
文|正经的烧杯
编辑|正经的烧杯
«——【·前言·】——»
增材制造技术又称3D打印,与传统减法制造技术相比,增材制造技术提供了更多的设计自由,将零件三维模型化。
借助于离散∕堆积的思想理念进行切片分层,通过不同热源(激光束、电弧、离子束等)对多种形式的填充材料(丝材、粉材等)进行“自下而上”逐层沉积的新型制造技术。
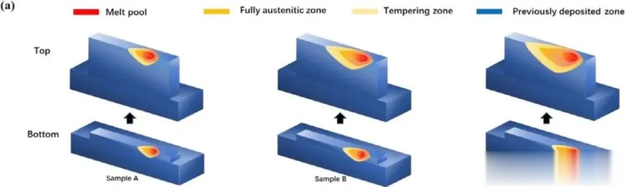
增材制造技术因其效率高、设备成本低、材料选择种类多和生产周期短等优势某公司在轨道交通领域得到了广泛应用。
低合金高强钢是通过加入一定量的合金元素来改善加工性能并提高综合力学性能,使其具有了较高的强度和塑韧性,凭借其优异的性能被广泛用于汽车领域。
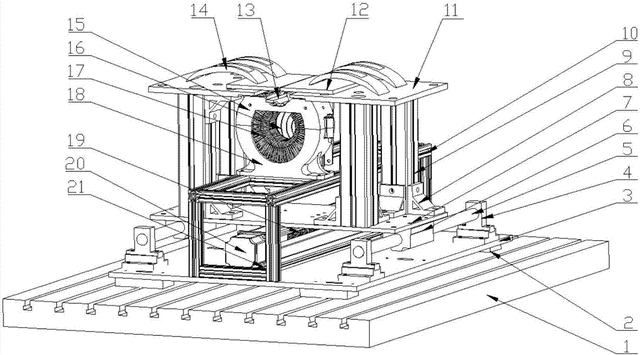
对于高强钢零件传统的加工方法存在生产成本高、制作周期长、成形精度差且易出现缺陷等问题,采用增材制造技术制作高强钢零件,可以有效改善耗时长、成本高、精度差等问题,国内外学者针对高强钢增材制造开展了研究。
目前关于高强钢增材制造的研究虽然很多,但主要集中于单一热源的增材制造方法。文中采用新型高强钢焊丝AFEW6-86。
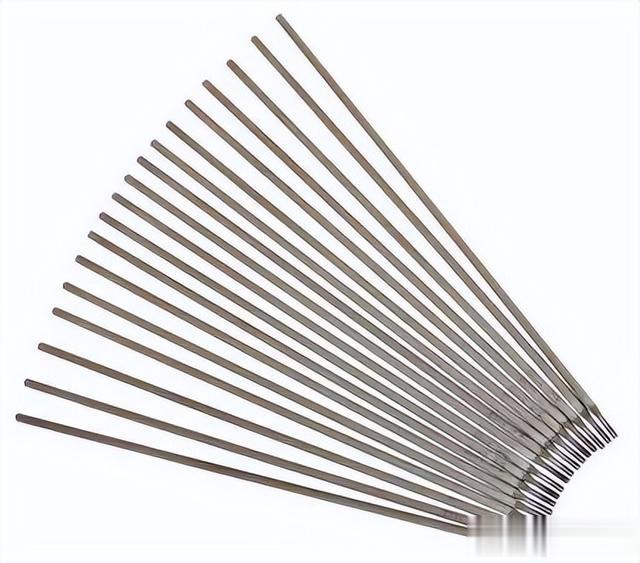
利用低功率脉冲激光诱导TIG电弧复合热源开展增材制造工艺研究,探究其增材制造试件的显微组织转化规律与综合力学性能,分析性能与组织之间的内在联系,为进一步研究高强钢增材制造组织调控和性能优化提供理论与数据支持。
«——【·试验材料及方法·】——»
试验设备采用自主搭建的低功率脉冲激光诱导电弧-TIG电弧增材制造系统,由OTCFD-V20型六轴机器人、XL-800WF脉冲式光纤传导激光器、DA300P型交直流TIG焊机、自动送丝机构成。
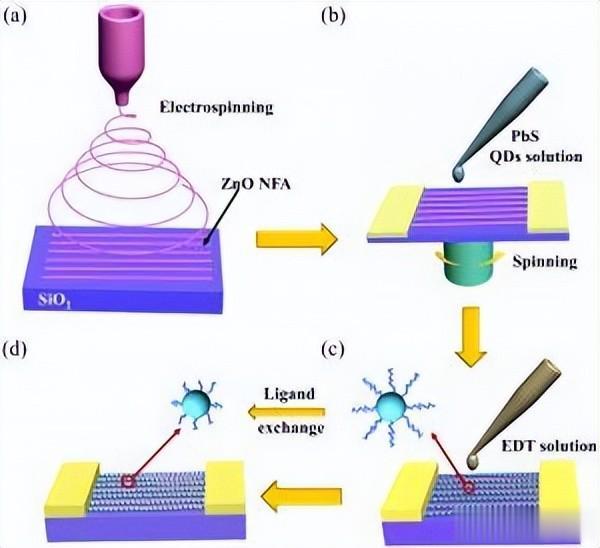
增材制造系统示意图如图1a所示,每层焊道搭接示意图如图1b所示。焊枪与激光束的夹角为45°,试验过程始终保持前送丝,焊丝进给方向与基板呈15°。
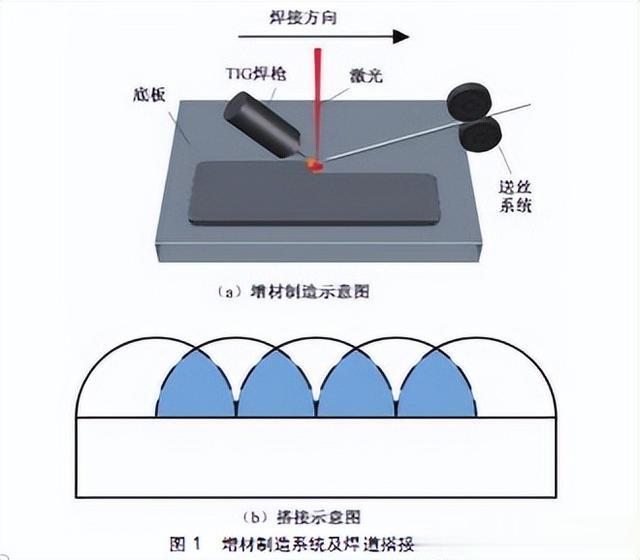
试验基板采用200mm×200mm×15mm的316不锈钢板材,试验前用无水乙醇和丙酮擦洗基板表面,以去除表面的油污及杂质。
试验所用焊丝为AFEW6-86新型高强钢焊丝,直径为1.2mm,其化学成分及力学性能分别见表1、表2。


试验过程采用激光在前、电弧在后的平行同向堆积方法,增材制造出110mm×40mm×5mm的多道多层薄块试件,试验参数见表3。
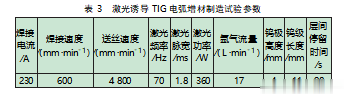
从试件的上、中、下3个部分取金相试样,经打磨、抛光后,用φ(HNO3)4%酒精溶液进行腐蚀,观察并分析其微观组织。
在横截面选取靠近基板以上5mm×5mm的正方形区域,每隔0.5mm采用维氏硬度计测量硬度,试验力为10N,载荷时间为10s。
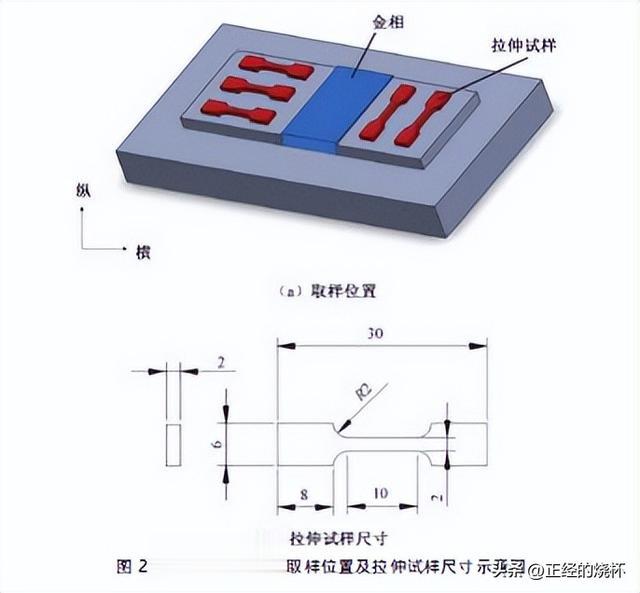
使用线切割,沿试件横向与纵向2个方向切取共5个拉伸试样,利用Instron电子万能材料试验机测量其抗拉强度和伸长率,取样位置与拉伸试样尺寸如图2所示。利用SUPARR55型场发射扫描电镜观察其拉伸试样的拉伸断口。
«——【·结果与分析·】——»
图3是采用激光诱导-TIG电弧增材制造技术成形的多层多道高强钢薄块试件宏观图。从图3可以看出,试件表面较为平整,可以观察到多层多道增材时每层焊道互相搭接的痕迹,没有飞溅和金属熔液流淌的现象,总体表面成形质量良好。
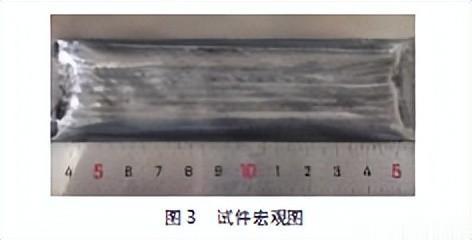
图4为高强钢增材制造薄块试件的宏观截面图,其中图4a为金相腐蚀前的宏观截面图,观察试件无明显的气孔、裂纹等缺陷,且试件顶层平整。
图4b为φ(HNO3)4%酒精溶液腐蚀后的宏观截面图,可以明显观察到每一层沉积层的边界,且呈层间带状,沉积层平均高度约为1mm,层与层之间冶金结合紧密,致密性优异;波浪状的熔池边界是因为增材时的沉积方式导致的,多层多道增材时相邻焊道搭接率为50%。
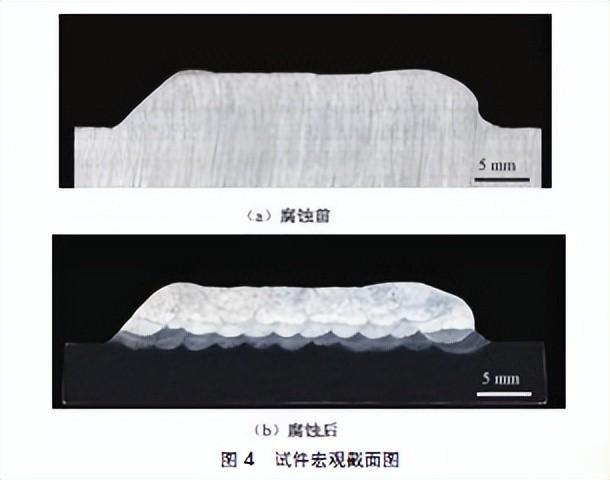
图5为试件不同位置处的显微组织,试件组织主要由贝氏体和针状铁素体构成,这种组织不仅具有较高强度,同时也具有较好的延展性。所用AFEW6-86焊丝中的Ni,Cr和Mo等元素有助于贝氏体在合适的冷却速率下形成。
图5a为试件底层显微组织图,观察沉积层组织为胞状晶,以粒状贝氏体和针状铁素体为主。对于底部沉积层,基板温度低,底层沉积层的热量以热传导的方式从基板传导出去,该方向冷却速率较大,晶粒生长方向均沿此方向,并指向熔池中心。
图5b为试件中部显微组织图,观察到沉积层组织为柱状晶,由呈羽毛状和针状的贝氏体、部分区域的少量板条马氏体和针状铁素体组成。
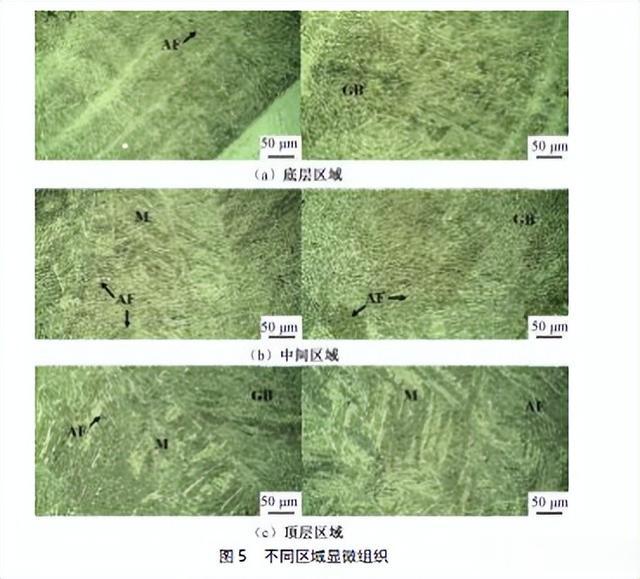
中部沉积层的底部熔池因接触上一层沉积层,接触位置处冷却速度较快,散热方向垂直于上一层沉积层,近似与增材方向相同,形成相互平行并呈一定方向的柱状晶。
由于增材制造过程的反复加热,热量会从基板处向薄壁上部累积增加,中部沉积层的冷却速率减小,温度梯度减小,这也降低了马氏体含量。图5c为试件顶部显微组织图,由板条马氏体、粒状贝氏体和针状、块状铁素体组成。
激光诱导电弧增材制造中的熔池凝固是非平衡凝固,晶粒生长方向与最大冷却方向相反,故呈现一定方向性。经观察发现:顶部晶粒方向较中部组织发生变化,这与顶部散热方式发生变化有关。
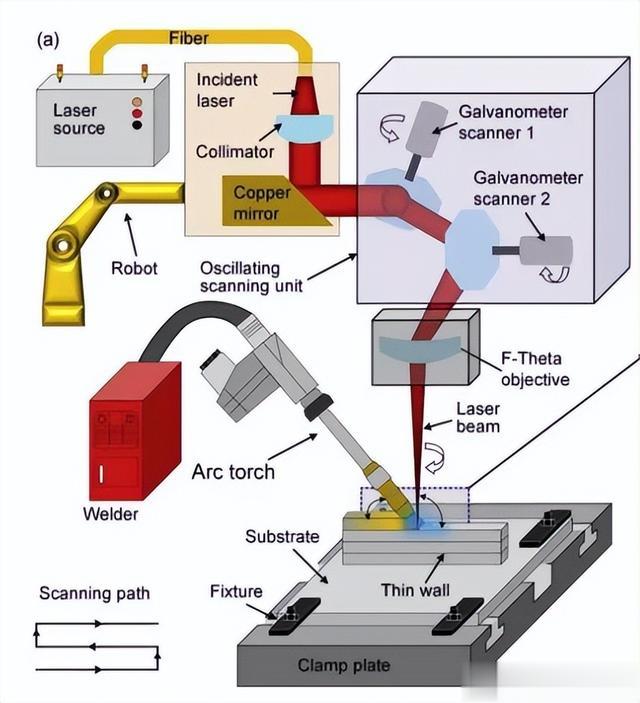
顶部组织散热有2种方式,一种是与沉积层的热传导方式,另一种是与空气的辐射换热,散热条件的改变提高了冷却速率,增加了顶部组织中马氏体含量。
图6为层与层之间过渡区域显微组织图。从图6可见,其为3个相邻沉积焊道的交界处,不同沉积焊道的交界较为明显,呈现为弧形曲线。
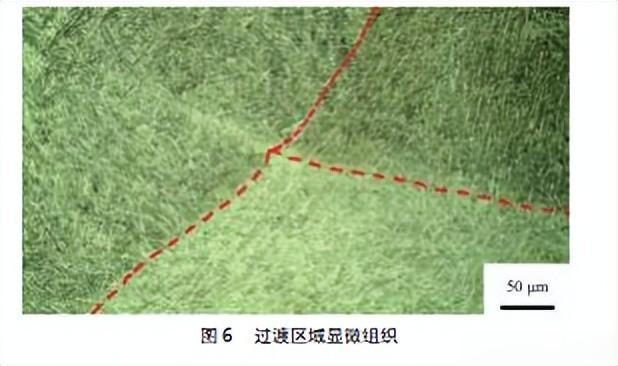
由于是相邻的3个不同沉积焊道,其中的晶粒生长方向有所区别,均垂直于自身沉积焊道的边界。这是因为在沉积时的低功率激光和TIG电弧共同作用下,在垂直于自身沉积焊道边界方向上的温度梯度较大,指向熔池中心。
在沉积过程中,熔池会向相邻沉积层传递热量,形成具有一定宽度的重熔区,这种热处理效果导致该区域冷却速率降低,同时导致该区域的晶粒偏大。
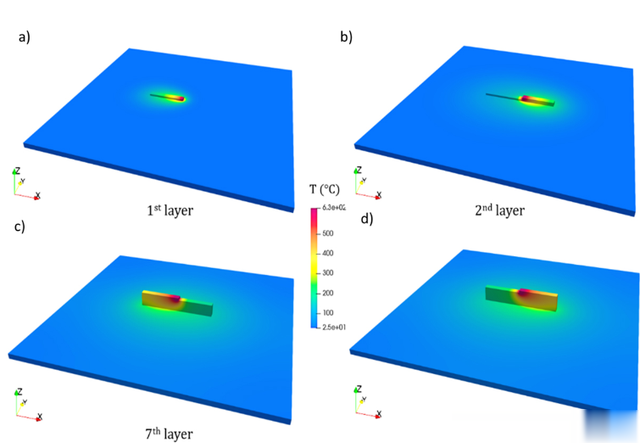
«——【·力学性能·】——»
图7为试件横向与纵向两个方向的拉伸性能图。图7a为试件的应力-应变曲线,图7b为试件的抗拉强度和伸长率。
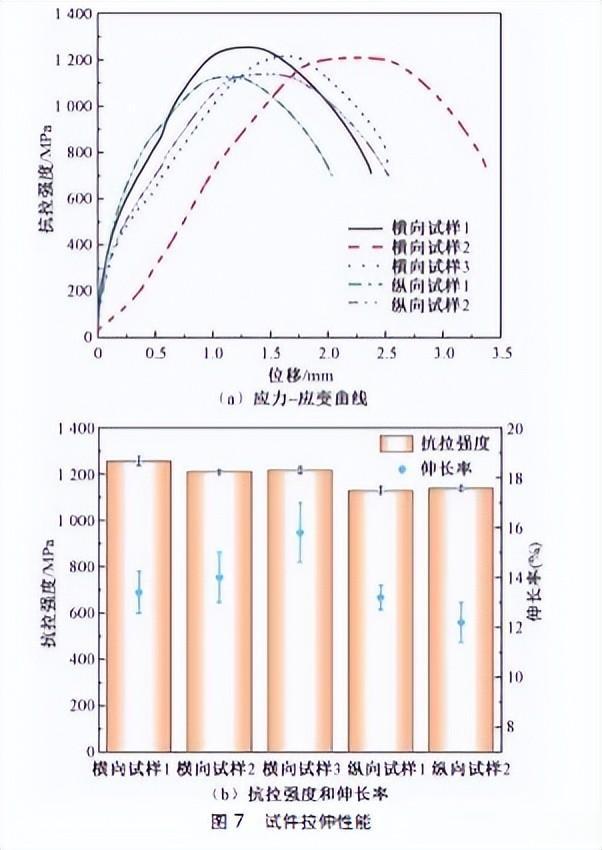
从图7可看出,试件横向平均抗拉强度为1227MPa,纵向平均抗拉强度为1133MPa,试件横向平均伸长率为14.4%,纵向平均伸长率为12.7%。
由于试件组织主要由贝氏体和针状铁素体构成,因而这种组织不仅具有较高强度,同时也具有较好的延展性。所用AFEW6-86焊丝中的Ni,Cr和Mo等元素有助于贝氏体在合适的冷却速率下形成。
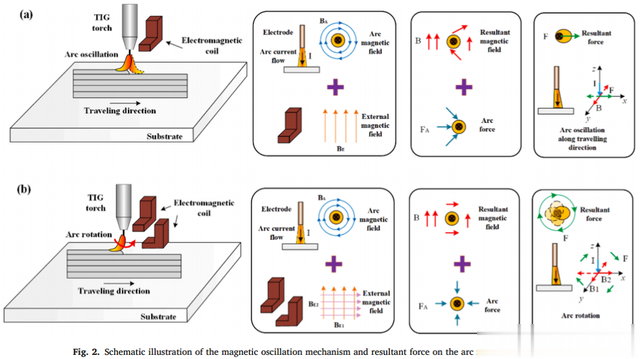
横、纵两个方向抗拉强度之间的差异为8%,伸长率的差异为13%,抗拉强度与伸长率在横、纵两个方向均存在差异,分析认为试件存在各向异性。
造成拉伸性能在两个方向上存在差异的原因是试件在横向拉伸过程中的载荷方向与沉积轨迹一致,平行沉积轨迹构成一定的方向,与材料变形过程中产生的纤维组织结构相似。
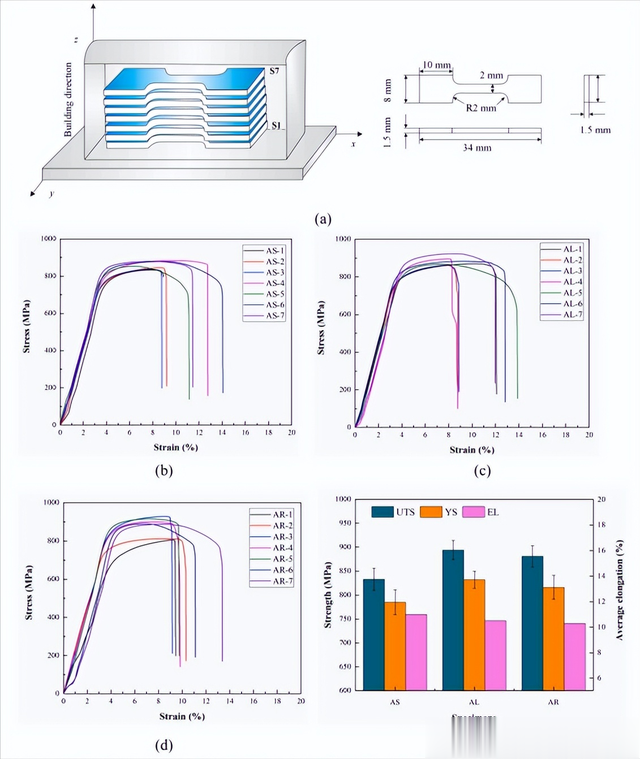
即在拉伸变形(轧制)中晶粒沿拉伸方向伸长,晶粒变得细长,晶粒边界也变得不规则,最终难以区分每个晶粒,呈现出平行的纤维条纹。
沿沉积方向的抗拉强度高于堆积方向的抗拉强度,即横向抗拉强度高于纵向抗拉强度,文中实际测量的抗拉强度数据符合其规律。
选取横向试样3和纵向试样1进行拉伸断口扫描,图8a为横向试样拉伸断口扫描图,图8b为纵向试样拉伸断口扫描图。
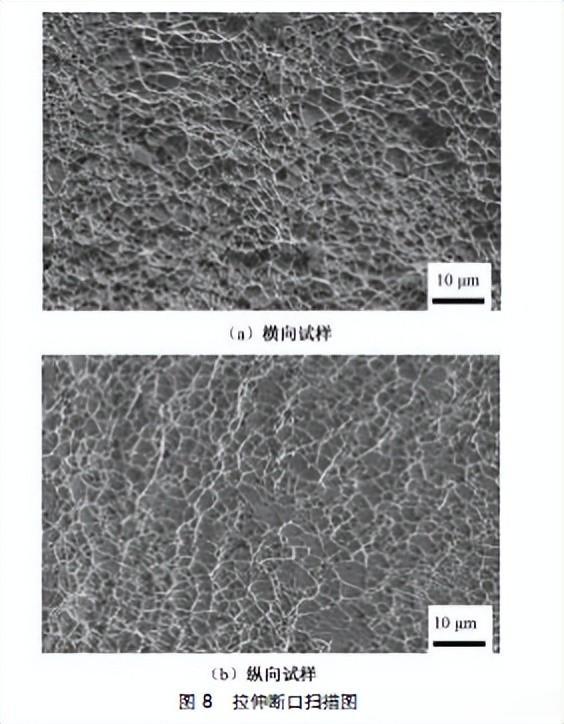
从图8可以看出,2个试样的断口均分布有大量韧窝,具有韧性断裂特征。对比可发现,横向试样的韧窝均匀分布,细小且深度较深,韧窝数量多于纵向试样;纵向试样的韧窝较粗大,同时深度也较浅,由此可以说明横向试样的韧性优于纵向试样的,这与伸长率的实际测量结果相同。
图9为试件横截面的显微硬度云图。从图9可以看出,增材制造试件的硬度分布范围为340.0HV~428.6HV,平均硬度为384.3HV,随距基板距离的增加,硬度值呈先减小后增大的分层趋势。
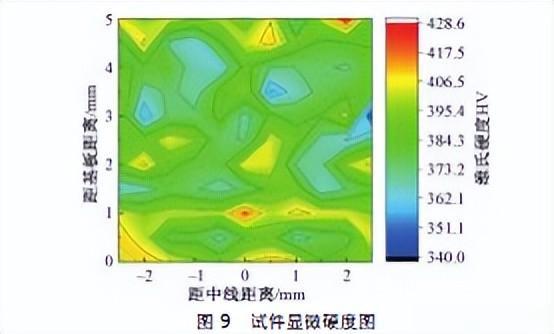
硬度的分布趋势与显微组织有密切的关联性,出现这种现象的原因可归结于热积累与冷却速率的变化。增材制造过程是一个逐层叠加的过程,后一沉积层会对上一沉积层进行重熔,并对前几层沉积层产生反复热循环的作用。
随着增材高度的增加,沉积层之间出现热量累积,导致冷却速率降低,在中部区域形成较粗大的晶粒。
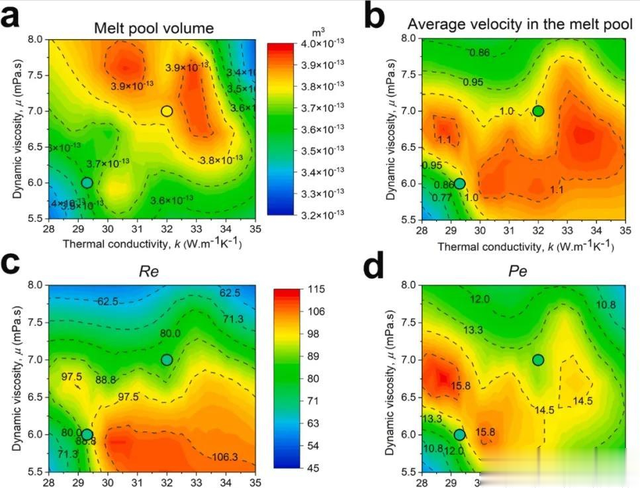
而当增材到达顶层时,散热条件发生改变且没有后续热处理作用,顶部组织的冷却速率增大,部分区域得到硬度较高的马氏体。
为了探究试件中合金元素的分布情况,并分析其强化机理,对试件的不同位置进行了场发射电子探针面扫描测试(EPMA),根据结果进行讨论分析。
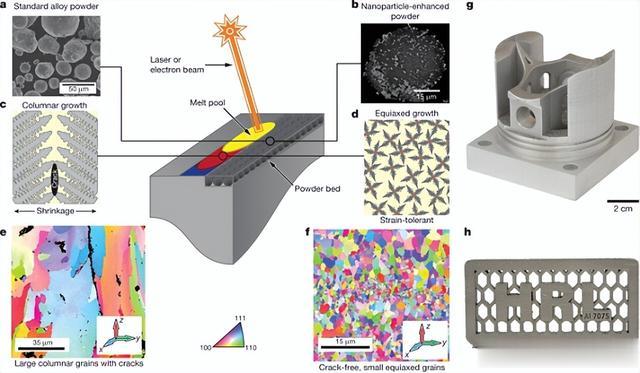
对焊丝成分中的合金元素Ni,Mn,Si,Cr,Mo等均进行了面扫描测试,发现Ni,Mn的分布具有一定趋势,其他元素无明显的趋势,呈弥散分布于组织中。
«——【·结语·】——»
激光诱导-TIG电弧增材制造技术成形的多层多道高强钢薄块试件宏观成形良好、表面平整、无飞溅和金属熔液流淌等问题;截面无明显气孔、裂纹等缺陷,层与层之间冶金结合紧密,致密性优异。

试件不同位置的显微组织因冷却速率的不同而有所差异。顶层组织由板条马氏体、针状贝氏体和部分粒状贝氏体组成;中部组织由呈羽毛状和针状的贝氏体和部分区域的少量板条马氏体组成,底层组织由粒状贝氏体组成。
焊丝的抗拉强度为922MPa,而试件横向平均抗拉强度为1227MPa,纵向平均抗拉强度为1133MPa,抗拉强度明显提升。
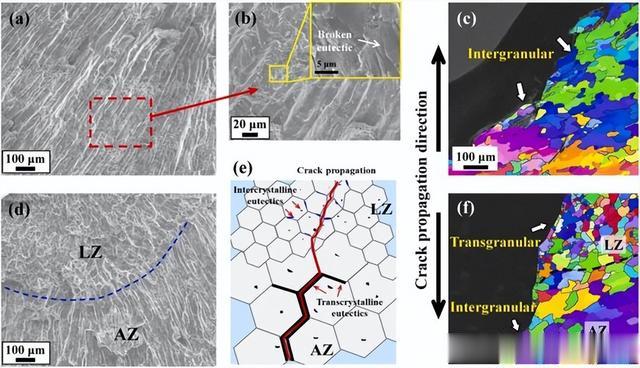
横、纵方向拉伸断口均为韧性断裂;焊丝的伸长率为17.64%,试件横向平均伸长率为14.4%,纵向平均伸长率为12.7%,伸长率有所降低。而试件抗拉强度和伸长率在横纵两个方向存在差异,试件具有各向异性。
试件的显微硬度随距基板距离的增加呈先减小后增大的分层趋势,硬度分布范围为340.0HV~428.6HV,平均硬度为384.3HV。