
文|正经的烧杯
编辑|正经的烧杯
«——【·前言·】——»
高压电缆线路是城市电网安全供电系统的重要组成部分,然而近年来高压电缆频繁发生缓冲层烧蚀故障,主要集中于皱纹铝护套结构的高压电缆。
据不完全统计,2017年—2022年,国内主要城市因高压电缆缓冲层烧蚀缺陷引发的电缆本体绝缘击穿故障比例超过80%,造成了巨大的经济损失。
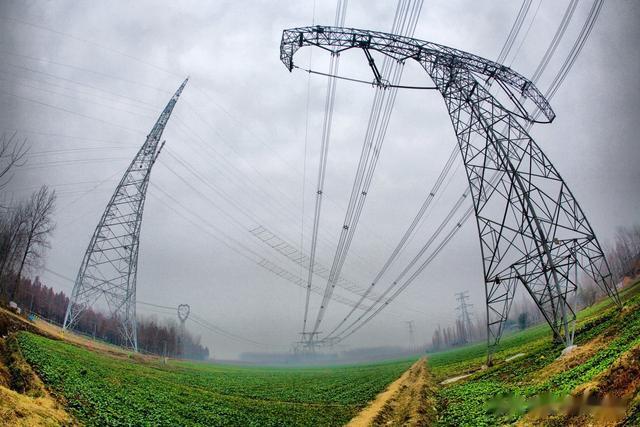
且现阶段存量电缆中仍有大量潜伏性缺陷未被检出,给电缆线路的安全稳定运行带来了极大隐患,因此开展高压电缆缓冲层烧蚀缺陷检测技术的研究具有重要意义。
2022年12月,由某公司自主研发的高压电缆缓冲层烧蚀修复技术在某供电公司110kV大长度高压电缆线路中成功应用,且对已修复的电缆用红外探测仪检测,发现烧蚀区域产生的发热点全部消失,达到应用效果。
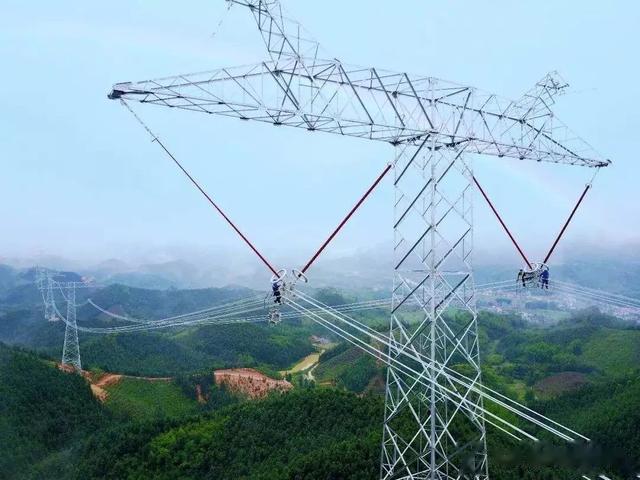
国内已针对高压电缆缓冲层烧蚀缺陷检测技术开展了相关研究。通过X射线成像检测到了高压电缆缓冲层烧蚀缺陷,并通过电缆解体验证了X射线检测的可靠性。
然而X射线成像受电缆敷设环境影响较大,且会对人体造成较高的损伤,某专家采用宽频阻抗谱检测到了高压电缆缓冲层烧蚀缺陷,但仅能粗略判断电缆中烧蚀故障的位置,无法进行精准定位。
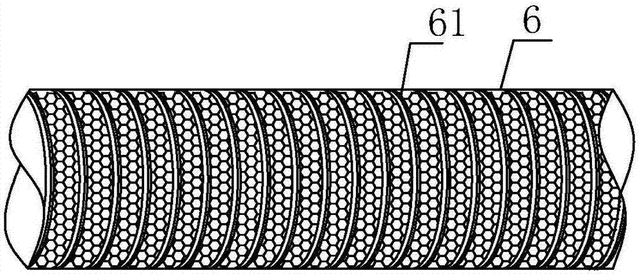
通过研究了高压电缆缓冲层烧蚀缺陷的局部放电检测技术,能够检出电缆中的部分烧蚀缺陷,但在缓冲层电阻率较高、缓冲层与铝护套间隙较大等情况下均无法检测到局部放电信号。
可以看出上述方法的准确度、可操作性以及推广度均难以满足现阶段存量电缆缓冲层烧蚀缺陷检测的需求,因此急需开展缓冲层烧蚀缺陷检测方法的深入研究。
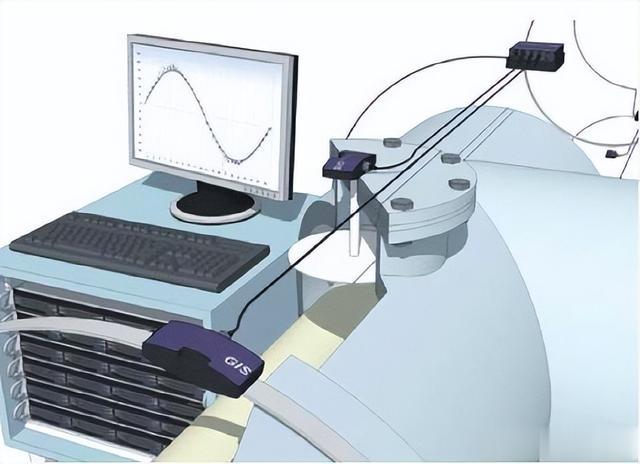
超声检测技术是一种无损检测的重要手段,可以有效检出电力设备内部的多种缺陷,有望成为潜在的电缆缓冲层烧蚀缺陷检测方法。目前已有少数学者开展了相关方面的研究。
基于当前研究现状,文中首次对基于铝护套内表面粗糙度的高压电缆缓冲层烧蚀缺陷的超声检测方法进行了研究,开展了潮湿条件下缓冲层烧蚀模拟实验,通过激光共聚焦显微镜以及电化学阻抗谱测试研究了烧蚀过程中铝片表面粗糙度与烧蚀严重程度的关联。
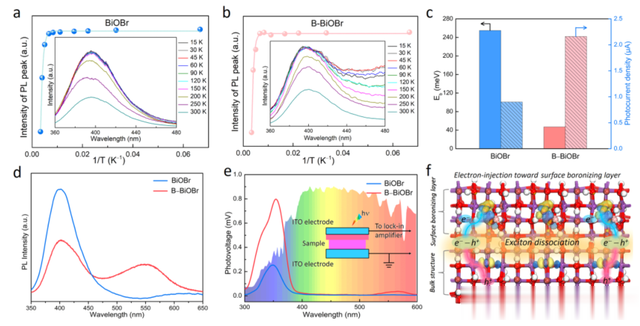
其次对烧蚀后的铝片开展了超声检测研究,并基于超声检测波形推算出了铝片内表面粗糙度的变化,推算结果与铝片的实际粗糙度变化相对应,并可用于判断缓冲层烧蚀的严重程度,文中结果为开发高压电缆缓冲层烧蚀缺陷的超声检测技术提供了研究基础。
«——【·实验方法·】——»
采用商用缓冲层材料、电工铝片以及半导电屏蔽材料开展烧蚀模拟实验,试样厚度分别为2cm、2cm、1cm,尺寸均为3cm×3cm。
向缓冲层试样中均匀注入1mL蒸馏水模拟潮湿条件下的缓冲层状态,采用砂纸将电工铝片表面打磨光滑,并反复擦拭去除其表面的污垢。
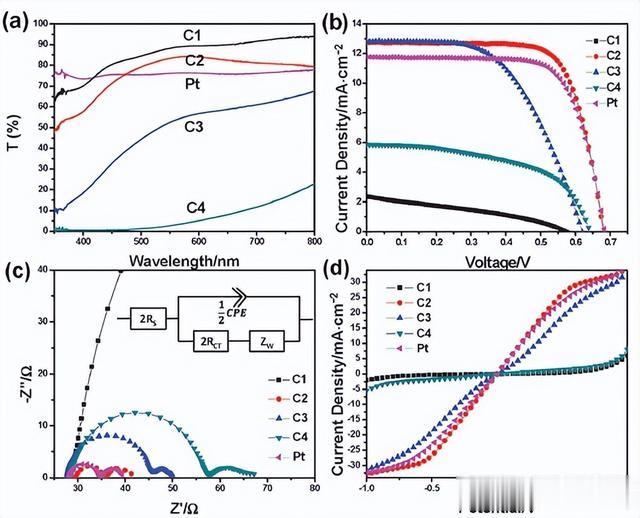
将处理好的试样按图1所示置于电极之间,模拟实际电缆中的缓冲层结构,其中铝片与缓冲层的蓬松棉侧相接触。
对电极两端施加10V交流电压,开展潮湿条件下缓冲层的烧蚀模拟,烧蚀时间分别持续5min、2h、6h,以模拟不同的烧蚀严重程度。
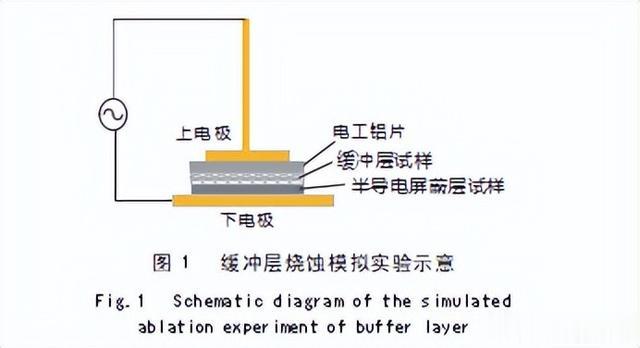
激光共聚焦显微镜实验:采用0LYMPUS-OLS5100型激光共聚焦显微镜对铝片试样表面粗糙度进行测试,透镜倍数为20,视窗尺寸为640μmX640μm。
电化学阻抗谱实验:采用PRINCETON-PARSTATMS电化学工作站对不同烧蚀程度下的铝片试样进行测试。
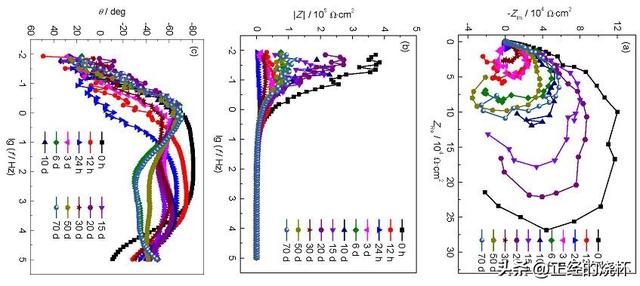
实验采用三电极系统铝片试样为工作电极,对电极采用铂电极,参比电极为饱和甘汞电极,电解质溶液为质量分数0.1%的聚丙烯酸钠阻水粉溶液,测试频率范围为10'~10°Hz,交流电压幅值为10my。
超声检测实验:采用OLYMPUS-OMNISCANX3型超声探测仪对铝片试样进行检测,测试模式为幅值扫描,检测频率为7.5MHz,超声探头测试面的直径为1cm,楔块直径为2cm。
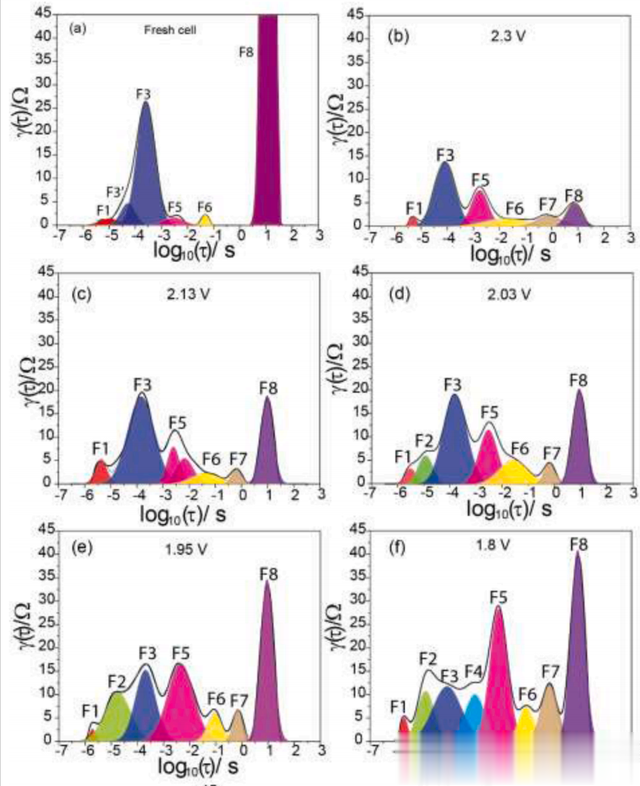
«——【·结果分析·】——»
烧蚀过程中铝片表面形貌变化:经过不同烧蚀时间后铝片的表面形貌如图2所示,缓冲层表面的形貌如图3所示,可以看出烧蚀后铝片表面出现了明显的腐蚀痕迹,缓冲层表面生成了白色物质,该物质为潮湿条件下缓冲层烧蚀过程中电化学反应的产物。
并且随着烧蚀时间的增加,铝片表面的腐蚀程度逐渐加深,缓冲层表面的白色物质逐渐增多,表明烧蚀的严重程度逐渐加重。
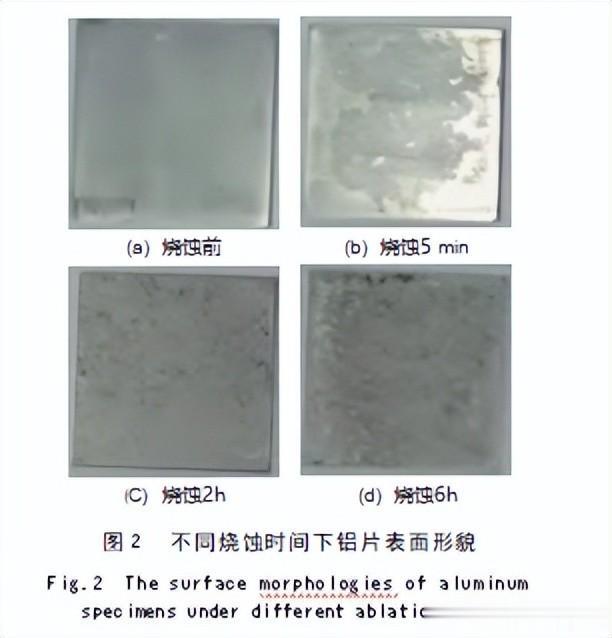
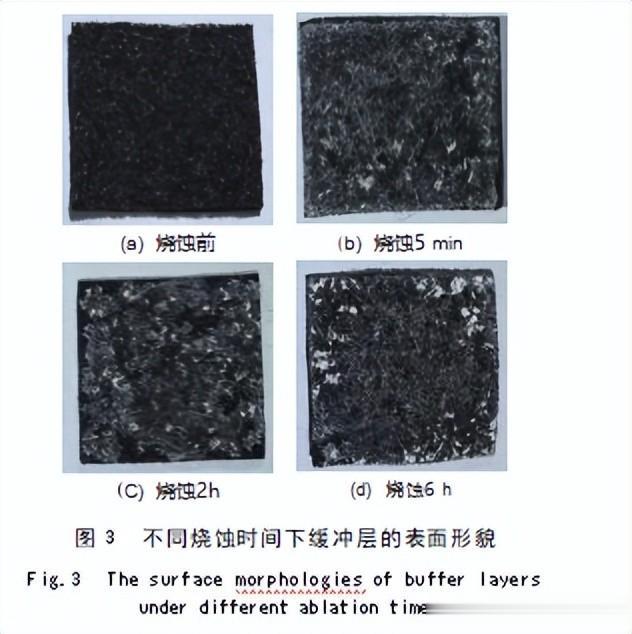
采用激光共聚焦显微镜对铝片表面的三维形貌进行测试,结果如图4所示。
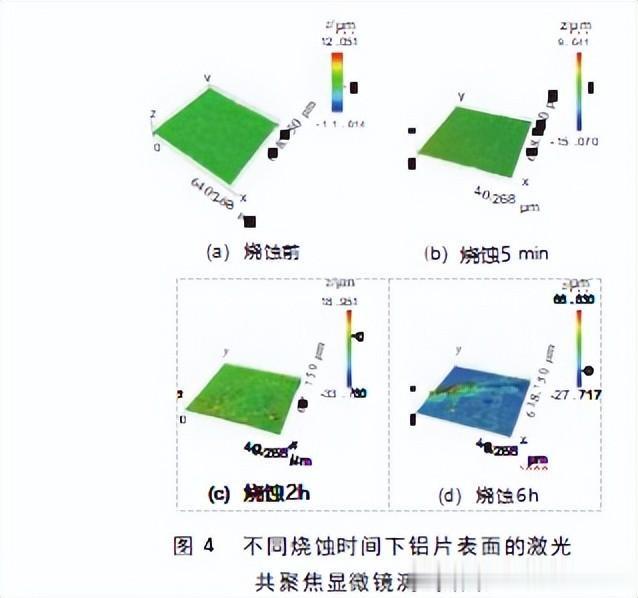
根据铝片的表面形貌特征,能够计算得到铝片表面的均方根粗糙度Sq。计算公式为:

式中:A为测试面积;x、y为测试面的坐标;z(x,y)为测试表面的高度关于位置的函数。
根据式(1),计算得到不同烧蚀时间下的铝片表面粗糙度分别为1.13μm、1.28μm、3.11μm、9.08μm。可以看出,随着烧蚀时间的增加,铝片表面的粗糙度逐渐增加。
不同烧蚀时间下铝片的电化学阻抗谱测试结果如图5所示,其中Z′、-Z″分别为阻抗实部和虚部。
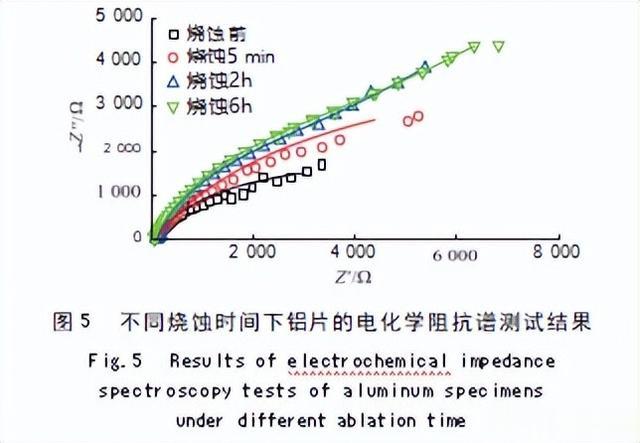
基于电化学腐蚀电池的等效电路模型,采用Zview软件对电化学阻抗谱曲线进行拟合,得到不同烧蚀时间下铝片的电荷转移阻抗,分别为1617Ω、2181Ω、3623Ω、4959Ω。
可以看出随着烧蚀时间的增加,铝片表面的电荷转移阻抗逐渐增加,表明铝片表面的腐蚀过程逐渐趋于完善,腐蚀程度逐渐增加。
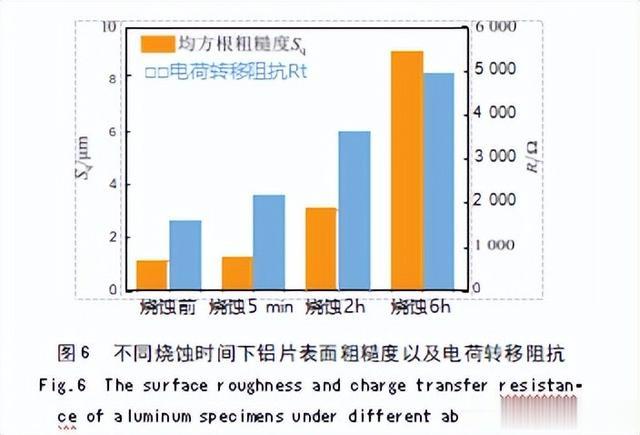
图6给出了铝片表面粗糙度以及电荷转移阻抗随烧蚀时间的变化可以看出,随着烧蚀时间的增加,铝片的表面粗糙度以及电荷转移阻抗均逐渐增加,且铝片的表面粗糙度越大,对应的电荷转移阻抗也越高。
铝片的表面粗糙度能在一定程度上反映出铝片的腐蚀程度,粗糙度越大表明腐蚀过程越趋于完善,腐蚀程度越大。
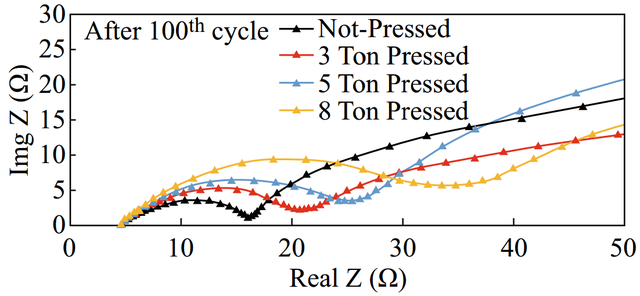
因此通过检测铝片的表面粗糙度,能够推断出铝片的腐蚀程度,进而判断缓冲层的烧蚀严重程度,基于铝片表面粗糙度的缓冲层烧蚀缺陷超声检测分析图7为超声检测实验的示意图。
其中超声探头用于发出和接受超声波信号,有机玻璃楔块用于控制超声波束的角度,耦合剂用于排出楔块与铝片之间的空气,使声波能有效传导至铝片,通常选用水作为耦合剂。
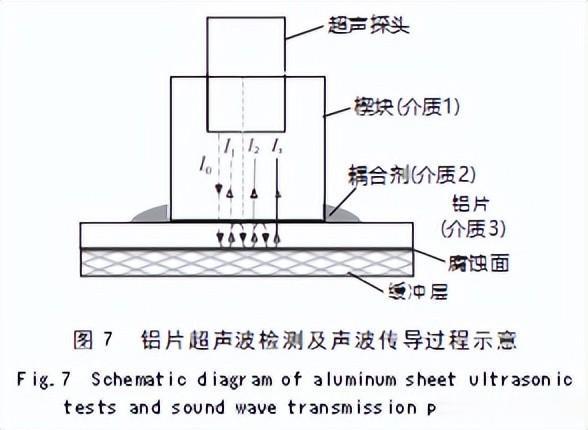
超声波传播到2种不同介质的界面处时会发生透射和反射,反射系数与透射系数可由式(2)、式(3)计算得到。
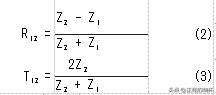
式中:R12、T12分别为超声波从介质1向介质2传播过程中在界面处的反射系数与透射系数;Z1、Z2分别为介质1和介质2的声阻抗不同介质的声阻抗如表1所示。
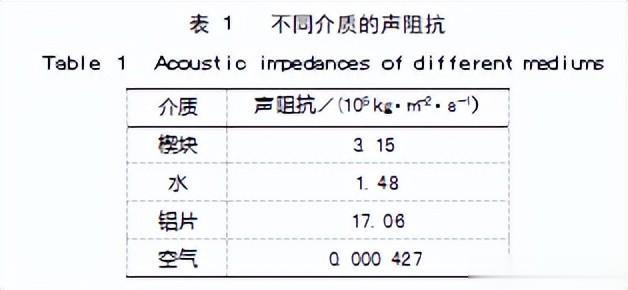
为简化图7所示超声波传导过程,文中仅考虑超声波在铝片内部的反射与透射过程。
超声探头将测到的信号传输到示波器中,显示出入射波以及各回波的信号,如图8所示。
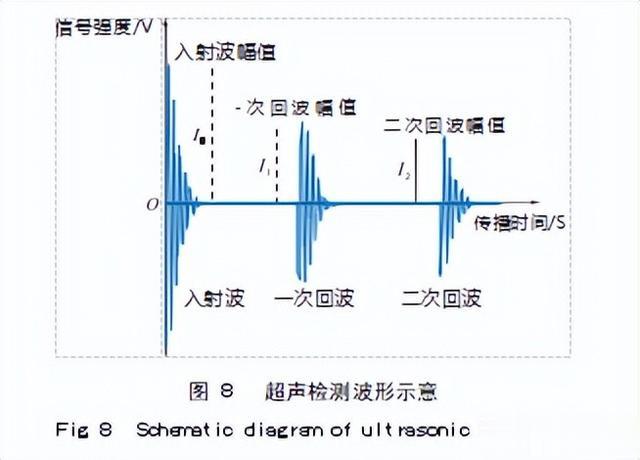
将测得的各回波幅值按入射波信号幅值进行归一化,得到超声波信号幅值的衰减曲线,如图9所示,可以看出超声信号波的幅值随反射次数的增加逐渐衰减。
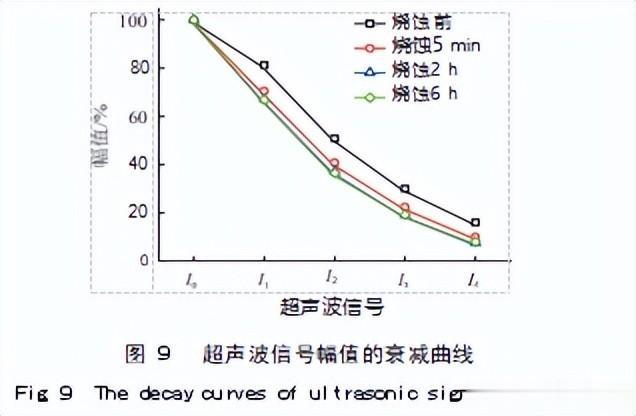
可以看出随着烧蚀时间的增加,铝片表面的均方根粗糙度也逐渐增加,对应于铝片的腐蚀程度逐渐增加,表明缓冲层的烧蚀严重程度逐渐加深,结果如表2所示。
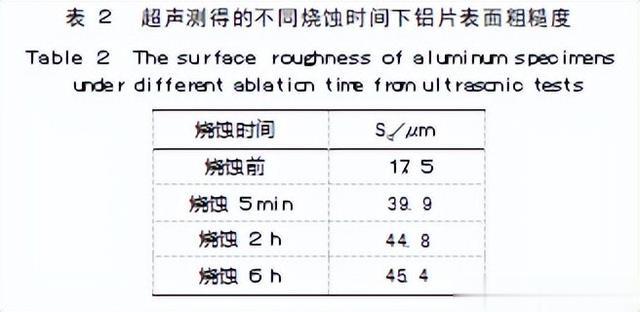
由于超声波在传导至铝护套内表面时基本会被全部反射,因此铝护套与缓冲层之间的空气间隙基本不会影响超声波检测结果。
同时铝护套内表面粗糙度也能够反映缓冲层的体积电阻率大小,当缓冲层体积电阻率较低时(小于5×104Ω·cm),缓冲层中基本不存在高阻性物质,表现为产生严重的电化学腐蚀,此时铝护套内表面粗糙度应较低。

但值得注意的是,计算得到的铝片表面均方根粗糙度与通过激光共聚焦显微镜测得的值有所差异,这可能是因为二者的测量面积以及测试面积存在较大差异,文中所用激光共聚焦显微镜的视窗面积约为0.41mm2,而超声探头的面积约为78.5mm2。
因此通过激光共聚焦显微镜测量得到的是铝片表面局部微区的粗糙度,而通过超声波检测得到的是铝片表面更大范围的平均粗糙度,这导致2种方法的粗糙度测量结果有所差异。

后续将通过减小超声探头检测面积、提高超声检测频率等方式进一步优化超声检测方法,以测得更准确的粗糙度。
«——【·结语·】——»
文中研究了基于铝护套表面粗糙度的高压电缆缓冲层烧蚀缺陷超声检测方法,主要结论如下。
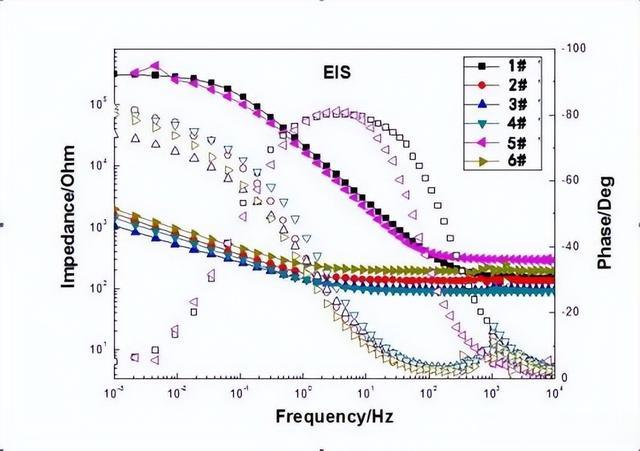
开展了潮湿条件下的缓冲层烧蚀模拟实验,发现铝片的表面粗糙度以及电荷转移阻抗均随烧蚀时间逐渐增加,缓冲层烧蚀严重程度也相应增加,表明铝片的表面粗糙度能够反映潮湿条件下缓冲层烧蚀缺陷的严重程度。
通过对铝片的上表面施加超声信号,并根据相邻回波信号的幅值比可以推算出铝片下侧腐蚀面的粗糙度。
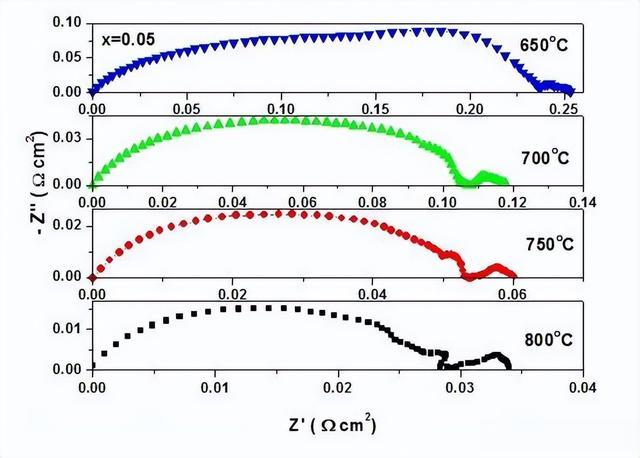
在不同烧蚀程度下,铝片粗糙度的推算结果与实际测量结果具有相同的变化趋势,因此可以用于判断缓冲层烧蚀缺陷的严重程度。
该方法在实际电缆中应用时,需要将电缆外护套剥离并测试铝护套波谷处的超声波回波信号特性,以此计算得到铝护套内表面粗糙度,从而判断该处的烧蚀严重程度。