
文|正经的烧杯
编辑|正经的烧杯
«——【·前言·】——»
金属增材制造技术具有成形接近任意复杂结构的能力,是一种设计制造一体化的变革性技术,选择性激光熔化成形(Selectivelasermelting,简称SLM)技术是近年来发展迅速的金属零部件精密增材制造技术。
它使用高功率密度激光器选择性地熔化金属粉末,直接获得高性能金属零件,并实现复杂金属零件的近净成形,这种加工方法特别适用于制造具有复杂精细结构的金属零件,在航空航天、生物等领域受到了广泛关注。
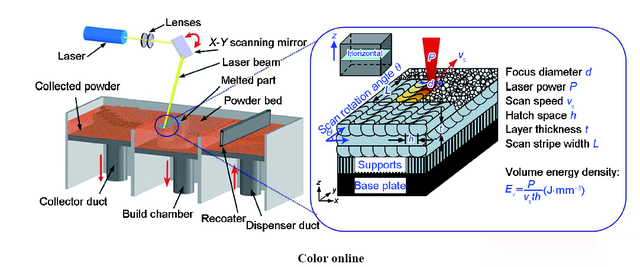
表面粗糙度和磨损性能,是衡量机械零件性能的重要指标,为了改善SLM成形零件的表面质量和磨损性能。
而北京一企业,大量学者进行了深入研究,通过研究了激光能量密度对A1Si10Mg样品表面粗糙度的影响,发现随着激光能量密度的增加,孔隙率和表面粗糙度显著降低,而表面粗糙度缓慢增加。
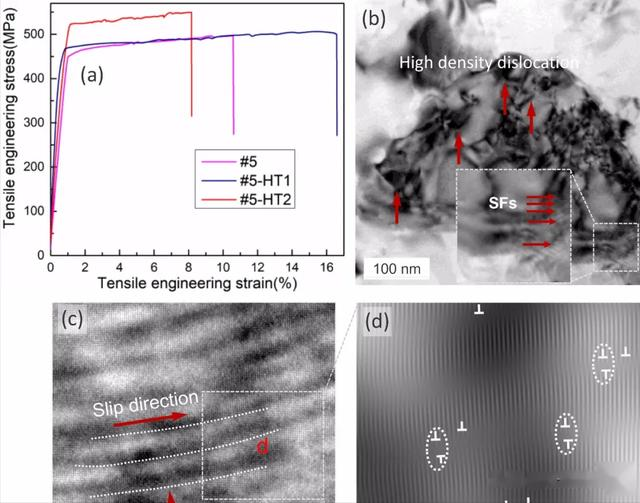
本文基于SLM技术制备了多组316L样件,在样件制备过程中分组进行了0、1、2、3次激光重熔,对不同激光重熔次数下的样件表面利用三维轮廓扫描仪、扫描电子显微镜等进行了表征,利用高速往复摩擦磨损试验机对样件进行了摩擦磨损试验,利用电子分析天平测定了磨损前后的质量。
对表征和磨损性能进行了分析,分析了重熔次数对表面质量和摩擦磨损的影响机理,提出了经济重熔次数概念。
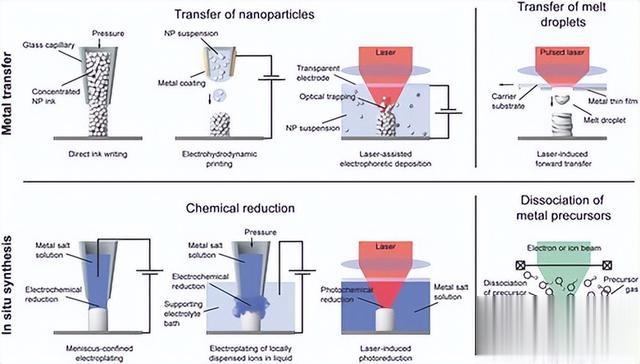
确定了1、2、3次重熔对表面粗糙度和摩擦磨损性能综合改变率,确定了经济重熔次数为2,根据研究成果,给出了经济重熔次数的应用实例,展望了经济重熔次数的应用前景。
«——【·样件制备及测试方法·】——»
首先建立样件三维数字化模型。然后使用切片软件进行切片处理。接下来将切片文件导入SLM增材制造设备进行打印。
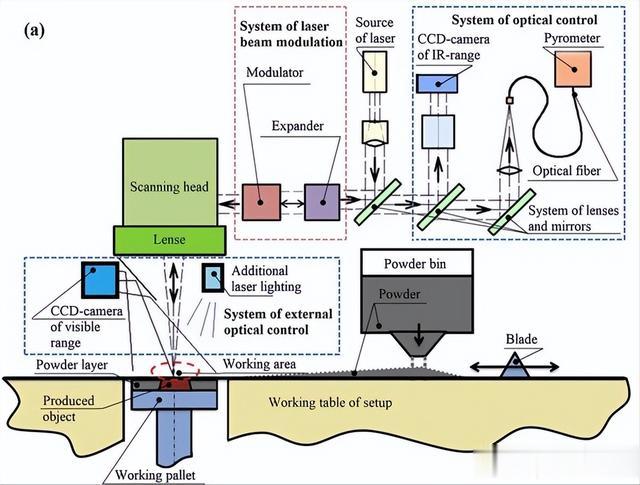
打印过程可分为:对刀、气洗、打印和后处理。打印完成后,关闭打印机,等待设备成形室冷却至室温,氧气含量恢复正常,然后取出带有样件的基板。
然后将基板送至金属电火花线切割机进行切割,切割后,将样件和基板分离(切割之前对样件按照切片时的序号进行标记)。
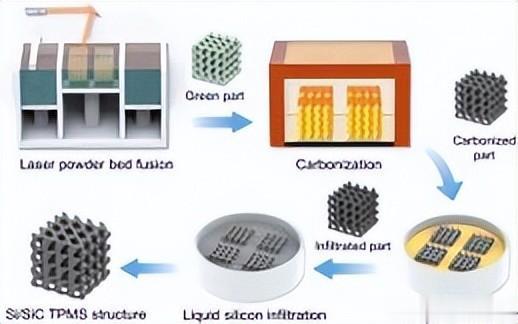
样件切割下来之后,收集样件进行超声波清洗,以去除粘附的粉末,然后,将所有样件送往测试设备进行测试。
测试分为表面粗糙度测试、表面形貌测试和摩擦磨损测试,分析测试结果,探索重熔次数对表面质量和磨损性能的影响机理。所提出的总体流程图如图1所示。
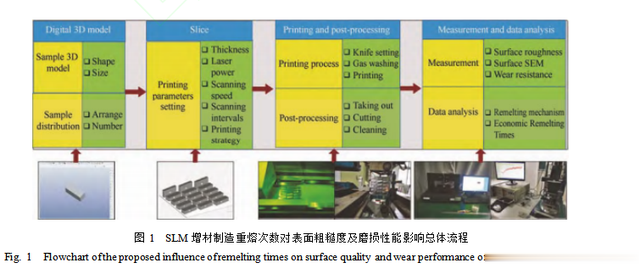
制备样件使用的SLM成形设备是西安铂力特增材技术股份有限公司生产的S210金属打印机,该金属打印机,主机包括最大功率为500W的光纤激光器、自动铺粉系统、氩气循环系统和计算机控制系统。
保护气体为氩气,在制造开始之前,成型室预先填充氩气,将O2含量控制在0.03%以下,用于降低316L不锈钢在成型过程中的氧化程度,粉末参数如表1所示。
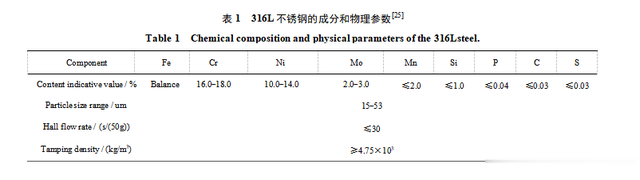
每个加工样件,是一个30mmX10mmX5mm的长方体,三维模型是在三维建模软件Creo5.0中建立的,然后将其保存为st1格式,并导入切片软件Magics21.0。
根据需要数量导入15个(编号为1~15),根据图2所示的编号和布局位置,在切片软件中设置样件加工位置。
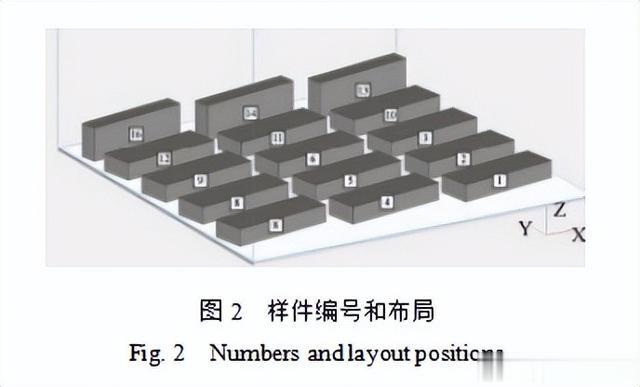
采用增材制造工艺制作试验样件。工艺参数也为西安铂力特增材技术股份有限公司提供的工艺参数SLM-S210-316L-020-BP3.1-V1.0SLM。
1、2、3号样件正常打印(0次重熔),4、5、6号样件在正常打印结束后,在其表面进行一次重熔,7、8、9号样件表面进行二次重熔,10、11、12号样件表面进行三次重熔。
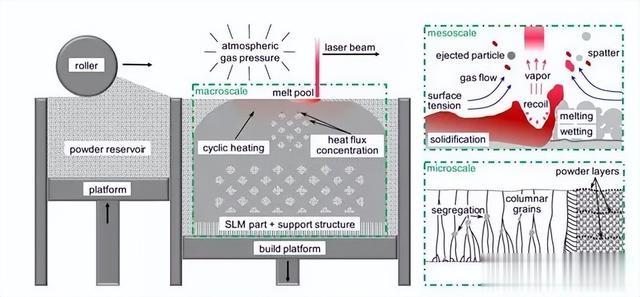
由于样件13-15与1-12高度不一致,将影响1-12表面的重熔,遂在13-15打印了30层(0.6mm)后取消了13~15的打印,在完成切片、对刀和气体清洗(让设备中充满氩气,将氧气含量降至0.03%以下)后,打开打印模式,设备用于样件生产。
在整个增材制造过程完成后,关闭设备,等待设备基板自然冷却至室温,设备成型舱室中的含氧量自然恢复至正常,然后打开舱门,取出带有加工样件的基板,1.2.2后处理切割样品。首先,按照1~12的顺序标记样件。
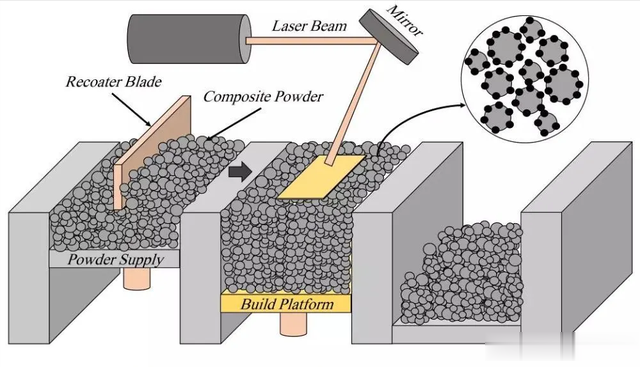
然后将标记好的基板,及其样件带到线切割机进行切割处理,将样件切割下来,线切割机采用的是DK-M中走丝线切割机床,清洁样件,为了去除可能吸附在样件表面的漂浮粉末,清洁切割下来的样件(1~12个样件共有12个,其他13~15个样件先前已取消打印)。
清洗过程,是将样件放入含有无水乙醇的烧杯中,然后将烧杯放入超声波清洗机中30min。
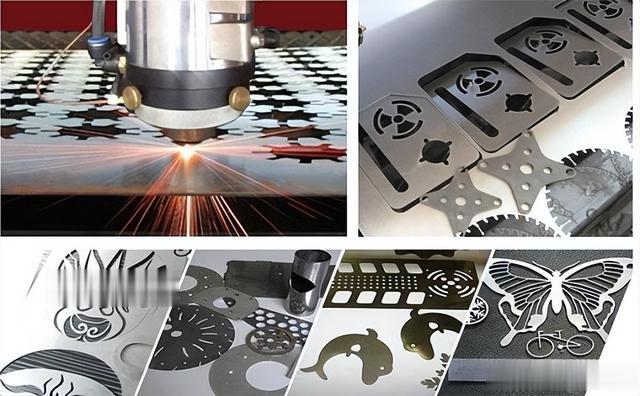
测量表面质量,使用共焦三维轮廊测量仪对12个样件的外观和三维形态进行全方位扫描,然后,使用分析软件提取扫描的数据,获得三维轮廓、平面度、表面粗糙度、高差和接缝宽度等数据。
为了避免边界对结果的影响,测量时选择每个样件表面的中间部位,在测量时,仪器的扫描范围设置为5mmX15mm;扫描速度设置13.5mm/s,扫描间隔设置为0.02mm。
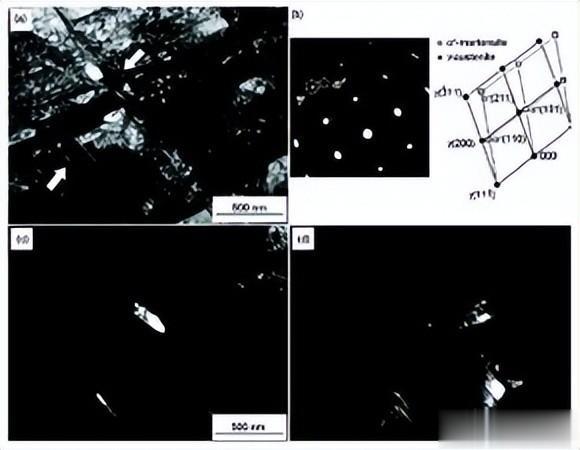
表面粗糙度值的评定,表面粗糙度会影响零件的不同触觉、外观和感觉,也会影响零件与其他物体接触时的磨损量或紧密度,根据增材制造零件的实际应用要求,选择了对零件的粗糙度评定、疲劳寿命和摩擦阻力影响较大的S-、Sv、Sa、Sa进行测量。可以由式(1)来表示:
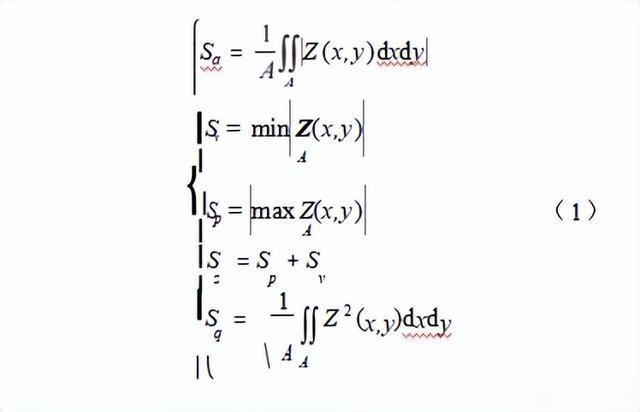
式(1)中,S。是算术平均高度,用于表示每个点相对于表面平均表面的高度差绝对值的平均值,使用表面上的所有凹凸进行计算,通常用于评估表面粗糙度;S,是最大谷深,用于表示定义区域内最低点高度的绝对值,该值影响零件的疲劳寿命;S,是最大峰值高度。
表示定义区域中最高点的高度,S是最大高度,定义区域内的最大峰高和最大谷深之和影响零件与其他物体相互作用时的摩擦力s,是高度的标准偏差;z(x,y)是测量区域中点(x,y)的测量凹凸高度值。
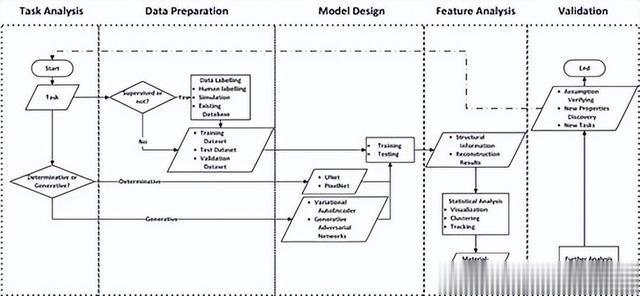
测量样品形貌,样品形貌采用扫描电子显微镜(简称SEM)测量。对每一个样件进行逐一扫描测量,扫描电子显微镜测量时的参数根据样品厚度操作时适时调整,扫描电压为15.0~20.0ky,扫描距离12.2~20.4mm。
在HSR-2M型高速往复摩擦磨损试验机进行摩擦磨损试验,本次摩擦磨损试验采取的摩擦形式为高速往复式摩擦,上摩擦副采用直径为4mm的Al2O₃陶瓷球,陶瓷球硬度为91HRA,下摩擦副为待测试样。
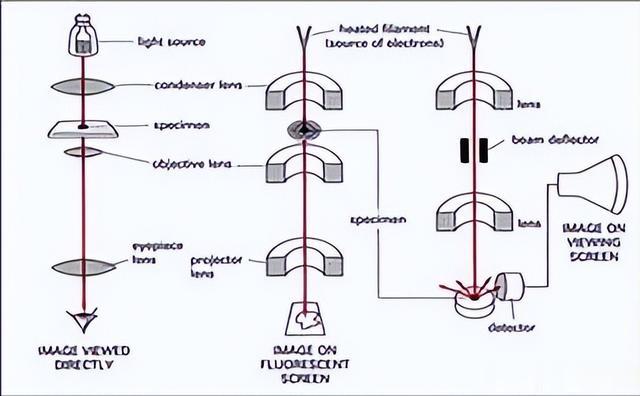
实验中工作载荷为1N,摩擦试验时间为5min,往复长度5mm,运行速度500t/m,采样频率1Hz。
与设备相连的计算机,自动记录摩擦因数曲线及相关数据,在试样磨损试验前、后都经过超声波清洗30min,清洗后在烘干箱中烘干。烘干后分别用电子分析天平记录试样摩擦磨损前、后的质量。
«——【·结果与讨论·】——»
样件SLM增材制造过程和结果如图3所示。
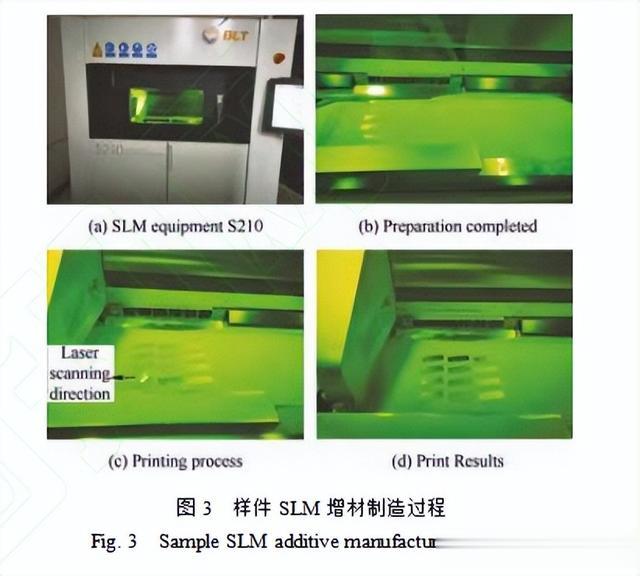
样件增材制造过程完成后,等待基板冷却至室温,成型室中的氧气含量逐渐恢复至正常,然后打开设备成型室舱门,取出基板,将基板拿到线切割设备上切割,将样件切割下来。切割过程及结果如图4所示。
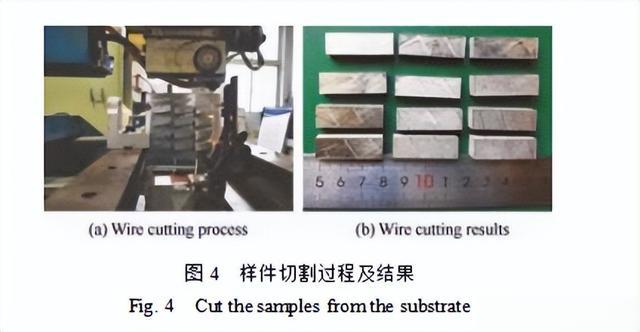
在超声波清洗和吹风干燥后,对样件进行逐一测量表面轮廓和表面粗糙度,三维轮廓仪的表面轮廓、表面粗糙度测量过程和测量结果如图5所示(图中以11号样件上表面的测量过程和结果为例)。
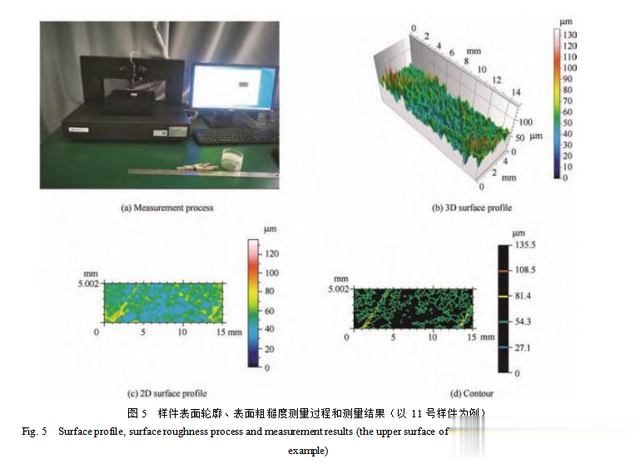
对同一重熔次数下的三个样件测量数值取平均值,可得样件表面粗糙度与重熔次数关系如图6所示。
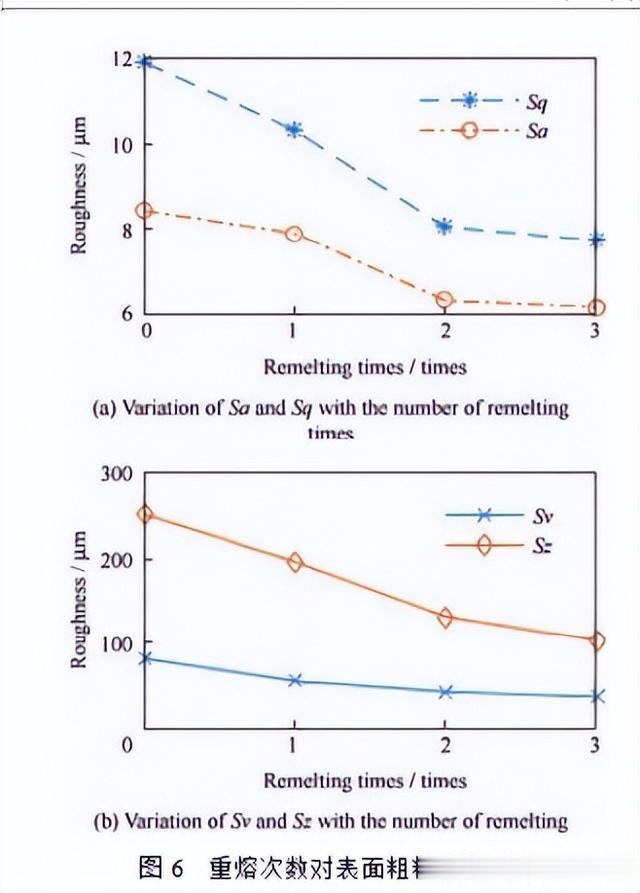
由图6中可以看出,样件表面粗糙度Sv、Sz数值比Sq、Sa大一个数量级。表面粗糙度Sa、Sq、Sv、Sz均随重熔次数的增加,逐渐降低。
3次重熔后,Sa、Sq、Sv、Sz较0次重熔(正常打印),数值分别从8.437、11.88、82.68、252.2μm降低到了6.18、7.735、37.597、104.36μm,分别降低26.75%、34.89%、54.53%、58.62%。但是不同重熔次数改变的表面粗糙度值降低的幅度不同。
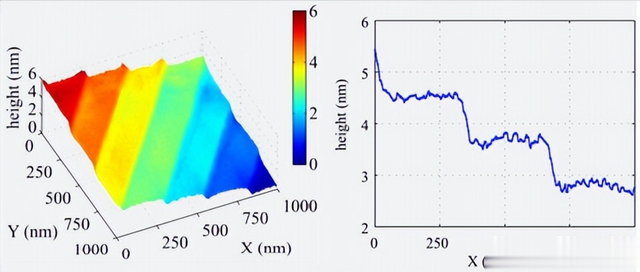
由图7可知,由于SLM激光选区增材制造粉末熔融逐层累加的特点,正常打印结束后制件表面(如图7a、7b所示)存在许多突出的球形颗粒(图中椭圆标出部分),和很深的激光熔接痕。
在1次重熔后(如图7c、7d所示),突出的球形颗粒大幅减少,且球形颗粒基本融陷,不再具备完整的球形。
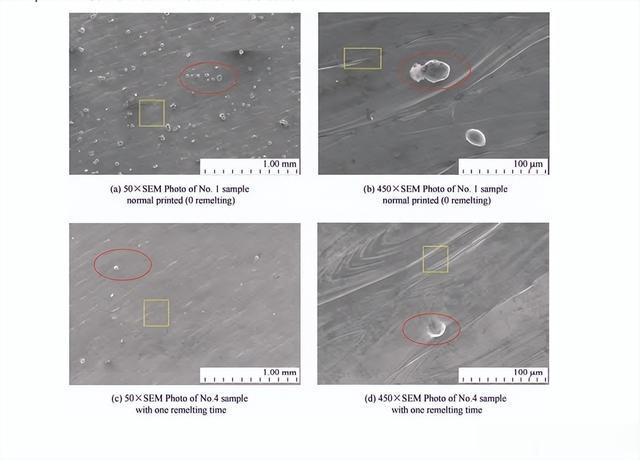
激光熔接痕变浅;在2次重熔后(如图7e、7f所示),球形颗粒继续变少,很多融陷,只剩小小的一点,激光熔接痕继续变细变浅;在3次重熔后(如图7g、7h所示),突出的球形颗粒基本消失不见,激光熔接痕继续变浅,几乎与周围区域保持一致。
可以发现多次重熔能够降低表面粗糙度,是因为每次重熔都会使表面吸附的粉末颗粒及熔接痕进一步融化融陷,直至消失。
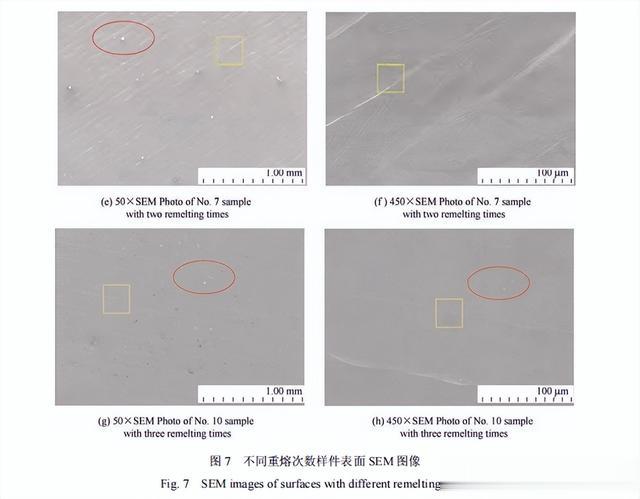
相邻熔道搭接处的“峰谷”现象得到抑制,孔隙和球化等缺陷逐渐被修复,表面变得更加平整,但是重熔次数越多,时间成本、能量消耗成本就会越高,在实际生产过程中并不是重熔次数越多越好。因此,在保证表面质量提升的前提下选择合适的重熔次数是必要的。
摩擦磨损试验机记录的摩擦阻力数据,如图8所示(受图幅所限,随机选取了不同重熔次数组别中具有代表性的样件,图中给出了1、5、8、11号样件摩擦因数变化情况)。
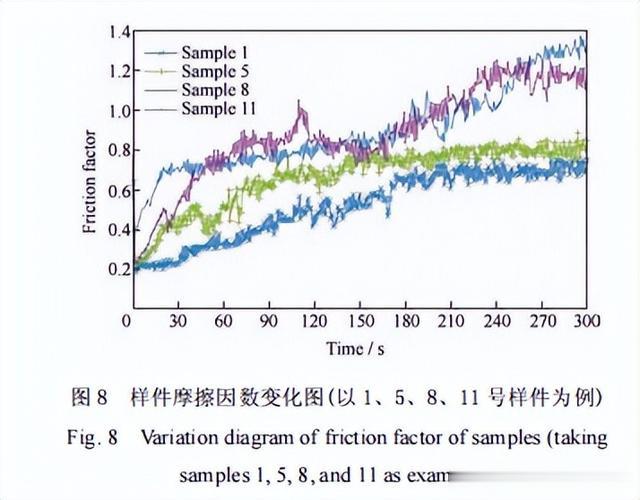
图8中,1、5、8、11样件分别是重熔次数0(正常打印)、1、2、3次的典型代表。全部样件摩擦因数变化都遵从逐步波动增大,然后在较大值附近平稳波动的整体变化情况。
随着重熔次数的增加,摩擦阻力逐步增加至较大值波动的时间越短,这与重熔次数提升了零件表面质量,减少了“球形颗粒”有关,表面球形颗粒越少,摩擦副与较大平整、洁净面接触的越多,摩擦阻力越大。
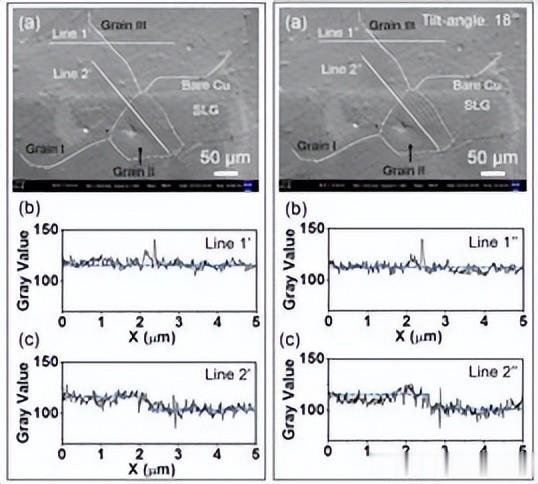
重熔次数大于2后,样件瞬时最大摩擦因数在磨损实验的后半段出现了大于1的情况,这是由于多次重熔后,样件表面非常洁净,导致摩擦副接触非常紧密,在发生明显滑动之前出现“接点增长”。
接点面积不断增大,致使摩擦力超过正压力,摩擦因数大于1。对每个样件磨损前后都进行30min超声清洗,清洗后烘干,利用电子天平测出每个样件磨损前后质量。
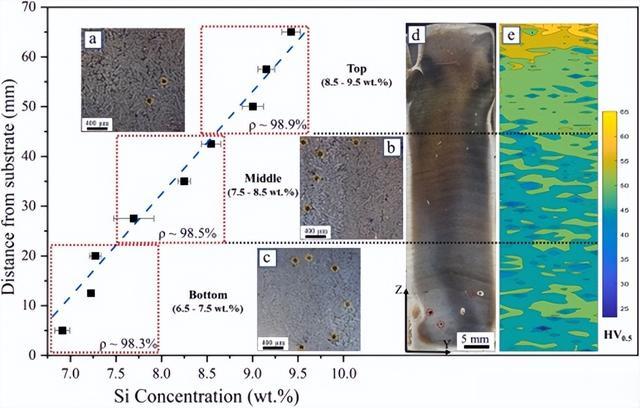
«——【·结语·】——»
采用SLM增材制造设备制备0、1、2、3次激光重熔次数下的316L样件,对样件进行表面表征和摩擦磨损性能试验,对试验过程中所出现的现象进行了分析。
SLM增材制造样件表面粗糙度随重熔次数的增加而逐渐减小,平均摩擦因数随重熔次数的增加逐渐增大,质量磨损量随重熔次数的增加逐步减小。

造成上述变化的原因是,每次重熔都会使样件表面吸附的粉末颗粒及熔接痕进一步融化融陷,直至消失,相邻熔道搭接处的“峰谷”现象得到抑制,孔隙和球化等缺陷逐渐被修复,表面变得更加平整。
不同重熔次数对表面粗糙度和磨损改变的程度不同,提出了经济重熔次数概念,确定了经济重熔次数为2。
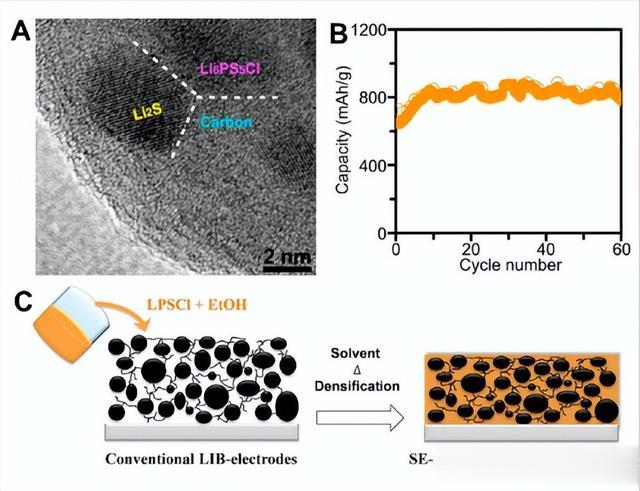
经济重熔次数不仅可以应用于SLM增材制造样件表面处理,也可以用于SLM增材制造样件逐层累积的全过程;在矿山机械及其他有表面质量和耐磨性能提升需求的其他机械领域都有广阔的应用前景;其概念还可以拓展到其他制造形式。