《前言》
降本增效是一种常用的企业管理策略和方法,它旨在通过优化生产流程、降低成本、提高效率等手段来实现经济目标,为企业的可持续发展提供支持。
Δ降本是指:通过节约成本等手段来提高企业的盈利水平。在当今激烈的市场竞争中,企业需要保持竞争力,而降本则可以为企业提供一个重要的战略优势。例如,在生产成本方面,企业可以通过改善生产工艺、压缩人员及管理成本、采用更加环保和节能的技术等方式来降低生产成本,从而提高产品的竞争力和市场占有率。
Δ增效是指:提高企业的生产效率和资源利用率,进一步提高企业的竞争力和盈利水平。企业可以通过优化生产流程,强化市场营销,创新技术应用等方式提高生产效率和资源配置,在不同的环节中实现效益最大化。
一、 企业不同发展阶段,降本增效的方针
在企业发展的不同阶段,随着市场的渗透程度不同,公司对成本的控制策略不尽相同(如下图所示)。
在初创期,为了拓展市场,必然要持续投入推广费用,不宜过于控制成本,因此降本并不是首要目标;
到了成长阶段,产品逐步占据市场,毛利逐渐由负转正,整体业务欣欣向荣,蒸蒸日上,企业首要目标还是以拓展市场为主,众志成城,很多问题被高涨的热情所掩盖,降本的收益并不明显,也不会被重视;
随着市场的逐渐稳定,竞争对手的奋勇直追,企业会依次经历稳定期,然后逐渐过渡到衰退期,在稳定期及衰退期这漫长的两个阶段,业务遭遇瓶颈,增长乏力,同时市场会被对手一步一步瓜分,企业整体毛利会稳中有降,为了保证稳定的净利润,企业往往会从成本层面开刀,开始开源节流,降本对企业来讲就至关重要了。
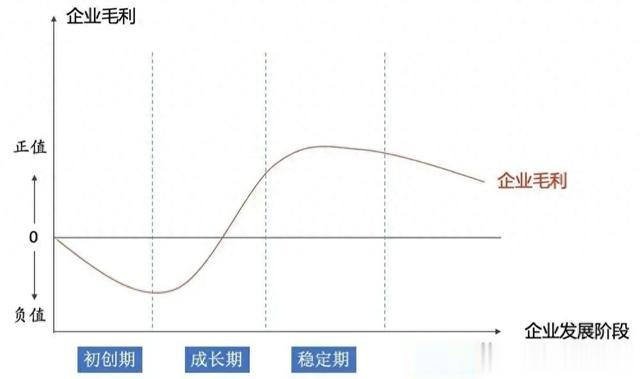
二、 企业如何降本增效?
降本增效是一个长期坚持的过程,需要从组织的重视,流程的完善和系统的支持等多个方面来展开,缺了任何一方都无法达到理想的效果。
降本增效的措施可以从以下几个方面展开:
(一)规模化。
无论从采购,还是生产加工、库房操作、配送运输等环节,都可以追求规模效应来达到降本增效的目的。
①从成本层面来讲,固定成本是恒定的,规模增大了,才会将固定成本均摊,从而降低整体的平均成本。
②从效率层面来讲,很多浪费的动作和等待时间是必不可少的,所以要在这些浪费产生的时候尽可能创造更多的价值。
(二)自动化。
在成本投入可控的前提下,通过自动化来减少人力投入,并提升效率。自动化的建设又可分为系统自动化和设备自动化,两者都是用一次性投入来换取持续性的降本增效,并通过系统操作来降低差错率。
①系统自动化。
使用系统批量处理的方法,尽量减少人工的干预。以此避免人工操作的滞后性和差错。针对有规律的常规型业务,交由系统自动处理,无规律的非常规业务,交由人工处理。
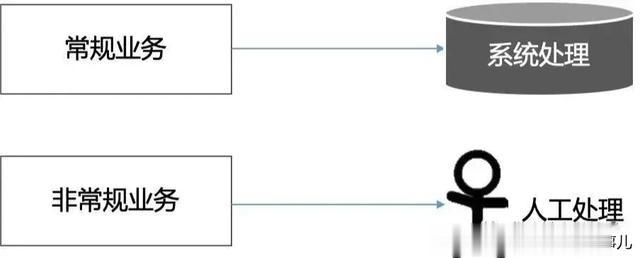
②设备自动化。
自动化设备最大的优势在于可以24小时不间断黑灯作业,且不会出错。
(三)流程优化。
通过对管理流程进行优化,发现不合理的地方并予以改进,以减少一些不必要的浪费, 达到降本增效的目的。
① 工艺设计优化。
对产品的工艺进行改进,将一些能够共用的零部件设计为标准样式,减少零部件的规格数量,可以达到降低管理成本的目标;零部件规格数变少了,就可以批量作业了,效率也自然提升。
② 标准化流程。
对流程进行标准化管理,可以减少培训成本、管理成本、系统设计成本,让生产流程更加精简,出了问题也更加容易排查和解决。
③ 延迟差异化。
所谓延迟差异化,指将赋予产品个性化的制造环节延后的管理办法。延迟差异化可以将差异化的需求、流程放到最后环节处理,让前面的环节尽量标准化、规模化。这样,既可以通过标准化和规模化降本增效,还能有效避免需求的频繁变化。
④定期做精简。
定期对臃肿的人员结构、多余的库房面积、积压的库存、作业中的多余环节进行梳理精简,减少浪费、无效等待和多余动作,增大规模效应。
⑤外包策略。
把一些自身不专业或非核心的业务、流程进行外包,集中精力处理核心的业务。
(四)协同。
通过企业内部各部门、各工序之间的协同,借助系统实现信息共享,可以极大地降低沟通成本、信息处理成本,提升物流、资金流和信息流的流转效率。
三、企业开展降本增效工作的流程路径
1、企业深入诊断
要对企业做一个相对全面和客观的诊断(深入诊断),真正系统而全面地发现企业运行的问题。
需要理论功底扎实且实操经验丰富的专业老师展开或指导诊断工作、一般企业管理人员都不具备这样的能力,这是全面、真实、客观、深入发现问题的必经之路。
2.痛点根因分析
经过系统的诊断,发现工厂痛点问题,找到痛点问题的根因所在。根因分析一定需要用到分析工具,比如鱼骨图、5WHY、QC七大工具等。
需要具备丰富经验的专业老师支持,否则也很可能会走偏,导致分析的原因不痛不痒,解决起来似乎有点效果,但又不能根本解决。
3.针对性极强的对策
对策,就要有极强的针对性,否则就是“大事化小,小事化了”、“挠痒痒”、“做表面文章”......这些都是在欺骗公司,欺骗自己。制定对策的人,一定要是有责任担当、能客观公正、敢于向自己开炮的人。
4.持续推行改善
在对策落地的过程中,需要各层级有较强的执行力,需要有系统化的运行和人员能力的支撑。否则就是改善效果上下波动很大,改善成果难以扩大,止步不前。
5.梯队人才培养
企业的问题都是老板的问题,因为老板的认知和决策决定了企业走什么样的道路;企业的问题都是管理的问题,不管是销售、研发,还是人员,本质上都是管理;企业的问题都是人的问题,一切都是由人来支撑的。培养人才,培养梯队人才、持续培养梯队人才,是企业降本增效和持续发展的核心。
四、企业实施降本增效的误区
(一)盲目压价采购成本,导致原材料质量下降。
一些企业片面追求采购环节成本最低,导致采购的原材料价格低廉。如果只是在采购环节,确实实现了成本优化,但由于原材料质量差,造成生产环节成本增加,销售部门成本增加,客户满意度降低。由于采购价格的下降,导致原材料出现劣质现象,造成质量事故,导致企业品牌损失。
(二)将降低成本片面认为是单纯地降低生产成本。
大多数管理者自然而然把成本理解为生产成本,把成本降低限制在生产活动中,不考虑其他地方。在传统制造业中,生产成本只是总成本的一部分,约占50-70%。技术研发、营销、企业管理、客户服务等领域都产生了相当大的成本,但在成本分析中却很少受到重视。
(三)将降本视为供应链各环节的成本都降低。
供应链是企业通过控制信息流、物流和现金流,从原材料采购开始,制作中间产品和最终产品,最后通过营销网络将产品交付给消费者。
一些企业经理认为,企业应该追求所有环节的成本最小化,这显然是不科学的。供应链是由企业相互依赖的一系列价值增值活动组成的系统,成本在各个环节之间发生相互制约作用,应通过各供应链环节之间的相互协调和优化,带来降本增效的机会,追求总成本的优化。
(四)将降本理解为大力削减机构、精简人力,减少福利。
降低成本的真正意义是提高货币计量的投入产出率,而不是盲目地降低成本。
遗憾的是,许多企业的成本控制已经陷入了误解,特别是在劳动力成本管理方面。其结果只能是逆向淘汰,劣币驱逐良币,成为同行企业的人才培训基地。
(五)忽视产品开发、技术研发对成本的影响。
产品设计通常考虑到市场竞争、消费者需求、工厂生产能力、原材料成本等方面的影响。一旦成品成型,其60%的成本将被锁定。因此,企业应将研发设计作为降低整体成本的重要环节,充分考虑原材料获取方便、生产工艺成熟、生产效率稳定、物流运输方便等方面的设计成本,使企业成本领先战略赢在起跑线上。
(六)降本因素相互矛盾、交叉影响。
企业在降低成本时,由于缺乏总体规划和事先规划,往往会以相互矛盾的方式降低不同环节的成本。比如,为了增加市场份额,从规模效应中受益,大量承接多品种、多规格的产品,反而增加了管理成本,降低了规模效应。
(全文完)