有一种观点认为“煤矿智能化“建设将大大减轻工人劳动强度,一线工人使用量越来越少,所以煤矿不存在劳动力市场紧张的问题。对这样的论断,不赞同、不支持,“煤矿智能化”的局限性还很大,理想很丰满、现实很骨感。
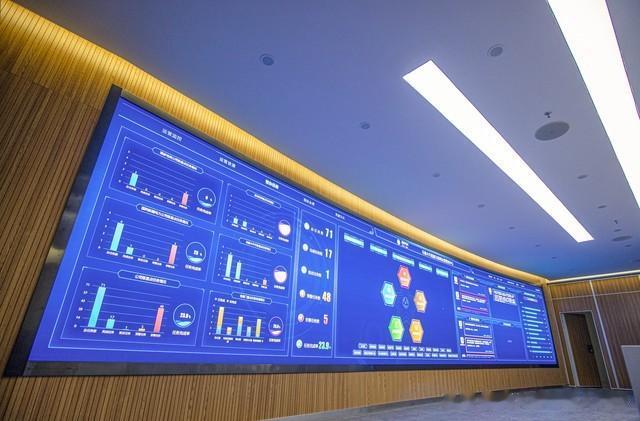
不能否认智能化的集约化、网络化的先进性,在煤矿安全生产中的积极作用,但把智能化作为矿井发展先进的象征有点勉为其难。因为煤矿企业生产特殊,在井下生产依靠的是什么?综采支架、采煤机、破碎机、转载机、综掘机、单体支柱、各种皮带运输机件等,在工作面安装、回撤,综掘机拆解、安装过程中,需要人力进行分解,借助组装机、起重机、绞车等完成相关工作。这个过程短则几天,长则一到两个月,耗费的人力、物力成本高昂。
制约的因素之一是大型装备必人力拆解。煤矿作为井下作业场所,地理环境特殊,受矿井压力影响,煤矿所送的巷道断面根据地质条件和顶板岩性,除主要运输巷道、主要绞车道外,巷道断面都只能满足基本的运输需要。综采支架、破碎机、转载机、综掘机、单体支柱、各种皮带运输机件基本上需要进行拆解,运输到井下工作面。在运输过程中,个别装备超宽、超重,需要运输人员配合,不断地调整管路和拆卸管路,才能让装备顺利通过,再由工人们进行组装、调试和投入使用。工人肩扛手抬占据了工作的大部分时间,智能化只能在使用过程中发挥其作用。
制约的因素之二是采煤工作面地质条件影响。煤矿井下条件复杂,地质条件决定了煤层走向;采煤工作面上、下巷和安装综采支架的数量、角度等,而且还受到工作面顶底板情况、淋水、温度、湿度影响,智能综采设备的自动割煤、移动支架等功能受到一定的限制。在煤层赋存条件差的矿井,一旦遇到断层、顶板破碎,智能化基本上没有效能而言。处理断层时打浅眼、省装药、放小炮等方式,将断层处岩石震动或震碎,采煤机再慢慢前进,防止截齿损耗过大。过破碎带时,需要人工拉架,打好临时支护,漏顶严重时,需要架板梁或钢梁使前梁探进檐子等。遇到上述等不正常情况时,再智能的装备也无法发挥作用。大煤层、大采高,一个综采工作面能生产半年或一年的煤矿企业有多少家呢?
制约的因素之三是装备的多头供应融合效果差。现在的煤矿智能装备生产是百家争鸣、百花齐放,厂家都有自己的拳头产品和先进装备。硬件厂家、软件厂家,连5G网络都是移动、联通、电信三家在竞争,选择成为了困难。每个智能化建设矿井需要的硬件和软件众多,各方面关系和招投标等原因,导致煤矿是多个厂家的装备到矿,多个厂家技术人员在帮助煤矿往一起融合。但融合的东西不靠谱,今天这个有问题、明天那个出故障,再加上煤矿的智能装备人才不足,水平不高,一点小问题都让整套装备停摆。
解决煤矿人力短缺的办法也有,一是设备的减重。用新材料新技术替代传统的铸钢、铸铁设备,让工人在井下拆卸能轻松些。二是发展自走装备,地面都有机器狗帮背着重物,井下也可以发展类似设备啊。让人轻易就扛上百斤的备件爬900米的斜坡,确实伤不起啊。
发展智能化要切合实际,造了一堆设备,只能给检查和参观的看,就是最大的浪费。
现代社会还有这种保守派。如果说因为贵和麻烦就拒绝科技,和闭关锁国有什么区别。等别的国家用无人机上月球采矿,我们还排队坐火箭上月球?