铝及铝合金在空气中极容易氧化,氧化后在其表面形成致密的三氧化二铝(AI2O3)氧化膜,该氧化膜的熔点高达2050℃,比铝的熔点658℃高出近1400℃。因此,在焊接加热过程中,往往表面的AI203,氧化膜还未达到温度,而氧化膜下面的纯铝却已熔化,使焊工难以控制焊接热输入,无法保证接质量。另外,氧化还极易吸收水分,它不仅妨碍煌缝的良好熔合,还是形成气孔的根源之一。为了保证焊接质量,焊前必须仔细地清理焊件待焊处、丝表面的氧化膜及油污。
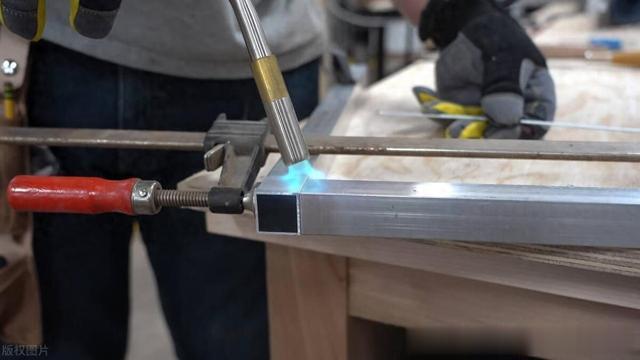
焊前清理主要有机械清理和化学清理两种方法。
(1)机械清理
清理前先用有机溶剂(汽油或丙酮)擦拭待焊处表面,然后用细铜丝刷或不锈钢丝刷(金属丝直径<0.15mm)及各种刮刀,将待焊处的表面刷净(刮净),要刷(刮)到露出金属光泽为止。由于铝及铝合金表面硬度较软,清理焊件表面时,不可以不用各种砂纸、砂布或砂轮进行打磨,以免在打时脱落的砂粒被压入铝及铝合金表面,影响焊接质量。
机械清理时,不仅清理焊件表面,还要认真清理坡口钝边和坡口面,否则,容易在焊接过程中产生气孔、夹渣等接缺陷。机械清理方法主要适用于去除铝及铝合金表面的氧化膜、各种锈蚀在铝及铝合金表面的污染,以及在轧制生产过程中产生的氧化皮等。
机械清理方法常用于大尺寸件表面,焊接生产周期较长、多层焊接,以及经过化学清理后又被污染的焊件清理。
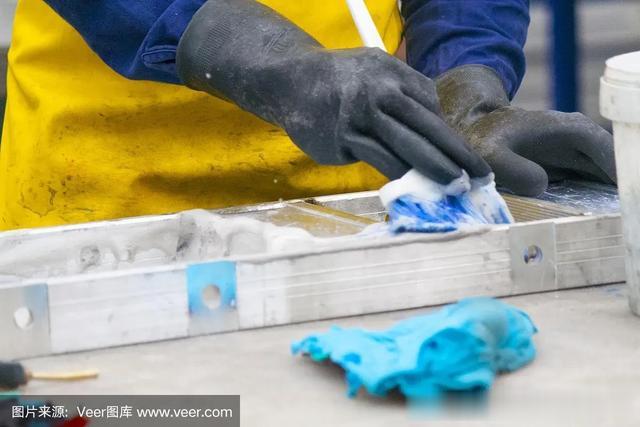
(2)化学清洗
用化学清洗的方法,不仅可以去除氧化膜,还可以起到去除油污的作用。清洗过程用酸和碱等溶液清洗焊件,不仅效率高,而且清洗质量稳定,常适用于被清洗的焊丝尺寸不大、成批量生产的焊件。
用碱溶液或酸溶液进行清洗时,溶液中碱或酸的含量及清洗时间,是随着溶液的温度高低而不同的。如果溶液的温度高,则可以降低溶液中碱或酸的含量或缩短清洗时间;清洗后的铝及铝合金表面是无光泽的银白色。
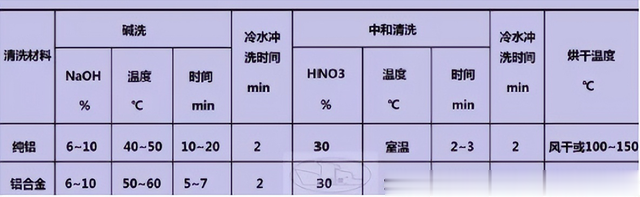
常用铝及铝合金的表面焊前化学清理方法