的位置后即可确定所有栓孔的空间位置。
以采集数据桁段A2、A3为例,通过第2节及第3节的方法构建桁段逆向模型并分别提取特征点,每个桁段选取64个特征点,特征点为每个弦杆端头在固定位置上选择8个特征点,8个点分布在弦杆端头的两侧。
拼装过程中选择桁段A2右侧弦杆的32个点和桁段A3左侧弦杆的32个点进行匹配,匹配过程如图12所示。
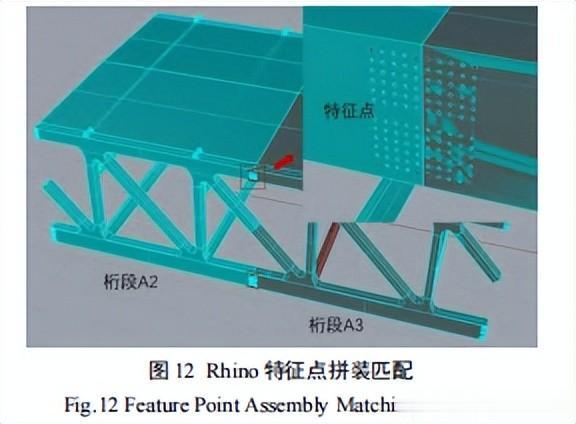
通过grasshopper中电池块进行设置广义普氏算法,运用可视化编程用目标函数及扭转、平移向量计算模块将两个桁段的特征点代入计算,运用GalapagosEditor设置迭代计算规则进行迭代,迭代规则为两个矩阵中对应点的向量模均值为最小,并通过运算器进行求解。
迭代计算完成后,可以将所有的栓孔中心点按照最佳匹配算法进行计算,批量输出运算结果,如表3所示。
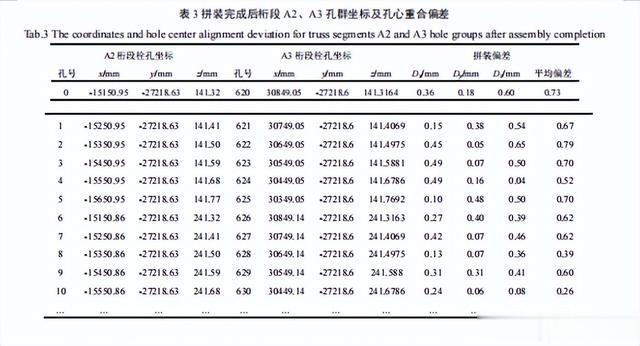
该桥栓孔设计尺寸为33mm,高栓直径为30mm,通过输出结果可知,1240个栓孔孔心重合率均低于1.5mm,其中92.1%的孔心重合率在1mm以内。
通过该方法能够快速计算出螺栓的合格率同时根据精细化孔群模型计算出各弦杆极边孔距以及拼装完成后顺桥向长度偏差,根据偏差为线形调整提供依据,指导后续钢桁梁拼装施工。
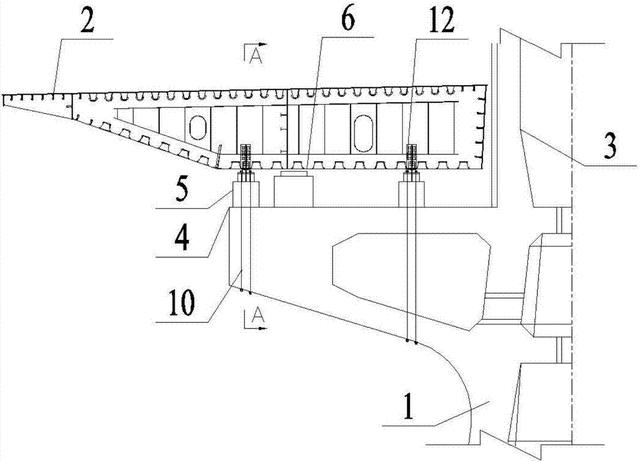
«——【·结语·】——»
本文针对特大钢桁梁桥桁段1+1拼装施工问题,提出了基于多尺度三维激光扫描的数字化虚拟拼装技术,并通过理论分析和现场测试进行了验证,主要结论如下。
钢桁构件尺寸大且制造精度要求高,采用基站式扫描仪可以快速获取构件轮廓尺寸,但是对于孔群等拼装特征难以获取,需要结合手持式扫描仪对细节尺寸进行精细化扫描。
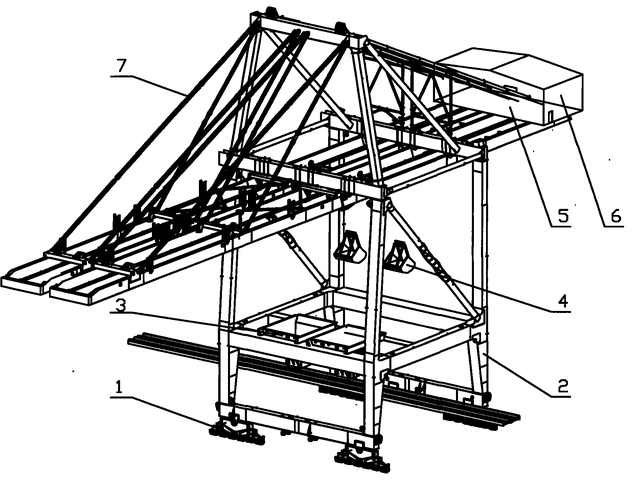
通过扫描获取了桁段数据后,通过研发点云拟合算法实现了多尺度点云的定位及匹配,形成了一套桁段点云逆向模型快速构建方法。实现了点云模型进行拼装特征的矩阵提取,为桁段1+1拼装计算提供基础。
基于广义普氏分析法,运用RhinoGrasshopper可视化编程制定拼装算法,对两个桁段提取的特征信息进行拼装模拟研究及实验,实现了桁段1+1拼装螺栓孔群匹配度自动运算及孔心偏差快速校核,通过3个板块的研究验证分析了数字化虚拟拼装在实际施工过程中的可行性进行了验证。