
文|正经的烧杯
编辑|正经的烧杯
«——【·前言·】——»
随着科学技术的进步,微电子机械系统(MEMS)由于其小体积、低惯性、轻质量、低能耗、低成本、稳定性能、可批量生产和集成化等特点,在信息、航天、电子、医疗、生物、环境等领域具有广阔的应用前景。
然而与传统机械零件相比,MEMS零件的尺寸较小,表面积与体积之比明显增大,这导致了其所受粘附力和摩擦力的相对增加。
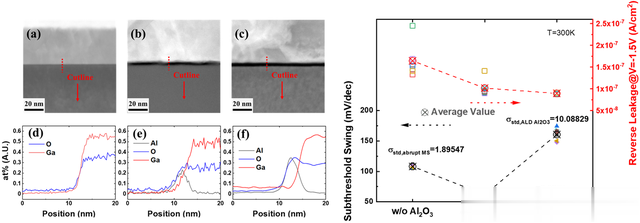
因此在MEMS零件表面进行适当的改性对于提高其可靠性至关重要。其中单晶硅及其氧化物被广泛应用于制造MEMS零件,国内外大量学者对改善硅材料的摩擦学性能进行了大量研究。
某公司已经对表面织构减摩抗磨和改善温度分布的能力进行了一定的研究,但是大部分研究主要针对凹坑、矩形类的单个离散型织构,对环形、网状类的连续型织构的研究较少,并且对表面织构改善单晶硅材料摩擦生热的研究也较少。
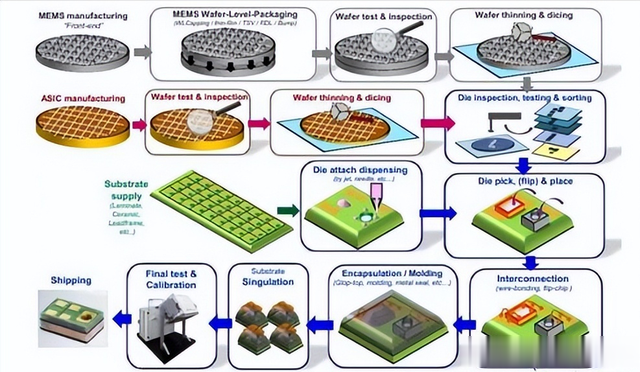
鉴于此本研究采用目前较为成熟的激光加工技术在单晶硅表面制备了不同间距和图案的微织构,并研究了其对单晶硅表面摩擦性能,结构强度及散热能力的影响,旨在为MEMS零件的减摩和抗磨提供一定的指导。
«——【·摩擦磨损实验·】——»
使用MRTR-1摩擦磨损实验仪,对单晶硅试样进行回转式摩擦磨损实验,并记录实验数据绘制摩擦系数曲线。
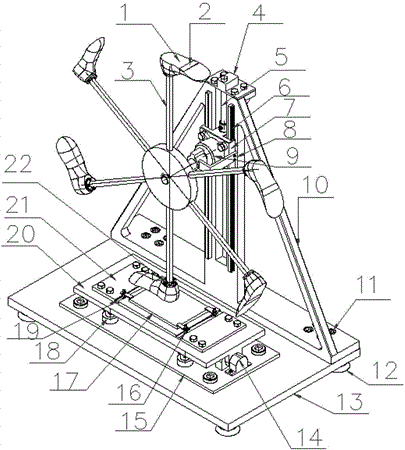
在MEMS的实际工作中,一对摩擦副的材料应为相同的,但由于单晶硅销较难加工,并且在装夹至实验机上时极易损坏,因此上试样选用304不锈钢圆柱形销,其尺寸为直径d=3mm、高度18mm。
下试样选用单晶硅片,其为购自顺生电子科技20mm×20mm×0.7mm的单面抛光正方形单晶硅片,物理性质见表1。虽然摩擦副材料与实际情况有差异,但分析得到的实验结论是相通的。

首先使用制图软件(AutoCAD)绘制表面织构图案,如图1。之后使用型号为X355-3A的紫外激光器在单晶硅片表面制备宽度为0.1mm,间距分别为0.1mm、0.2mm、0.3mm的不同图案的织构,其深度约为0.2mm。
激光输出功率、发射波长、重复频率、扫描速度分别为3W、355nm、30KHz、800mm/s。之后将织构化的单晶硅片放入KXT-163超声波清洗机中进行清洗。
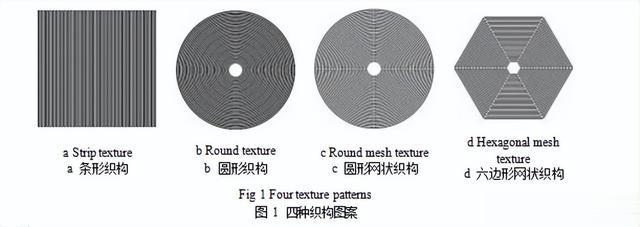
清洗时将硅片抛光面向下放入烧杯中,加入无水乙醇浸没单晶硅片,清洗时间为10分钟。实验前使用蔡司G300型电子显微镜拍摄的激光加工织构后的单晶硅表面形貌。
使用MRTR-1多功能摩擦磨损实验机对试样进行回转式摩擦磨损实验。上试样装夹在夹具上,下试样单晶硅片固定在转动盘上,使销的端面与下试样平行接触。实验时上试样固定不动,下试样随转动盘转动,实现回转运动式的摩擦磨损实验。
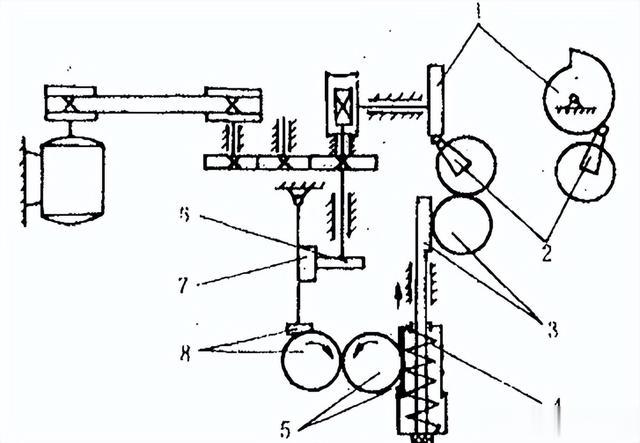
实验中上下试样为干摩擦接触,参考某专家得到的实验结论,选择实验载荷0.5N,转速300r/min,为了保证数据结果稳定可靠,实验进行120min。
固定载荷和转速不变,改变下试样的织构形貌以及织构间距,实验分组如表2所示,每组实验重复三次,实验数据取平均值。
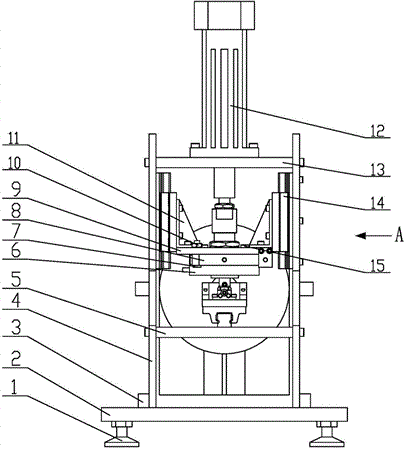
实验中多功能摩擦磨损实验仪自动采集得到的摩擦系数,用于之后的结果分析。实验后用体式显微镜XTL-100观察下试样的表面形貌。实验前后采用电子天平称量试样的质量,通过式(1)计算磨损率k。

式中:V为磨损体积,X为转动距离,为垂直载荷。
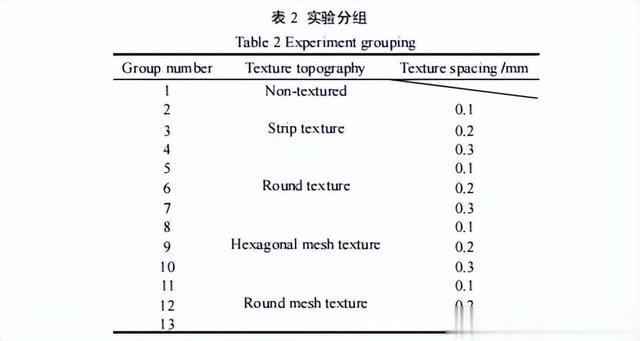
«——【·结果与分析·】——»
图2为使用电子显微镜拍摄得到的间距0.1mm织构试样表面,可以看到织构凸峰表面形成许多不规则坑洼,而织构凹槽中也同样存在类似的结构。
这是因为激光加工时,单晶硅被光束刻蚀,部分碎屑飞溅聚集而形成脊状结构。与无织构光滑表面的试样相比,织构表面明显变得更加粗糙。另外,部分织构边缘还存在细小飞刺及一定缺陷。

为了探究织构形状和织构间距对摩擦副表面摩擦性能的影响,分析实验得到的摩擦系数曲线,计算磨损率,得到的结论如下。
图3为不同织构图案的摩擦系数曲线。从图中可以看到,在实验中无织构试样的摩擦系数曲线波动剧烈,加工织构试样摩擦系数曲线则较为平稳。
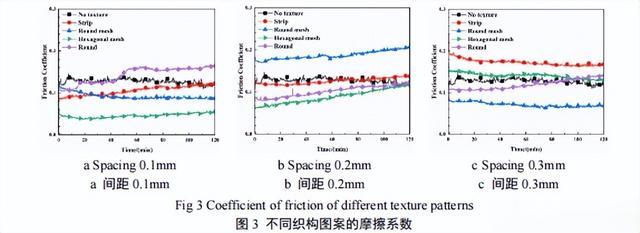
在图3a中间距0.1mm的六边形网状织构具有最低摩擦系数,条形织构的摩擦系数随时间逐渐增加,最后数值接近无织构试样。
而圆形织构在摩擦进行到40min后摩擦系数高于无织构试样,圆形网状织摩擦系数构则随时间逐渐降低。
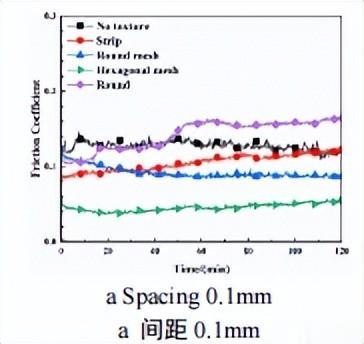
在图3b中,间距0.2mm的各种形状织构摩擦系数均随时间逐渐增加,条形、六边形网状和圆形织构的摩擦系数在实验开始时均低于无织构试样,最后数值和无织构试样接近,而圆形网状织构摩擦系数一直高于无织构试样。
在图3c中,织构间距0.3mm的圆形网状织构具有最低的摩擦系数,圆形织构摩擦系数随时间逐渐上升,并在实验到90min时超过无织构试样。条形织构和六边形网状织构的摩擦系数则一直高于无织构试样。
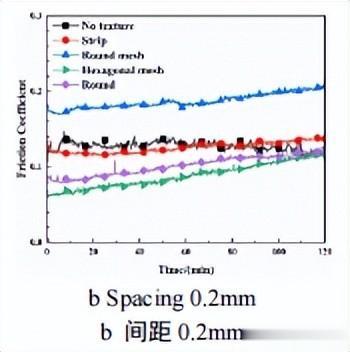
从上述结果中可以看出,在单晶硅表面加工织构并不一定能够降低表面的摩擦系数,这是因为在激光加工织构时在织构表面产生的飞刺和缺陷会增加表面的粗糙度从而导致其摩擦系数变大。
此外所有织构试样对比未加工织构的试样均有更平滑的摩擦系数曲线,并且合适的织构参数能够切实起到降低摩擦副表面摩擦系数的作用。
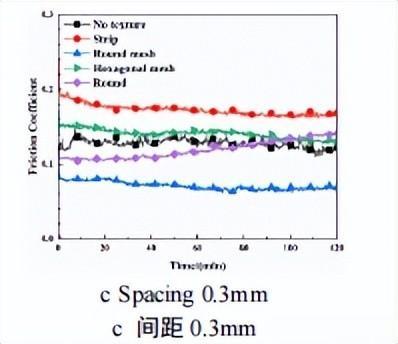
图4为不同织构图案的磨损率从图中可以看到无织构试样的磨损率远高于加工织构的试样。在图4a和图4b中,间距0.1mm和0.2mm的圆形织构具有最低的磨损率。
在图4c中,间距0.3mm的六边形网状织构则具有最低的磨损率。这说明在单晶硅表面加工织构能够有效降低摩擦副在摩擦时的磨损率,对保护材料有明显作用。
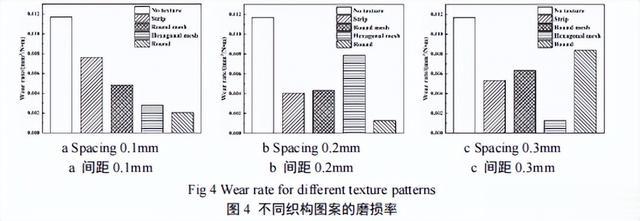
图5所示为织构图案分别为条形、圆形、六边形网状和圆形网状织构情况下不同织构间距的摩擦系数曲线。
从图5a中看到,织构间距0.1mm和0.2mm的条形织构的摩擦系数随时间逐渐增加,而间距0.3mm试样的摩擦系数则随时间逐渐减小。
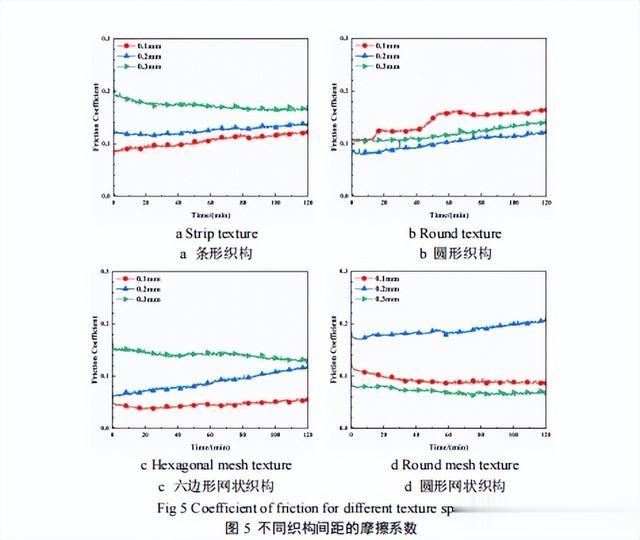
在图5b中,三种间距的圆形织构试样的摩擦系数均随时间逐渐增大,间距0.1mm的试样在实验50min后摩擦系数超过无织构试样,间距0.3mm的试样则是在80min后摩擦系数超过无织构试样。
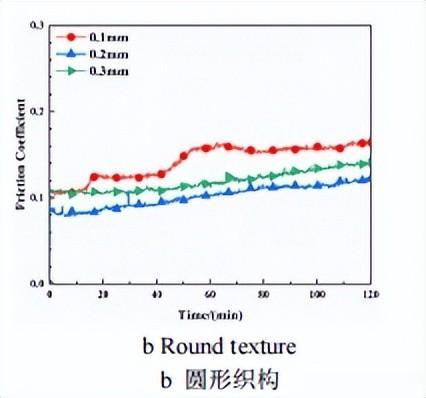
在图5c中,间距0.1mm的六边形网状织构具有明显的减摩效果,间距0.2mm的试样在实验中摩擦系数逐渐增大,并且在110min后和无织构试样相近,间距0.3mm的试样摩擦系数则一直高于无织构试样。
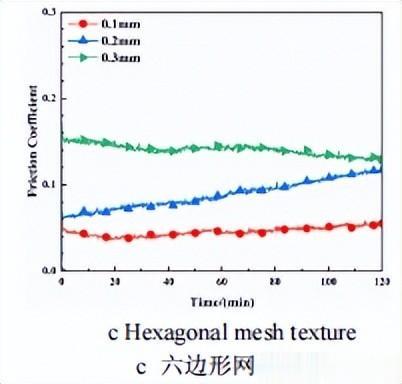
在图5d中,间距0.2mm的圆形网状织构试样的摩擦系数远高于无织构试样,间距0.1mm和0.2mm的试样摩擦系数低于无织构试样,具有较好的减摩效果。
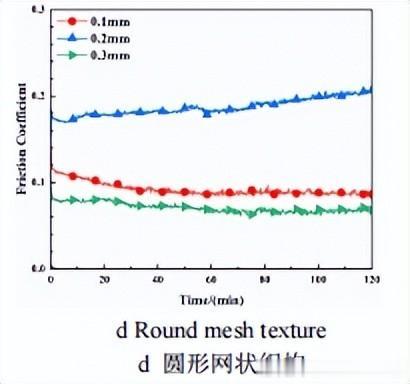
上述结果说明,织构间距对不同形状的织构图案的影响不同,并且除了间距0.3mm的条形织构和六边形网状织构以及间距0.2mm的圆形网状织构以外的试样,摩擦系数均在某个时段之前小于无织构试样,这说明不同织构参数的织构有效工作时间不同。
图6为不同织构间距的磨损率。对于条形织构,圆形织构和圆形网状织构来说,间距0.2mm时具有最低的磨损率,而六边形网状织构在间距0.3mm时有最小的磨损率。
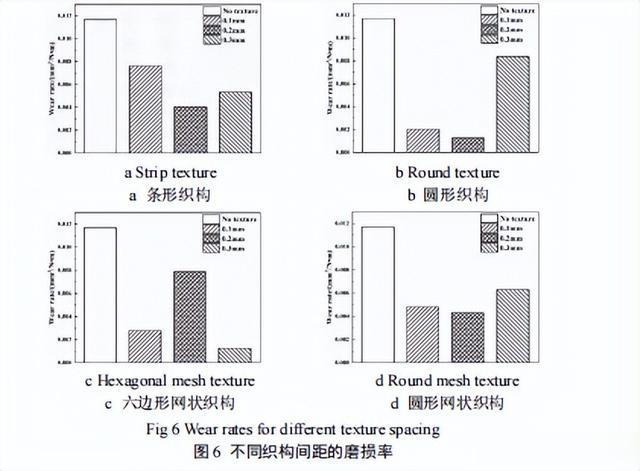
综上所述表面织构对单晶硅表面摩擦性能的影响可以分为对摩擦系数和磨损率的影响。激光加工表面织构虽然在一定程度上会增加单晶硅表面的粗糙度,使摩擦系数变大。
但是织构能够收集磨损磨屑并使摩擦系数保持稳定,对保护摩擦副表面有重要意义,而在减少磨损率方面,表面织构较无织构试样的效果显著,能够有效减少摩擦磨损。
图7为实验后织构试样的宏观磨损形貌图,能看到较为明显的摩擦痕迹。使用光学显微镜观察实验后试样表面的磨损形貌,单晶硅试样微观摩擦磨损形貌如图8所示。
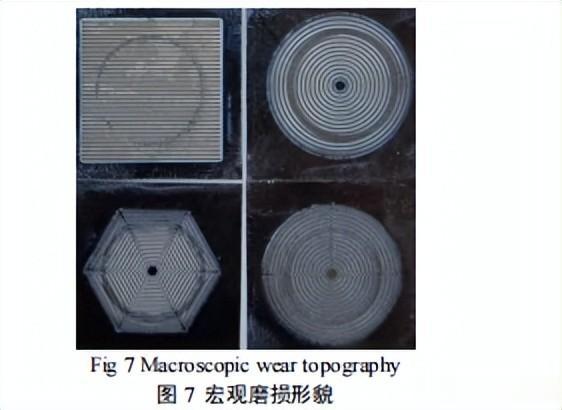
从图8a中可以看到,试样表面有材料涂抹痕迹,并有部分单晶硅碎屑附着在磨痕周围以及非常明显的划痕和沟壑。
这是由于随着摩擦的进行,单晶硅表面结合力较弱的部分被上试样卷走并附着在上试样表面,随着摩擦进行,落到下试样表面形成碎屑。伴随着摩擦的进行,部分碎屑参与到摩擦中,进一步破坏摩擦副表面。
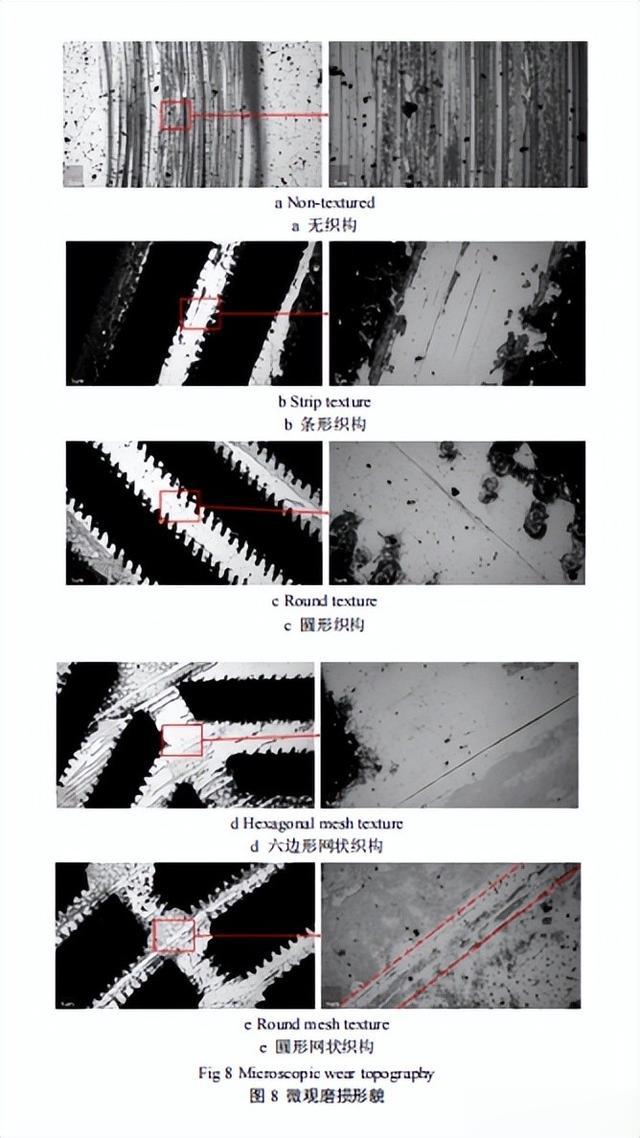
上述结果表面单晶硅的主要磨损机制为磨粒磨损和粘着磨损。图8b,c,d,e为织构间距0.3mm的几种织构试样的磨损形貌。从图中可以看到,织构试样表面的磨痕更光滑且只出现极少的犁沟,并没有涂抹痕迹。试样表面的SEM及EDS检测结果如图9所示。
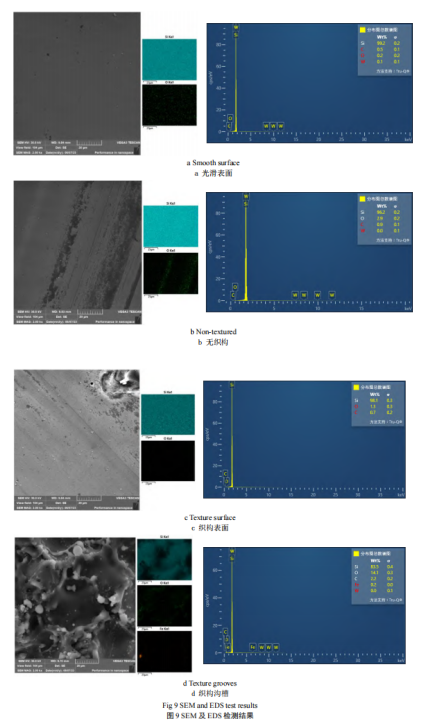
«——【·微织构摩擦行为的仿真分析·】——»
为了探究表面织构对试样表面结构强度的影响以及表面织构对摩擦生热的影响,使用ANSYS有限元分析软件,模拟了各种织构在摩擦磨损实验机上的摩擦行为,并计算其等效应力及温度。
通过solidworks软件建立试样的销-盘接触模型,如图10。其中,模型尺寸和实际情况下试样和销的尺寸保持一致。
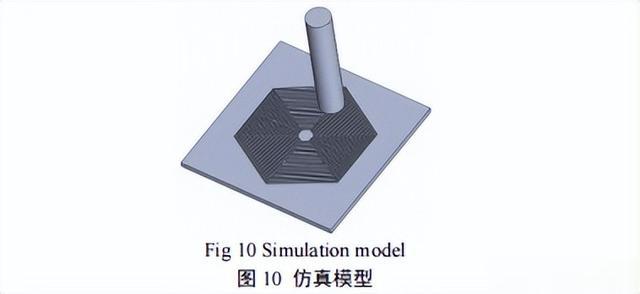
在仿真模拟中,选择固定上试样销,让下试样绕中心轴旋转,给定速度300r/min,环境温度22℃,在上试样销的上表面施加压力0.5N,并约束上试样销在x和y方向的位移以及绕x轴y轴z轴旋转的自由度,仅保留沿z轴位移的自由度。
不同试样的等效应力仿真模拟结果如表3所示。从表中可以看到,无织构试样的平均等效应力是所有结果中最小的,这是因为无织构试样表面平整光滑,为一个完整的整体,不易出现应力集中现象。
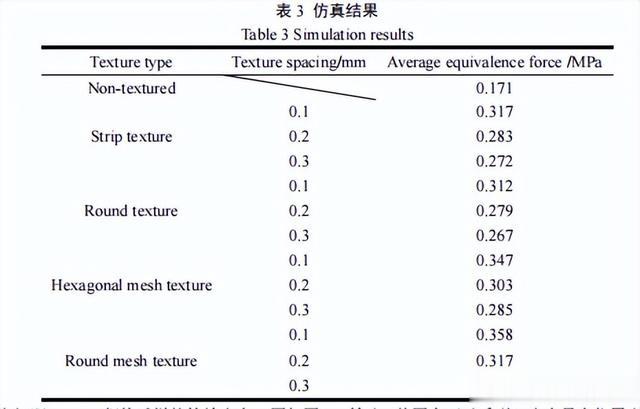
加工织构的试样表面,织构图案破坏了试样表面的整体性,因此容易出现应力集中的现象,并且图案越复杂例如两种网状织构,平均等效应力越大。
此外还可以发现,随着织构间距的增加,试样的平均等效应力逐渐减小。这是因为较大的织构间距使织构在摩擦接触中的占有率越小,试样表面的结构强度越高,承载力越强。
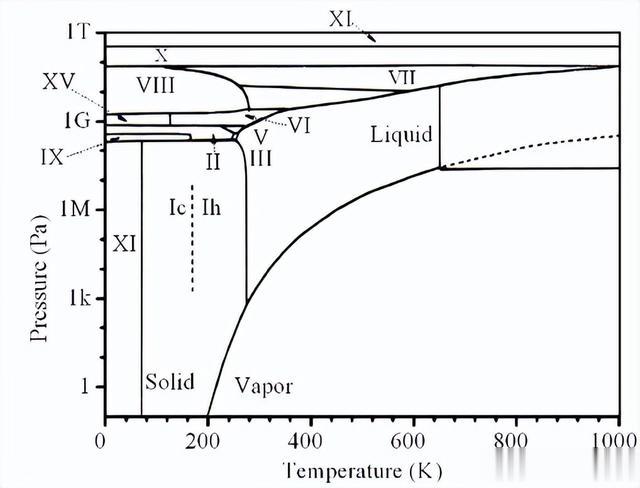
这是因为织构间距越小,图案越复杂织构的在接触中的占有率越大,上下试样的接触面积越小,在单位面积上承载的压力越大。
无织构试样和间距0.3mm织构试样的等效应力云图如图11所示。从图中可以看到,应力最大位置出现在上下试样接触部位,在织构试样中应力集中出现在织构的转角处。说明表面织构会改变原本试样的结构强度,织构图案较为复杂的试样在工作中更容易损坏失效。
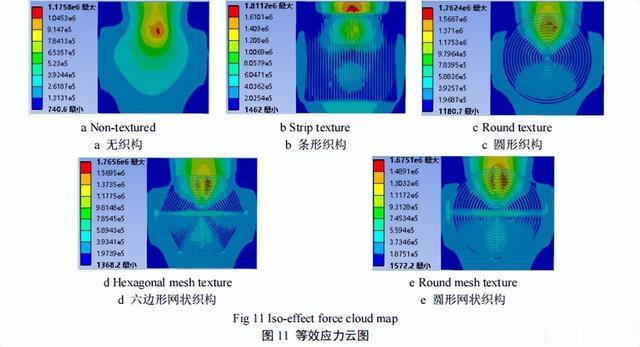
«——【·结语·】——»
利用紫外激光加工技术,在单晶硅试样表面加工出间距分别为0.1mm,0.2mm和0.3mm的圆形、条形、圆形网状和六边形网状织构。激光加工过程中形成的凸起,坑洼缺陷等,会使试样表面粗糙度增加。
通过观察分析试样的磨损形貌,发现无织构处理的单晶硅试样的磨损形式主要为磨粒磨损和粘着磨损,而织构化单晶硅试样能起到减少摩擦生热、收集磨屑的作用,从而减轻磨损并保护材料表面。
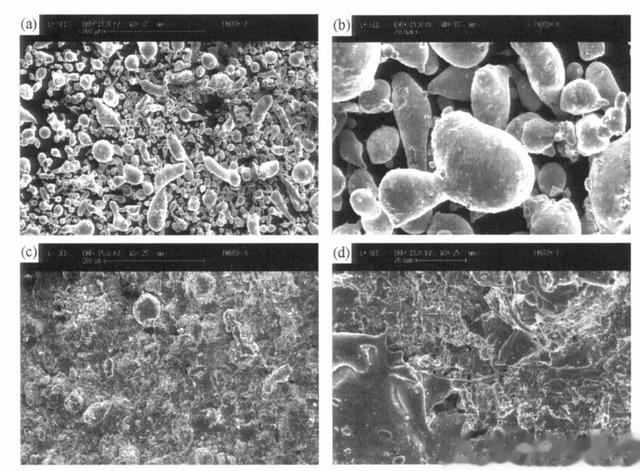
有限元分析表明在试样表明加工织构会影响其结构强度。织构密度越高结构强度越低,并且在织构的转折位置有应力集中现象,在实际应用中这些位置的织构容易损坏失效,因此在加工织构时应选择等效应力较小且摩擦性能良好的织构类型。